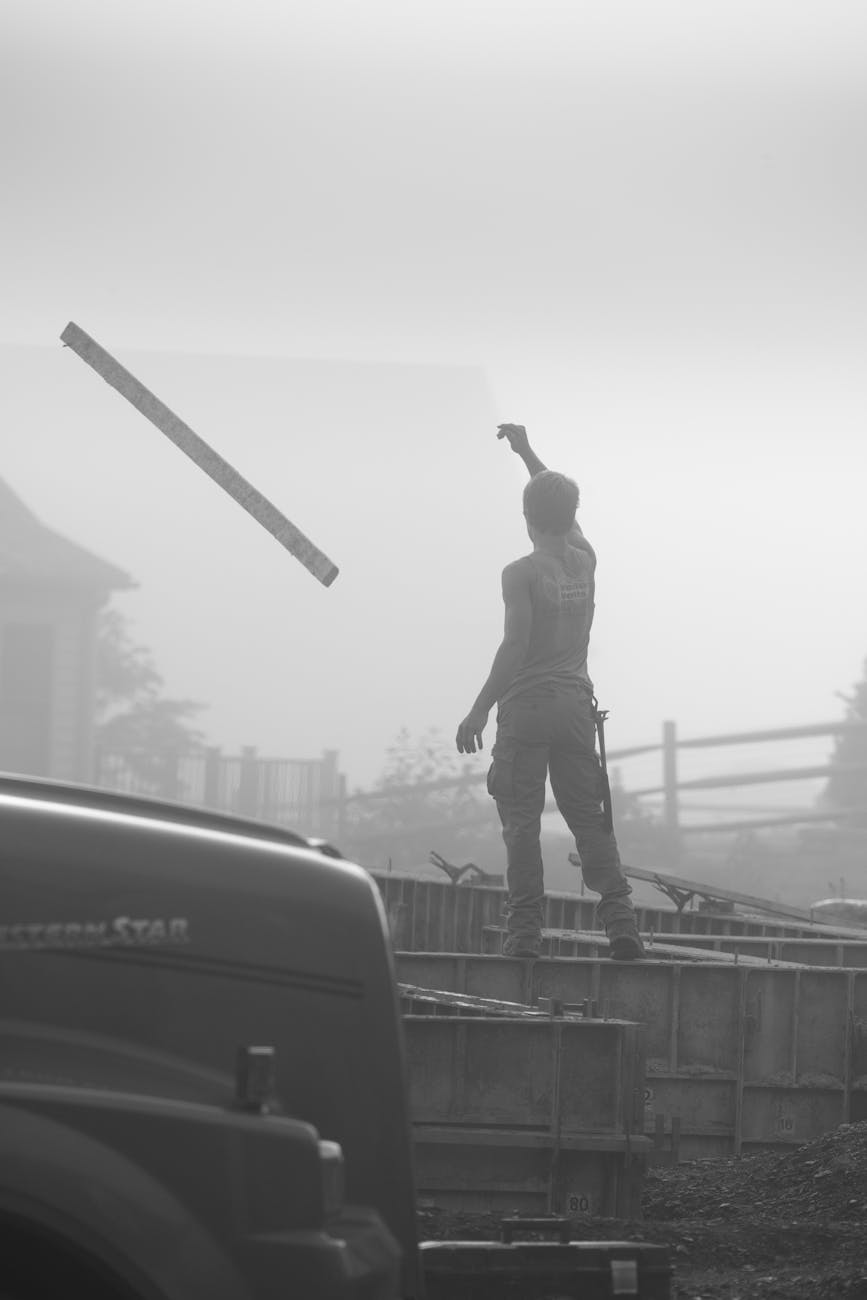
Formwork Safety: Hazards and Control Measures
1. Introduction
Formwork is a critical temporary structure used to support wet concrete until it achieves sufficient strength. While essential in construction, oil & gas, and manufacturing projects, formwork operations present numerous safety hazards that can lead to severe injuries or fatalities if not properly managed. This guide examines key formwork hazards and provides practical control measures to enhance workplace safety.
2. What is Formwork?
Formwork refers to the temporary molds into which concrete is poured to achieve desired shapes and structural elements. Types include:
- Traditional timber formwork
- Engineered modular systems
- Climbing formwork (for tall structures)
- Slipforming (for continuous pours)
- Permanent insulated formwork
Proper formwork design and installation are crucial for structural integrity and worker safety.
3. Common Formwork Hazards
A. Structural Collapse Risks
- Cause: Inadequate design, overloading, or improper bracing
- Impact: Catastrophic failures can crush workers beneath tons of wet concrete
B. Falls from Height
- Cause: Working on unguarded platforms or during formwork assembly/dismantling
- Impact: Major cause of fatalities in construction
C. Material Handling Injuries
- Cause: Manual handling of heavy formwork components
- Impact: Musculoskeletal disorders and crush injuries
D. Struck-by Hazards
- Cause: Falling tools/materials or shifting formwork components
- Impact: Head injuries and fatalities
E. Confined Space Dangers
- Cause: Working in formwork voids or enclosed areas
- Impact: Suffocation or entrapment
F. Electrical Hazards
- Cause: Contact with overhead power lines during installation
- Impact: Electrocution risks
G. Chemical Exposure
- Cause: Formwork release agents and curing compounds
- Impact: Dermatitis and respiratory issues
4. Control Measures for Formwork Safety
A. Engineering Controls
- Design Compliance: Ensure formwork meets structural engineering specifications
- Fall Prevention: Install guardrails and toe boards on working platforms
- Shoring Systems: Use properly braced adjustable metal props
- Modular Systems: Prefabricated formwork reduces onsite hazards
B. Administrative Controls
- Competent Supervision: Formwork erectors must be trained and certified
- Load Limits: Clearly mark maximum concrete pour heights
- Inspection Regime: Daily checks before and after concrete placement
- Permit Systems: For high-risk formwork operations
C. Personal Protective Equipment (PPE)
- Hard Hats: ANSI Z89.1 compliant
- Fall Arrest Systems: Full-body harnesses with shock-absorbing lanyards
- High-Visibility Clothing: Especially near mobile plant
- Steel-toe Boots: For foot protection
- Gloves: When handling rough formwork materials
D. Safe Work Practices
- Sequential Dismantling: Follow engineered removal sequence
- No Work Under Loads: Prohibit workers beneath suspended formwork
- Concrete Monitoring: Wait until adequate strength is achieved before stripping
- Housekeeping: Keep work areas clear of trip hazards
5. Industry-Specific Considerations
A. Construction Sector
- Challenge: Frequent formwork reuse increases wear risks
- Solution: Implement rigorous inspection protocols
B. Oil & Gas Industry
- Challenge: Formwork in confined process areas
- Solution: Hot work permits and gas monitoring
C. Manufacturing Facilities
- Challenge: Integrating formwork with existing structures
- Solution: Detailed interface planning with plant operations
6. FAQs
FAQ 1: What qualifications do formwork workers need?
Answer: Workers should complete:
- OSHA 10/30-hour construction training
- Manufacturer-specific system training
- Fall protection certification
- Competency assessments for complex formwork
FAQ 2: How often should formwork be inspected?
Answer:
- Before concrete pour: Comprehensive check
- During pour: Continuous monitoring
- After extreme weather: Immediate re-inspection
- Daily: General condition assessment
FAQ 3: What’s the minimum concrete strength before formwork removal?
Answer: Typically 70% of design strength (verify with engineer). Test with:
- Rebound hammer tests
- Break-off cylinder tests
- Maturity method monitoring
FAQ 4: How to prevent formwork blowouts during concrete placement?
Answer:
- Use adequate bracing and ties
- Control concrete pour rate
- Employ vibration limits near forms
- Install pressure relief mechanisms
FAQ 5: What are the key differences between conventional and system formwork safety?
Answer:
Factor | Conventional | System Formwork |
---|---|---|
Fall Risk | Higher during assembly | Integrated guardrails |
Collapse Risk | More variable | Engineered safety factors |
Worker Skill | General carpentry | Specialized training |
FAQ 6: How to handle formwork in high wind conditions?
Answer:
- Suspend operations at 25 mph (40 km/h)
- Secure loose components
- Increase bracing
- Follow site-specific wind action plan
FAQ 7: What are the most common formwork design failures?
Answer:
- Inadequate lateral support
- Underestimated concrete pressure
- Poor connection details
- Foundation settlement
- Construction sequence errors
FAQ 8: How to safely handle formwork chemicals?
Answer:
- Refer to SDS for each product
- Use gloves and eye protection
- Ensure adequate ventilation
- Store away from ignition sources
FAQ 9: What emergency procedures are needed for formwork operations?
Answer:
- Collapse rescue plan
- Fall victim retrieval
- Concrete engulfment response
- Emergency contact protocols
FAQ 10: How does cold weather affect formwork safety?
Answer:
- Ice accumulation creates slip hazards
- Frozen ground affects stability
- Special curing methods required
- Extended stripping times needed
7. Conclusion
Effective formwork safety requires a systematic approach combining:
✔ Proper design and engineering
✔ Comprehensive worker training
✔ Rigorous inspection regimes
✔ Appropriate PPE usage
✔ Strict adherence to safe work practices
By implementing these control measures across construction, oil & gas, and manufacturing sectors, organizations can significantly reduce formwork-related incidents while maintaining productivity. Regular safety audits and continuous improvement programs help sustain high safety standards throughout project lifecycles.
Painting Work Safety: Hazards and Control Measures
Demolition Safety: Hazards and Control Measures
Chemical Safety & Hazard Communication (GHS, SDS)
Manufacturing Safety: Machine Guarding & Lockout-Tagout (LOTO)
National Fire Service Day 2025: History, Significance, and Key Facts