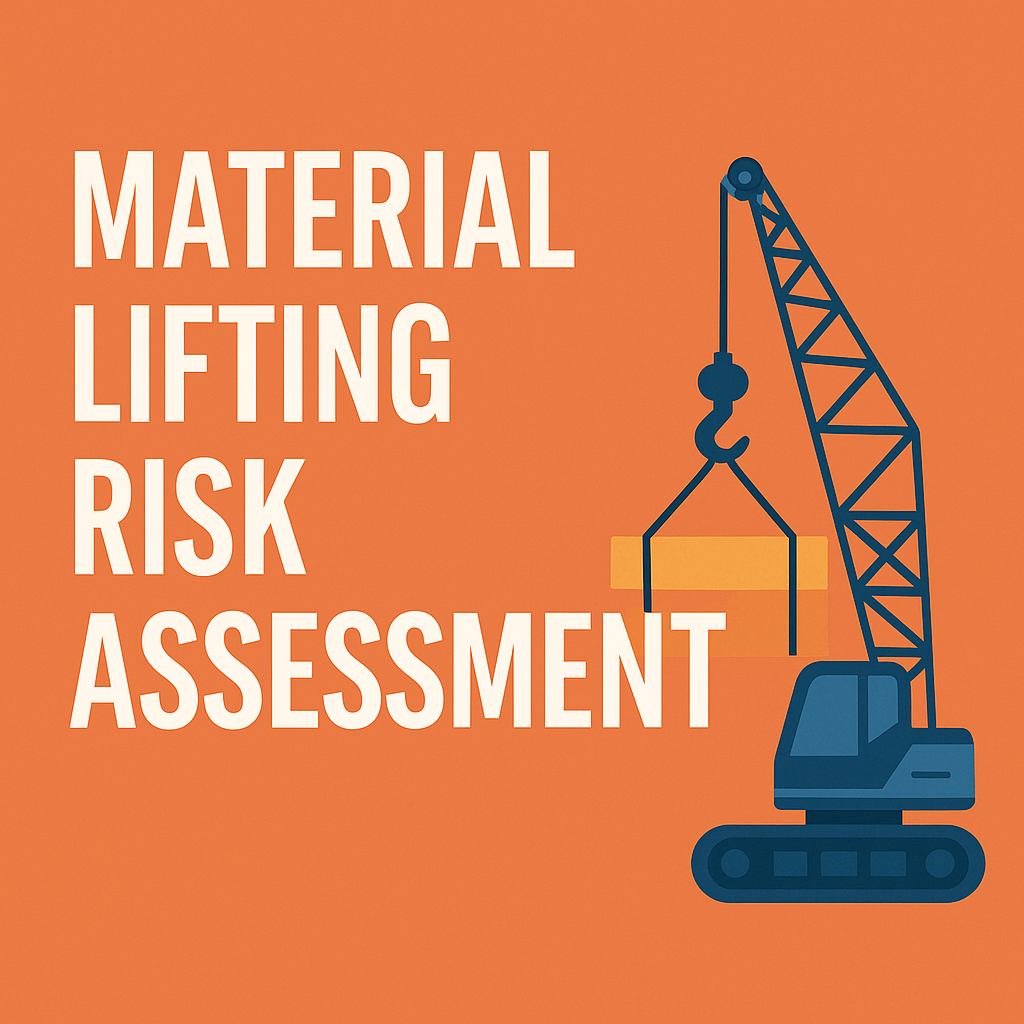
Material Lifting Risk Assessment
Material lifting is a daily activity on construction sites, factories, and warehouses — and one of the leading causes of workplace injuries and fatalities. From manually lifting a box to hoisting a 10-ton beam with a crane, each operation carries risk.
A material lifting risk assessment helps you spot the hazards, protect your people, and plan for a safe lift — whether it’s done by hand or machine. It’s not just about paperwork; it’s about preventing accidents before they happen.
Legal Requirements and Safety Standards
OSHA Lifting Safety Regulations
Under OSHA 29 CFR 1910.178 and 1926.251, employers must ensure lifting operations are planned, supervised, and executed safely. This includes equipment inspections, load limits, and operator training.
LOLER (UK) – Lifting Operations and Lifting Equipment Regulations
LOLER 1998 requires employers in the UK to ensure lifting equipment is strong, stable, and used by competent people. Regular inspections are mandatory.
Indian Guidelines for Lifting Safety
In India, BIS codes like IS 3696 and the Factories Act emphasize lifting equipment certification, operator competency, and safe lifting practices.
Common Types of Material Lifting
Manual Lifting
Lifting by hand, often underestimated but a major cause of musculoskeletal disorders (MSDs).
Mechanical Lifting – Cranes, Hoists, Forklifts
Machines do the heavy work — but misuse or poor planning can lead to catastrophic results.
Rigging and Slinging Activities
Involves connecting loads to lifting devices using chains, slings, shackles, and hooks. Requires skill, precision, and proper judgment.
Key Hazards in Material Lifting Operations
Load Drops and Equipment Failure
A snapped sling or malfunctioning crane can send a load crashing down — risking lives and property.
Overloading and Unbalanced Loads
Going beyond load limits or improper rigging leads to tipping, swaying, or sudden shifts.
Struck-by or Caught-between Hazards
A swinging or falling load can strike workers. Poor exclusion zone control can crush limbs or trap workers.
Manual Handling Injuries
Poor posture, overexertion, or repetitive lifting causes back pain, sprains, and long-term injuries.
Step-by-Step Lifting Risk Assessment Process
Step 1 – Identify the Lifting Task and Hazards
Is the load heavy? Bulky? Is the lift high-risk or repetitive? What’s around the lift zone?
Step 2 – Determine Who Might Be Harmed
Think operators, riggers, spotters, nearby workers, and even visitors.
Step 3 – Evaluate the Risks and Decide Controls
What can go wrong? Will it crush someone? Can the crane tip? Choose the right controls.
Step 4 – Record the Risk Assessment
Document hazards, control measures, responsible persons, and timelines.
Step 5 – Review and Update Regularly
If something changes — like new equipment or location — reassess immediately.
Risk Control Measures for Safe Lifting
Pre-Lift Planning and Toolbox Talks
Plan every lift. Walk the area. Hold a toolbox talk. Assign roles and confirm signals.
Load Weight Verification and Center of Gravity
Know the weight and balance point. Never guess. Use load charts and labels.
Use of Trained Operators and Riggers
No training = no lifting. Ensure certification and hands-on experience.
Proper Selection of Lifting Equipment
Pick the right sling, hook, or crane. One wrong match can break the whole system.
Establishing Exclusion Zones
Keep people out of the drop zone. Use barriers, flags, and spotters to control access.
Hierarchy of Controls in Lifting Operations
Eliminate Unnecessary Lifting
Can the material be delivered directly where needed?
Substitute with Safer Lifting Methods
Use conveyor belts, pallet jacks, or vacuum lifters when possible.
Engineering Controls – Lifting Aids and Devices
Use cranes, hoists, and turntables to reduce strain and improve precision.
Administrative Controls – SOPs and Training
Write clear procedures. Refresh training. Supervise every lift.
PPE – Gloves, Helmets, Safety Boots
Protect hands from cuts, feet from crushes, and heads from falling tools.
Safety Tips for Material Lifting
Never Walk Under a Suspended Load
It may look secure, but one snap and it’s a disaster. Stay clear.
Communicate Using Hand Signals or Radios
Miscommunication leads to mishaps. Use certified signals or clear radio protocols.
Inspect Equipment Before Each Use
Slings, shackles, hooks, cranes — check them like your life depends on it. Because it might.
Real-Life Case Studies
Case 1: Crane Overturn Due to Overloading
A mobile crane tipped over when lifting beyond its rated load. No outriggers deployed. The result? Property damage and a serious injury.
Lesson: Always follow load charts and stabilize the crane.
Case 2: Manual Lifting Back Injury Incident
A warehouse worker repeatedly lifted 30 kg boxes without training. Months later, he developed chronic back pain.
Lesson: Train workers and enforce lifting limits.
Material Lifting Risk Assessment Template
What to Include in the Risk Assessment
- Description of the lift
- Type of load and weight
- Equipment used
- Identified hazards
- Controls applied
- Responsible persons
- Review schedule
Practical Use On-Site
Use this document before every complex lift. Review it with your team, post it near the lift zone, and update it when conditions change.
Material Lifting Risk Assessment
General Information
- Project/Site Name: ABC Infra Pvt. Ltd. – Tower 4 Project
- Assessment Title: Material Lifting Risk Assessment
- Location: Ground to 5th Floor – Tower Block
- Assessed By: Mahendra Lanjewar (Safety Officer)
- Assessment Date: 01 July 2025
- Review Date: 01 October 2025
- Activity Description: Lifting and shifting of steel rods, cement bags, and construction materials using cranes, chain pulleys, and manual handling.
Material Lifting Risk Assessment Table
Task | Hazards Identified | Persons at Risk | Risk Rating (Before Control) | Control Measures | Risk Rating (After Control) | Responsible Person |
---|---|---|---|---|---|---|
1. Lifting heavy materials with tower crane | Load drop, crane failure, swinging loads | Riggers, signalmen, nearby workers | High | – Only certified crane operators allowed – Conduct pre-use inspection – Use tag lines to control swing – Don’t exceed SWL (Safe Working Load) – Area below to be barricaded | Low | Crane Operator / Rigger Supervisor |
2. Manual lifting of cement bags and bricks | Back injuries, muscle strain | Laborers, masons | Medium | – Use correct lifting techniques – Team lift for heavy items – Provide mechanical aids (trolleys) – Train workers in manual handling | Low | Site Supervisor |
3. Use of chain pulley block for vertical lifting | Chain snap, overloading, tool malfunction | Workers operating pulley | Medium | – Use tested/labeled lifting equipment – Never exceed load limit – Regular maintenance and lubrication – Use PPE including hand gloves and helmets | Low | Storekeeper / Equipment Inspector |
4. Communication failure during lifting | Miscommunication, dropped loads, collision | Crane operator, rigger, signalman | High | – Use trained and certified signalman – Standard hand signals and radios – Pre-lift briefing before every major lift | Low | Rigger Supervisor |
5. Poorly stacked lifted material | Collapse or falling objects | All nearby workers | High | – Stack material on level ground – Use chocks for rolling materials – Don’t stack above shoulder height | Low | Material Handling Team |
6. Working near live electrical lines | Electrocution during crane boom movement | Crane operator, signalman | High | – Maintain safe distance from power lines – De-energize nearby lines if required – Appoint a spotter to monitor clearance | Low | Safety Officer / Crane Operator |
Risk Rating Matrix
Severity | Likelihood | Risk Rating |
---|---|---|
1 – Minor injury | 1 – Unlikely | Low |
2 – Lost time injury | 2 – Possible | Medium |
3 – Major/fatal injury | 3 – Likely | High |
Note: Risk Rating = Severity × Likelihood
Additional Notes
- Training Provided: Riggers, signalmen, and crane operators are trained in lifting safety and emergency procedures.
- PPE Required: Safety helmet, gloves, reflective vest, safety boots, face shield (for dust).
- Permit to Work: Mandatory for lifting heavy or critical loads.
- Lifting Plan: Prepared for all non-routine or high-risk lifts.
- Emergency Preparedness: Nearby area clear of obstructions, and a first-aid kit with stretcher is available.
Review and Sign-Off
Name | Designation | Signature | Date |
---|---|---|---|
Rupesh Wasnik | Safety Officer | [Signature] | 01-07-2025 |
Deepak Sharma | Crane Operator | [Signature] | 01-07-2025 |
Kiran Patil | Site Engineer | [Signature] | 01-07-2025 |
Conclusion
Whether it’s a steel beam or a toolbox, lifting is serious business. One mistake can destroy equipment — or worse, a life. That’s why a material lifting risk assessment is a non-negotiable part of the job. Plan smart. Lift safe. And remember, every load lifted safely is a life protected.
Confined Space Risk Assessment
Scaffolding Work Risk Assessment
FAQs
1. When is a lifting plan required?
A lifting plan is needed for all complex or critical lifts, especially when using cranes or heavy machinery.
2. What is the most common cause of lifting accidents?
Poor planning and lack of training are top causes — followed by equipment failure and overloading.
3. Who is responsible for the lifting risk assessment?
A competent person such as a safety officer or lifting supervisor is responsible.
4. How do I know if a sling or chain is safe to use?
Inspect for cuts, wear, deformities, and check inspection tags before use.
5. Can manual lifting be eliminated entirely?
Not always, but using lifting aids, team lifts, and smart layout design can reduce manual handling significantly.