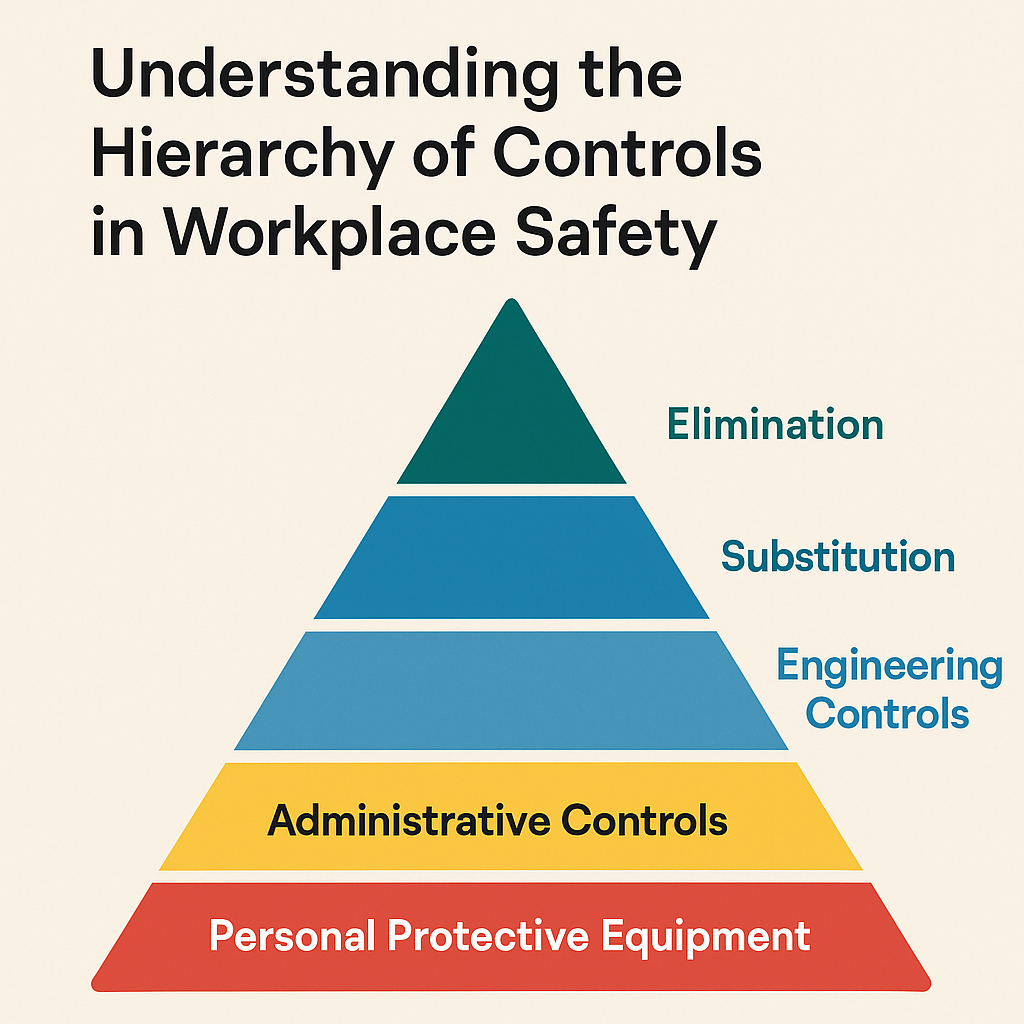
Understanding the Hierarchy of Controls in Workplace Safety
Why Workplace Safety Matters
Workplace safety isnāt just a box to tick ā itās a matter of life and death. Every day, workers across the world face potential risks, from slippery floors to dangerous chemicals. A solid safety culture not only protects employees but also saves companies from financial losses, legal trouble, and reputation damage.
The Role of Risk Management
At the heart of every effective safety program lies risk management ā identifying hazards, assessing their potential harm, and finding the best ways to control them. And thatās exactly where the Hierarchy of Controls comes in.
What is the Hierarchy of Controls?
Definition and Purpose
The Hierarchy of Controls is a step-by-step approach to minimizing or eliminating exposure to hazards. Think of it like a ladder ā the higher you go, the more effective the control. Developed by safety organizations like NIOSH and widely adopted by OSHA and ISO standards, it’s become a gold standard in safety management.
Who Developed It?
Although the concept has evolved, its roots go back to the National Institute for Occupational Safety and Health (NIOSH), which structured these controls based on their reliability and impact on worker safety.
The 5 Levels of the Hierarchy of Controls
1. Elimination ā Remove the Hazard Completely
If thereās no hazard, thereās no risk. Elimination is the most effective form of control ā simple as that.
Example:
Instead of requiring workers to manually lift heavy boxes, you redesign the process so no lifting is needed ā such as using automated conveyors.
2. Substitution ā Replace the Hazard
When you canāt eliminate the hazard, replace it with something less dangerous.
Example:
Switching from a toxic solvent to a non-toxic, biodegradable alternative. The task still gets done ā but with less risk.
3. Engineering Controls ā Isolate People from the Hazard
If the hazard must stay, isolate workers from it using physical changes to the workplace.
Example:
Installing machine guards on rotating equipment or fume hoods in laboratories. The hazard remains, but itās kept away from people.
4. Administrative Controls ā Change the Way People Work
These controls focus on policies, training, and work practices to limit exposure.
Examples:
- Rotating shifts to reduce time exposed to loud noise
- Lockout/Tagout procedures for machinery
- Safety signage and training
While useful, these controls rely on human behavior ā which can be unpredictable.
5. Personal Protective Equipment (PPE) ā Protect the Worker
PPE is the last line of defense, used only when all other methods aren’t enough.
Example:
Gloves, helmets, respirators, safety glasses ā these protect the worker, but they donāt remove the hazard. If the gear fails, the worker is directly at risk.
Why the Hierarchy is Ranked That Way
The hierarchy is ordered based on effectiveness. The higher up you go, the less it depends on the worker doing everything right. PPE, at the bottom, depends on perfect use and maintenance ā which isnāt always realistic.
Benefits of Using the Hierarchy in Safety Planning
- Reduces injuries and illnesses
- Cuts insurance and legal costs
- Builds a strong safety culture
- Enhances compliance with regulations like OSHA or ISO 45001
Common Misconceptions
āPPE is Enoughā
Itās not. PPE should never be your only control. If you can remove or isolate the hazard, do that first.
āOne Control is Sufficientā
In reality, combining controls often offers the best protection. For example, use ventilation (engineering), limit exposure time (admin), and provide respirators (PPE).
Implementing the Hierarchy in Real Workplaces
Steps to Apply:
- Identify the hazard
- Assess its severity
- Try elimination or substitution
- Use engineering/admin controls if needed
- Add PPE as the final step
Case Study ā Chemical Handling:
In a lab dealing with a toxic chemical:
- They substituted it with a less hazardous one.
- Installed a fume hood.
- Trained staff on handling protocols.
- Required gloves, goggles, and lab coats.
This layered approach drastically reduced the risk.
Challenges and How to Overcome Them
Budget Constraints
Yes, elimination and engineering controls cost more upfront. But think long-term ā avoiding just one serious injury can save thousands.
Resistance to Change
People donāt like change. Explain the why, show data, and get worker involvement early in the process.
Final Thoughts on Making the Workplace Safer
The Hierarchy of Controls is more than a chart ā itās a mindset. If we stop settling for PPE alone and start thinking about elimination first, we can design safer workplaces from the ground up. Itās not just about compliance ā itās about care.
Conclusion
To truly protect your workforce, you need more than hard hats and gloves. The Hierarchy of Controls helps you think smarter, not harder ā pushing you to remove hazards at the root. Start at the top of the hierarchy and only work your way down when absolutely necessary.
Every injury prevented is a life improved ā and thatās a goal worth working for.
What is Risk Assessment? Step-by-Step Guide with Real Examples
Demolition Work Risk Assessment
Formwork and Shuttering Risk Assessment
Concrete Pouring Risk Assessment
Reinforcement Steel Fixing Risk Assessment
FAQs
1. What is the most effective control in the hierarchy?
Elimination ā because it removes the hazard entirely, eliminating the risk.
2. Can you use multiple controls together?
Absolutely! In fact, combining controls (like engineering + PPE) provides layered protection.
3. Why is PPE considered the last line of defense?
Because it doesnāt eliminate the hazard ā it just reduces the damage if something goes wrong.
4. How do I decide which control to implement?
Start at the top (elimination) and work down. If elimination isnāt possible, try substitution, then engineering, and so on.
5. Are there regulations that enforce the hierarchy?
Yes ā agencies like OSHA and ISO reference the hierarchy as a best practice in health and safety planning.