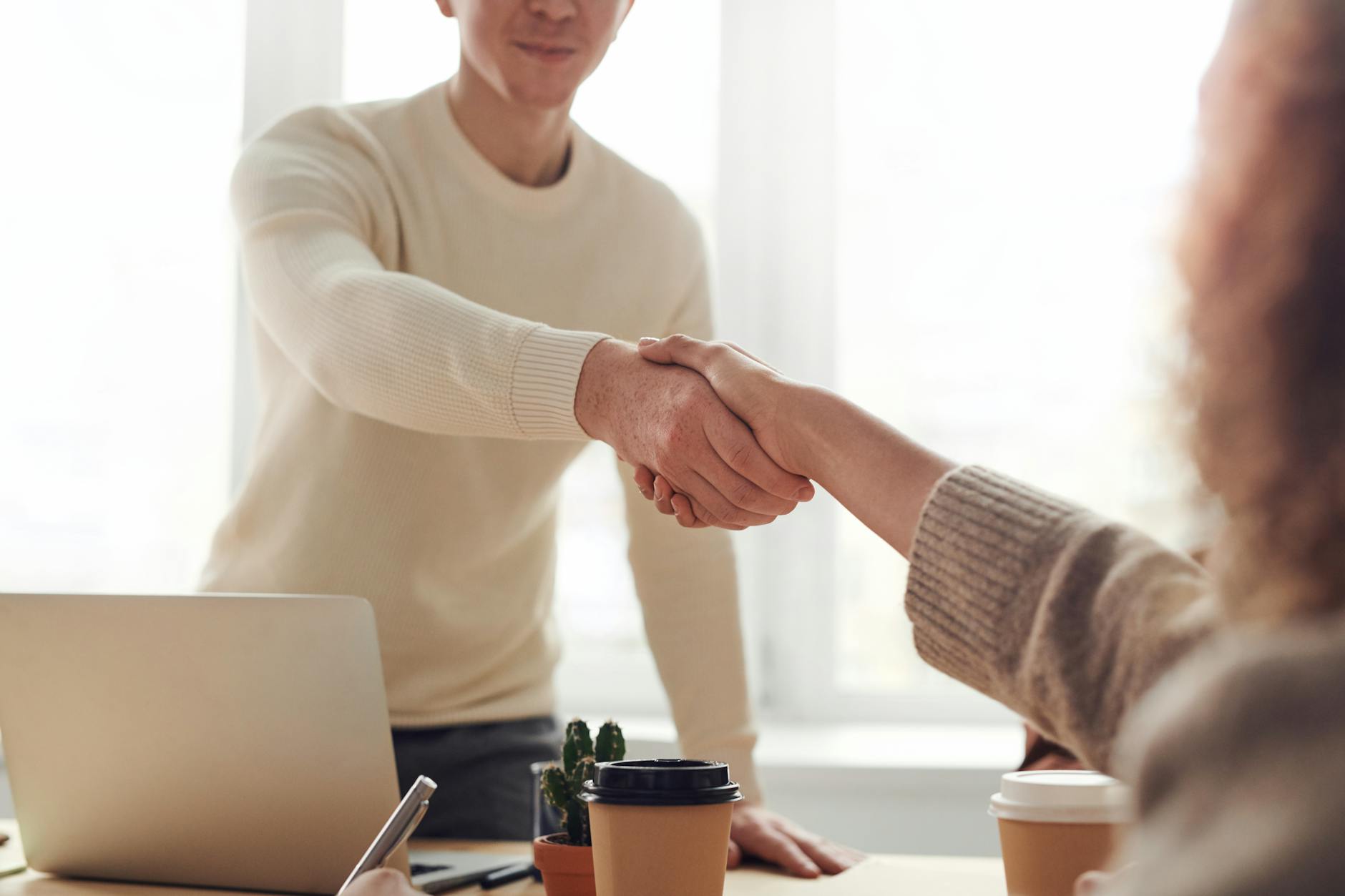
Construction Safety Officer: 50+ Safety Job interview Questions & Answers
General Safety Knowledge
1. What are the primary responsibilities of a Construction Safety Officer?
A Construction Safety Officer ensures compliance with OSHA and other safety regulations, conducts site inspections, trains workers on safety protocols, investigates incidents, and implements corrective actions to prevent hazards.
2. What OSHA standards are most relevant to construction safety?
Key OSHA standards include:
- 29 CFR 1926 (Construction Industry Regulations)
- Fall Protection (1926.501)
- Scaffolding (1926.451)
- Hazard Communication (1910.1200)
- Personal Protective Equipment (PPE) (1926.95)
3. How do you stay updated with changing safety regulations?
I regularly review OSHA updates, attend safety training seminars, participate in industry webinars, and follow safety organizations like ASSP and NSC.
4. What is a Job Hazard Analysis (JHA), and how do you conduct one?
A JHA identifies potential hazards for specific tasks. Steps include:
- Breaking down the job into steps.
- Identifying hazards for each step.
- Implementing controls (elimination, substitution, PPE).
5. Explain the hierarchy of hazard controls.
The hierarchy (from most to least effective):
- Elimination
- Substitution
- Engineering Controls
- Administrative Controls
- PPE
Site Safety Inspections & Audits
6. How do you conduct a construction site safety inspection?
I follow a checklist covering:
- Fall protection
- Scaffolding & ladders
- Electrical safety
- PPE compliance
- Hazard communication
- Heavy equipment safety
7. What are the most common safety violations on construction sites?
Common violations include:
- Lack of fall protection
- Improper scaffolding
- Inadequate hazard communication
- Missing PPE (hard hats, gloves, eye protection)
- Unsafe trenching/excavation
8. How would you handle a worker refusing to wear PPE?
I would:
- Explain the risks and regulations.
- Offer alternative PPE if comfort is an issue.
- Enforce disciplinary action if non-compliance continues.
9. What should be included in a daily safety report?
- Identified hazards
- Corrective actions taken
- Near-misses/incidents
- Worker compliance observations
- Weather/environmental concerns
10. How do you ensure subcontractors follow safety protocols?
- Conduct pre-work safety briefings.
- Include safety compliance in contracts.
- Perform regular audits.
- Enforce penalties for violations.
Incident Investigation & Emergency Response
11. Describe your process for investigating a workplace accident.
- Secure the scene.
- Gather witness statements.
- Analyze root causes (5 Whys or Fishbone Diagram).
- Recommend corrective actions.
- Document findings in a report.
12. What is a near-miss, and why is reporting it important?
A near-miss is an unplanned event that could have caused injury. Reporting helps prevent future incidents by addressing hazards before they cause harm.
13. How would you handle a chemical spill on-site?
- Evacuate the area.
- Contain the spill (absorbent materials).
- Follow SDS guidelines for cleanup.
- Report the incident.
- Review procedures to prevent recurrence.
14. What are the key elements of an Emergency Action Plan (EAP)?
- Evacuation routes
- Emergency contacts
- Fire extinguisher locations
- First-aid procedures
- Roles and responsibilities
15. How do you conduct a fire safety drill?
- Notify workers in advance.
- Simulate an emergency scenario.
- Monitor evacuation times and routes.
- Debrief and address any issues.
Training & Communication
16. How do you ensure workers understand safety training?
- Use hands-on demonstrations.
- Conduct quizzes or Q&A sessions.
- Provide materials in multiple languages if needed.
- Reinforce training with toolbox talks.
17. What topics should be covered in new employee safety orientation?
- Site-specific hazards
- Emergency procedures
- PPE requirements
- Reporting injuries/near-misses
- Safe equipment operation
18. How do you handle language barriers in safety training?
- Use visual aids/videos.
- Hire bilingual trainers.
- Provide translated materials.
- Use simple, clear language.
19. What are toolbox talks, and how often should they be conducted?
Short safety discussions on specific hazards. They should be held weekly or before high-risk tasks.
20. How would you promote a safety culture on-site?
- Lead by example.
- Recognize safe behavior.
- Encourage worker participation in safety programs.
- Maintain open communication.
Hazard-Specific Questions
21. What are the risks of working at heights, and how do you mitigate them?
Risks: Falls, dropped objects.
Controls: Guardrails, harnesses, safety nets, toe boards.
22. How do you ensure trenching and excavation safety?
- Slope, shore, or shield trenches.
- Conduct daily inspections.
- Keep spoil piles at least 2 feet from the edge.
23. What precautions are needed for confined space entry?
- Permit-required system.
- Air quality testing.
- Attendant on standby.
- Rescue plan in place.
24. How do you prevent electrical hazards on-site?
- Use GFCI outlets.
- Inspect cords for damage.
- Maintain safe distances from power lines.
- Lockout/Tagout (LOTO) procedures.
25. What are the dangers of silica dust, and how do you control exposure?
Dangers: Lung cancer, silicosis.
Controls: Wet cutting, ventilation, respirators, worker training.
Behavioral & Situational Questions
26. Describe a time you resolved a safety conflict between workers.
Example: Two workers argued over PPE use. I explained the risks, provided alternatives, and enforced compliance.
27. Have you ever shut down a project due to safety concerns? Why?
Example: Yes, due to unsafe scaffolding. I halted work until proper guardrails were installed.
28. How do you handle pushback from management on safety costs?
Present data on incident costs vs. prevention savings. Emphasize legal and reputational risks.
29. What would you do if you saw a supervisor ignoring a safety rule?
Address it privately first. If unresolved, escalate to higher management.
30. How do you prioritize safety tasks on a busy site?
Focus on high-risk areas first (heights, excavations, heavy equipment). Use risk assessments to guide priorities.
Regulatory & Documentation
31. What records must a Construction Safety Officer maintain?
- Training logs
- Inspection reports
- Incident investigations
- Safety meeting minutes
- OSHA 300 logs
32. When is an OSHA 300 log required?
For recording work-related injuries/illnesses in companies with 10+ employees.
33. What’s the difference between an OSHA 300, 300A, and 301 form?
- 300: Injury/illness log.
- 300A: Annual summary.
- 301: Detailed incident report.
34. How do you prepare for an OSHA inspection?
- Ensure all records are up to date.
- Conduct internal audits.
- Train workers on their rights.
- Assign a company representative to accompany the inspector.
35. What are the penalties for OSHA violations?
- Willful: Up to $156,259 per violation.
- Serious: Up to $16,131 per violation.
- Repeat: Up to $161,323 per violation.
Technical & Equipment Safety
36. What safety checks are needed for scaffolding?
- Stable footing.
- Guardrails & toe boards.
- Planking integrity.
- No overloading.
37. How do you inspect a fall arrest system?
- Check harnesses for wear.
- Inspect lanyards & anchors.
- Ensure D-rings are secure.
- Verify proper labeling.
38. What are the hazards of crane operations?
- Electrocution from power lines.
- Overloading.
- Swing radius strikes.
- Improper rigging.
39. What is Lockout/Tagout (LOTO), and when is it used?
LOTO prevents accidental equipment startup during maintenance. Required for servicing heavy machinery.
40. How do you ensure forklift safety?
- Operator certification.
- Speed limits.
- Load capacity checks.
- Horn use at blind spots.
Personal Experience & Problem-Solving
41. What certifications do you hold?
Example: OSHA 30, CSP, First Aid/CPR, Fall Protection Competent Person.
42. Describe a safety program you implemented.
Example: Introduced a “Stop Work Authority” policy, reducing incidents by 30%.
43. How do you measure safety program success?
- Reduced incident rates.
- Increased near-miss reporting.
- Audit compliance scores.
44. What’s your approach to safety incentives?
Reward positive behavior (e.g., safety suggestions) rather than just “zero incidents.”
45. How do you handle worker fatigue on long shifts?
- Enforce break schedules.
- Rotate strenuous tasks.
- Monitor for signs of exhaustion.
Final Questions
46. Why do you want to work as a Safety Officer here?
Highlight company reputation, safety culture, and alignment with your experience.
47. What’s your biggest safety accomplishment?
Example: Reduced recordable injuries by 40% at my last site through enhanced training.
48. How do you handle stress in high-risk environments?
Stay organized, prioritize tasks, and maintain clear communication.
49. Where do you see yourself in 5 years?
Example: Advancing to a Regional Safety Manager role.
50. Do you have any questions for us?
Ask about:
- Current safety challenges.
- Safety training budgets.
- Company safety KPIs.
10 Situational Safety Interview Questions and Answers
25 Technical HSE Interview Questions and Answers
Top 20 HSE Interview Questions for Freshers
50 Safety Officer Interview Questions and Answers
101 Safety Officer Interview Questions & Answers (2025 Edition)