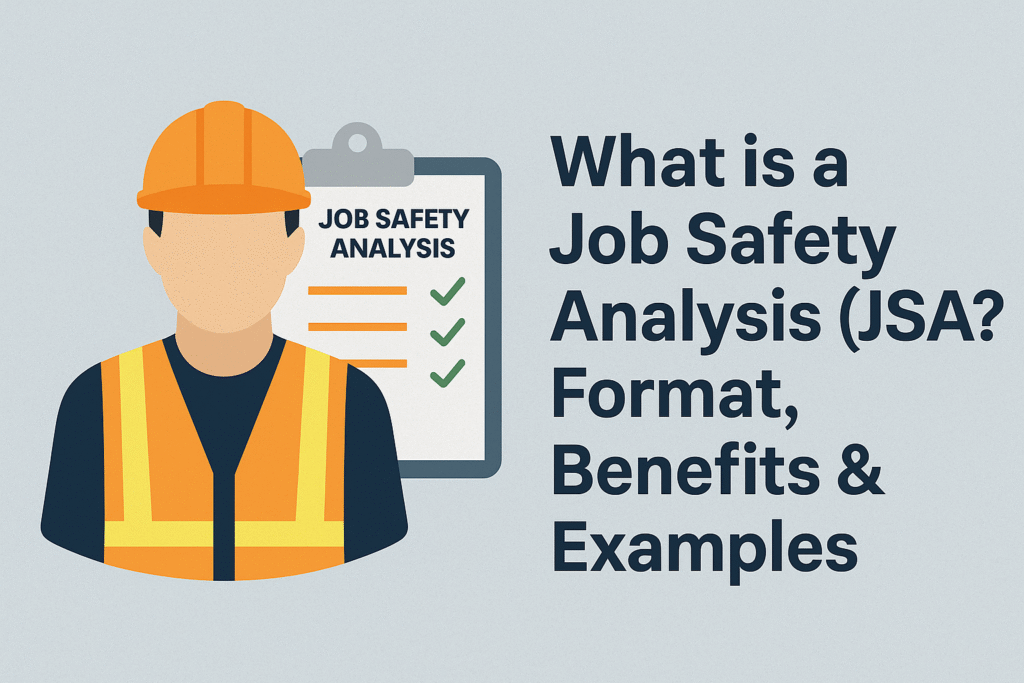
What is a Job Safety Analysis (JSA)? Format, Benefits & Examples
A Job Safety Analysis (JSA) is like the safety blueprint of any job task. Think of it as zooming into a task to uncover every little danger hiding in plain sightābefore it becomes a problem. Itās a process that breaks down a job into steps, identifies hazards at each step, and lays out safety controls to prevent accidents.
Every job has risks, whether itās operating machinery, climbing ladders, or mixing chemicals. JSA helps you see these risks before they hurt someone.
Understanding the Purpose of JSA
A JSA isnāt just about ticking a compliance boxāitās a proactive safety tool.
Preventing Workplace Accidents
By systematically identifying hazards, companies can reduce injuries and create a safer work environment.
Improving Task Efficiency
Surprisingly, JSAs donāt just make work saferāthey make it smarter. Analyzing each step of a job can highlight unnecessary or risky actions that can be improved or removed.
Legal and Regulatory Compliance
Regulatory bodies like OSHA expect employers to assess and manage risks. JSA supports compliance, helping companies avoid fines and legal issues.
When and Where Should JSA Be Conducted?
Not every task needs a JSA, but itās a must in the following cases:
- High-risk jobs like confined space entry, working at heights, or hot work.
- New jobs where hazards arenāt fully understood yet.
- Modified tasks after equipment changes or process updates.
- After an incident or near miss, to prevent recurrence.
Who Should Be Involved in a JSA?
Creating a JSA shouldnāt be a solo job. Itās most effective when itās a team effort.
- Supervisors understand the job requirements.
- Employees know the actual ground-level realities.
- Safety officers bring technical hazard-identification expertise.
Combining these views leads to a more accurate and practical analysis.
Step-by-Step Process of Job Safety Analysis
Step 1 ā Select the Job to Be Analyzed
Choose a task that has a history of incidents, is new, or is considered high-risk.
Step 2 ā Break Down the Job into Steps
Identify all steps in the order they are performed. Keep it simple and logical.
Example: For ladder use ā 1. Carry ladder to location, 2. Inspect ladder, 3. Set up ladder, 4. Climb ladder, 5. Perform task, 6. Descend and store ladder.
Step 3 ā Identify Hazards for Each Step
Think: What could go wrong here?
- Slips
- Trips
- Falls
- Equipment failure
- Exposure to chemicals
Step 4 ā Determine Preventive Measures
For each hazard, list how to eliminate or control it.
- PPE
- Engineering controls
- Administrative actions
- Safe work procedures
Step 5 ā Record and Review the JSA
Document your findings in a standard format and review regularly.
Format of a JSA Document
A typical JSA form includes:
Job Step | Potential Hazard | Recommended Control Measures |
---|---|---|
Climb ladder | Fall from height | Use safety harness, inspect ladder before use |
Use power tool | Electric shock | Check insulation, wear rubber gloves |
Other sections may include:
- Job title
- Date
- Names of contributors
- PPE requirements
- Emergency procedures
Real-Life Example of a JSA
Example ā JSA for Ladder Use
Step | Hazard | Control |
---|---|---|
Setting ladder | Unstable ground | Use ladder with slip-resistant base |
Climbing ladder | Fall | Maintain 3-point contact, donāt overreach |
Working on ladder | Falling tools | Use tool belt or tether |
Example ā JSA for Welding Work
Step | Hazard | Control |
---|---|---|
Connecting cables | Electric shock | Turn off power before handling |
Welding | Burns, UV exposure | Use PPE: gloves, face shield, flame-resistant clothing |
Benefits of Conducting JSA
- Fewer injuries and incidents
- Better communication between workers and management
- Higher productivity due to fewer delays from accidents
- Improved employee moraleāthey feel heard and protected
- Useful training tool for new employees
Common Mistakes to Avoid in JSA
- Being too vagueāHazards and controls should be specific.
- Using outdated informationāRegular reviews are a must.
- Excluding employeesāThey know the real risks firsthand.
- Not using the JSAāIt should be a living document, not a shelf warmer.
Difference Between JSA, JHA, and Risk Assessment
- JSA (Job Safety Analysis): Focuses on identifying hazards in each step of a job.
- JHA (Job Hazard Analysis): Basically another name for JSAāused interchangeably.
- Risk Assessment: Broader process that includes risk evaluation, prioritization, and mitigation strategies for all tasks, not just one job.
JSA in Different Industries
Construction
Crucial for scaffold setup, lifting operations, and trenching.
Oil & Gas
Used daily for permit-to-work systems, especially in drilling and shutdowns.
Manufacturing
Helps prevent injuries during machine maintenance and chemical handling.
Legal Compliance and Standards
OSHA (Occupational Safety and Health Administration) doesnāt mandate JSA specifically but expects employers to analyze and control hazards.
OSHA 29 CFR 1910 and 1926 cover general industry and construction safety obligations.
How to Train Your Team on JSA
- Conduct toolbox talks using real examples.
- Practice mock JSA creation.
- Encourage questions and open feedback.
- Review past incident reports and link them to poor or missing JSAs.
Conclusion
A Job Safety Analysis isnāt just paperworkāitās a life-saving tool. When done right, it empowers teams, prevents injuries, boosts productivity, and keeps your site legally compliant. Whether you’re a seasoned safety professional or just starting out, mastering JSA is one of the smartest moves you can make. Donāt wait for an accident to get serious about itābe proactive, stay prepared, and keep everyone safe.
What is Risk Assessment? Step-by-Step Guide with Real Examples
Demolition Work Risk Assessment
Formwork and Shuttering Risk Assessment
Concrete Pouring Risk Assessment
Reinforcement Steel Fixing Risk Assessment
FAQs
1. What is the difference between JSA and HIRA?
JSA focuses on job-specific hazards step-by-step, while HIRA (Hazard Identification and Risk Assessment) looks at broader risks across a site or operation.
2. Can a fresher safety officer conduct a JSA?
Yes, if theyāre trained and guided by experienced professionals. Itās a great learning tool too.
3. How often should JSAs be updated?
At least annually, or whenever thereās a change in equipment, procedure, or after an incident.
4. Is JSA mandatory under OSHA?
Not specifically, but OSHA requires hazard assessments and controlsāwhich JSA helps fulfill.
5. What are the key components of a good JSA?
Clear job steps, specific hazards, practical control measures, and team collaboration.