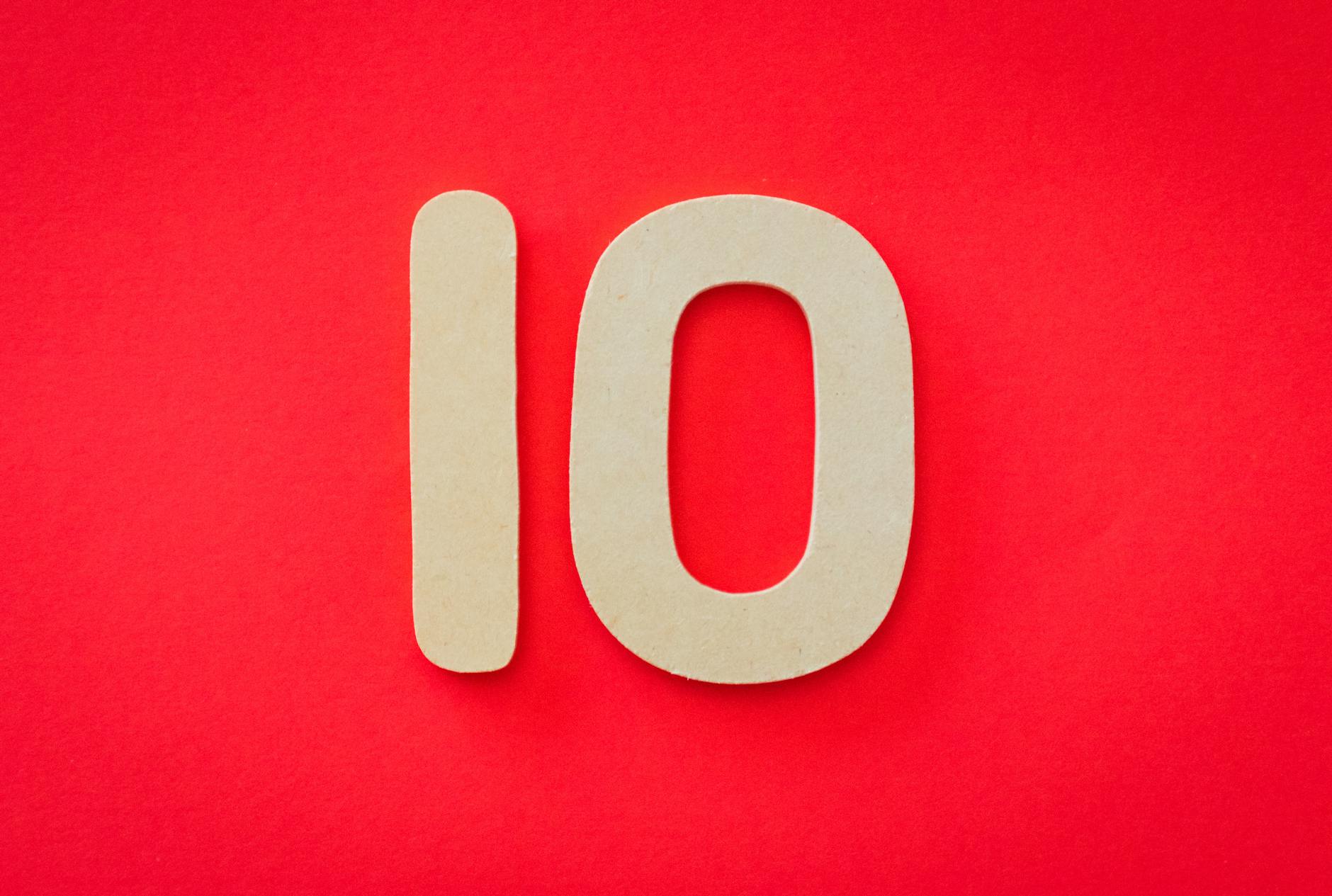
10 Principles of Kaizen
Kaizen, a Japanese term meaning “change for better,” refers to the philosophy of continuous improvement. It’s a systematic approach to achieving small, incremental changes in processes, products, or services over time. This article delves into the ten fundamental principles of Kaizen and how they can revolutionize organizational efficiency and effectiveness.
1. Continuous Improvement
At the core of Kaizen lies the principle of continuous improvement. It emphasizes the need for ongoing efforts to enhance processes, systems, and behaviors. Instead of seeking perfection in one giant leap, Kaizen advocates for small, incremental changes that accumulate over time, leading to significant improvements.
2. Standardization
Standardization ensures consistency and reliability in processes. By establishing standardized procedures, organizations can minimize variations, reduce errors, and enhance efficiency. Kaizen encourages the creation and adherence to standardized work practices to streamline operations and drive continuous improvement.
3. Elimination of Waste
Kaizen aims to eliminate waste in all its forms, including overproduction, unnecessary inventory, defects, waiting time, excessive motion, and underutilized talent. By identifying and eliminating waste, organizations can optimize resources, improve productivity, and deliver greater value to customers.
4. Empowerment of Employees
Kaizen emphasizes the importance of empowering employees at all levels to contribute to the improvement process. By involving workers in decision-making and problem-solving, organizations can harness their creativity, expertise, and insights to drive meaningful change and innovation.
5. Flexibility
Flexibility is essential for adapting to changing market conditions, customer preferences, and technological advancements. Kaizen encourages organizations to embrace flexibility in their processes, systems, and strategies to remain agile and responsive in dynamic environments.
6. Teamwork
Collaboration and teamwork are integral to the success of Kaizen initiatives. By fostering a culture of collaboration, organizations can leverage the collective intelligence and capabilities of teams to tackle complex challenges, generate innovative solutions, and drive continuous improvement.
7. Just-in-Time Delivery
Just-in-time delivery involves delivering products or services exactly when they are needed, neither too early nor too late. Kaizen promotes the implementation of just-in-time principles to minimize inventory costs, reduce lead times, and enhance overall efficiency and responsiveness.
8. Automation
Automation plays a crucial role in streamlining processes, reducing manual labor, and increasing efficiency. Kaizen encourages the judicious use of automation technologies to eliminate repetitive tasks, improve accuracy, and free up resources for more value-added activities.
9. Quality Focus
Quality is paramount in Kaizen philosophy. Organizations are encouraged to prioritize quality in all aspects of their operations, from product design and development to manufacturing and customer service. By focusing on quality, organizations can enhance customer satisfaction, build brand loyalty, and drive long-term success.
10. Customer Satisfaction
Ultimately, the goal of Kaizen is to meet and exceed customer expectations. By consistently delivering high-quality products and services that meet customer needs and preferences, organizations can build trust, loyalty, and satisfaction, driving sustainable growth and success.
Conclusion
In conclusion, the principles of Kaizen offer a powerful framework for driving continuous improvement and organizational excellence. By embracing these principles and integrating them into their operations, organizations can enhance efficiency, quality, and customer satisfaction while fostering a culture of innovation and collaboration. Kaizen is not just a methodology; it’s a mindset that empowers organizations to adapt, evolve, and thrive in today’s rapidly changing business landscape.
Mobile Equipment Safety: Prioritizing Operator Training and Maintenance Practices
Zero Harm Culture: Nurturing a Safety Mindset in the Workplace
Chemical Hygiene in Laboratories: Promoting Safe Handling and Storage Practices
Radiation Monitoring: Safeguarding Environments through Dosimetry and Contamination Control
FAQs (Frequently Asked Questions)
1. Is Kaizen only applicable to manufacturing industries?
Kaizen principles can be applied to any industry or sector, including healthcare, services, and technology. The core philosophy of continuous improvement is universally applicable.
2. How long does it take to see results from Kaizen initiatives?
The timeline for seeing results from Kaizen initiatives varies depending on the nature of the improvements and the scale of implementation. However, organizations often start experiencing benefits within a few months of initiating Kaizen projects.
3. What role does leadership play in implementing Kaizen?
Leadership commitment and support are crucial for the successful implementation of Kaizen. Leaders need to champion the philosophy, provide resources, and create a culture that encourages experimentation, innovation, and continuous improvement.
4. How can organizations overcome resistance to change when implementing Kaizen?
Effective communication, employee involvement, and education are key strategies for overcoming resistance to change. By involving employees in the improvement process, addressing their concerns, and highlighting the benefits of Kaizen, organizations can foster buy-in and engagement.
5. Are there any limitations to Kaizen?
While Kaizen offers numerous benefits, it’s not without its challenges. Cultural barriers, resistance to change, and resource constraints can hinder the successful implementation of Kaizen initiatives. However, with proper planning, leadership support, and employee engagement, these challenges can be overcome.