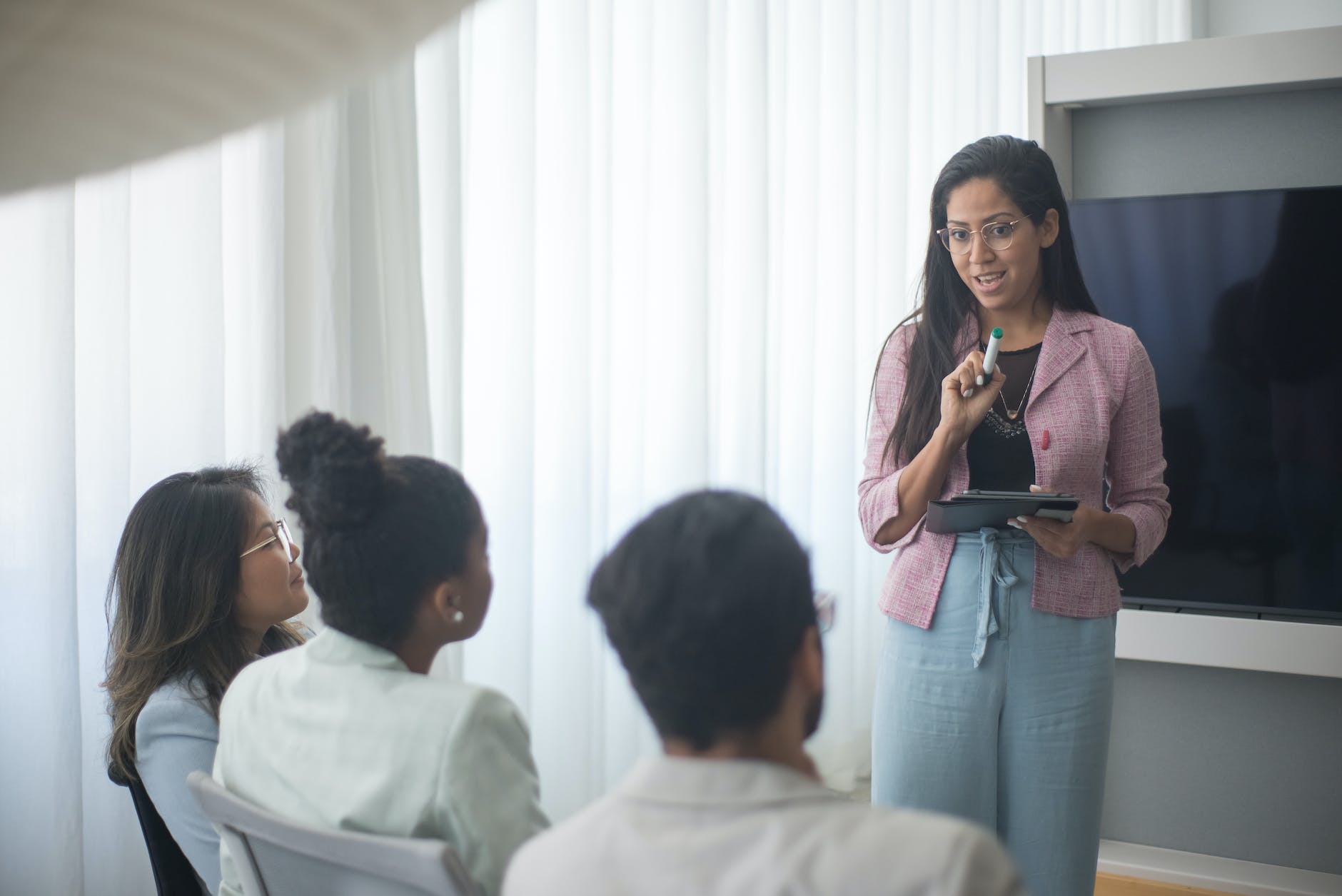
20 Safety Training Topics for Your Workplace
20 Safety Training Topics for Your Workplace : Workplace safety is a paramount concern for both employers and employees. Ensuring a safe work environment not only protects the well-being of the workforce but also minimizes accidents, reduces downtime, and complies with legal requirements. In this article, we’ll delve into 20 crucial safety training topics that every workplace should consider.
1. Introduction
Maintaining a safe workplace is vital to the success of any business. Employers have a responsibility to provide their workers with a safe and healthy working environment. Safety training is a proactive approach to prevent accidents and injuries, making it an essential component of every organization.
2. The Importance of Safety Training
Safety training instills knowledge and awareness among employees, empowering them to identify and mitigate potential hazards. It promotes a culture of safety within the workplace, reducing the likelihood of accidents and injuries.
3. Legal Requirements for Workplace Safety
Various regulations and standards, such as OSHA in the United States, require employers to provide safety training. Failure to comply with these regulations can result in fines and legal consequences.
4. Creating a Safe Work Environment
To ensure workplace safety, organizations should establish robust safety policies and procedures. They should also have emergency response plans in place, provide necessary safety equipment and gear, and regularly inspect and maintain the workplace for safety.
- Safety Policies and Procedures: Developing clear and accessible safety policies and procedures helps guide employees on safety protocols.
- Emergency Response Plans: Having a well-defined plan for emergencies like fires, natural disasters, or accidents is crucial.
- Safety Equipment and Gear: Providing employees with the right safety equipment, such as helmets, gloves, and goggles, is essential.
5. Safety Training Topics
General Safety Training
- Understanding Workplace Hazards
- Reporting Unsafe Conditions
- Safety Communication
Hazardous Materials Handling
- Identification of Hazardous Materials
- Safe Handling and Storage
- Emergency Response
First Aid and CPR
- Basic First Aid Techniques
- Cardiopulmonary Resuscitation (CPR)
- Automated External Defibrillator (AED) Usage
Fire Safety
- Fire Prevention
- Fire Extinguisher Use
- Evacuation Procedures
Electrical Safety
- Electrical Hazards Awareness
- Safe Electrical Practices
Machine and Equipment Safety
- Machine Operation Safety
- Lockout/Tagout Procedures
Fall Protection
- Fall Hazards Recognition
- Proper Use of Fall Protection Equipment
Chemical Safety
- Hazardous Chemical Identification
- Safe Handling and Storage of Chemicals
20 Safety Training Topic
General Safety Training
- Understanding Workplace Hazards:
- In this training, employees learn to recognize potential hazards in their workplace. This includes identifying anything that could cause harm, such as slippery floors, exposed wires, or heavy machinery.
- Reporting Unsafe Conditions:
- Employees are educated on the importance of reporting any unsafe conditions or hazards they encounter. This encourages a proactive approach to safety and helps prevent accidents.
- Safety Communication:
- Effective communication is essential in ensuring workplace safety. This training emphasizes the significance of clear and concise communication to alert colleagues about dangers and emergencies.
Hazardous Materials Handling
- Identification of Hazardous Materials:
- Employees are taught how to identify hazardous materials, such as chemicals, in the workplace. This includes understanding labels, safety data sheets, and warning signs.
- Safe Handling and Storage:
- This training covers the proper procedures for handling, storing, and disposing of hazardous materials to minimize the risk of accidents and exposure to harmful substances.
- Emergency Response:
- In the event of a hazardous material spill or accident, employees should know how to respond. This includes evacuation procedures, containment measures, and contacting emergency services.
First Aid and CPR
- Basic First Aid Techniques:
- Employees learn basic first aid skills, including how to administer first aid for common injuries such as cuts, burns, and sprains. This can make a significant difference in the outcome of workplace accidents.
- Cardiopulmonary Resuscitation (CPR):
- CPR training teaches employees how to perform life-saving techniques in cases of cardiac arrest or respiratory distress. Quick and effective CPR can significantly increase the chances of survival.
- Automated External Defibrillator (AED) Usage:
- AEDs are devices used to restart a person’s heart in case of sudden cardiac arrest. Training on AED usage can be critical in saving lives.
Fire Safety
- Fire Prevention:
- Employees learn how to prevent fires by identifying potential fire hazards and taking measures to reduce the risk. This can include proper storage of flammable materials and safe electrical practices.
- Fire Extinguisher Use:
- Training on the correct use of fire extinguishers ensures that employees can respond effectively if a fire breaks out. They learn how to select the right extinguisher and use it safely.
- Evacuation Procedures:
- In case of a fire, employees should know how to evacuate safely. This training covers evacuation routes, assembly points, and the importance of staying calm during an emergency.
Electrical Safety
- Electrical Hazards Awareness:
- This training focuses on identifying electrical hazards in the workplace, such as exposed wiring or malfunctioning equipment. It emphasizes the importance of reporting these hazards promptly.
- Safe Electrical Practices:
- Employees are educated on safe electrical practices, including proper use of outlets, electrical equipment, and the importance of using appropriate personal protective equipment (PPE) when working with electricity.
Machine and Equipment Safety
- Machine Operation Safety:
- Employees learn the safe operation of machines and equipment in the workplace. This includes understanding safety features, proper usage, and the importance of regular maintenance.
- Lockout/Tagout Procedures:
- Lockout/tagout procedures are essential for preventing the unexpected startup of machinery during maintenance or repair. This training covers the correct steps to isolate and secure equipment.
Fall Protection
- Fall Hazards Recognition:
- Employees are trained to identify potential fall hazards, such as unprotected edges, slippery surfaces, or unstable platforms.
- Proper Use of Fall Protection Equipment:
- This training covers the correct use of fall protection gear like harnesses and lifelines to prevent or minimize injuries in case of a fall.
Chemical Safety
- Hazardous Chemical Identification:
- Employees learn how to identify hazardous chemicals, understand safety data sheets, and recognize warning labels to avoid accidents and exposure.
- Safe Handling and Storage of Chemicals:
- Training on the safe handling and storage of chemicals ensures employees know how to work with potentially dangerous substances without risk to their health or safety.
Each of these training topics is essential to ensuring workplace safety. They equip employees with the knowledge and skills necessary to prevent accidents and respond effectively in emergencies.
6. Tailoring Training to Your Workplace
It’s essential to customize safety training to suit the specific risks and challenges of your workplace. Generic training may not cover all the potential hazards your employees could encounter.
7. Ongoing Safety Training
Safety training is not a one-time event. Continuous training and refresher courses are crucial to keep employees updated on new safety procedures, equipment, and regulations.
8. Conclusion
Prioritizing workplace safety through comprehensive training is a responsibility that benefits both employers and employees. It reduces accidents, increases productivity, and ensures compliance with legal requirements.
What is Safety Induction Training?
Safety Induction Training for New Employees
Health and Safety Induction for New Employees
How To Conduct Safety Induction
Frequently Asked Questions
1. Are there legal requirements for safety training in workplaces?
Yes, many countries have regulations and standards that require employers to provide safety training to their employees.
2. How can I tailor safety training to my specific workplace needs?
You can assess the unique risks in your workplace and customize training to address those specific hazards.
3. Why is ongoing safety training important?
Ongoing training ensures that employees are continually aware of safety procedures and can adapt to new safety requirements.
4. What should I do if an employee refuses to participate in safety training?
It’s essential to communicate the importance of safety training and address any concerns or misconceptions the employee may have.
5. Can safety training really reduce workplace accidents?
Yes, comprehensive safety training significantly reduces the likelihood of workplace accidents and injuries.