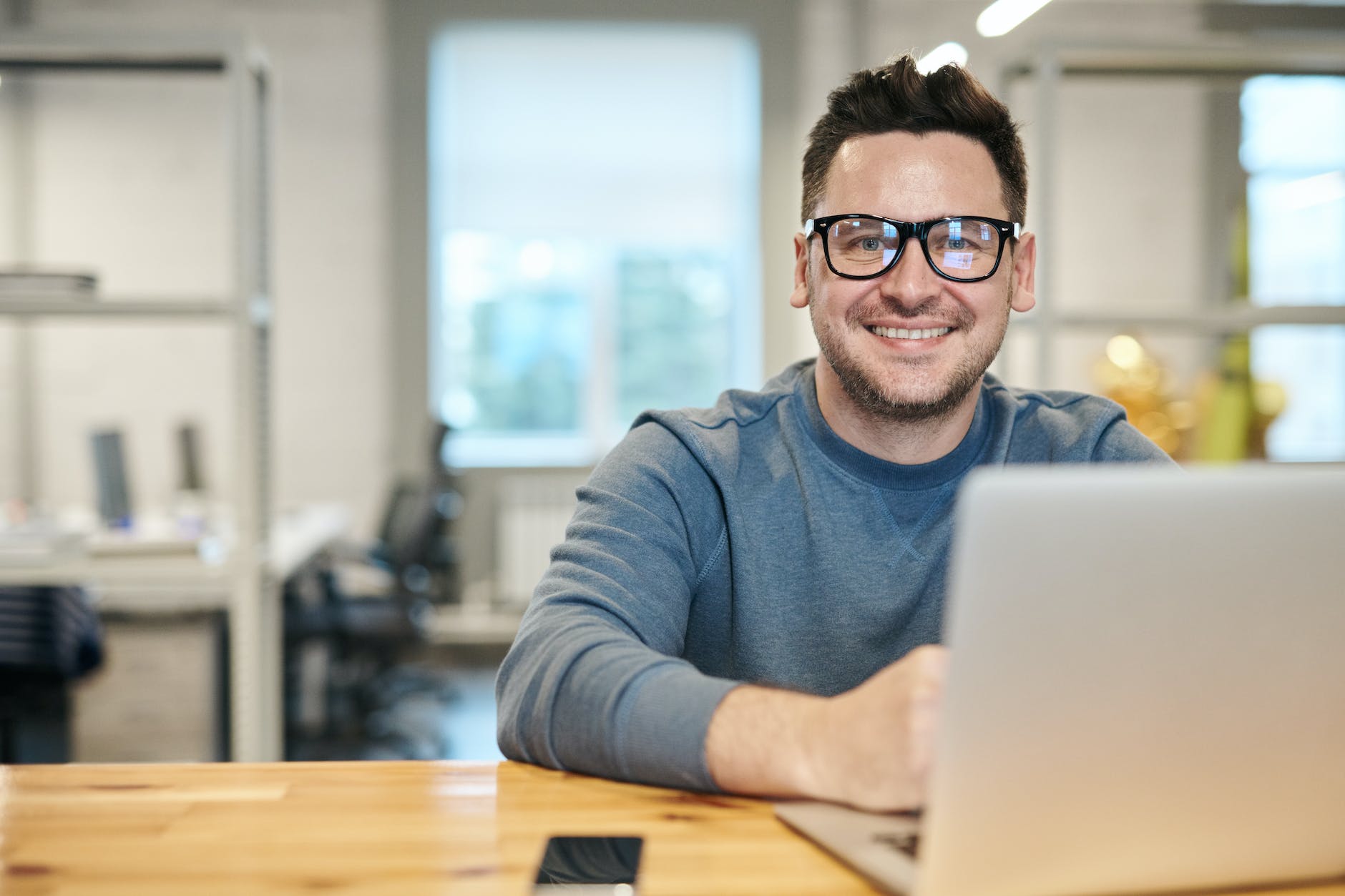
50 Duties of Safety Inspector
50 Duties of Safety Inspector : Safety inspectors play a pivotal role in ensuring the well-being of individuals within various industries. Their expertise and diligence contribute significantly to maintaining safe working environments.
The Role and Importance of Safety Inspectors
Defining the Role Safety inspectors are tasked with assessing workplaces to identify potential hazards, ensuring compliance with safety regulations, and recommending corrective actions.
Significance in Various Industries From construction sites to healthcare facilities, safety inspectors are indispensable. They safeguard employees, visitors, and the general public from potential risks.
Qualifications and Skills Required
Educational Background Typically, safety inspectors possess degrees in occupational health and safety or related fields. Certifications and ongoing training bolster their expertise.
Essential Skills Strong attention to detail, analytical thinking, communication, and a deep understanding of safety protocols are imperative for success in this role.
Key Duties and Responsibilities
Conducting Site Inspections Inspectors regularly visit workplaces, meticulously examining equipment, processes, and adherence to safety protocols. They document findings and suggest improvements.
Implementing Safety Regulations They ensure compliance with local and federal safety regulations, implementing measures to mitigate risks and maintain a safe environment.
Training and Education Initiatives Safety inspectors conduct training sessions, educating employees about safety practices and emergency procedures.
Challenges Faced by Safety Inspectors
Balancing Compliance and Productivity Striking a balance between enforcing safety standards and minimizing disruptions to workflow poses a constant challenge.
Evolving Safety Standards With technological advancements and changing work environments, safety inspectors must adapt swiftly to new regulations and practices.
Here are 50 duties commonly associated with a safety inspector:
- Inspect workplaces regularly for compliance with safety regulations.
- Identify potential hazards in the workplace.
- Evaluate machinery and equipment to ensure they meet safety standards.
- Conduct safety audits and inspections.
- Develop and implement safety procedures and protocols.
- Train employees on safety practices and procedures.
- Investigate accidents and incidents to determine causes and prevent recurrence.
- Recommend safety improvements to management.
- Review and analyze safety data and reports.
- Ensure proper use and maintenance of safety equipment.
- Collaborate with management to address safety concerns.
- Conduct risk assessments and hazard analyses.
- Monitor and enforce compliance with safety policies.
- Provide guidance on emergency procedures.
- Keep abreast of changes in safety regulations and standards.
- Participate in safety committees or meetings.
- Conduct safety briefings and toolbox talks.
- Inspect fire suppression systems and emergency exits.
- Assess the effectiveness of safety programs.
- Investigate employee complaints related to safety.
- Develop safety protocols for specific tasks or job roles.
- Perform ergonomic assessments to prevent injuries.
- Ensure proper handling and storage of hazardous materials.
- Collaborate with medical professionals for health-related safety concerns.
- Evaluate personal protective equipment (PPE) requirements.
- Conduct safety training for new hires.
- Inspect electrical systems for safety compliance.
- Verify compliance with OSHA or other regulatory agencies.
- Investigate near-miss incidents and potential hazards.
- Review and update safety manuals and documentation.
- Conduct safety walkthroughs and observations.
- Verify the effectiveness of safety signage.
- Provide recommendations for safety-related purchases or upgrades.
- Coordinate safety drills and exercises.
- Assess workplace lighting for safety.
- Monitor air quality and ventilation systems.
- Develop safety protocols for hazardous work environments.
- Review and approve safety permits.
- Investigate safety concerns raised by employees.
- Collaborate with engineers for safety design considerations.
- Conduct safety seminars or workshops.
- Ensure compliance with environmental safety regulations.
- Monitor and report on safety performance metrics.
- Evaluate safety training effectiveness.
- Provide guidance during equipment installations for safety considerations.
- Perform safety inspections during construction or renovation projects.
- Review incident reports and recommend corrective actions.
- Coordinate with contractors for safety compliance.
- Conduct safety reviews for new processes or procedures.
- Develop and maintain a culture of safety in the workplace.
Conclusion
Safety inspectors are the guardians of workplace safety. Their commitment to upholding standards and adapting to advancements ensures a safer future for all.
Fresher Safety Supervisor Salary
Fresher Safety Engineer Salary
FAQs
- What industries do safety inspectors typically work in?Safety inspectors are found across various industries such as construction, manufacturing, healthcare, transportation, oil and gas, and more. Their expertise is crucial in any field where occupational hazards exist.
- Are there any specific software or tools used by safety inspectors?Safety inspectors utilize a range of tools and software to enhance their inspections. These can include inspection checklists, safety management software, data analysis tools, and even specialized equipment depending on the industry.
- How often should workplace inspections be conducted?The frequency of workplace inspections varies based on several factors including industry standards, regulations, and the nature of the workplace. Generally, regular inspections, ranging from weekly to annually, are conducted to ensure ongoing safety.
- What are the consequences of non-compliance with safety regulations?Non-compliance with safety regulations can result in severe consequences including legal penalties, fines, work stoppages, injuries, and even loss of life. It can also tarnish a company’s reputation and trust within the industry.
- Can a company appoint an internal safety inspector?Absolutely, many companies appoint internal safety inspectors who are trained and dedicated to ensuring workplace safety. These individuals often have a profound understanding of the specific safety needs within their organization.