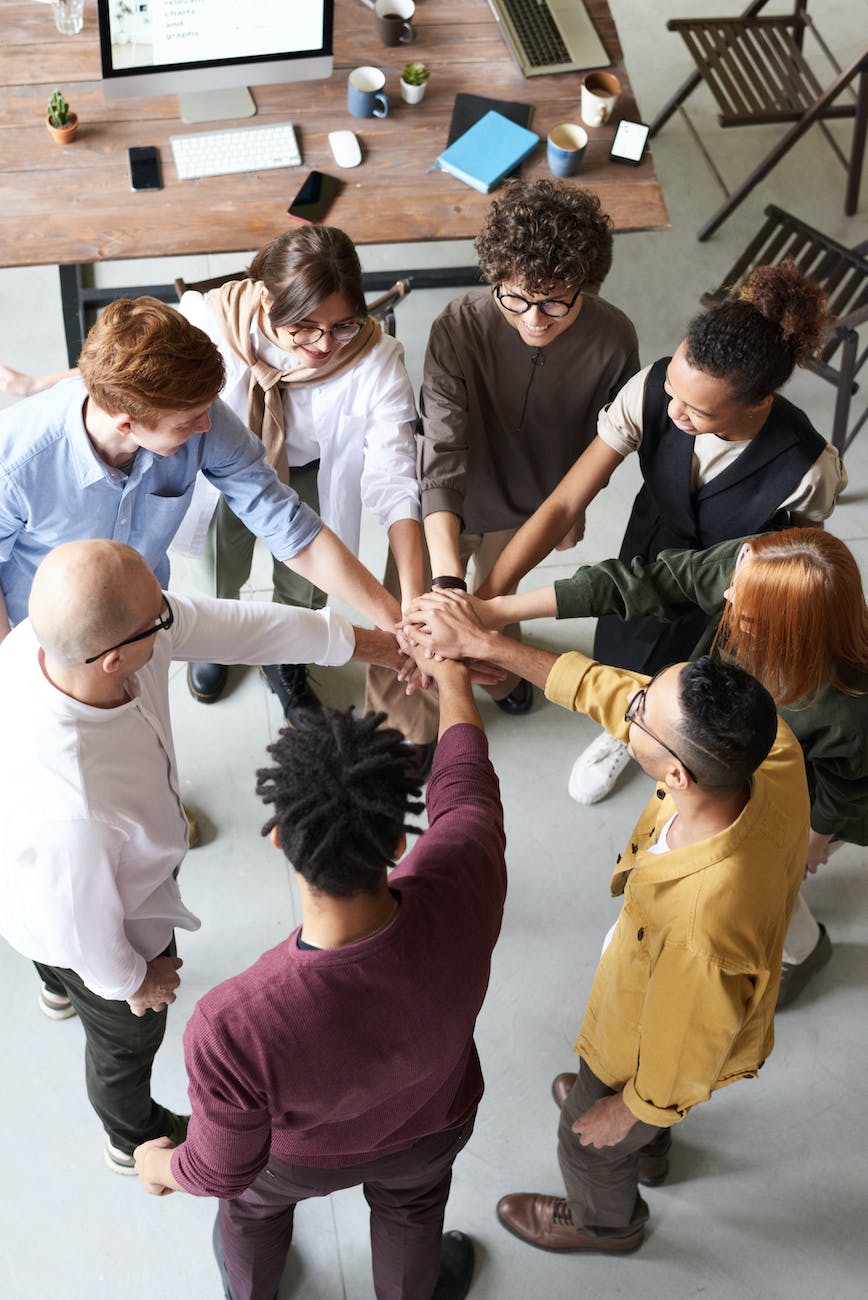
5S Principles in the Workplace
Introduction
5S Principles in the Workplace : In the fast-paced world of business, efficiency and productivity are key factors that determine the success of any organization. The 5S principles, a systematic approach to workplace organization and cleanliness, have emerged as a powerful tool in achieving these goals. This article will delve into the world of 5S, explaining the principles and demonstrating how they can revolutionize the workplace for the better.
What are the 5S Principles?
The 5S principles, derived from five Japanese words – Seiri (Sort), Seiton (Set in Order), Seiso (Shine), Seiketsu (Standardize), and Shitsuke (Sustain) – provide a structured methodology for organizing and optimizing a workspace. These principles promote a clean and efficient work environment that fosters productivity and teamwork.
The Origin of 5S
The 5S methodology originated in Japan and was popularized by Toyota as a key component of the Toyota Production System (TPS). It has since spread worldwide, becoming a cornerstone of lean manufacturing and continuous improvement strategies.
Sort (Seiri)
Importance of Sorting
Sorting (Seiri) is the first step in the 5S process, involving the removal of unnecessary items from the workplace. This process eliminates clutter and minimizes distractions, enabling employees to focus on essential tasks.
How to Implement Sorting
Implementing sorting requires a systematic approach to categorize items into essential and non-essential, then removing what is not needed. This process streamlines the workspace, creating a foundation for the subsequent steps.
Set in Order (Seiton)
Benefits of Setting in Order
Setting in order (Seiton) involves arranging necessary items in a logical and organized manner. This step reduces the time wasted searching for tools and materials, improving efficiency and reducing errors.
Organizing Your Workspace
Effective organization ensures that everything has a designated place. Tools and materials should be stored in an accessible and easily identifiable manner, contributing to a smoother workflow.
Shine (Seiso)
Significance of Shining
Shining (Seiso) emphasizes the need for cleanliness and maintenance in the workplace. A clean workspace not only enhances the visual appeal but also prevents accidents and equipment breakdowns.
Maintaining Cleanliness
Regular cleaning schedules and practices are key to maintaining a shining workplace. Employees should be encouraged to participate in this ongoing process.
Standardize (Seiketsu)
Why Standardization Matters
Standardization (Seiketsu) focuses on creating consistent processes and practices. This ensures that the gains made in sorting, setting in order, and shining are maintained over time.
Creating Consistency
Checklists, visual aids, and clear procedures help standardize work practices, making it easier for employees to follow the established standards.
Sustain (Shitsuke)
Sustaining the Gains
Sustaining (Shitsuke) is about embedding the 5S principles into the organization’s culture. This step ensures that the improvements made are lasting and continue to evolve.
Cultivating a Culture of Continuous Improvement
Training, regular audits, and employee involvement are essential to sustaining the gains and fostering a culture of continuous improvement.
The 5S Methodology in Various Industries
The 5S principles are versatile and can be applied to various industries, from manufacturing and healthcare to office settings. The adaptability of the methodology makes it a valuable tool for organizations seeking to improve their operations.
5S and Lean Manufacturing
The synergy between 5S and lean manufacturing is powerful. Lean principles aim to eliminate waste, and 5S is a foundational element in achieving this goal by reducing unnecessary actions, materials, and space.
Conclusion
In conclusion, the 5S principles provide a structured and effective approach to workplace organization and efficiency. By sorting, setting in order, shining, standardizing, and sustaining, organizations can create a workspace that fosters productivity, safety, and continuous improvement.
Workplace Safety Toolbox Talk Meeting
How to Promote a Safe Workplace
Frequently Asked Questions
- What is the primary goal of the 5S methodology?The primary goal of the 5S methodology is to create a clean, organized, and efficient workplace. It aims to eliminate waste, improve productivity, enhance safety, and foster a culture of continuous improvement within an organization.
- How can I get started with implementing 5S in my workplace?Getting started with 5S involves a few key steps. First, educate your team about the 5S principles. Then, assess your current workspace, identify areas that need improvement, and develop a plan for implementation. Engage employees in the process, start with sorting, and gradually work through each of the 5S steps. Regular audits and continuous improvement efforts are crucial for success.
- What are the key challenges in sustaining 5S practices?Sustaining 5S practices can be challenging due to factors like employee resistance, lack of commitment, and changing work environments. To overcome these challenges, it’s essential to provide ongoing training, involve employees in decision-making, conduct regular audits, and celebrate successes. Creating a culture of continuous improvement is key to long-term sustainability.
- How does 5S relate to other quality improvement methodologies?5S is often considered a foundational element of many quality improvement methodologies, including lean manufacturing and Six Sigma. It complements these methodologies by providing a systematic approach to organizing the workplace, reducing waste, and ensuring consistent processes.
- Can the 5S principles be applied to non-manufacturing industries?Yes, absolutely! The 5S principles are highly adaptable and can be applied to a wide range of industries beyond manufacturing. They have proven effective in healthcare, offices, retail, and service sectors. Any organization seeking to improve efficiency, reduce waste, and create a safer and more organized workspace can benefit from implementing 5S.