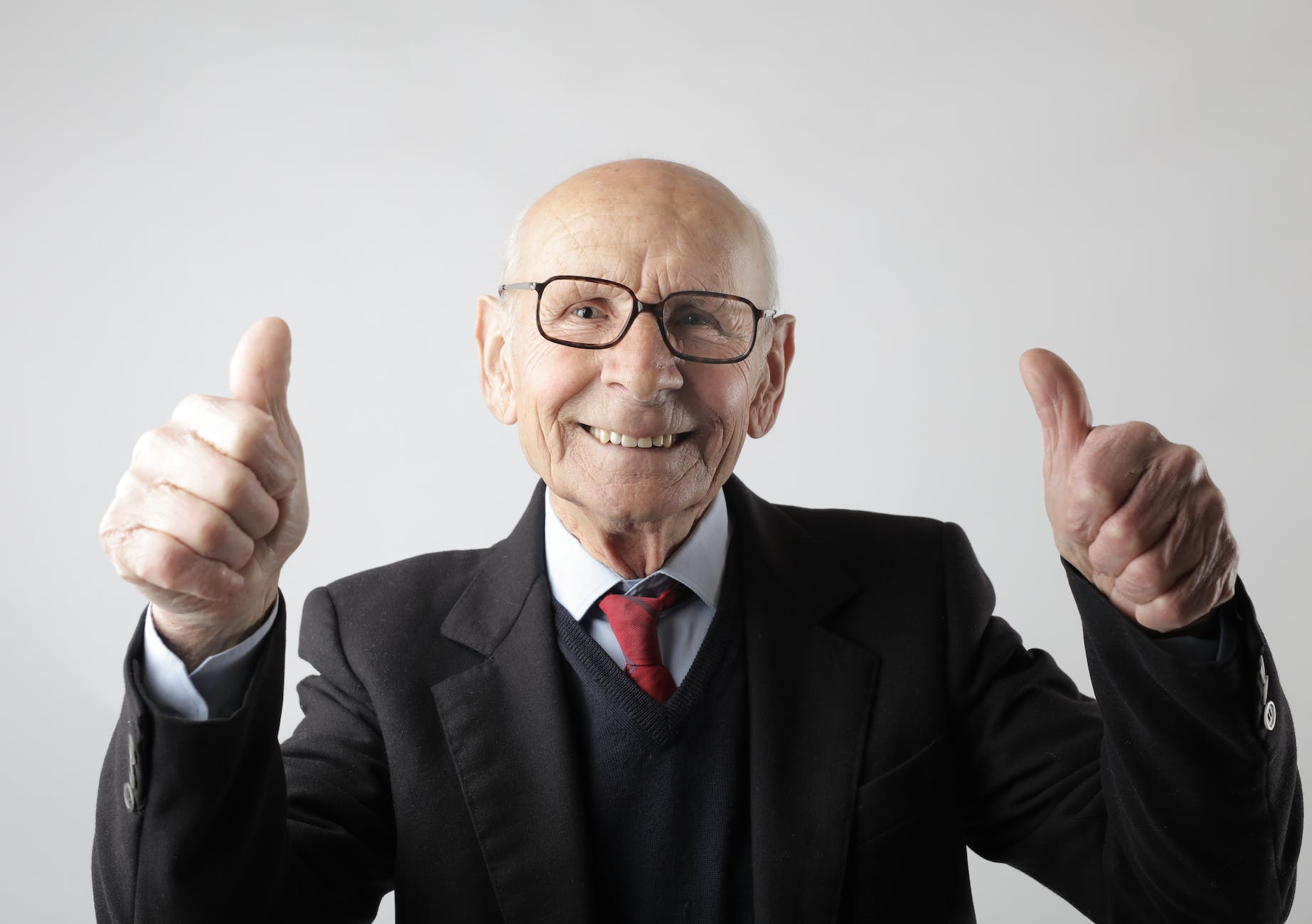
61 Duties of a HSE Manager You Must Know
Safety in the workplace is paramount, and at the forefront of ensuring a secure work environment is the Health, Safety, and Environment (HSE) Manager. This role carries a multitude of responsibilities that go beyond traditional safety protocols. In this article, we’ll delve into the 61 duties of an HSE Manager that you must be aware of.
I. Introduction
A. Definition of HSE Manager
The HSE Manager, short for Health, Safety, and Environment Manager, is a professional responsible for overseeing the organization’s safety protocols, environmental initiatives, and health programs.
B. Importance of HSE Managers
HSE Managers play a crucial role in preventing accidents, promoting a culture of safety, and ensuring compliance with health and environmental regulations. Their expertise is vital for maintaining a secure and healthy workplace.
II. Qualifications and Skills
A. Educational background
HSE Managers typically hold degrees in occupational health and safety, environmental science, or related fields. Educational qualifications lay the foundation for understanding the complexities of the role.
B. Certifications
Certifications such as Certified Safety Professional (CSP) or NEBOSH certification add credibility to an HSE Manager’s profile, showcasing their commitment to continuous learning.
C. Soft skills
Apart from technical know-how, effective communication, leadership, and problem-solving skills are essential for an HSE Manager to excel in their role.
III. Core Duties
A. Risk assessments
HSE Managers conduct thorough risk assessments to identify potential hazards in the workplace and develop strategies to mitigate them.
B. Safety inspections
Regular inspections are conducted to ensure compliance with safety standards and to identify areas for improvement.
C. Incident investigations
In the unfortunate event of an accident, HSE Managers lead investigations to determine the root cause and implement corrective measures.
D. Emergency preparedness
HSE Managers develop and implement emergency response plans, ensuring employees are well-prepared for unforeseen events.
IV. Regulatory Compliance
A. Stay updated on regulations
Staying abreast of evolving health, safety, and environmental regulations is crucial for an HSE Manager to ensure organizational compliance.
B. Implementing compliance measures
HSE Managers work proactively to implement measures that align with regulatory requirements, avoiding legal complications.
V. Training Programs
A. Employee training
Conducting regular safety training programs ensures that employees are well-versed in safety protocols and aware of potential risks.
B. Continuous professional development
HSE Managers invest in their team’s professional growth, keeping them updated on the latest safety trends and technologies.
VI. Communication Skills
A. Interdepartmental communication
Effective communication with various departments is essential to implement cohesive safety measures across the organization.
B. Report writing
Clear and concise report writing is a key skill for HSE Managers, enabling them to communicate findings and recommendations effectively.
C. Presentation skills
Conducting training sessions and presenting safety data to stakeholders require strong presentation skills.
VII. Safety Culture Promotion
A. Creating awareness
HSE Managers actively promote a safety culture by creating awareness campaigns and encouraging employees to prioritize safety.
B. Fostering a safety-conscious environment
Building a culture where safety is ingrained in the organization’s values is crucial for long-term success in accident prevention.
VIII. Environmental Management
A. Sustainability initiatives
HSE Managers initiate and oversee sustainability programs to minimize the organization’s environmental footprint.
B. Environmental impact assessments
Conducting assessments helps identify potential environmental impacts, allowing for proactive measures to mitigate them.
IX. Health and Wellness Programs
A. Employee health initiatives
Implementing programs that promote employee health, such as fitness challenges or wellness workshops, contributes to a healthier workplace.
B. Mental health awareness
Recognizing the importance of mental health, HSE Managers incorporate initiatives to address and support employees’ mental well-being.
X. Incident Response
A. Develop response plans
Creating detailed response plans ensures a swift and coordinated reaction to accidents or emergencies.
B. Coordinate emergency drills
Regular drills help prepare employees for real-life emergency situations, reducing panic and improving response times.
XI. Technology Integration
A. Use of safety software
HSE Managers leverage cutting-edge safety software to streamline processes, track incidents, and analyze data for continuous improvement.
B. IoT in safety management
Integration of Internet of Things (IoT) devices enhances real-time monitoring, providing valuable insights into potential safety risks.
XII. Continuous Improvement
A. Analyzing incident data
Regularly analyzing incident data allows HSE Managers to identify trends and implement preventive measures for continuous improvement.
B. Implementing feedback loops
Creating channels for feedback ensures that employees are actively involved in the improvement process, fostering a culture of continuous learning.
XIII. Collaboration with Other Departments
A. Working with HR
Collaborating with Human Resources ensures alignment in employee policies and seamless integration of safety protocols.
B. Coordinating with facilities management
Working closely with facilities management ensures that safety measures are integrated into the physical aspects of the workplace.
XIV. Crisis Management
A. Planning for unforeseen events
Developing comprehensive crisis management plans prepares organizations for unexpected events, minimizing their impact.
B. Crisis communication strategies
Effective communication during crises is paramount; HSE Managers develop strategies to keep stakeholders informed and reassured.
XV. Performance Metrics and Reporting
A. Key performance indicators
Establishing key performance indicators (KPIs) helps measure the effectiveness of safety programs and identify areas for improvement.
B. Annual safety reports
Compiling annual safety reports provides a comprehensive overview of the organization’s safety performance, facilitating strategic planning.
Health, Safety, and Environment (HSE) Managers play a crucial role in ensuring that organizations maintain high standards of safety, health, and environmental practices. Here are 61 duties of an HSE Manager:
- Develop and implement HSE policies and procedures.
- Conduct risk assessments to identify potential hazards.
- Create and deliver HSE training programs for employees.
- Monitor and enforce compliance with HSE regulations.
- Investigate accidents and incidents, and prepare reports.
- Establish emergency response plans and procedures.
- Conduct regular safety audits and inspections.
- Collaborate with departments to ensure HSE integration.
- Manage the HSE budget and allocate resources effectively.
- Keep abreast of new HSE regulations and industry best practices.
- Develop and implement a process for incident reporting.
- Advise management on HSE-related issues.
- Coordinate with external agencies for HSE compliance.
- Implement and manage safety incentive programs.
- Oversee the proper handling and disposal of hazardous materials.
- Monitor workplace conditions to ensure a safe environment.
- Conduct health risk assessments for employees.
- Develop and maintain safety data sheets for chemicals.
- Establish a system for recording and analyzing HSE data.
- Conduct safety meetings and toolbox talks.
- Design and implement safety signage and labeling.
- Evaluate the effectiveness of HSE programs.
- Investigate complaints related to HSE matters.
- Monitor and enforce the use of personal protective equipment.
- Develop and maintain relationships with regulatory agencies.
- Create and update the organization’s safety manual.
- Implement a system for reporting near misses.
- Provide guidance on ergonomics and workplace design.
- Ensure compliance with industrial hygiene standards.
- Coordinate employee wellness programs.
- Develop safety communication strategies.
- Conduct noise level assessments in the workplace.
- Evaluate and select safety equipment and vendors.
- Implement a process for safety drills and exercises.
- Analyze trends in incident data to prevent recurrence.
- Assess contractor compliance with HSE requirements.
- Establish a system for managing contractor safety.
- Review and approve subcontractor safety plans.
- Develop and implement a process for incident investigation.
- Conduct job safety analyses for various tasks.
- Oversee the use and maintenance of safety equipment.
- Develop and implement a process for managing change.
- Conduct safety reviews for new projects and facilities.
- Facilitate safety committees and meetings.
- Coordinate with HR on workers’ compensation claims.
- Evaluate and recommend improvements to work processes.
- Implement a system for monitoring employee health.
- Establish procedures for handling hazardous waste.
- Conduct safety performance evaluations.
- Develop and implement a fire prevention plan.
- Investigate and report on workplace fatalities.
- Monitor and manage air quality in the workplace.
- Establish and maintain a first aid program.
- Develop and implement a process for safety reporting.
- Assess and address physical and mental workplace stressors.
- Implement procedures for handling chemical spills.
- Review and update evacuation plans.
- Establish and monitor safety-related KPIs.
- Conduct safety culture assessments.
- Develop and implement a process for safety incentives.
- Stay informed about emerging HSE technologies and practices.
Conclusion
In conclusion, the role of an HSE Manager goes far beyond traditional safety duties. Their multifaceted responsibilities contribute to fostering a secure, healthy, and compliant work environment. As organizations evolve, HSE Managers play a pivotal role in adapting and implementing innovative strategies for the well-being of both employees and the environment.
How to Become a Certified Safety Officer in 2024?
How to Become a Certified Safety Engineer?
HSE Manager: What is the Qualification Required to Become an HSE Manager?
HSE Engineer: What is the Qualification Required to Become a HSE Engineer?
HSE Supervisor: What is the Qualification Required to Become an HSE Supervisor?
FAQs
- What qualifications does an HSE Manager need?
- HSE Managers typically need a degree in occupational health and safety, environmental science, or a related field, along with relevant certifications.
- How often should safety drills be conducted?
- Safety drills should be conducted regularly to ensure that employees are well-prepared for emergency situations.
- How can HSE Managers promote a safety culture?
- HSE Managers can promote a safety culture by creating awareness campaigns, conducting regular training, and fostering a mindset where safety is a priority.
- Why is crisis management important for HSE Managers?
- Crisis management is crucial for HSE Managers to plan for unforeseen events, minimize their impact, and communicate effectively during crises.