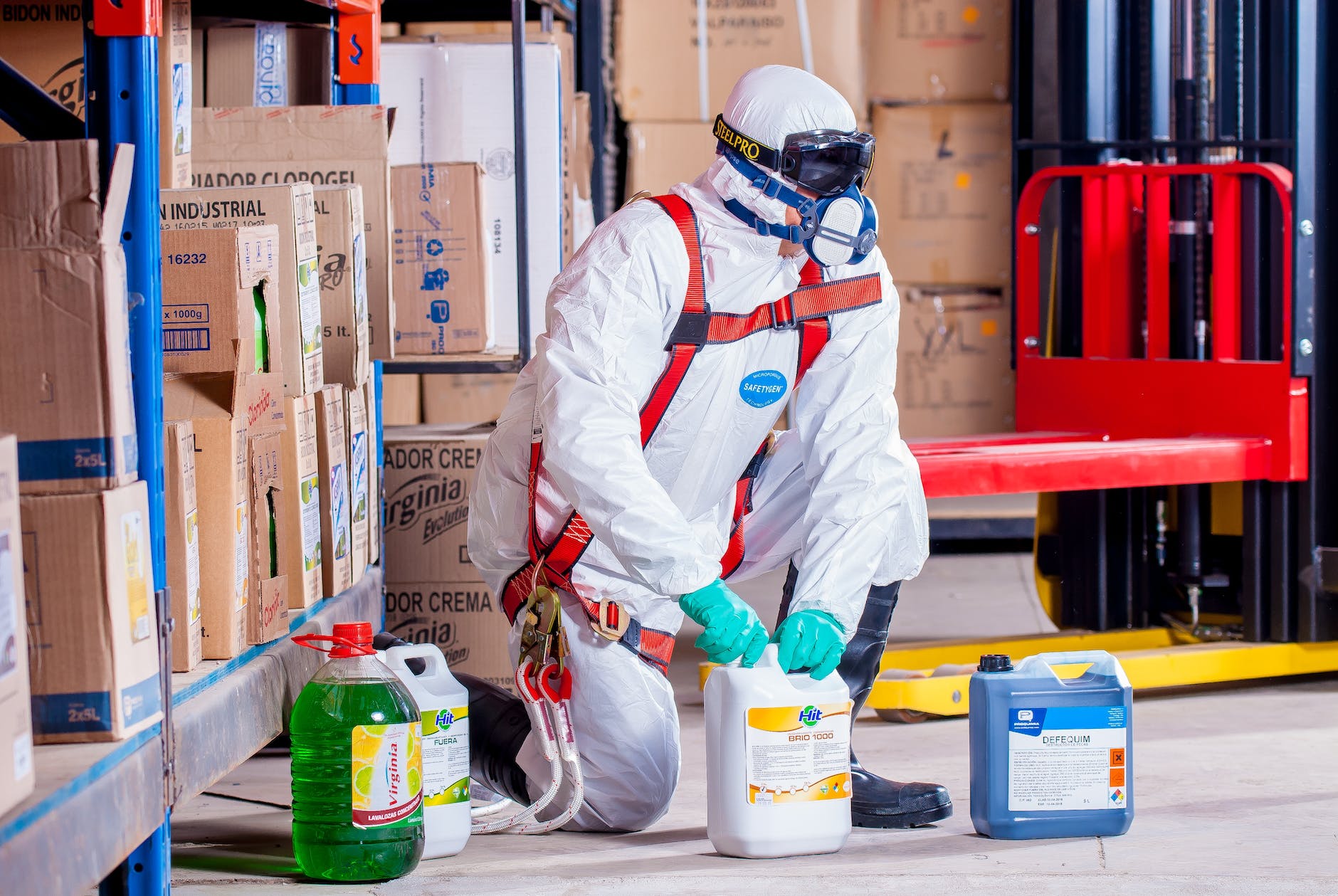
Chemical Safety Engineering: Hazard Identification and Risk Assessment
Chemical safety engineering is a critical discipline that focuses on identifying and managing hazards associated with the handling, storage, and use of chemicals. This article explores the foundational principles of chemical safety engineering, emphasizing the importance of thorough hazard identification and risk assessment in mitigating potential dangers.
Understanding Chemical Safety Engineering
Chemical safety engineering involves a systematic approach to ensure the safe handling, storage, and utilization of chemicals in various industries. It integrates principles of chemistry, engineering, and safety management to prevent accidents, protect workers, and safeguard the environment.
Importance of Hazard Identification
Recognizing Potential Risks
The first step in chemical safety engineering is recognizing potential hazards associated with different chemicals. This includes understanding the properties of chemicals, their reactivity, toxicity, and potential for causing harm in various scenarios.
Systematic Hazard Identification Process
Chemical safety engineers employ systematic hazard identification processes, which may include reviewing material safety data sheets (MSDS), conducting chemical inventories, and assessing potential interactions between different chemicals. This thorough approach helps create a comprehensive overview of potential risks.
Preventing Accidents and Incidents
Effective hazard identification is crucial for preventing accidents and incidents. By proactively recognizing potential risks, chemical safety engineers can implement preventive measures and safety protocols to reduce the likelihood of accidents in the workplace.
Risk Assessment in Chemical Safety Engineering
Quantifying Risks
Once hazards are identified, chemical safety engineers proceed with risk assessment. This involves quantifying the risks associated with specific chemicals and processes. The goal is to assign numerical values to the likelihood and severity of potential incidents.
Risk Matrix and Prioritization
A risk matrix is often employed to visualize and prioritize risks. This matrix considers the probability of an event occurring against the severity of its consequences. High-risk scenarios are prioritized for immediate attention and mitigation efforts.
Informed Decision-Making
Risk assessment provides the foundation for informed decision-making. Chemical safety engineers can use the results of risk assessments to recommend changes in procedures, enhance safety measures, or even substitute certain chemicals with less hazardous alternatives.
Implementing Risk Mitigation Strategies
Engineering Controls
Engineering controls involve designing safety measures into processes or equipment. This may include ventilation systems, containment structures, or automated shut-off systems. These controls aim to minimize exposure and prevent the release of hazardous substances.
Administrative Controls
Administrative controls focus on procedures and policies to reduce risk. This includes developing and enforcing safety protocols, providing training to personnel, and establishing emergency response plans. Well-informed and trained employees are key to mitigating risks effectively.
Personal Protective Equipment (PPE)
PPE is the last line of defense in risk mitigation. Chemical safety engineers evaluate the necessity of PPE based on risk assessments. This may include respirators, gloves, goggles, and other protective gear to minimize direct contact with hazardous substances.
Continuous Monitoring and Improvement
Regular Audits and Inspections
Chemical safety engineering is an ongoing process that requires continuous monitoring. Regular audits and inspections ensure that safety measures are adhered to and that any changes in processes or chemicals are promptly assessed for potential risks.
Updating Safety Protocols
As new information becomes available or processes change, safety protocols must be updated accordingly. Chemical safety engineers play a vital role in staying informed about advancements in chemical safety and ensuring that safety measures align with current best practices.
Chemical safety engineering focuses on identifying and managing potential hazards associated with the use, storage, and transportation of chemicals in various industries. Hazard identification and risk assessment are crucial steps in ensuring the safe handling of chemicals. Here's a guide to the key aspects of chemical safety engineering in the context of hazard identification and risk assessment:
- Chemical Inventory:
- Maintain a comprehensive inventory of all chemicals used, stored, or produced in the facility.
- Include information on the properties, quantities, and locations of each chemical in the inventory.
- Material Safety Data Sheets (MSDS):
- Review and keep updated Material Safety Data Sheets for each chemical. MSDS provides vital information about the properties, hazards, and safe handling procedures for chemicals.
- Regulatory Compliance:
- Ensure compliance with local, national, and international regulations governing the use and handling of chemicals, such as OSHA’s Hazard Communication Standard or REACH in Europe.
- Hazard Identification:
- Conduct a systematic hazard identification process to recognize potential hazards associated with each chemical. Consider physical, chemical, biological, and ergonomic hazards.
- Use available resources, databases, and expertise to identify specific hazards related to the properties and uses of each chemical.
- Process Hazard Analysis (PHA):
- Perform Process Hazard Analyses for processes involving the handling or production of hazardous chemicals.
- Methods such as Hazard and Operability Studies (HAZOP) or What-If Analysis can be used to systematically assess potential hazards.
- Risk Assessment:
- Quantitatively or qualitatively assess the risks associated with identified hazards.
- Evaluate the likelihood of an incident occurring and the potential consequences, considering factors such as exposure, toxicity, and environmental impact.
- Hierarchy of Controls:
- Apply the hierarchy of controls to manage and mitigate risks. This includes elimination or substitution of hazardous chemicals, engineering controls, administrative controls, and the use of personal protective equipment (PPE).
- Exposure Assessment:
- Assess the potential for exposure to hazardous chemicals during normal operations, as well as in the event of accidents or spills.
- Use exposure assessment to determine if control measures are effective in reducing exposure to acceptable levels.
- Emergency Preparedness and Response:
- Develop and implement emergency response plans for chemical-related incidents. Ensure that all personnel are trained on emergency procedures.
- Conduct regular drills and exercises to test the effectiveness of emergency response measures.
- Safe Work Practices:
- Establish safe work practices for handling, storing, and transporting chemicals. This includes proper labeling, storage procedures, and handling protocols.
- Implement standard operating procedures (SOPs) for tasks involving hazardous chemicals.
- Training and Communication:
- Provide comprehensive training for employees regarding the hazards of the chemicals they work with and the necessary safety measures.
- Maintain clear communication channels to disseminate safety information and updates.
- Monitoring and Surveillance:
- Implement monitoring systems to continuously assess chemical exposure levels and detect any deviations from established safety thresholds.
- Use air monitoring, personal dosimeters, or other appropriate methods to ensure a safe working environment.
- Continuous Improvement:
- Establish a feedback loop for continuous improvement. Regularly review incidents, near misses, and the effectiveness of control measures.
- Update hazard assessments and risk mitigation strategies based on new information or changes in processes.
- Documentation and Record Keeping:
- Keep detailed records of hazard assessments, risk analyses, and control measures implemented.
- Maintain accurate documentation of incidents, corrective actions, and training records.
- Community and Environmental Considerations:
- Consider the potential impact of chemical hazards on the surrounding community and the environment.
- Engage in dialogue with stakeholders and regulatory bodies to address community concerns and meet environmental protection requirements.
By systematically identifying hazards and assessing risks associated with chemical processes, safety engineers contribute to the development of effective control measures, ultimately enhancing the safety of both workers and the surrounding environment.
Conclusion
In conclusion, chemical safety engineering is a vital discipline in preventing accidents, protecting workers, and mitigating environmental impacts associated with the handling of chemicals. Through rigorous hazard identification, risk assessment, and the implementation of effective risk mitigation strategies, chemical safety engineers contribute to creating safer workplaces and promoting responsible chemical management.
Safety Data Sheets for Chemicals
What Is the Purpose of a Safety Data Sheet?
FAQs
- What is chemical safety engineering?
- Chemical safety engineering is a discipline that focuses on ensuring the safe handling, storage, and use of chemicals by identifying and managing potential hazards and risks.
- Why is hazard identification crucial in chemical safety engineering?
- Hazard identification is crucial as it allows chemical safety engineers to recognize potential risks associated with different chemicals, enabling them to implement preventive measures and safety protocols.
- What is risk assessment in chemical safety engineering?
- Risk assessment involves quantifying the risks associated with specific chemicals and processes, assigning numerical values to the likelihood and severity of potential incidents.
- How are risks prioritized in chemical safety engineering?
- Risks are prioritized using a risk matrix, considering the probability of an event occurring against the severity of its consequences. High-risk scenarios are addressed with immediate attention.
- What role does continuous monitoring play in chemical safety engineering?
- Continuous monitoring involves regular audits and inspections to ensure safety measures are followed, and safety protocols are updated. It ensures that safety measures align with current best practices.
i done b tech chemical engineering and diploma in industrial safety
I done BTech Chemical Engineering form NIT Durgapur