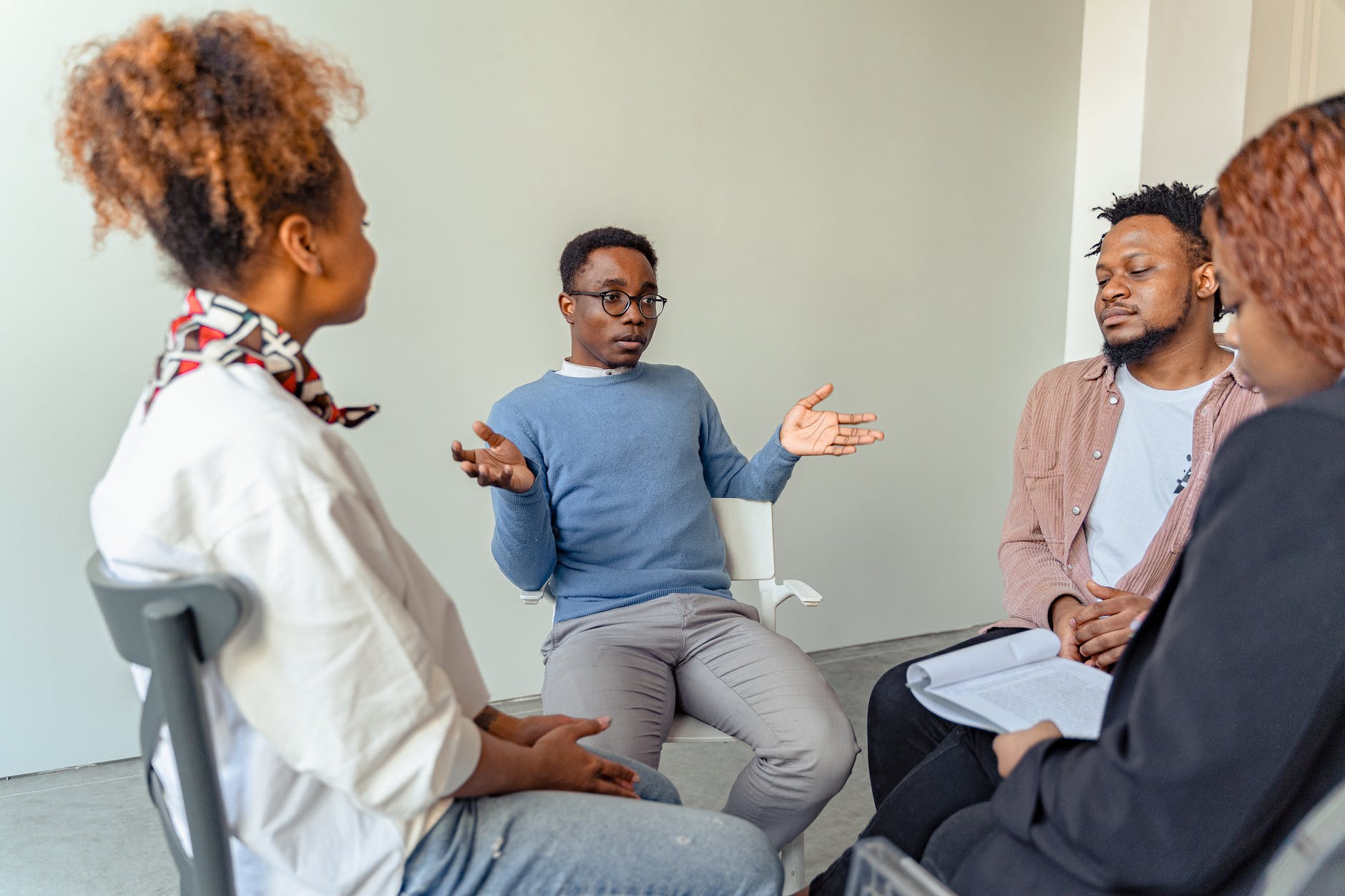
COSHH Risk Assessment
COSHH stands for Control of Substances Hazardous to Health, and a COSHH risk assessment is a process used to identify and assess the risks associated with the use of hazardous substances in the workplace. Here’s a general outline for a COSHH risk assessment:
- Identification of Hazardous Substances:
- List all the hazardous substances used in your workplace.
- Include chemicals, products, and materials that may pose a risk to health.
- Assessment of Risks:
- Consider how each substance could potentially harm health (inhalation, skin contact, ingestion).
- Assess the likelihood and severity of exposure.
- Identify specific health hazards associated with each substance (e.g., respiratory irritation, skin sensitization, carcinogenicity).
- Evaluate Control Measures:
- Identify existing control measures in place (e.g., ventilation systems, personal protective equipment).
- Assess the effectiveness of current controls in preventing or minimizing exposure.
- Consider alternative substances or processes that may be safer.
- Implement Control Measures:
- Implement or improve control measures based on the assessment.
- Ensure that control measures are suitable and sufficient to minimize the risk of exposure.
- Training and Information:
- Provide training to employees on the safe use of hazardous substances.
- Ensure that employees are aware of the risks, control measures, and emergency procedures.
- Monitoring and Health Surveillance:
- Establish a system for monitoring exposure levels where necessary.
- Implement health surveillance for employees working with particularly hazardous substances.
- Emergency Procedures:
- Develop and communicate clear emergency procedures in case of accidental exposure or spillage.
- Provide appropriate first aid facilities and information.
- Review and Revision:
- Regularly review and update the risk assessment.
- Revise control measures if circumstances change, such as the introduction of new substances or processes.
- Record Keeping:
- Maintain records of the risk assessment, control measures, and any incidents or exposure levels.
- Ensure that all relevant personnel have access to this information.
- Consultation and Communication:
- Consult with employees, safety representatives, and other relevant parties during the risk assessment process.
- Communicate the findings and control measures effectively.
Remember, the specific details of a COSHH risk assessment will depend on the nature of the substances used in your workplace. Always refer to local regulations and guidelines for specific requirements.
Scenario: Painting Workshop
In a painting workshop, various hazardous substances are used regularly, including paint solvents, thinners, and varnishes. Conducting a COSHH risk assessment is crucial to ensure the safety and health of the workers in this environment.
- Identification of Hazardous Substances:
- List of substances used: Paint solvents (Xylene, Toluene), varnish containing formaldehyde, and paint thinners.
- Assessment of Risks:
- Xylene and Toluene can cause respiratory issues and skin irritation upon prolonged exposure.
- Formaldehyde in varnish poses a risk of skin sensitization and respiratory irritation.
- Evaluate Control Measures:
- Current control measures: Local exhaust ventilation, gloves, and respirators.
- The ventilation system needs an upgrade for better efficacy against solvent vapors.
- Implement Control Measures:
- Upgrade ventilation system to efficiently remove solvent vapors.
- Provide training on proper handling, use of PPE, and the importance of ventilation.
- Training and Information:
- Conduct workshops to educate employees on the safe use of hazardous substances.
- Display clear signage outlining safety protocols and emergency procedures.
- Monitoring and Health Surveillance:
- Implement regular monitoring of air quality for solvent levels.
- Schedule periodic health check-ups for employees handling hazardous substances.
- Emergency Procedures:
- Create an emergency response plan for spills or accidental exposure.
- Ensure first aid kits equipped for treating chemical exposures are readily available.
- Review and Revision:
- Schedule regular reviews of the risk assessment, especially when introducing new substances or processes.
- Revise control measures based on feedback and changing circumstances.
- Record Keeping:
- Maintain detailed records of risk assessments, monitoring results, and incidents.
- Keep a log of employee training sessions and health surveillance outcomes.
- Consultation and Communication:
- Encourage open communication with employees regarding safety concerns.
- Establish a feedback mechanism for workers to report any safety issues promptly.
This hypothetical scenario demonstrates the steps involved in conducting a COSHH risk assessment in a painting workshop environment. Adjustments and specific measures would vary based on the substances and processes used, but the core principles of assessment, control, and monitoring remain consistent.
Conclusion:
In conclusion, conducting a COSHH (Control of Substances Hazardous to Health) risk assessment is vital for ensuring a safe and healthy working environment, especially where hazardous substances are used or handled. By systematically identifying, assessing, and mitigating risks associated with these substances, employers can protect the well-being of their employees and comply with regulatory standards.
Implementing control measures, providing adequate training, and regularly reviewing and updating the assessment are key steps in managing risks effectively. Through collaboration, communication, and a commitment to ongoing safety protocols, workplaces can minimize exposure to hazardous substances and prevent potential health issues.
Remember, every workplace is unique, and the specifics of a COSHH risk assessment will vary based on the substances used and work processes involved. Adhering to local regulations and seeking professional advice when needed are essential for ensuring a comprehensive and effective risk assessment.
COSHH (Control of Substances Hazardous to Health)
Chemical Safety Toolbox Talk Meeting
Chemical Safety Basic Knowledge
Personal Protective Equipment (PPE) for Chemical Safety
FAQs (Frequently Asked Questions):
- Why is a COSHH risk assessment important? A COSHH risk assessment helps identify and mitigate risks associated with hazardous substances, safeguarding the health and safety of workers and preventing potential health issues.
- Who should conduct a COSHH risk assessment? Trained personnel familiar with the workplace and the substances used should conduct the assessment. Often, health and safety professionals or designated competent individuals within the organization perform this task.
- What control measures are typically used in a COSHH assessment? Control measures may include ventilation systems, personal protective equipment (PPE), substitution of hazardous substances, employee training, and implementing safe handling procedures.
- How often should a COSHH risk assessment be reviewed? Regular reviews are crucial, especially when introducing new substances, processes, or if circumstances change. Typically, assessments should be revisited at least annually.
- Are there legal requirements for COSHH assessments? Yes, in many countries, there are legal obligations for employers to conduct COSHH risk assessments under health and safety regulations. Compliance helps avoid legal liabilities and ensures a safer workplace.
- What should employees do if they suspect hazardous substance exposure? Employees should report any suspected exposure immediately to their supervisor or designated safety personnel. Access to first aid and medical attention should be provided promptly.
Remember, while this FAQ section covers general information, specific regulations and practices might vary by region or industry. Consulting local authorities or health and safety experts can provide tailored guidance for your workplace.
I like how you presented your safety issues.
If I may ask how much cost is your study guide.
How to join your class especially of risk assessment.