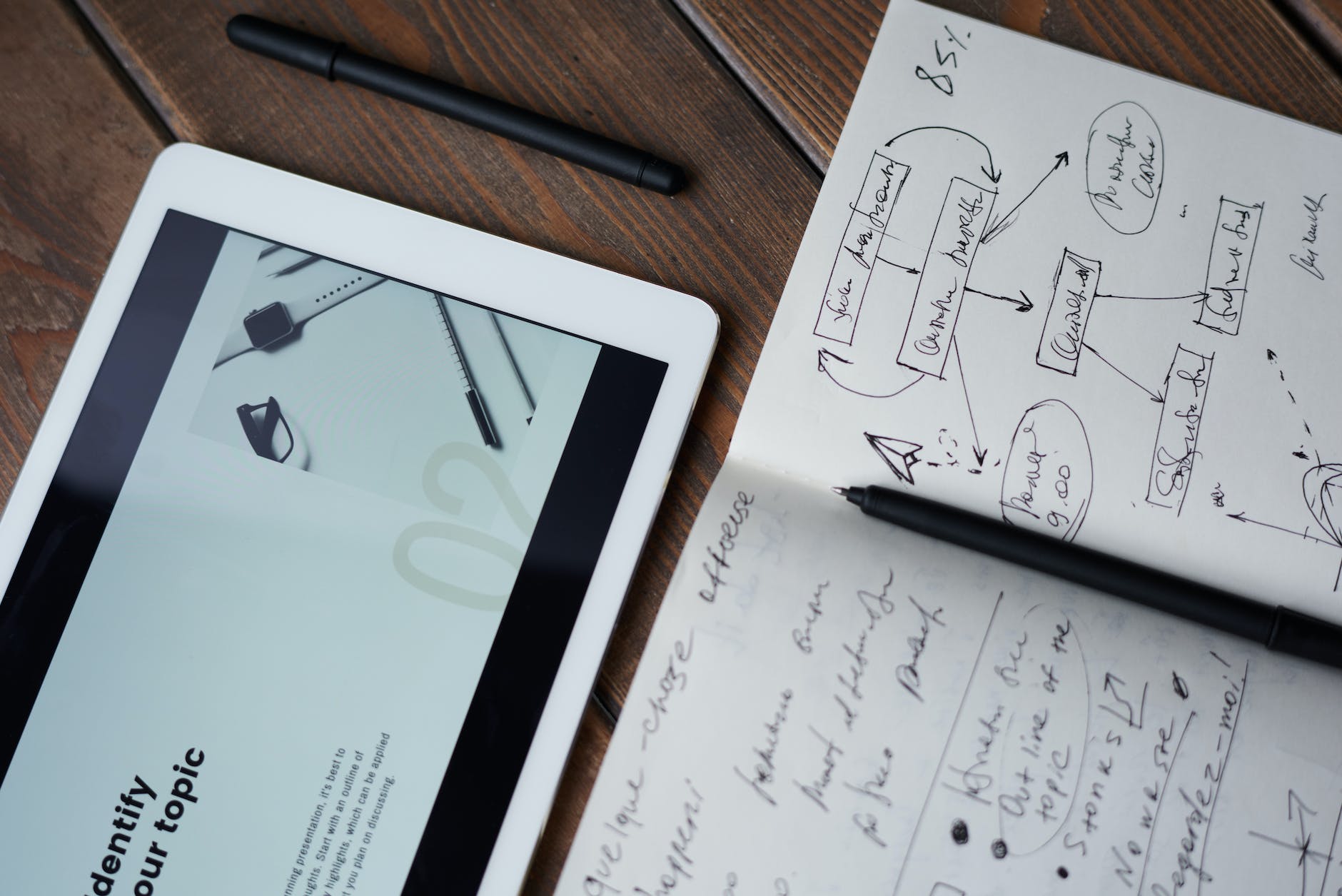
Failure Mode and Effects Analysis (FMEA): Application in Safety Engineering
Introduction
In the ever-evolving landscape of safety engineering, proactive risk management is crucial to prevent incidents and ensure the well-being of individuals. One powerful tool in the safety engineer’s arsenal is Failure Mode and Effects Analysis (FMEA). This article delves into the application of FMEA in safety engineering, exploring its principles, methodology, and real-world benefits.
Understanding Failure Mode and Effects Analysis (FMEA)
Defining FMEA
Failure Mode and Effects Analysis (FMEA) is a systematic method for evaluating processes, systems, and products to identify potential failure modes and their consequences. It provides a structured approach to proactively assess risks and prioritize mitigation strategies.
Core Principles of FMEA
- Identification of Failure Modes: FMEA involves a thorough examination to identify potential failure modes within a system or process.
- Analysis of Effects: Once failure modes are identified, the analysis extends to understanding the effects or consequences of each potential failure.
- Assigning Severity, Occurrence, and Detection Ratings: FMEA assigns numerical ratings for the severity of consequences, the likelihood of occurrence, and the ability to detect the failure before it reaches the end-user.
- Calculating Risk Priority Numbers (RPN): By multiplying severity, occurrence, and detection ratings, an RPN is calculated. Higher RPN values indicate higher risks.
- Prioritization of Mitigation Strategies: FMEA facilitates the prioritization of mitigation strategies by focusing on addressing high-risk areas first.
Application of FMEA in Safety Engineering
Risk Assessment in Safety Systems
FMEA is widely applied in safety engineering to assess the risks associated with complex systems and processes. By systematically identifying potential failure modes, safety engineers can prioritize their efforts to enhance the overall safety of the system.
Design and Process Improvement
During the design phase of safety-critical systems, FMEA helps identify vulnerabilities and weaknesses. This proactive approach allows safety engineers to make informed design decisions that mitigate risks and enhance the reliability of safety features.
Root Cause Analysis for Incidents
When incidents occur, FMEA serves as a valuable tool for root cause analysis. By understanding the failure modes and their effects, safety engineers can trace back the factors that contributed to an incident, enabling targeted corrective actions.
Decision Support for Resource Allocation
FMEA aids safety engineers in making informed decisions regarding resource allocation. By focusing on high-risk areas identified through the analysis, engineers can allocate resources strategically to address critical points in safety systems.
Continuous Improvement in Safety Protocols
FMEA is not a one-time exercise but an ongoing process. Safety engineers use it as a framework for continuous improvement, regularly reassessing risks and updating mitigation strategies to align with changing circumstances and emerging technologies.
Real-World Benefits of FMEA in Safety Engineering
Proactive Risk Management
FMEA’s proactive approach allows safety engineers to anticipate and address potential issues before they manifest as safety incidents. This not only prevents harm but also enhances the overall reliability and performance of safety systems.
Cost Savings
Identifying and mitigating risks early in the design or operational phases can result in substantial cost savings. Rectifying safety issues after they occur is often more expensive and can lead to downtime and reputation damage.
Improved Safety Culture
Implementing FMEA fosters a safety-conscious culture within an organization. By emphasizing the importance of identifying and mitigating risks, employees at all levels become actively engaged in maintaining a safe work environment.
Enhanced Regulatory Compliance
FMEA assists organizations in meeting and exceeding regulatory requirements. By systematically assessing risks and implementing mitigation measures, safety engineers ensure that safety protocols align with industry standards and governmental regulations.
Data-Driven Decision-Making
FMEA provides a structured and data-driven approach to decision-making. Safety engineers can objectively prioritize risks based on severity, occurrence, and detection, guiding their efforts to where they are most needed.
Failure Mode and Effects Analysis (FMEA) is a systematic method used in safety engineering to identify and prioritize potential failure modes within a system, process, or product. It involves a structured approach to assess the possible consequences of failures and prioritize them based on their severity, likelihood of occurrence, and the ability to detect or mitigate the failure. The application of FMEA in safety engineering is crucial for proactively managing risks and enhancing the overall safety and reliability of systems. Here's how FMEA is applied:
- Identifying Components and Processes:
- System Definition: Clearly define the system, process, or product being analyzed, and identify its individual components or steps.
- Boundary Identification: Establish the boundaries of the system to determine the scope of the analysis.
- Formation of a Cross-Functional Team:
- Multidisciplinary Team: Form a team that includes individuals from different disciplines, such as engineering, operations, maintenance, and safety, to ensure a comprehensive analysis.
- Expertise Inclusion: Ensure that the team includes individuals with expertise in the specific system or process under consideration.
- Listing Potential Failure Modes:
- Brainstorming: Conduct brainstorming sessions to identify all possible failure modes for each component or step in the process.
- Historical Data: Refer to historical data, incident reports, or similar systems to identify potential failure modes that have occurred in the past.
- Identifying Effects of Failure:
- Effects Analysis: Determine the consequences or effects of each identified failure mode on the system, process, or product.
- Severity Ranking: Assign a severity ranking to each potential effect based on the impact on safety, operations, or other critical criteria.
- Assessing the Likelihood of Occurrence:
- Likelihood Analysis: Evaluate the likelihood or probability of each failure mode occurring. Consider factors such as operating conditions, environmental influences, and human factors.
- Occurrence Ranking: Assign a ranking to each failure mode based on its likelihood of occurrence.
- Determining Detection and Mitigation Measures:
- Detection Methods: Identify methods or measures in place to detect or identify each failure mode before it leads to serious consequences.
- Mitigation Strategies: Develop mitigation strategies for each failure mode to reduce the severity or likelihood of occurrence.
- Calculating Risk Priority Numbers (RPN):
- RPN Calculation: Calculate the Risk Priority Number (RPN) for each failure mode by multiplying the severity, occurrence, and detection rankings.
- Prioritization: Prioritize the failure modes based on their RPN values, focusing on those with higher RPNs for further attention.
- Implementing Risk Mitigation Actions:
- Action Plans: Develop and implement action plans to address the identified high-risk failure modes.
- Monitoring: Regularly monitor and review the effectiveness of the implemented actions to ensure continuous improvement.
- Documentation and Reporting:
- FMEA Report: Document the entire FMEA process, including the identified failure modes, consequences, rankings, and mitigation actions.
- Communication: Share the FMEA results and recommendations with relevant stakeholders, including management, engineering teams, and safety personnel.
- Periodic Review and Update:
- Regular Review: Conduct periodic reviews of the FMEA to account for changes in the system, process, or external factors.
- Update FMEA: Update the FMEA as needed, incorporating new information, lessons learned, and changes in the operating environment.
In summary, the application of Failure Mode and Effects Analysis in safety engineering provides a systematic and proactive approach to identifying and managing potential risks. By prioritizing and addressing high-risk failure modes, organizations can enhance the safety and reliability of their systems and processes, ultimately preventing accidents and improving overall performance.
Conclusion
In conclusion, Failure Mode and Effects Analysis (FMEA) stands as a cornerstone in safety engineering, offering a systematic and proactive approach to risk management. By applying FMEA principles, safety engineers can enhance the reliability of safety systems, prevent incidents, and continuously improve safety protocols in a dynamic and ever-changing environment.
FAQs
- What is Failure Mode and Effects Analysis (FMEA)?
- FMEA is a systematic method for evaluating processes, systems, and products to identify potential failure modes and their consequences, enabling proactive risk management.
- How does FMEA contribute to safety engineering?
- FMEA contributes to safety engineering by systematically identifying potential failure modes, assessing their consequences, and prioritizing mitigation strategies to enhance the overall safety of systems.
- What are the core principles of FMEA?
- The core principles of FMEA include the identification of failure modes, analysis of their effects, assigning severity, occurrence, and detection ratings, calculating Risk Priority Numbers (RPN), and prioritizing mitigation strategies.
- How is FMEA applied in safety engineering?
- FMEA is applied in safety engineering for risk assessment in safety systems, design and process improvement, root cause analysis for incidents, decision support for resource allocation, and continuous improvement in safety protocols.
- What are the real-world benefits of using FMEA in safety engineering?
- The real-world benefits of using FMEA in safety engineering include proactive risk management, cost savings, improved safety culture, enhanced regulatory compliance, and data-driven decision-making.
Richly educative!