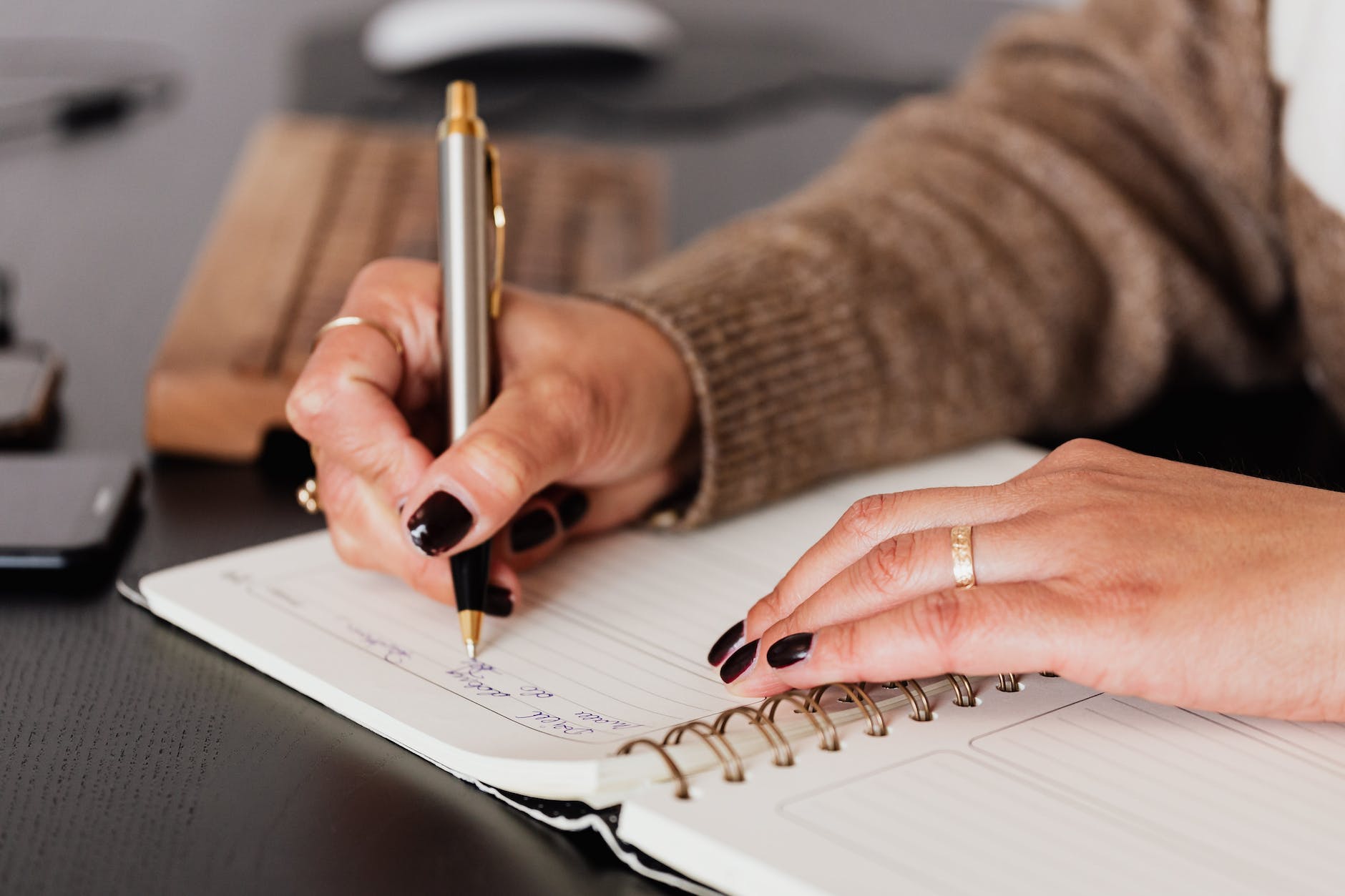
Hand-Arm Vibration Risk Assessment
Hand-Arm Vibration Risk Assessment : In today’s industrial and construction environments, the health and safety of workers are paramount. One critical aspect of this is the assessment and management of Hand-Arm Vibration (HAV) risks. This article delves into what HAV is, why it poses health risks, the legal obligations surrounding it, the importance of HAV risk assessment, and how to conduct one effectively.
Introduction
Hand-Arm Vibration (HAV) refers to the transmission of vibration into the hands and arms of individuals operating hand-held power tools or equipment. This constant exposure to vibrations can have adverse effects on the health of workers, leading to a range of conditions collectively known as Hand-Arm Vibration Syndrome (HAVS). HAVS can cause discomfort, pain, and potentially permanent damage, making it essential to assess and manage these risks.
What Is Hand-Arm Vibration (HAV)?
HAV is a common consequence of using tools such as jackhammers, chainsaws, and pneumatic drills. It occurs when the continuous vibration from these tools is transmitted through the hand and arm, affecting blood circulation and causing damage to nerves, muscles, and blood vessels.
Health Risks Associated with HAV
The health risks associated with HAV are significant. Workers exposed to high levels of vibration are at risk of developing HAVS. This syndrome includes symptoms like numbness, tingling, and reduced dexterity, and in severe cases, it can lead to painful vascular and neurological disorders.
Legal Obligations and Regulations
Many countries have established strict legal regulations to protect workers from HAV exposure. Employers are obligated to assess and manage HAV risks in the workplace to ensure the safety of their employees. These regulations may include exposure limits, requirements for monitoring and control measures, and the provision of training and information to workers.
Importance of Hand-Arm Vibration Risk Assessment
The importance of HAV risk assessment cannot be overstated. Assessing the risks allows employers to understand the level of exposure and take appropriate measures to protect their workers. It also helps in ensuring legal compliance, reducing potential compensation claims, and maintaining the health and productivity of the workforce.
Factors Affecting HAV Exposure
Various factors influence the extent of HAV exposure, including the type of tools used, the duration of exposure, and the vibration levels generated by the equipment. Assessing these factors is crucial in determining the level of risk and implementing control measures.
Conducting a HAV Risk Assessment
A comprehensive HAV risk assessment involves identifying exposure levels, assessing the tools used, and evaluating worker exposure. This assessment is typically carried out by health and safety professionals who are trained in the field.
Measurement and Monitoring Techniques
Accurate measurement and monitoring of vibration levels are vital components of a HAV risk assessment. Specialized equipment and devices are used to measure the vibration levels generated by tools and equipment.
Control Measures
Controlling HAV exposure includes implementing measures to reduce vibration transmission. This may involve selecting low-vibration tools, maintaining equipment, and providing anti-vibration gloves to workers.
Training and Awareness
Proper training and raising awareness among workers are essential. Employees should be educated on the risks associated with HAV and instructed on how to use equipment safely.
Reporting and Record Keeping
Maintaining records of assessments, exposure levels, and control measures is crucial for compliance and accountability. These records also help in tracking changes over time.
Scenario: A Construction Company’s HAV Risk Assessment
John, the health and safety officer at a busy construction company, was keen on ensuring the well-being of his team. Construction sites were notorious for the use of heavy machinery and power tools, which often exposed workers to Hand-Arm Vibration (HAV). John was determined to conduct a thorough HAV risk assessment to mitigate the health risks associated with prolonged exposure.
Step 1: Identifying the Tools
In his risk assessment, John began by identifying the tools used most frequently on the construction site. He realized that jackhammers, concrete drills, and pneumatic drills were among the high-vibration tools commonly in use.
Step 2: Determining Exposure Levels
John used specialized equipment to measure the vibration levels generated by these tools. He found that some workers were consistently exposed to high levels of HAV due to their specific job roles and the machinery they operated.
Step 3: Worker Interviews
John conducted interviews with workers to understand their experiences and concerns. He discovered that some workers had been experiencing symptoms like numbness and tingling in their hands after using the tools for extended periods.
Step 4: Implementing Control Measures
Armed with this information, John decided to implement control measures. He introduced anti-vibration gloves for workers, which reduced the transmission of vibration to their hands and arms. Additionally, he scheduled regular breaks to minimize prolonged tool operation.
Step 5: Training and Awareness
John organized training sessions for the workers, focusing on the correct use of tools and the importance of taking preventive measures. Workers were made aware of the potential risks and the need for vigilance.
Step 6: Regular Monitoring
To ensure that the control measures were effective, John established a routine monitoring process. He kept records of exposure levels, incidents, and the usage of safety equipment.
Outcome: A Safer Work Environment
Over time, John noticed a positive change in the workplace. Workers reported fewer incidents of numbness and tingling in their hands and arms, and productivity remained consistent. The implementation of HAV risk assessment and control measures had created a safer and more comfortable work environment for everyone on the construction site.
This scenario demonstrates how a diligent HAV risk assessment can lead to proactive measures that not only protect worker health but also enhance workplace safety and overall productivity.
Benefits of HAV Risk Assessment
Assessing and managing HAV risks in the workplace offers several benefits, including a safer work environment, reduced liability, and improved worker well-being and productivity.
Conclusion
In conclusion, Hand-Arm Vibration Risk Assessment is a critical element of workplace safety. HAV exposure can have severe health implications for workers, making it essential for employers to conduct thorough assessments and implement control measures. By complying with legal regulations and prioritizing worker safety, organizations can create healthier and more productive work environments.
Vibration Hazards and Control Measures
Vibration Hazards and Control Measures
Whole-Body Vibration Syndromes
FAQs
1. What are the main health risks associated with HAV exposure?
Exposure to Hand-Arm Vibration (HAV) can lead to a condition known as Hand-Arm Vibration Syndrome (HAVS). The main health risks associated with HAV exposure include numbness, tingling, and reduced dexterity in the hands and arms. In severe cases, it can lead to painful vascular and neurological disorders, which may become permanent if not addressed.
2. How often should a HAV risk assessment be conducted in the workplace?
The frequency of HAV risk assessments may vary depending on the nature of the work and the tools being used. In general, it’s recommended to conduct these assessments regularly, especially when new equipment is introduced or if there are changes in work conditions. Many organizations conduct these assessments annually, but more frequent assessments may be required for high-risk environments.
3. What control measures can employers implement to reduce HAV exposure?
Employers can implement various control measures to reduce HAV exposure. These include selecting low-vibration tools, maintaining equipment to ensure it operates efficiently, providing anti-vibration gloves to workers, and introducing engineering controls like vibration isolation or damping. Training workers on safe tool usage and promoting regular breaks can also help reduce exposure.
4. Are there specific tools that produce less HAV than others?
Yes, some tools produce less HAV than others. Manufacturers often provide information on the vibration levels generated by their tools. When selecting equipment, it’s advisable to choose those with lower vibration levels, as this can significantly reduce the risk of HAVS. Regular maintenance and proper calibration of tools are also crucial to keep vibration levels in check.
5. What are the potential consequences for employers who neglect HAV risk assessment and management?
Neglecting HAV risk assessment and management can have severe consequences for employers. They may face legal repercussions, including fines and lawsuits, if they fail to comply with occupational health and safety regulations. Furthermore, neglecting HAV risk management can lead to a higher rate of worker absenteeism due to health issues, reduced productivity, and potential long-term liabilities related to compensation claims. Prioritizing HAV risk assessment and management is not only ethically responsible but also financially prudent for employers.
Thanks for valuable information about HAV
Thank You!