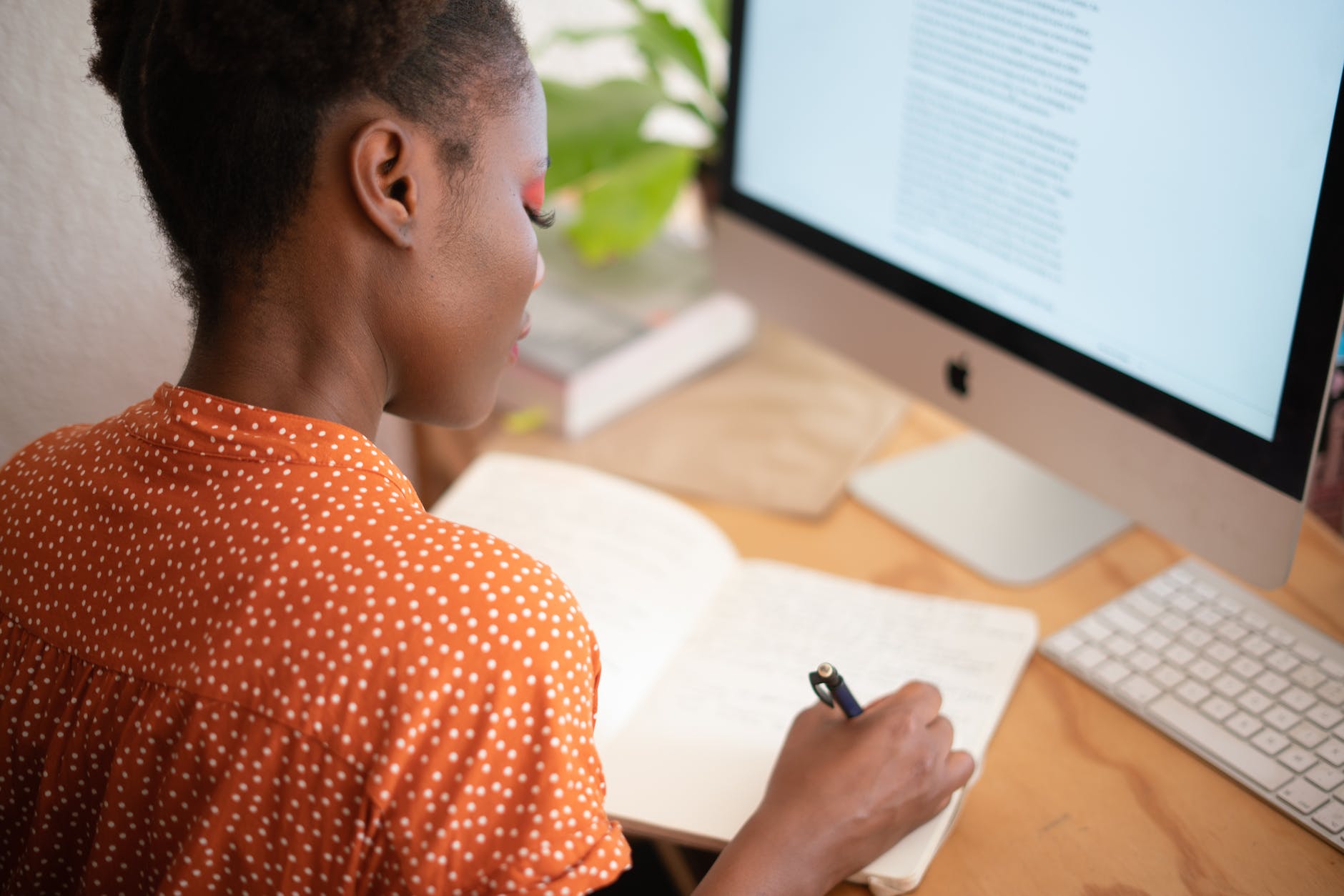
HAZOP Study in Chemical Plant
Chemical plants are intricate systems where safety and operational efficiency are paramount. Within these environments, the Hazard and Operability Study (HAZOP) emerges as a critical tool in identifying potential hazards and optimizing operational processes.
Introduction to HAZOP Studies
HAZOP, a systematic and structured approach, aims to assess and mitigate risks within chemical plants. It involves a comprehensive examination of the plant’s design, operation, and processes to identify deviations that could lead to hazardous situations.
Objectives of HAZOP Studies
The primary goals revolve around pinpointing potential hazards, understanding operability issues, and enhancing overall safety protocols. By scrutinizing various parameters and scenarios, HAZOP aids in foreseeing potential risks before they manifest.
Methodology of HAZOP
Typically conducted by a multidisciplinary team, HAZOP meticulously dissects each process node, considering deviations from the intended design. This process involves brainstorming sessions, where deviations and their consequences are thoroughly assessed.
Key Elements Analyzed in HAZOP
Parameters such as temperature, pressure, flow rates, and material composition are meticulously analyzed. Risk assessment is coupled with mitigation strategies, ensuring a proactive approach to safety measures.
Benefits of Conducting HAZOP Studies
Implementing HAZOP results in enhanced safety measures, reducing the probability of accidents and potential financial losses. Over time, it proves to be a cost-effective approach, outweighing initial investment with long-term safety dividends.
Case Studies Highlighting HAZOP Impact
Real-life examples showcasing successful HAZOP implementations underscore its effectiveness. These instances illustrate tangible outcomes post HAZOP execution, emphasizing its significance in averting potential disasters.
Challenges and Limitations of HAZOP
Despite its effectiveness, HAZOP encounters challenges in addressing complex systems and overcoming limitations in foreseeing unprecedented scenarios. However, continuous refinement mitigates these shortcomings.
Evolution of HAZOP Studies
HAZOP methodologies have evolved over time, integrating technological advancements and adopting best practices. This evolution ensures its adaptability to modern systems, paving the way for more robust safety protocols.
Industry Standards and Compliance
Regulations and guidelines set by governing bodies emphasize the importance of HAZOP in ensuring compliance with stringent safety norms within chemical plants.
Training and Education in HAZOP
Skilled professionals trained in HAZOP methodologies play a pivotal role. Educational initiatives and comprehensive training programs contribute to building a competent workforce in this domain.
A Hazard and Operability (HAZOP) study is a systematic method used in the chemical industry to identify potential hazards and operational issues in a plant. It involves a multidisciplinary team that carefully examines each element of a process to understand how deviations from the intended design or operations could lead to hazards or undesirable outcomes.
During a HAZOP study, the team looks at various parameters like pressure, temperature, flow rate, and others to systematically analyze potential deviations from the normal operating conditions. Each parameter is examined under different scenarios to identify potential risks, their causes, and consequences. This thorough analysis helps in devising strategies to mitigate or eliminate these risks, making the plant safer and more efficient.
The findings and recommendations from a HAZOP study are documented in a report, and the implementation of suggested measures is crucial for ensuring the safety and reliability of the chemical plant. Regular HAZOP reviews may also be conducted as part of ongoing safety management to address changes in processes, equipment, or regulations.
Here's a simplified example of a HAZOP study in a chemical plant:
Scenario: Consider a chemical plant that produces a certain type of solvent through a continuous distillation process.
Parameter: Temperature
Intended Operation: The distillation column maintains a temperature of 150°C to separate the desired solvent from other components.
Deviation Scenario: The team considers a deviation where the temperature in the distillation column rises unexpectedly.
Analysis:
- Cause of Deviation: Potential causes could include a malfunctioning temperature control system, overheating due to increased pressure, or failure in the cooling system.
- Consequences: Higher temperatures might lead to the decomposition of the solvent or other chemicals, causing toxic fumes, fire, or an explosion. It could also damage the equipment or compromise the quality of the final product.
- Mitigation Measures: Implement redundant temperature control systems, install alarms for rapid temperature changes, conduct regular maintenance of cooling systems, and establish emergency shutdown protocols.
This is just one parameter (temperature) in a simplified example. A comprehensive HAZOP study would consider multiple parameters and deviations across various stages of the chemical process to identify and mitigate potential hazards comprehensively.
Conclusion
HAZOP studies stand as an indispensable tool in the realm of chemical plant safety. Their systematic approach in identifying potential hazards and optimizing operational processes underscores their significance in averting disasters.
OSHA Hazard Identification Requirements
OSHA Hazard Identification Training Tool
Hazard Identification Methods in the Workplace
FAQs
- What industries benefit from HAZOP studies? HAZOP studies benefit a wide array of industries, especially those dealing with complex processes, such as chemical manufacturing, oil and gas, pharmaceuticals, and even power generation. Any industry where operational safety is critical can benefit from HAZOP assessments.
- How frequently should HAZOP studies be conducted? The frequency of HAZOP studies depends on various factors like the nature of the processes, changes in the system, and regulatory requirements. Typically, they’re conducted during the design phase, and periodic reviews are recommended, often every few years or when significant modifications occur.
- Can HAZOP completely eliminate risks in chemical plants? While HAZOP studies are incredibly effective in identifying and mitigating risks, they cannot entirely eliminate all risks. However, they significantly reduce the probability of accidents by addressing potential hazards proactively.
- Is HAZOP applicable to new and existing chemical plants alike? Absolutely. HAZOP studies are beneficial for both new and existing plants. For new plants, they are conducted during the design phase, while for existing ones, they help in identifying potential hazards, even in established processes.
- What role does government regulation play in HAZOP implementation? Government regulations often mandate the implementation of safety assessments like HAZOP. These regulations set standards and guidelines that industries must adhere to, emphasizing the importance of safety protocols and HAZOP studies in particular.