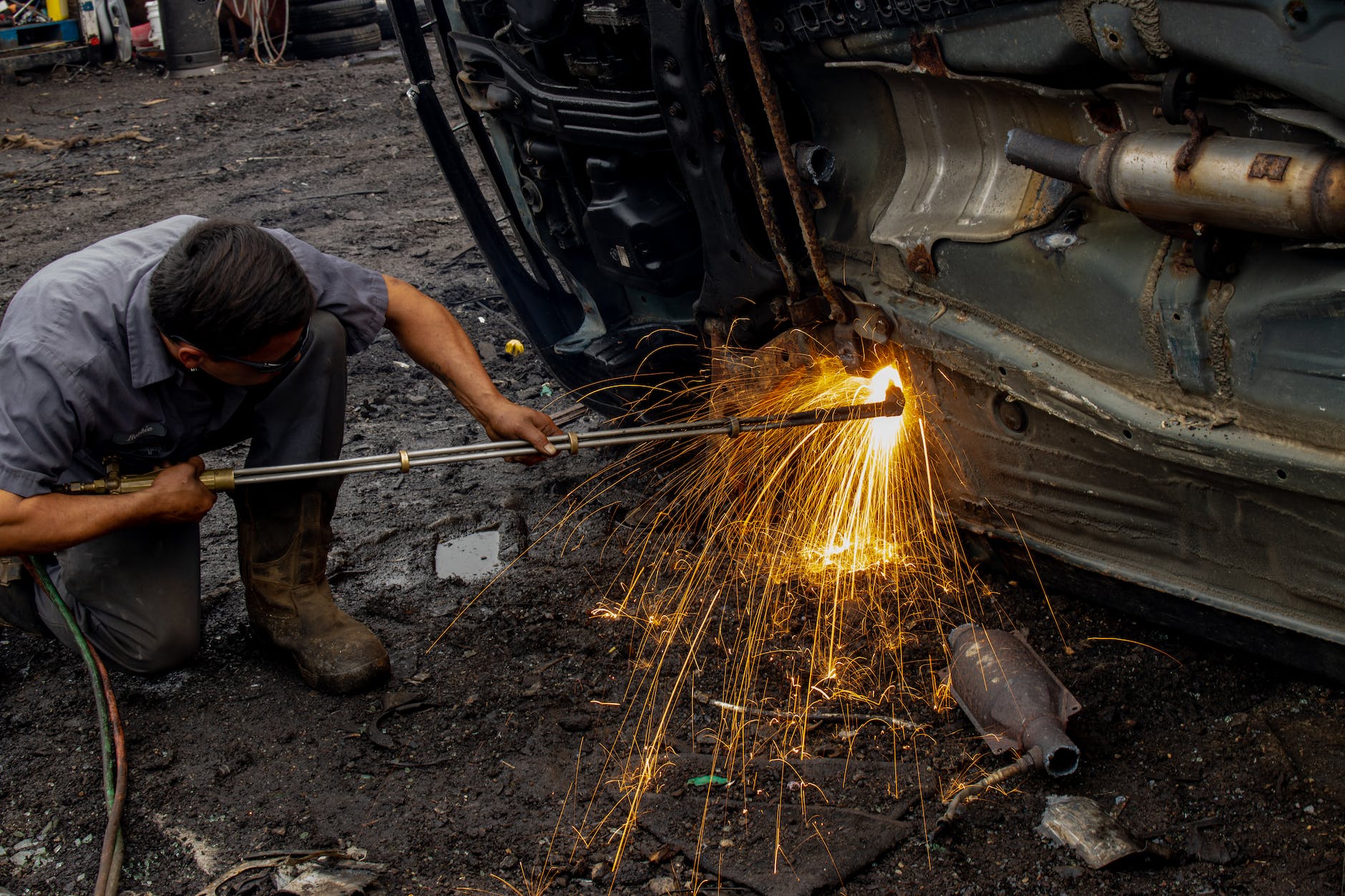
Heat Source Safety: Preventing Burns and Scalds in the Workplace
Introduction
In various work environments, the presence of heat sources is inevitable. Whether in kitchens, manufacturing facilities, or laboratories, understanding heat source safety is paramount to prevent burns and scalds. This article delves into effective measures for preventing burns and scalds in workplaces where heat sources are prevalent.
Understanding the Risks of Heat Sources
- Common Workplace Heat Sources
- Cooking Equipment: Kitchens and food preparation areas.
- Industrial Machinery: Manufacturing plants and workshops.
- Laboratories: Heat-producing equipment for experiments.
- Types of Burns and Scalds
- Thermal Burns: Result from direct contact with hot surfaces or liquids.
- Scalds: Caused by hot liquids or steam coming into contact with the skin.
- Factors Contributing to Incidents
- Lack of Awareness: Insufficient knowledge about the risks associated with specific heat sources.
- Inadequate Training: Employees not adequately trained in safe practices around heat sources.
Preventive Measures for Burns and Scalds
- Employee Training
- Heat Source Awareness: Ensure all employees are educated about the specific heat sources present in their workplace.
- Safe Practices: Provide comprehensive training on safe practices when working around heat-producing equipment.
- Use of Personal Protective Equipment (PPE)
- Heat-Resistant Clothing: Supply employees with heat-resistant clothing to minimize skin exposure.
- Gloves and Aprons: Ensure the use of appropriate gloves and aprons when handling hot materials or liquids.
- Proper Equipment Handling
- Equipment Familiarization: Train employees on the correct operation and handling of heat-producing machinery.
- Hot Surface Awareness: Clearly mark and identify hot surfaces to alert employees of potential hazards.
- Temperature Controls and Monitoring
- Regular Maintenance: Ensure that equipment with temperature controls undergoes regular maintenance.
- Thermometer Use: Install and regularly check thermometers to monitor temperatures effectively.
- Emergency Response Training
- First Aid Training: Equip employees with basic first aid training for immediate response to burns and scalds.
- Emergency Showers and Eyewash Stations: Install emergency showers and eyewash stations in areas where exposure to hot substances is likely.
Safe Practices for Specific Heat Sources
- Cooking Equipment Safety
- Proper Pan Handling: Train kitchen staff on proper handling of hot pans and utensils.
- Use of Oven Mitts: Encourage the use of heat-resistant oven mitts when dealing with hot ovens and stoves.
- Industrial Machinery Guidelines
- Lockout/Tagout Procedures: Implement lockout/tagout procedures during maintenance to prevent accidental activation.
- Warning Signs: Clearly mark areas around industrial machinery with warning signs indicating potential heat hazards.
- Laboratory Safety Protocols
- Ventilation Systems: Ensure laboratories have adequate ventilation systems to dissipate heat and fumes.
- Heat-Resistant Countertops: Use heat-resistant countertops to minimize the risk of thermal burns during experiments.
Creating a Culture of Heat Source Safety
- Leadership Commitment
- Policy Development: Develop and communicate a comprehensive heat source safety policy.
- Resource Allocation: Allocate resources for ongoing training and the implementation of safety measures.
- Regular Safety Audits
- Conduct Audits: Regularly audit workplaces for compliance with heat source safety protocols.
- Employee Feedback: Encourage employees to provide feedback on potential safety improvements.
- Communication Channels
- Open Dialogue: Foster an open dialogue between management and employees about heat source safety.
- Reporting Mechanisms: Establish easy and confidential reporting mechanisms for safety concerns.
Conclusion
Preventing burns and scalds in the workplace requires a proactive approach to heat source safety. By prioritizing employee training, implementing preventive measures, and creating a culture that values safety, organizations can significantly reduce the risk of incidents related to heat sources. Through leadership commitment, regular safety audits, and effective communication channels, workplaces can foster an environment where employees feel secure and empowered to work safely around heat-producing equipment.
Safety Training Program Evaluation: Measuring Effectiveness and Impact
Psychosocial Risk Assessment in the Workplace: Addressing Mental Health Concerns
Root Cause Analysis (RCA): Identifying and Addressing Underlying Causes of Safety Incidents
Risk Assessment and Hazard Identification: A Key Responsibility for Safety Officers
Personal Protective Equipment (PPE): Selection, Usage, and Maintenance for Safety Officers
Frequently Asked Questions (FAQs)
- What are common workplace heat sources?
- Common workplace heat sources include cooking equipment in kitchens, industrial machinery in manufacturing plants, and heat-producing equipment in laboratories.
- How can employees be trained to prevent burns and scalds?
- Employees can be trained through awareness programs on specific heat sources, safe practices, the use of personal protective equipment (PPE), and emergency response training.
- What are preventive measures for burns and scalds?
- Preventive measures include proper employee training, the use of heat-resistant clothing and PPE, proper equipment handling, temperature controls, and emergency response training.
- What are safe practices for specific heat sources, such as cooking equipment and industrial machinery?
- Safe practices include proper pan handling and oven mitt use in kitchens, lockout/tagout procedures and warning signs around industrial machinery, and the use of ventilation systems and heat-resistant countertops in laboratories.
- How can organizations create a culture of heat source safety?
- Organizations can create a culture of heat source safety through leadership commitment, regular safety audits, fostering open dialogue, and establishing effective reporting mechanisms for safety concerns.