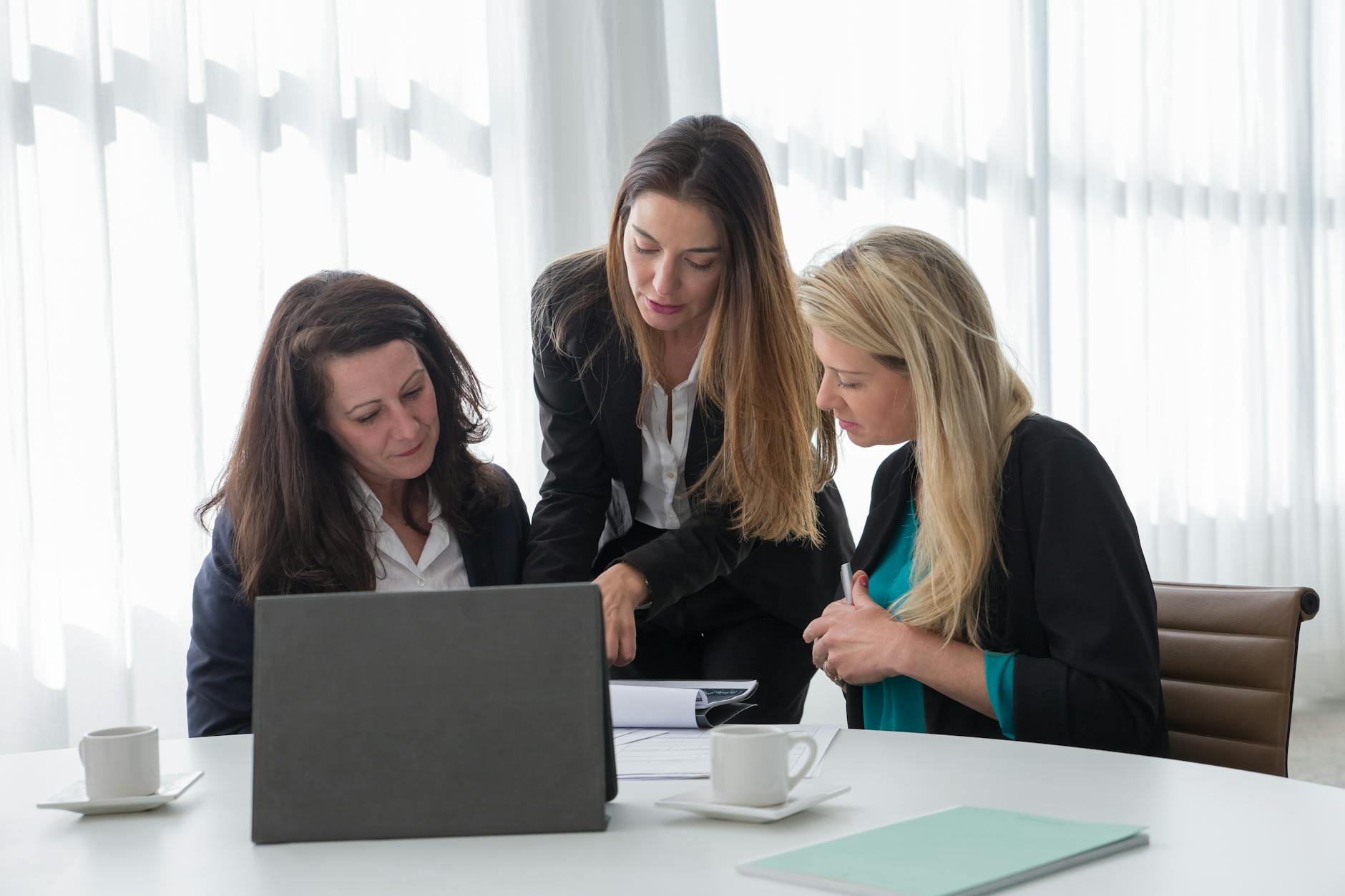
HSE Training Requirements: Ensuring Workplace Safety and Compliance
In today’s rapidly evolving industrial landscape, ensuring the safety and well-being of employees is paramount. Occupational hazards and environmental concerns underscore the need for comprehensive Health, Safety, and Environmental (HSE) training programs. From regulatory compliance to industry-specific protocols, HSE training requirements play a crucial role in safeguarding employees and mitigating risks.
Importance of HSE Training
Regulatory Requirements
HSE training is not just a moral imperative but a legal obligation for organizations. Regulatory bodies such as the Occupational Safety and Health Administration (OSHA) mandate employers to provide a safe working environment through proper training and education. Failure to comply with these regulations can result in hefty fines and legal liabilities.
Key Elements of HSE Training
HSE training encompasses a broad spectrum of topics aimed at fostering a culture of safety and environmental stewardship within organizations.
Health and Safety Training
Health and safety training cover topics such as hazard identification, emergency response, first aid, and workplace ergonomics. Employees are trained to recognize potential risks and take preventive measures to mitigate them.
Environmental Training
Environmental training focuses on sustainable practices, waste management, pollution prevention, and regulatory compliance with environmental laws. It empowers employees to minimize their ecological footprint and contribute to a cleaner, greener future.
Compliance Standards
OSHA Regulations
OSHA sets forth stringent standards for workplace safety, requiring employers to implement comprehensive HSE training programs tailored to their specific industry hazards. Regular inspections ensure adherence to these standards, promoting a culture of safety consciousness.
Environmental Protection Agency (EPA) Guidelines
The EPA oversees environmental regulations aimed at protecting human health and the environment. Companies must comply with EPA guidelines regarding waste disposal, chemical handling, air quality control, and pollution prevention measures.
Industry-specific Training Needs
Different industries have unique HSE training requirements tailored to their specific operational risks and challenges.
Construction
Construction sites are fraught with hazards such as falls, electrical shocks, and heavy machinery accidents. Workers receive specialized training on scaffolding safety, confined space entry, and hazard communication to mitigate these risks.
Manufacturing
Manufacturing facilities require HSE training to address machinery operation, chemical handling, and ergonomics. Emphasis is placed on lockout/tagout procedures, personal protective equipment (PPE) usage, and hazardous material management.
Healthcare
Healthcare settings mandate HSE training to ensure patient safety and infection control. Healthcare workers receive training on bloodborne pathogens, patient handling techniques, and sterilization procedures to minimize the risk of workplace injuries and nosocomial infections.
Oil and Gas
The oil and gas industry grapple with high-risk activities such as drilling, refining, and transportation of hazardous materials. Rigorous HSE training is imperative to prevent catastrophic accidents, oil spills, and environmental contamination.
Training Methods and Delivery
HSE training can be delivered through various methods to accommodate diverse learning styles and operational constraints.
Classroom Training
Traditional classroom-based training sessions allow for interactive learning experiences facilitated by instructors. Participants engage in discussions, case studies, and role-playing exercises to reinforce key concepts.
Online Training
E-learning platforms offer convenient, self-paced training modules accessible anytime, anywhere. Multimedia presentations, quizzes, and simulations enhance learner engagement and retention, making it an efficient mode of delivering HSE training.
On-the-Job Training
On-the-job training immerses employees in real-world scenarios, allowing them to apply theoretical knowledge in practical situations. Mentors guide trainees through hands-on tasks, providing immediate feedback and skill development opportunities.
Assessing Training Effectiveness
Measuring the effectiveness of HSE training programs is essential for continuous improvement and compliance assurance.
Evaluation Metrics
Performance metrics such as incident rates, near-miss reporting, and compliance audits serve as indicators of training effectiveness. Feedback from employees, supervisors, and external stakeholders provides valuable insights into areas for improvement.
Continuous Improvement
Continuous evaluation and refinement of HSE training initiatives ensure alignment with evolving regulatory requirements and industry best practices. Feedback loops facilitate the identification of emerging risks and the implementation of proactive measures to mitigate them.
Challenges in HSE Training
Despite its importance, HSE training faces several challenges that organizations must address to ensure effectiveness and sustainability.
Compliance Complexity
Navigating the intricate web of regulatory requirements can be daunting for organizations, especially those operating in multiple jurisdictions or industries. Harmonizing HSE training programs to meet diverse compliance standards requires careful planning and resource allocation.
Resource Allocation
Allocating sufficient resources, including time, budget, and personnel, is crucial for the success of HSE training initiatives. Competing priorities and budget constraints may hinder organizations’ ability to invest adequately in training and development, compromising employee safety and regulatory compliance.
HSE (Health, Safety, and Environment) training requirements vary depending on the industry, region, and specific job roles. However, there are some common areas that are typically covered in HSE training programs:
- General Safety Training: This includes basic safety principles, hazard recognition, emergency procedures, and accident prevention.
- Occupational Health and Safety: Training on specific hazards relevant to the workplace, such as chemical exposure, electrical safety, fire safety, and ergonomics.
- Environmental Protection: Instruction on environmental regulations, waste management, pollution prevention, and conservation practices.
- Personal Protective Equipment (PPE): Proper selection, use, and maintenance of PPE relevant to the job tasks and workplace hazards.
- Safety Procedures and Protocols: Training on operating machinery and equipment safely, following established safety protocols, and adhering to safety standards and regulations.
- Emergency Response and First Aid: Instruction on responding to accidents, injuries, fires, and other emergencies, including first aid and CPR training.
- Risk Assessment and Management: Training on identifying, assessing, and mitigating workplace hazards, as well as developing and implementing safety procedures and protocols.
- Legal and Regulatory Compliance: Education on relevant health, safety, and environmental laws, regulations, and standards applicable to the industry and workplace.
- Behavioral Safety: Training aimed at promoting a safety culture within the organization, emphasizing the importance of safe behaviors and attitudes among employees.
- Continuous Improvement: Encouraging ongoing learning and improvement in HSE practices through regular training sessions, reviews, and updates to policies and procedures.
Employers often have specific requirements for HSE training based on the nature of their operations and the risks associated with their activities. It's essential for employees to undergo regular training and refreshers to stay up-to-date with best practices and regulatory changes to ensure a safe and healthy work environment.
Conclusion
In conclusion, HSE training is a cornerstone of workplace safety and regulatory compliance, encompassing a wide range of topics and methodologies tailored to organizational needs. By investing in comprehensive HSE training programs, companies can mitigate risks, protect their workforce, and foster a culture of safety excellence.
Emergency Response Team Training: Navigating Roles and Responsibilities
Safety Training Program Evaluation: Measuring Effectiveness and Impact
10 Important OSHA Monthly Safety Topics 2024
FAQs
- What are the consequences of non-compliance with HSE training regulations? Non-compliance with HSE training regulations can result in severe consequences for organizations, including hefty fines, legal liabilities, damage to reputation, and, most importantly, the risk of harm to employees and the environment. Failure to adhere to regulatory standards may lead to workplace accidents, injuries, illnesses, environmental pollution, and even fatalities.
- How often should HSE training be conducted within an organization? The frequency of HSE training sessions depends on various factors, including regulatory requirements, industry standards, organizational policies, and the nature of work activities. Generally, initial HSE training is provided to new hires, followed by periodic refresher courses to reinforce knowledge and skills. Continuous training and awareness programs should be conducted to address emerging risks, changes in regulations, and technological advancements.
- What role does leadership play in promoting a culture of safety? Leadership plays a critical role in promoting a culture of safety within an organization. By demonstrating a commitment to safety, setting clear expectations, allocating resources for training and equipment, and actively participating in safety initiatives, leaders can influence employee attitudes and behaviors towards safety. Effective communication, empowerment, and recognition of safety achievements also foster a positive safety culture from the top down.
- Are there industry-specific certifications for HSE professionals? Yes, there are industry-specific certifications available for HSE professionals, tailored to different sectors such as construction, manufacturing, healthcare, oil and gas, and environmental management. Examples include the Certified Safety Professional (CSP), Occupational Health and Safety Technician (OHST), Certified Industrial Hygienist (CIH), and Certified Environmental Auditor (CEA). These certifications demonstrate proficiency in HSE principles, regulatory compliance, and best practices within specific industries.
- How can organizations measure the return on investment (ROI) of HSE training initiatives? Measuring the ROI of HSE training initiatives involves assessing both quantitative and qualitative factors. Quantitative metrics may include reductions in accident rates, absenteeism, workers’ compensation claims, insurance premiums, and regulatory fines. Qualitative indicators such as improvements in employee morale, engagement, safety culture, and customer satisfaction also contribute to assessing ROI. Conducting pre- and post-training evaluations, surveys, and benchmarking against industry standards help organizations gauge the effectiveness and value of their HSE training programs.
I’m highly interested in studying occupational health and safety