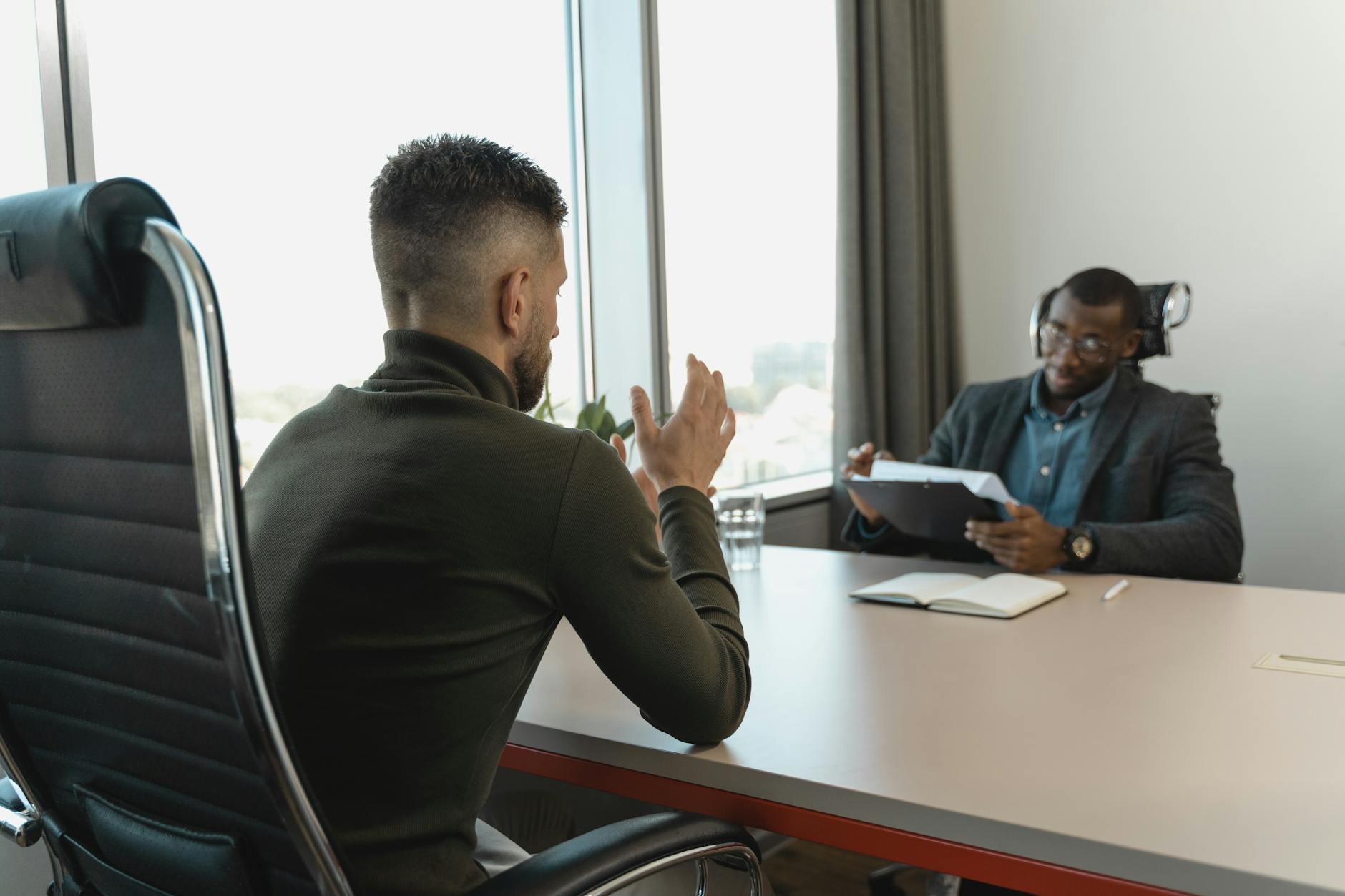
Industrial Safety Interview Questions and Answers
Here are some common industrial safety interview questions along with suggested answers:
- What is your understanding of industrial safety?
- Answer: Industrial safety refers to the measures and practices implemented to ensure the well-being of workers, the protection of the environment, and the prevention of accidents or injuries within an industrial setting. This involves the identification and mitigation of potential hazards, adherence to safety regulations, and the promotion of a culture of safety among all employees.
- Can you explain the importance of risk assessment in industrial safety?
- Answer: Risk assessment is a critical aspect of industrial safety as it involves identifying potential hazards, evaluating their severity and likelihood, and implementing measures to control or eliminate these risks. This process helps in prioritizing safety measures, allocating resources effectively, and ultimately reducing the likelihood of accidents or injuries.
- How do you ensure compliance with safety regulations in the workplace?
- Answer: Ensuring compliance involves staying informed about relevant safety regulations, conducting regular audits and inspections, providing ongoing safety training to employees, and promptly addressing any identified non-compliance issues. It also involves fostering a culture of accountability and responsibility for safety at all levels of the organization.
- What steps would you take to investigate a workplace incident or accident?
- Answer: When investigating an incident, I would follow a systematic approach. This includes securing the incident scene, gathering relevant information and witnesses’ statements, analyzing the root causes, and documenting findings. The aim is to understand what happened, why it happened, and how to prevent similar incidents in the future.
- How do you promote a culture of safety within an organization?
- Answer: Promoting a safety culture involves leading by example, encouraging open communication about safety concerns, providing regular training, recognizing and rewarding safe behaviors, and involving employees in safety decision-making processes. It’s essential to create an environment where employees feel empowered to actively contribute to and prioritize safety.
- What personal protective equipment (PPE) would you recommend for employees in a manufacturing environment?
- Answer: The specific PPE requirements depend on the nature of the manufacturing processes. Generally, it may include items such as safety helmets, gloves, eye protection, hearing protection, respiratory protection, and appropriate footwear. The selection of PPE should align with the identified risks in the workplace.
- How do you stay updated on the latest developments in industrial safety practices and regulations?
- Answer: I stay updated through continuous professional development, attending safety conferences, participating in relevant training programs, subscribing to industry publications, and actively engaging with professional safety networks. Keeping abreast of changes in regulations and best practices is crucial for maintaining a proactive approach to industrial safety.
- How do you prioritize safety when there are competing demands, such as production targets or deadlines?
- Answer: Safety is non-negotiable and must always remain a top priority. However, I believe that integrating safety into all processes enhances efficiency and productivity in the long run. I aim to strike a balance by emphasizing proactive safety measures without compromising on quality or timelines. Effective planning, resource allocation, and fostering a safety-conscious culture contribute to achieving both safety and production goals.
- Describe a challenging situation where you had to implement a safety improvement initiative. How did you approach it?
- Answer: In a previous role, we identified a high-risk area that required immediate safety improvements. I initiated a comprehensive risk assessment, involving input from relevant stakeholders, to understand the hazards. Then, I proposed a detailed action plan that included redesigning the workspace, implementing new safety protocols, and providing targeted training. Regular communication and involvement of the team ensured successful implementation and significantly reduced risks in that area.
- How do you handle resistance or lack of cooperation from employees regarding safety protocols?
- Answer: Addressing resistance involves understanding the concerns of employees and communicating the importance of safety in a transparent and respectful manner. I believe in fostering open dialogue to address misconceptions, providing clear explanations for the necessity of safety protocols, and actively involving employees in the decision-making process. Building trust and rapport while demonstrating the benefits of adherence to safety measures helps in gaining cooperation.
- Can you discuss a time when you successfully prevented a potential workplace hazard?
- Answer: In a previous role, I noticed a recurring issue with improper storage of hazardous materials. I initiated an awareness campaign and training sessions to educate employees about the correct storage procedures and risks associated with improper handling. Additionally, I redesigned the storage area to meet safety standards. This proactive approach significantly reduced the risk of potential accidents involving those materials.
- How do you ensure continuous improvement in safety standards within an organization?
- Answer: Continuous improvement in safety involves a systematic approach. Regular safety audits, analysis of incident reports and near-misses, soliciting feedback from employees, and benchmarking against industry best practices are key components. I believe in using this data to identify areas for improvement, implementing necessary changes, and ensuring that lessons learned are integrated into ongoing safety procedures.
- How do you communicate safety procedures and policies to a diverse workforce with varying levels of understanding?
- Answer: Communication is key, especially in diverse workplaces. I use multiple channels such as training sessions, visual aids, multilingual materials, and demonstrations to ensure that everyone comprehends the safety procedures. Tailoring the communication to different learning styles and languages helps in ensuring that the information is accessible and understood by all employees.
- What role do you think technology plays in enhancing industrial safety?
- Answer: Technology offers various tools that significantly improve industrial safety. For instance, the use of sensors for early hazard detection, wearable devices for monitoring workers’ health and safety, and advanced analytics for predictive maintenance and risk assessment. Integrating these technologies not only enhances safety but also provides real-time data to proactively address potential risks.
- How would you handle a situation where there’s a conflict between safety regulations and operational needs?
- Answer: In such situations, I prioritize the safety regulations as they are in place to protect employees and the environment. However, I also believe in finding solutions that meet both safety standards and operational needs. I would engage stakeholders, conduct a thorough risk assessment, explore alternative methods, and seek expert guidance to find a balanced approach that ensures safety without compromising operational efficiency.
- What steps do you take to ensure emergency preparedness and response in the workplace?
- Answer: Emergency preparedness involves thorough planning, training, and regular drills. I develop comprehensive emergency response plans that cover various scenarios, conduct training sessions for employees on emergency procedures, and regularly review and update these plans based on lessons learned from drills or incidents. Ensuring that everyone knows their roles and responsibilities during emergencies is crucial for an effective response.
- How do you encourage employees to actively participate in safety initiatives?
- Answer: I believe in creating a participatory environment where employees feel valued and empowered in contributing to safety. Encouraging feedback, recognizing and rewarding safety-conscious behaviors, involving employees in safety committees or decision-making processes, and fostering a sense of ownership towards safety initiatives are effective ways to encourage active participation.
Plant Safety Questions and Answers
How to Answer “Tell Me About Yourself” Job Interview Question?
Saudi Aramco HSE Officer Interview Questions and Sample Answers