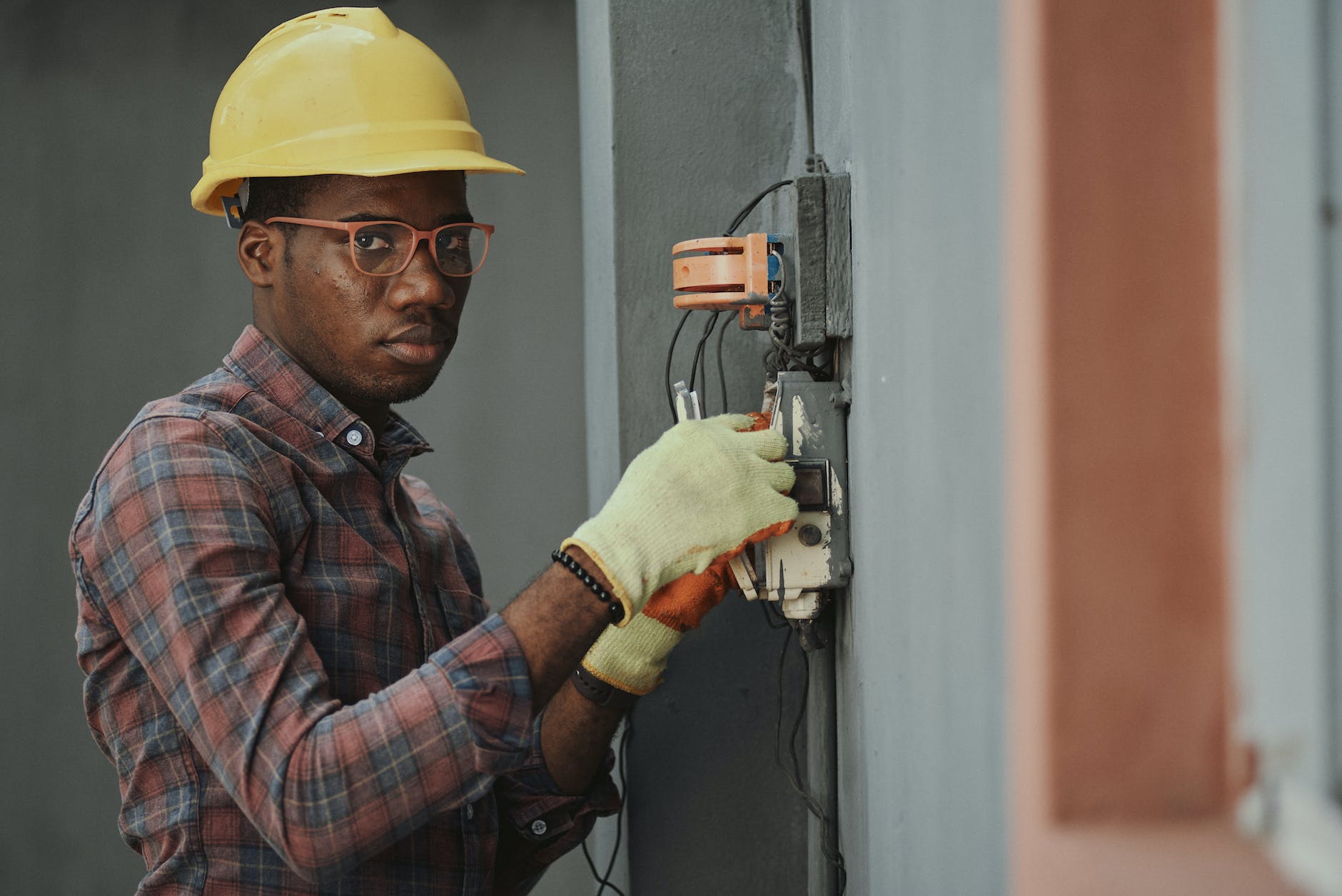
Lockout/Tagout: Procedure and Verification
In today’s fast-paced industrial landscape, ensuring the safety of workers is paramount. One critical safety procedure that stands out is Lockout/Tagout (LOTO). This article aims to delve into the intricacies of LOTO, from its basic principles to the importance of its verification process.
Introduction
Lockout/Tagout is a safety procedure designed to prevent the unexpected startup of machinery or release of hazardous energy during maintenance or servicing activities. The overarching goal is to protect workers from potentially life-threatening accidents. Workplace safety is not just a legal requirement; it’s a moral obligation that every employer should prioritize.
Understanding Lockout/Tagout
At its core, LOTO involves isolating energy sources and indicating their isolation to prevent accidents. These energy sources can include electrical, mechanical, hydraulic, pneumatic, chemical, thermal, or other forms of energy. Understanding the various energy sources covered by LOTO is crucial for its effective implementation.
OSHA Regulations and Compliance
The Occupational Safety and Health Administration (OSHA) has laid out specific regulations to ensure the proper implementation of LOTO. Businesses must comply with these standards to create a safe working environment. Non-compliance not only jeopardizes the well-being of employees but also exposes companies to legal repercussions.
Key Components of a Lockout/Tagout Program
Developing a comprehensive energy control plan is the cornerstone of any successful LOTO program. This plan should include a detailed procedure for isolating energy sources and clear guidelines for the use of energy-isolating devices. Adequate training for employees is also crucial to ensure they understand and follow the established procedures.
Procedure for Lockout/Tagout
Implementing LOTO involves a step-by-step process to isolate energy sources effectively. Employees must be trained to recognize and use the necessary equipment, including locks and tags, to ensure the safety of everyone involved. This procedure requires meticulous attention to detail and should be regularly reviewed and updated.
Verification Process
The verification process is a critical aspect of LOTO that is often overlooked. Once the energy sources are locked out, it is essential to verify that the isolation is successful. Various methods and tools can be employed to ensure that no hazardous energy is present before maintenance or servicing activities commence.
Challenges and Common Mistakes
Despite its importance, LOTO implementation comes with its share of challenges. Common mistakes include inadequate training, failure to identify all energy sources, and insufficient communication. Recognizing these challenges and learning from common errors is key to improving the overall effectiveness of LOTO programs.
Benefits of a Robust LOTO System
A robust LOTO system brings about a multitude of benefits for both employers and employees. By reducing workplace accidents and injuries, businesses can create a safer and more productive work environment. Moreover, a strong emphasis on LOTO positively influences the overall safety culture within an organization.
Technological Advancements in LOTO
As technology continues to advance, so do the tools and technologies available for LOTO. Modern solutions, such as digital lockout systems and automated verification processes, enhance the efficiency and accuracy of LOTO procedures. Adopting these advancements can significantly improve overall workplace safety.
Employee Empowerment and Involvement
Incorporating employees into the LOTO process fosters a sense of ownership and responsibility for safety. Workers should be empowered to identify potential hazards and actively participate in the development and execution of LOTO procedures. A safety-conscious work environment is a collective effort.
Continuous Improvement in LOTO
The effectiveness of LOTO procedures can be further enhanced through regular assessments and updates. Gathering feedback from employees involved in the process and incorporating their insights ensures that LOTO procedures remain relevant and effective over time.
Industry-specific Considerations
Different industries may face unique challenges when it comes to LOTO. Tailoring procedures to address specific industry needs and challenges is crucial for successful implementation. Recognizing and addressing these differences contribute to the adaptability and effectiveness of LOTO programs.
Global Perspectives on Lockout/Tagout
While OSHA regulations guide LOTO implementation in the United States, it’s essential to consider global perspectives. Various countries have their own regulations and practices regarding LOTO, and understanding these differences is vital for businesses operating on an international scale.
Lockout/Tagout (LOTO) is a safety procedure used in industries to ensure that dangerous machines are properly shut off and not able to be started up again prior to the completion of maintenance or servicing work. The procedure involves physically locking the energy-isolating device(s) to prevent the release of hazardous energy, and attaching a tag indicating that the equipment is under maintenance. Here is a general overview of the Lockout/Tagout procedure and the verification process:
Lockout/Tagout Procedure:
- Notify Employees:
- Inform all affected employees that a Lockout/Tagout procedure will be implemented.
- Identify the equipment to be locked out and communicate the reason for the lockout.
- Equipment Shutdown:
- Identify and locate the energy-isolating devices for the equipment.
- Shut down the equipment using its normal stopping procedure.
- Isolation of Energy Sources:
- Identify all energy sources associated with the equipment (electrical, mechanical, hydraulic, pneumatic, etc.).
- Isolate and lockout each energy source using appropriate lockout devices.
- Secure the isolation points with assigned locks.
- Release Stored Energy:
- Ensure that all residual or stored energy is released or dissipated.
- Test the equipment to verify that it is de-energized.
- Application of Lockout/Tagout Devices:
- Attach lockout devices to each energy-isolating device to prevent re-energization.
- Use standardized locks and tags that are durable and easily identifiable.
- Tagout:
- Attach a tag to the locked-out equipment indicating the reason for the lockout and identifying the individual who applied the lock.
- Verification of Isolation:
- Before starting maintenance work, verify that the equipment is de-energized.
- Check that all energy-isolating devices are properly locked and tagged.
- Test equipment controls to confirm they cannot be activated.
Verification Process:
- Visual Inspection:
- Conduct a visual inspection to ensure that all lockout/tagout devices are properly applied and in good condition.
- Communication:
- Communicate with the person who applied the lockout/tagout to confirm the status of the equipment and the purpose of the lockout.
- Testing:
- Test the equipment controls and components to ensure they do not operate.
- Verify that stored energy has been effectively released.
- Group Verification:
- In situations involving multiple employees, each employee should verify the lockout/tagout status independently.
- Documentation:
- Keep records of the lockout/tagout procedure, including the names of individuals involved, the equipment involved, and the date and time of the lockout.
- Removal of Lockout Devices:
- Only the employee who applied the lockout/tagout devices should remove them after ensuring that it is safe to do so.
The Lockout/Tagout procedure and verification process are critical for preventing accidents and ensuring the safety of employees during maintenance or servicing activities on machinery and equipment. Strict adherence to these procedures helps avoid the release of hazardous energy and protects workers from potential injuries.
Conclusion
In conclusion, Lockout/Tagout is not just a procedure; it’s a commitment to workplace safety. Prioritizing LOTO benefits everyone involved, from employees to employers. By understanding its principles, complying with regulations, and continuously improving procedures, businesses can create a safer work environment and mitigate the risk of accidents.
Mental Health in the Workplace: Addressing Psychological Safety as a Safety Officer
Safety Inspections: A Step-by-Step Guide for Safety Officers
Implementing and Evaluating Safety Training Programs for Employees
Occupational Health and Safety Trends: Staying Ahead as a Safety Officer
Emergency Response Planning: Best Practices for Safety Officers
Frequently Asked Questions (FAQs)
- What is Lockout/Tagout, and why is it important?
- Lockout/Tagout is a safety procedure that prevents unexpected machinery startup, protecting workers during maintenance. It’s crucial for workplace safety.
- How does OSHA regulate Lockout/Tagout?
- OSHA has specific regulations detailing the implementation of LOTO to ensure a safe working environment. Compliance is mandatory for businesses.
- Why is the verification process essential in Lockout/Tagout?
- Verification ensures that energy sources are effectively isolated, minimizing the risk of accidents during maintenance or servicing activities.
- What are the common challenges in implementing Lockout/Tagout?
- Challenges include inadequate training, failure to identify energy sources, and communication issues. Recognizing and addressing these challenges is crucial.
- How can businesses stay updated on technological advancements in Lockout/Tagout?
- Regularly monitoring industry publications and participating in safety conferences can help businesses stay informed about the latest technological advancements in LOTO.