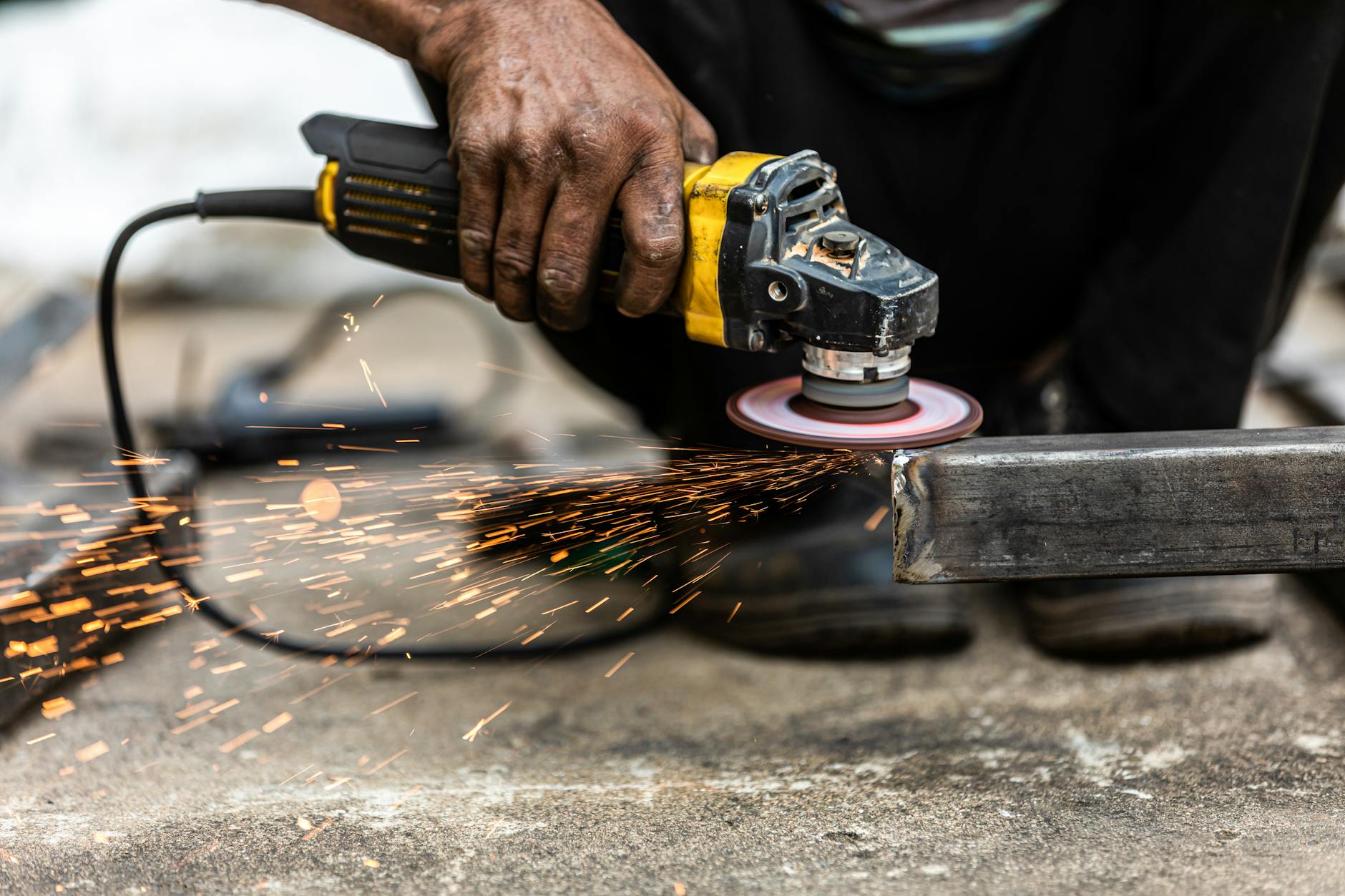
Machine Guarding: Importance and Types
Introduction
Machine guarding is a crucial aspect of workplace safety, serving as a protective barrier between workers and the potential hazards of operating machinery. This article delves into the importance of machine guarding and explores various types of guards employed to ensure a secure working environment.
Importance of Machine Guarding
- Worker Safety
- Prevention of contact with moving parts, reducing the risk of injuries
- Ensuring the well-being and health of employees operating machinery
- Compliance with Regulations
- Adherence to occupational safety and health regulations
- Compliance with standards set by organizations like OSHA to avoid legal repercussions
- Risk Mitigation
- Identification and mitigation of potential hazards associated with machinery
- Minimization of accidents and injuries through proactive safety measures
- Enhanced Productivity
- Reduced downtime due to accidents or injuries
- Improved focus and confidence among workers, leading to increased productivity
- Positive Safety Culture
- Cultivation of a workplace culture that prioritizes safety
- Encouragement of responsible machine operation and maintenance practices
Types of Machine Guards
- Fixed Guards
- Permanent barriers attached to the machine
- Effective in preventing access to moving parts during operation
- Interlocked Guards
- Linked to the machine’s control system
- Halts machine operation when the guard is opened, ensuring safety during maintenance or adjustments
- Adjustable Guards
- Customizable barriers that can be adapted to different machine sizes
- Provides flexibility while maintaining safety standards
- Self-adjusting Guards
- Automatically adjusts to the size and movement of the material being processed
- Ensures constant protection without requiring manual adjustments
- Presence-Sensing Devices
- Uses sensors to detect the presence of a worker and stop the machine
- Offers immediate response to potential danger, enhancing safety
- Two-Handed Controls
- Requires the use of both hands to operate the machine
- Ensures that hands are kept away from dangerous areas during operation
- Pullback Devices
- Utilizes cables or similar devices to pull hands away from danger zones
- Provides an additional layer of safety during machine operation
- Barrier Guards
- Physical barriers surrounding the machine to prevent access
- Suitable for large machinery or areas where multiple workers operate nearby
- Point of Operation Guards
- Shields the specific area where the machine performs its functions
- Focuses on protecting the point where the work is being conducted
- Safety Mats
- Pressure-sensitive mats that, when stepped on, stop machine operation
- Ideal for situations where frequent access to machinery is required
Best Practices in Machine Guarding Implementation
- Conducting Risk Assessments
- Regular assessment of machinery and work processes to identify potential hazards
- Customizing machine guarding solutions based on specific risks
- Employee Training
- Providing comprehensive training on machine operation and safety protocols
- Ensuring that workers are aware of the purpose and proper use of machine guards
- Routine Inspections and Maintenance
- Regularly inspecting machine guards for wear, damage, or malfunctions
- Prompt maintenance and replacement of guards to guarantee effectiveness
- Clear Communication
- Clearly communicating safety procedures and the importance of machine guarding
- Encouraging open communication between workers and management regarding safety concerns
- Continuous Improvement
- Seeking feedback from workers on the effectiveness of machine guards
- Implementing improvements based on insights from workers and safety assessments
Conclusion
In conclusion, machine guarding is not just a legal requirement but a fundamental aspect of ensuring the safety and well-being of workers. By understanding the importance of machine guarding and implementing various types of guards suited to specific needs, organizations can create a secure working environment, reduce the risk of injuries, and foster a positive safety culture.
Mental Health in the Workplace: Addressing Psychological Safety as a Safety Officer
Safety Inspections: A Step-by-Step Guide for Safety Officers
Implementing and Evaluating Safety Training Programs for Employees
Occupational Health and Safety Trends: Staying Ahead as a Safety Officer
Emergency Response Planning: Best Practices for Safety Officers
Frequently Asked Questions (FAQs)
- Why is machine guarding important in the workplace?
- Machine guarding is crucial for worker safety, compliance with regulations, risk mitigation, enhanced productivity, and the cultivation of a positive safety culture.
- What are some types of machine guards?
- Types of machine guards include fixed guards, interlocked guards, adjustable guards, self-adjusting guards, presence-sensing devices, two-handed controls, pullback devices, barrier guards, point of operation guards, and safety mats.
- How can organizations implement effective machine guarding?
- Effective machine guarding implementation involves conducting risk assessments, providing employee training, routine inspections and maintenance, clear communication, and continuous improvement based on feedback and safety assessments.