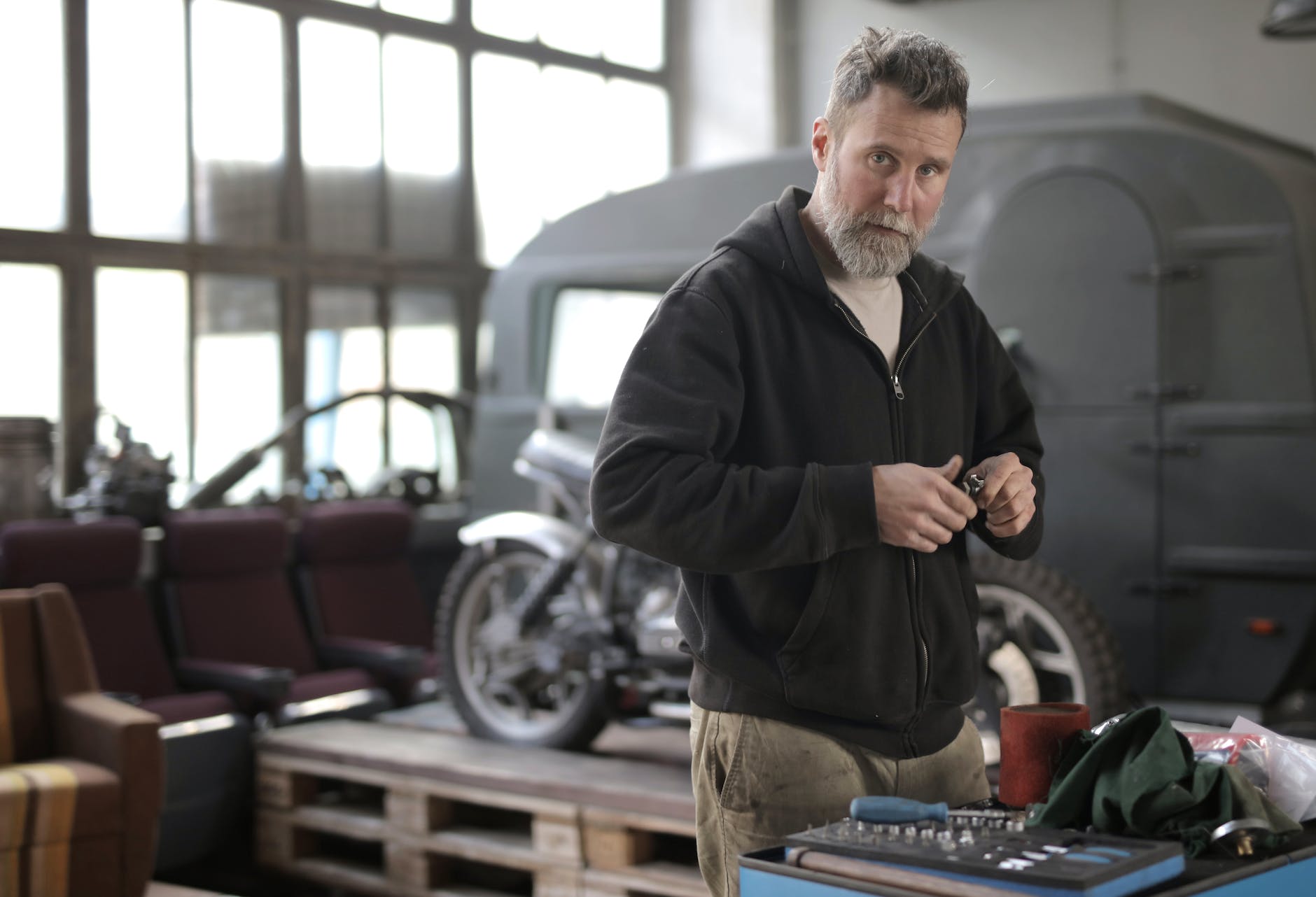
Manufacturing Workplace Mechanical Hazards: Ensuring Safety in the Industrial Setting
Introduction
Manufacturing Workplace Mechanical Hazards : In the fast-paced world of manufacturing, there’s no denying that it’s an industry that keeps the world running. However, amid the efficiency and productivity, there’s a looming threat – mechanical hazards. These hidden perils can disrupt operations, injure workers, and lead to severe accidents. In this article, we will explore the various mechanical hazards present in the manufacturing workplace and how industries can safeguard their workers and operations.
Understanding Mechanical Hazards
What are Mechanical Hazards?
Mechanical hazards in the manufacturing workplace encompass any potential source of harm that is caused by machines, equipment, or tools. These hazards can lead to various injuries, including cuts, fractures, and even fatalities. Let’s delve into some of the most common mechanical hazards and how they occur.
Types of Mechanical Hazards
1. Moving Parts Dangers
In many manufacturing settings, machinery with moving parts is the norm. These moving components can pose serious threats if not adequately safeguarded.
2. High Noise Levels
Besides the obvious hearing impairment risk, prolonged exposure to high noise levels can lead to stress and other health issues.
3. Mechanical Energies
Manufacturing equipment, including presses and stamping machines, can store mechanical energy. When released unexpectedly, it can result in severe injuries.
4. Material Handling
Material handling is a significant part of manufacturing. However, improper techniques can lead to injuries such as strains and sprains.
5. Pinch Points
Pinch points are areas where body parts or clothing can get caught between moving and stationary objects, leading to severe injuries.
Preventing Mechanical Hazards
1. Safeguarding Moving Parts
One of the primary steps in preventing mechanical hazards is safeguarding moving parts. Employing proper guarding, such as barriers or safety sensors, can significantly reduce the risk.
2. Noise Control Measures
To address high noise levels, industries should invest in noise control measures such as hearing protection and noise-reducing equipment.
3. Lockout-Tagout Procedures
Implementing lockout-tagout procedures can prevent unexpected releases of mechanical energy and ensure worker safety.
4. Training and Material Handling Equipment
Proper training and the use of ergonomic material handling equipment can minimize the risk of strains and sprains.
5. Safety Sensors
Using safety sensors can help identify pinch points and halt machinery before an injury occurs.
Conclusion
In the dynamic world of manufacturing, the importance of safety cannot be overstated. Mechanical hazards can disrupt operations and harm workers, but with the right precautions, they can be prevented. By investing in safeguarding measures, training, and safety equipment, industries can create a workplace where workers are protected, and operations run smoothly.
What is Meaning of %LEL and %UEL
Pyrophoric Materials and their Hazards and Precautions
FAQs
1. How can I protect my employees from moving parts dangers in a manufacturing setting?
- Implement proper guarding mechanisms and provide comprehensive training to employees on machine safety.
2. What are some common symptoms of hearing impairment due to high noise levels in the workplace?
- Common symptoms include tinnitus, difficulty hearing normal conversations, and stress-related health issues.
3. What is lockout-tagout, and why is it essential in the manufacturing industry?
- Lockout-tagout is a safety procedure that ensures machinery is de-energized and cannot be restarted until maintenance or repairs are completed, preventing unexpected releases of mechanical energy.
4. How can I reduce the risk of strains and sprains in material handling?
- Employ ergonomic material handling equipment, provide proper training, and encourage proper lifting techniques among employees.
5. What are safety sensors, and how do they help in identifying pinch points?
- Safety sensors are devices that can detect the presence of an object or body part and halt machinery to prevent injuries in pinch point situations.
In the modern manufacturing landscape, ensuring the safety of employees and operations is paramount. By addressing mechanical hazards through a combination of training, safety measures, and protective equipment, businesses can create a secure and efficient working environment.