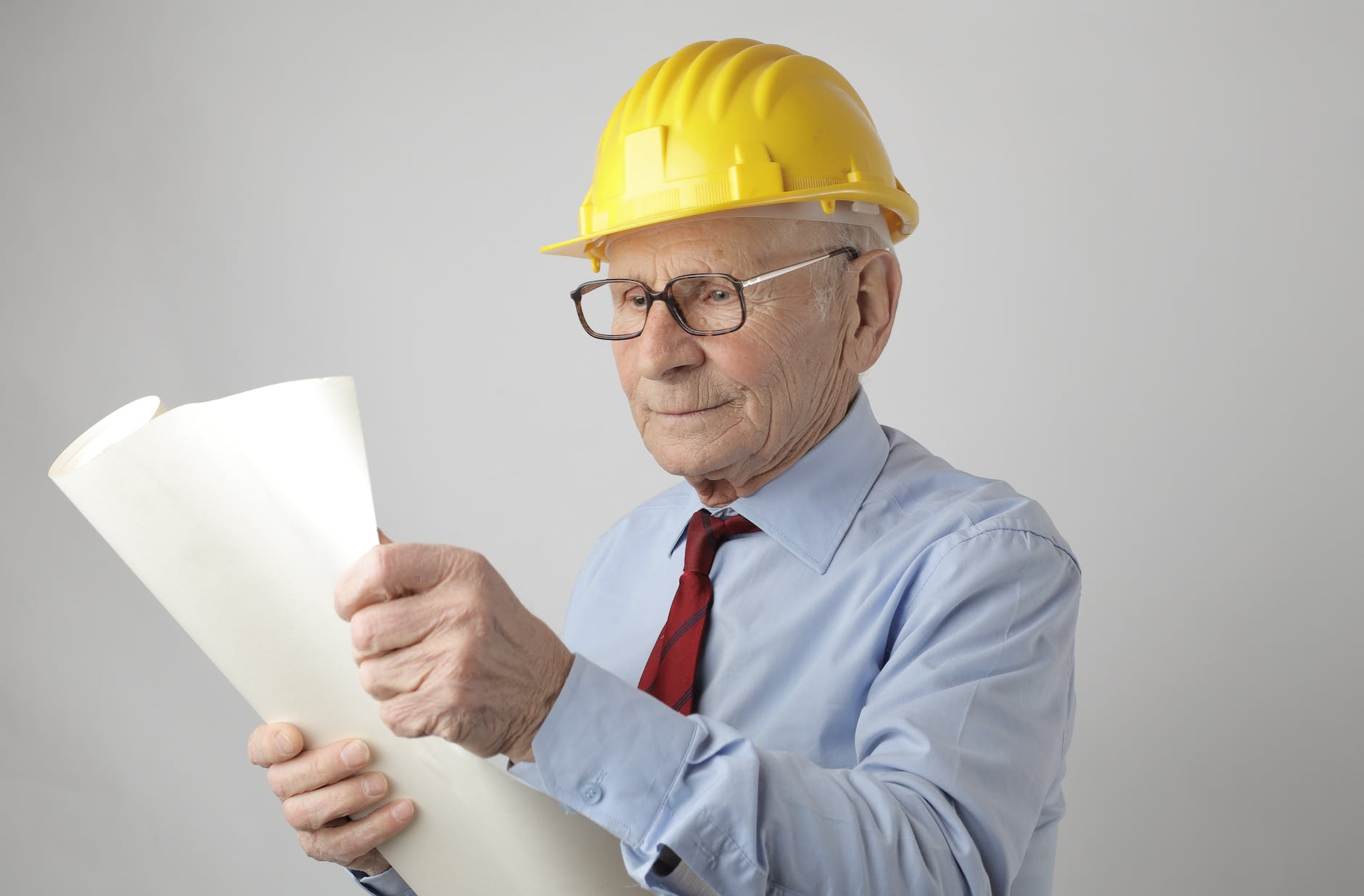
OSHA Safety Manager Requirements: Ensuring Workplace Safety
Introduction
Workplace safety is a top priority for businesses, and compliance with Occupational Safety and Health Administration (OSHA) regulations is crucial. OSHA safety managers play a pivotal role in ensuring a safe and healthy work environment. In this article, we’ll delve into the requirements for becoming an OSHA safety manager, the responsibilities associated with the role, and the benefits for both employees and employers.
Qualifications for OSHA Safety Manager
To become an OSHA safety manager, individuals must meet specific qualifications. A combination of educational background, professional experience, and OSHA-specific training is essential. A bachelor’s degree in occupational health and safety or a related field is often a prerequisite. Additionally, candidates should have relevant work experience and complete OSHA-approved training programs.
Responsibilities of an OSHA Safety Manager
OSHA safety managers are responsible for overseeing and implementing safety measures within a workplace. This includes conducting regular safety inspections, ensuring compliance with OSHA standards, and developing and implementing safety protocols. Their role is vital in creating a culture of safety and minimizing workplace hazards.
OSHA Certification Process
The certification process for OSHA safety managers involves passing a comprehensive exam. This exam covers various aspects of occupational safety, including hazard recognition, safety regulations, and emergency response procedures. Continuous education is crucial, and certified individuals must renew their certification periodically to stay abreast of evolving safety standards.
The Occupational Safety and Health Administration (OSHA) sets standards and regulations to ensure workplace safety in the United States. While there isn't a specific designation for an "OSHA safety manager," many companies designate individuals to oversee and implement OSHA compliance. Here are some general guidelines and qualifications that individuals responsible for OSHA compliance often possess:
- Education:
- A bachelor’s degree in occupational safety and health, industrial hygiene, environmental science, or a related field is often preferred.
- Relevant certifications, such as Certified Safety Professional (CSP) or Associate Safety Professional (ASP), may enhance qualifications.
- Experience:
- Practical experience in safety management is crucial. This may involve working in roles such as safety coordinator, safety specialist, or a related position.
- Familiarity with the specific industry and its associated hazards is beneficial.
- Knowledge of OSHA Regulations:
- A thorough understanding of OSHA standards and regulations is essential. This includes knowledge of general industry standards (29 CFR 1910) or construction standards (29 CFR 1926), depending on the workplace.
- Communication Skills:
- Strong communication skills are necessary to effectively convey safety policies and procedures to employees at all levels.
- The ability to conduct safety training sessions and effectively communicate with regulatory agencies is important.
- Risk Assessment and Hazard Analysis:
- Competence in identifying and assessing workplace hazards and developing strategies to mitigate risks is crucial.
- Experience in conducting job hazard analyses (JHAs) and implementing corrective measures.
- Emergency Preparedness:
- Knowledge of emergency response procedures and the ability to develop and implement emergency action plans (EAPs).
- Recordkeeping:
- Proficiency in maintaining accurate records related to safety inspections, incidents, training, and other relevant documentation.
- Leadership and Teamwork:
- Leadership skills to effectively lead safety committees or teams and foster a culture of safety within the organization.
- Regulatory Compliance:
- Keeping up-to-date with changes in OSHA regulations and ensuring the organization’s compliance.
- Continuous Improvement:
- A commitment to ongoing learning and improvement in safety processes and procedures.
Companies may have specific requirements based on their industry, size, and the nature of their operations. It's important for individuals in safety management roles to stay informed about changes in regulations and best practices to ensure a safe working environment.
Benefits of Hiring an OSHA Safety Manager
Businesses that invest in OSHA safety managers reap numerous benefits. Improved workplace safety leads to fewer accidents and injuries, reducing the company’s liability. Moreover, compliance with OSHA regulations enhances the company’s reputation, attracting both clients and employees who prioritize safety.
Challenges in OSHA Compliance
Staying compliant with OSHA regulations poses challenges, such as keeping up with evolving standards and addressing common compliance issues. However, companies must embrace continuous improvement and invest in resources to overcome these challenges.
OSHA Safety Manager’s Role in Emergency Preparedness
Emergency preparedness is a critical aspect of OSHA safety management. Safety managers must create and regularly update emergency response plans, conduct drills, and ensure that employees are well-trained to handle unexpected situations. Equipment readiness is also a key consideration.
Case Studies
Examining real-world examples of successful OSHA compliance and learning from incidents of non-compliance provides valuable insights. Case studies illustrate the importance of adherence to safety regulations and the consequences of neglecting them.
OSHA Safety Manager vs. Safety Committee
While OSHA safety managers play a central role, collaboration with safety committees is essential. Understanding the differences between the two and fostering cooperation ensures a comprehensive approach to workplace safety.
Common Misconceptions about OSHA Safety Managers
Dispelling myths and misinformation surrounding the role of OSHA safety managers is crucial. Clarifying responsibilities helps companies and employees better understand the significance of this position.
Tips for Companies to Ensure OSHA Compliance
Regular training programs, internal audits, and encouraging employee involvement in safety initiatives are essential for maintaining OSHA compliance. Companies must prioritize ongoing efforts to create a safe working environment.
OSHA Safety Manager Success Stories
Recognizing outstanding contributions by OSHA safety managers and highlighting their impact on workplace culture serves as inspiration for others. Success stories motivate businesses to invest in safety management.
Conclusion
In conclusion, OSHA safety managers are indispensable for ensuring workplace safety. Businesses must prioritize the qualifications, responsibilities, and continuous education of safety managers to create a secure work environment. By doing so, companies not only comply with regulations but also foster a culture of safety that benefits everyone.
How To Become OSHA Safety Manager 2024
How To Become OSHA Safety Engineer 2024
How To Become OSHA Safety Officer 2024
OSHA Fall Protection Plan Requirements
FAQs
Q: What are the primary qualifications for an OSHA Safety Manager? A: OSHA Safety Managers typically need a bachelor’s degree in occupational health and safety, relevant work experience, and completion of OSHA-approved training programs.
Q: How often should OSHA safety training be conducted? A: OSHA safety training should be conducted regularly, with frequency determined by the nature of the workplace and any changes in regulations.
Q: Can a company handle OSHA compliance without a dedicated safety manager? A: While possible, having a dedicated OSHA safety manager greatly enhances a company’s ability to navigate and adhere to OSHA regulations effectively.
Q: What are the consequences of OSHA non-compliance? A: Consequences of OSHA non-compliance may include fines, legal actions, increased insurance premiums, and damage to the company’s reputation.
Q: How can businesses stay updated on changing OSHA regulations? A: Businesses can stay updated on changing OSHA regulations by regularly checking the official OSHA website, participating in industry conferences, and enrolling in OSHA-approved training programs.