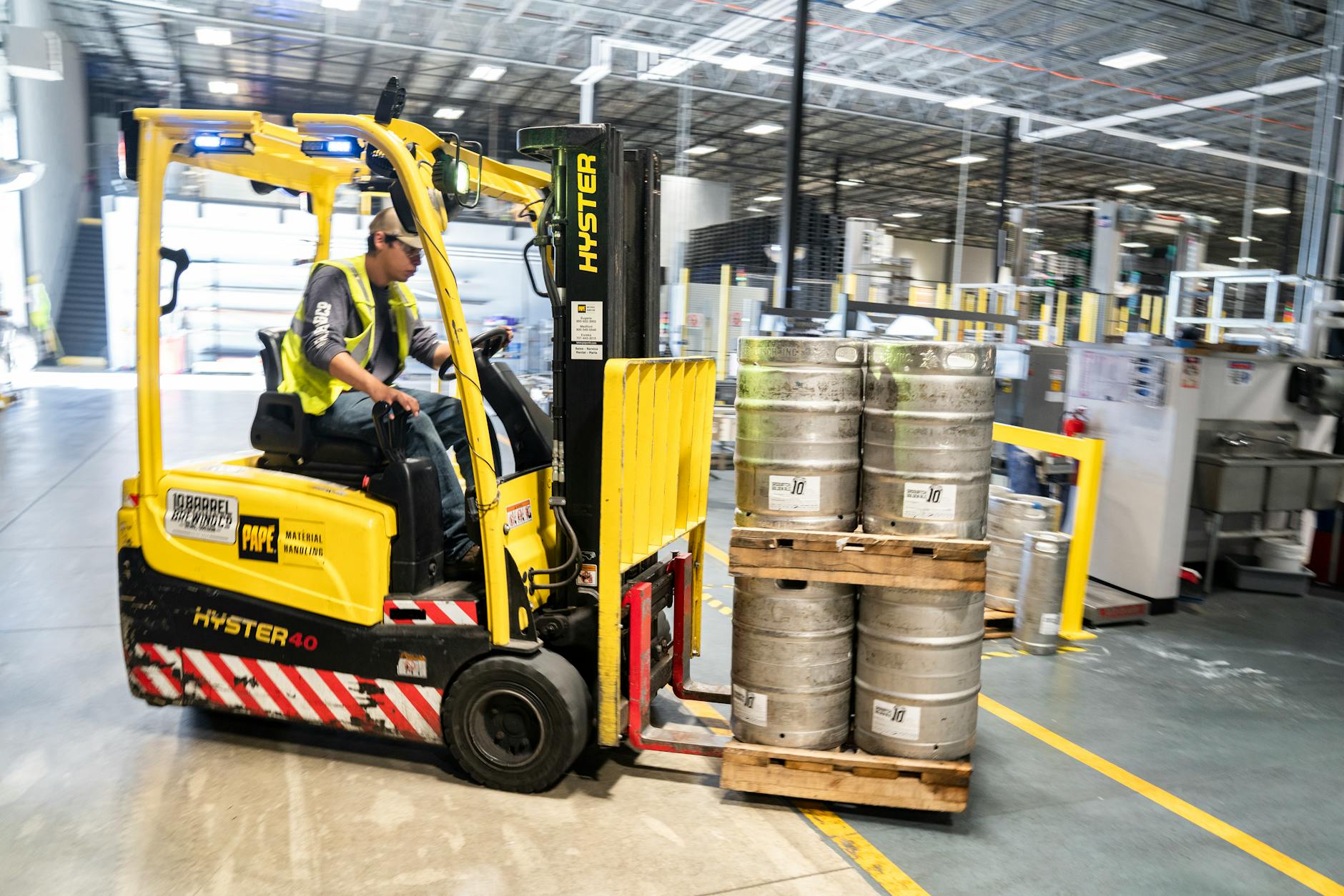
Powered Industrial Truck Safety: Forklift Operation and Maintenance
Introduction
Powered industrial trucks, commonly known as forklifts, play a vital role in material handling and warehouse operations. However, their operation comes with inherent risks that necessitate strict safety measures. This article explores the key aspects of forklift safety, focusing on both operation and maintenance to ensure a secure working environment.
Forklift Operation Safety
- Operator Training and Certification
- Comprehensive Training: Ensure operators undergo thorough training covering forklift operation, load handling, and safety protocols.
- Certification Programs: Encourage operators to obtain certification to validate their competence in safe forklift operation.
- Pre-Operational Checks
- Visual Inspection: Conduct pre-operational checks to visually inspect the forklift for any visible issues.
- Functional Tests: Ensure all controls, brakes, and safety features are in proper working condition before each use.
- Load Handling Protocols
- Load Capacity Awareness: Train operators to be aware of the forklift’s load capacity and avoid exceeding it.
- Secure Loading: Emphasize the importance of securing loads properly to prevent shifting during transport.
- Pedestrian Safety Measures
- Designated Walkways: Establish clear pedestrian walkways separated from forklift traffic.
- Horn Usage: Encourage the use of horns to alert pedestrians to the presence of a moving forklift.
- Safe Driving Practices
- Appropriate Speeds: Enforce safe driving speeds, especially in congested areas.
- No Unauthorized Riders: Strictly prohibit unauthorized individuals from riding on the forklift.
- Parking and Shutdown Procedures
- Secure Parking: Instruct operators to park forklifts in designated areas with the forks lowered and the parking brake engaged.
- Shutdown Protocol: Establish a shutdown protocol that includes turning off the ignition and removing the key after use.
Forklift Maintenance Best Practices
- Regular Inspections
- Scheduled Checks: Implement a routine inspection schedule for all forklifts to identify and address potential issues promptly.
- Documentation: Maintain detailed records of inspections, repairs, and maintenance activities.
- Battery Maintenance for Electric Forklifts
- Charging Guidelines: Adhere to manufacturer-recommended charging guidelines for electric forklift batteries.
- Watering Procedures: Follow proper procedures for watering lead-acid batteries to ensure optimal performance.
- Tire Inspection and Replacement
- Tread Wear Checks: Regularly inspect tire treads for wear and tear.
- Timely Replacement: Replace tires as soon as signs of excessive wear or damage are observed.
- Oil and Fluid Checks
- Fluid Levels: Monitor oil, hydraulic fluid, and coolant levels regularly.
- Scheduled Changes: Adhere to scheduled oil and fluid changes as recommended by the manufacturer.
- Brake System Maintenance
- Brake Inspections: Regularly inspect and test the forklift’s braking system.
- Prompt Repairs: Address any brake issues immediately to prevent accidents and ensure prompt stopping.
- Mast and Fork Inspection
- Structural Integrity: Inspect the mast and forks for any signs of damage or misalignment.
- Lubrication: Ensure proper lubrication of the mast and fork components to prevent friction-related issues.
Training and Communication Strategies
- Periodic Refresher Training
- Skill Reinforcement: Conduct periodic refresher training to reinforce safe forklift operation practices.
- Updated Information: Keep operators informed about any changes in regulations or best practices.
- Communication Channels
- Feedback Mechanisms: Establish channels for operators to provide feedback on safety concerns or equipment issues.
- Regular Meetings: Conduct regular safety meetings to address concerns, share updates, and reinforce safety culture.
Conclusion
Forklift safety is a shared responsibility that involves both operators and maintenance teams. By prioritizing comprehensive training, strict adherence to safety protocols, and regular maintenance practices, workplaces can create an environment where forklifts operate safely and efficiently, reducing the risk of accidents and ensuring the well-being of personnel.
Transportation Safety Engineering: Ensuring Safe Operations in the Transportation Sector
Crane Hazards and Control Measures
Web Sling Capacity Calculation
Frequently Asked Questions (FAQs)
- Why is operator training crucial for forklift safety?
- Operator training is crucial to ensure operators are competent in forklift operation, load handling, and adherence to safety protocols, reducing the risk of accidents.
- What are the key components of forklift maintenance?
- Key components of forklift maintenance include regular inspections, battery maintenance for electric forklifts, tire inspection and replacement, oil and fluid checks, brake system maintenance, and mast and fork inspection.
- How can workplaces reinforce forklift safety culture?
- Workplaces can reinforce forklift safety culture through periodic refresher training, open communication channels for feedback, and regular safety meetings to address concerns and share updates.
- Why is pedestrian safety important in forklift operation?
- Pedestrian safety is crucial in forklift operation to prevent accidents. Establishing designated walkways, using horns to alert pedestrians, and enforcing safe driving practices contribute to pedestrian safety.