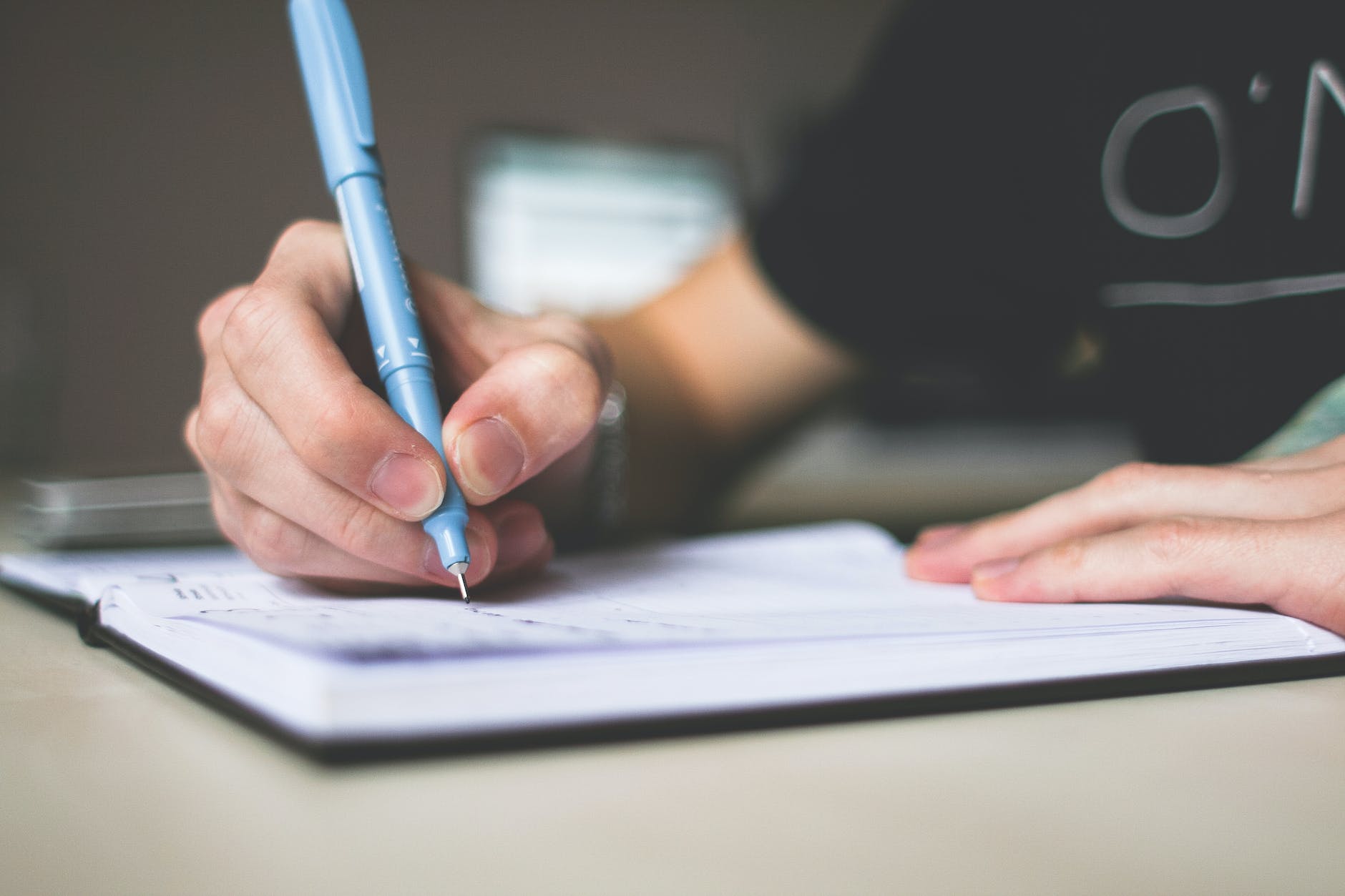
Root Cause Analysis Example
Introduction to Root Cause Analysis
Root Cause Analysis (RCA) is a crucial process in problem-solving that aims to identify the underlying causes of an issue rather than just addressing its symptoms. It goes beyond surface-level fixes, providing a comprehensive understanding of problems and ensuring long-lasting solutions.
The Basics of Root Cause Analysis
Before delving into real-world examples, it’s essential to grasp the fundamentals of root cause analysis. Begin by clearly defining the problem, understanding the scope, and establishing specific goals for the analysis. This sets the stage for a focused and effective investigation.
Common Techniques for Root Cause Analysis
Several techniques aid in the root cause analysis process. The “5 Whys” involves asking “why” repeatedly to get to the core issue. The fishbone diagram visually represents potential causes, while Failure Mode and Effects Analysis (FMEA) assesses potential failures and their consequences.
Here's an example of a root cause analysis:
Problem Statement: The production line in a manufacturing plant is experiencing frequent stoppages, leading to decreased productivity and increased downtime.
Root Cause Analysis:
- Identify the Problem:
- Production line stoppages are occurring frequently, leading to reduced productivity and increased downtime.
- Gather Data:
- Collect data on the frequency and duration of production line stoppages.
- Analyze maintenance records, operator logs, and equipment performance reports.
- Interview operators, maintenance personnel, and supervisors to gather insights.
- Identify Possible Causes:
- Equipment Failure: Machinery breakdowns may be causing stoppages.
- Operator Error: Lack of training or adherence to standard operating procedures.
- Maintenance Issues: Inadequate preventive maintenance or delayed repairs.
- Material Shortages: Lack of necessary materials causing production line stoppages.
- Environmental Factors: Temperature, humidity, or other external conditions affecting equipment performance.
- Perform Root Cause Analysis:
- Conduct a Fishbone Diagram (Ishikawa Diagram) to identify potential root causes under categories like Man, Machine, Material, Method, Measurement, Environment.
- Use the 5 Whys technique to drill down to the underlying cause of each identified factor. Ask “Why?” repeatedly to trace back to the root cause.
- Determine Root Causes:
- Equipment Failure: Insufficient maintenance leading to breakdowns.
- Operator Error: Inadequate training on equipment operation and maintenance procedures.
- Maintenance Issues: Reactive maintenance instead of preventive maintenance schedule.
- Material Shortages: Poor inventory management leading to stockouts.
- Environmental Factors: Inadequate climate control measures in the production area.
- Develop Solutions:
- Implement a preventive maintenance program to regularly inspect and maintain equipment.
- Provide comprehensive training for operators on equipment operation and maintenance protocols.
- Improve inventory management systems to prevent material shortages.
- Enhance climate control measures to stabilize environmental conditions in the production area.
- Implement Solutions:
- Roll out the preventive maintenance program and schedule regular equipment inspections.
- Conduct training sessions for operators on proper equipment handling and maintenance.
- Revise inventory management processes to ensure adequate stock levels.
- Install climate control systems or make adjustments to existing infrastructure.
- Monitor and Evaluate:
- Track production line performance metrics, including downtime and productivity.
- Monitor equipment reliability and maintenance schedules.
- Gather feedback from operators and maintenance staff on the effectiveness of implemented solutions.
- Continuously assess and adjust strategies to address any emerging issues.
By following these steps, the manufacturing plant can effectively identify and address the root causes of production line stoppages, leading to improved productivity and reduced downtime.
Benefits of Root Cause Analysis
The benefits of root cause analysis extend beyond immediate problem resolution. It helps prevent the recurrence of issues, enhances organizational learning, and contributes to a culture of continuous improvement. Investing time in thorough analysis yields long-term benefits.
Challenges in Root Cause Analysis
While root cause analysis is powerful, it comes with its set of challenges. Overcoming common obstacles and ensuring accuracy in the analysis process is crucial. This involves addressing biases, relying on accurate data, and fostering a collaborative approach within teams.
Successful Implementation Stories
Numerous companies have successfully implemented root cause analysis to address complex issues. These success stories highlight the positive outcomes that result from a commitment to thorough problem-solving and continuous improvement.
Conclusion
In conclusion, root cause analysis is a valuable tool for organizations aiming to address complex problems at their core. By going beyond surface-level fixes, businesses can implement lasting solutions and foster a culture of continuous improvement. The investment in time and resources for root cause analysis pays off in long-term efficiency and effectiveness.
FAQs
- What industries commonly use root cause analysis?
- Root cause analysis is widely used in industries such as manufacturing, healthcare, aviation, and information technology, where identifying and addressing the underlying causes of issues is critical.
- How long does a typical root cause analysis process take?
- The duration varies depending on the complexity of the problem. It can range from a few days to several weeks, with an emphasis on thoroughness rather than speed.
- Can individuals use root cause analysis for personal problem-solving?
- Yes, the principles of root cause analysis can be applied to personal problem-solving. It helps individuals understand the root causes of issues and implement effective solutions.
- What role does data play in the analysis?
- Data is crucial in root cause analysis as it provides evidence for the identified issues. Accurate and relevant data ensures a more precise analysis and effective decision-making.