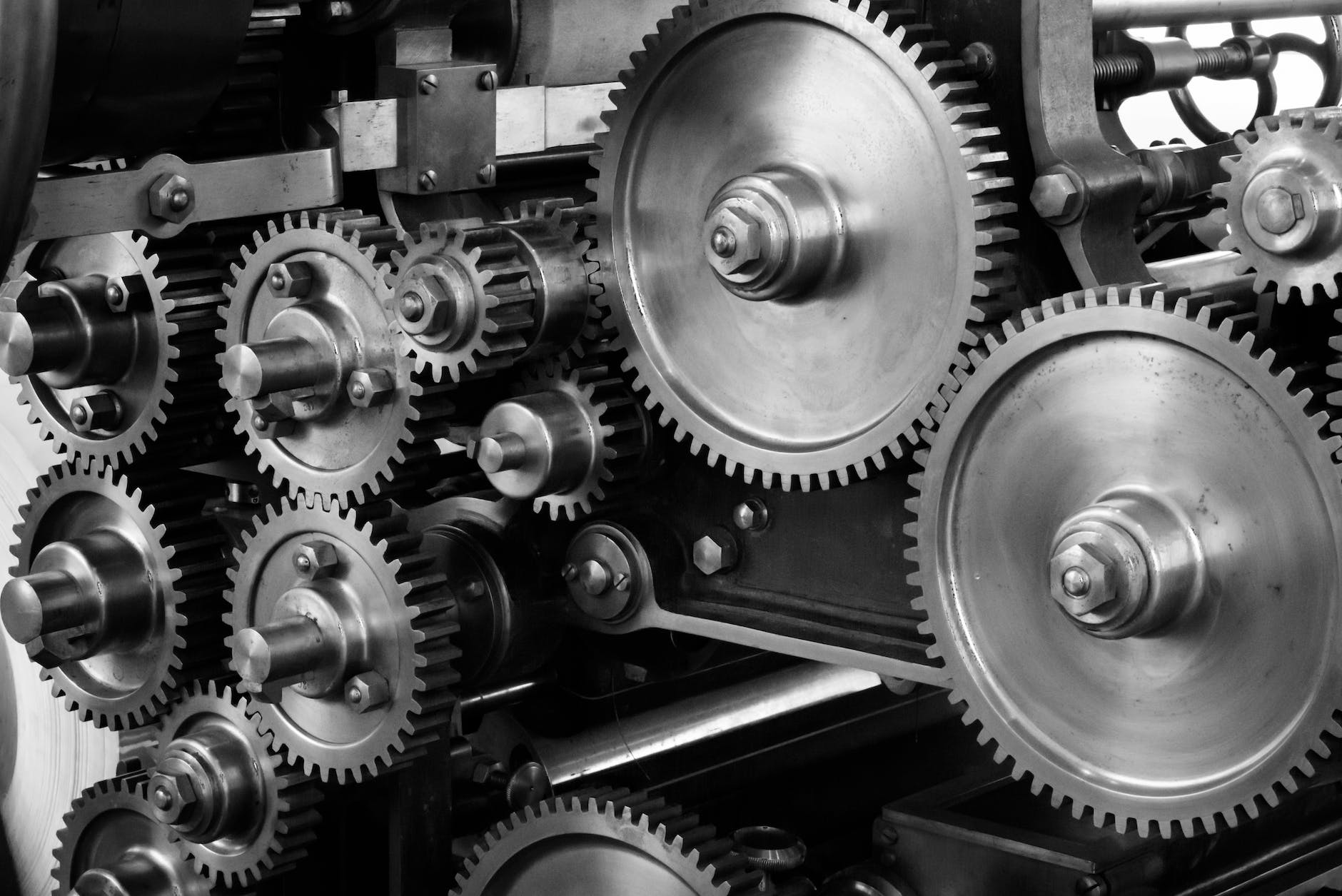
Safe Operating Procedures for Machinery
Safe Operating Procedures for Machinery : Machinery plays a vital role in numerous industries, aiding productivity and efficiency. However, the operation of machinery involves inherent risks that can pose significant dangers to workers if not handled correctly. This article delves into the crucial aspects of safe operating procedures for machinery to ensure a secure working environment.
Understanding Machinery Risks
Importance of Safety Measures
Safety within any workspace is paramount, especially when dealing with machinery. Understanding the potential risks associated with machinery operation underscores the necessity of implementing stringent safety measures.
Common Machinery Hazards
Identifying common hazards in machinery operation is crucial. These hazards may include moving parts, electrical risks, ergonomic issues, and potential exposure to harmful substances.
Creating a Comprehensive Safe Operating Procedure
Identifying Risks and Hazards
The first step in establishing safe operating procedures involves conducting a thorough risk assessment. This process entails identifying potential hazards and evaluating their level of risk.
Equipment Maintenance and Inspection
Regular maintenance and inspection of machinery are vital to ensure optimal functionality and minimize risks. Implementing a routine check-up schedule mitigates the chances of malfunctions or breakdowns.
Training and Communication
A well-informed workforce significantly contributes to a safer working environment. Adequate training on machinery operation, coupled with clear communication of safety protocols, empowers employees to handle machinery effectively.
Implementing Safe Operating Procedures
Steps to Safely Operate Machinery
A detailed set of guidelines for operating specific machinery is imperative. This section will detail step-by-step instructions, emphasizing safety protocols to follow during operation.
Emergency Protocols
Unforeseen circumstances may arise despite meticulous precautions. Establishing emergency protocols ensures swift and effective responses to mitigate potential accidents.
The Role of Compliance and Regulations
Adhering to industry-specific regulations and compliance standards is non-negotiable. Compliance not only ensures legal obligations are met but also reinforces a culture of safety within the organization.
Continuous Improvement and Evaluation
Continuous evaluation of operating procedures allows for refinement and adaptation. This iterative process fosters a culture of continuous improvement in safety protocols.
Safe Operating Procedures for Machinery
Operating machinery demands strict adherence to safety protocols to prevent accidents and ensure the well-being of operators. Here’s a comprehensive guide to safe operating procedures:
1. Training and Competency
- Training Programs: Ensure operators undergo comprehensive training specific to each machinery type they operate.
- Competency Evaluation: Assess operator competency before allowing them to work independently.
2. Pre-Operational Checks
- Inspect Machinery: Conduct thorough checks to ensure the machinery is in proper working condition, checking for any damage, leaks, or malfunctions.
- Verify Controls: Ensure all control systems are functioning correctly and emergency stop mechanisms are operational.
3. Personal Protective Equipment (PPE)
- Usage of PPE: Mandate the use of appropriate PPE, including helmets, goggles, gloves, and safety footwear, as per the machinery’s requirements.
4. Operational Procedures
- Start-Up Protocol: Follow the manufacturer’s recommended start-up procedures for the specific machinery.
- Operate Within Capacity: Ensure operators understand the machinery’s limitations and operate within its designated capacity.
5. Safe Handling of Materials
- Guidelines for Materials: Establish protocols for safe handling, lifting, and transporting materials using the machinery.
- Secure Loads: Ensure loads are properly secured before lifting or moving.
6. Clear Communication
- Effective Communication: Maintain clear communication between operators and other personnel working around the machinery to prevent accidents.
- Signage and Warnings: Use visible signage to indicate machinery operation zones and potential hazards.
7. Emergency Procedures
- Emergency Protocols: Establish clear procedures for responding to emergencies or equipment malfunctions.
- Emergency Contacts: Display emergency contact information prominently.
8. Regular Maintenance and Inspections
- Scheduled Maintenance: Follow a routine maintenance schedule as recommended by the manufacturer.
- Prompt Repairs: Address any malfunctions or issues immediately to prevent further complications.
9. Lockout/Tagout Procedures
- Energy Control: Implement lockout/tagout procedures during maintenance to prevent accidental machinery start-up.
10. Operator Fatigue and Mental Alertness
- Managing Fatigue: Avoid assigning complex machinery operations to fatigued operators to prevent accidents due to lack of focus.
- Mental Alertness: Encourage operators to stay mentally alert and vigilant during machinery operation.
Implementing and strictly adhering to these safe operating procedures for machinery significantly reduce the risk of accidents, ensuring the safety of operators and those working in the vicinity.
Conclusion
Prioritizing safe operating procedures for machinery is indispensable in maintaining a secure work environment. By identifying risks, implementing stringent protocols, and fostering a culture of continuous improvement, workplaces can significantly mitigate hazards associated with machinery operation.
Safe Operating Procedure for Bar Bending Machine
Safe Operating Procedure for Working at Height
Safe Operating Procedure (SOP)
7 Types of Permit To Work (PTW)
Frequently Asked Questions (FAQs)
- Why are safe operating procedures crucial for machinery? Safe operating procedures minimize risks and ensure the safety of individuals operating machinery within a workplace.
- How frequently should machinery be inspected for safety purposes? Regular inspections should occur based on manufacturer recommendations and usage frequency.
- What role does employee training play in ensuring machinery safety? Proper training equips employees with the necessary knowledge to operate machinery safely, reducing the likelihood of accidents.
- Are there specific regulations that govern machinery safety? Yes, various regulatory bodies set standards and guidelines for machinery safety, varying across industries.
- How can companies encourage a culture of safety regarding machinery operation? Companies can promote safety culture through regular training, clear communication of protocols, and fostering an environment that values safety above all.