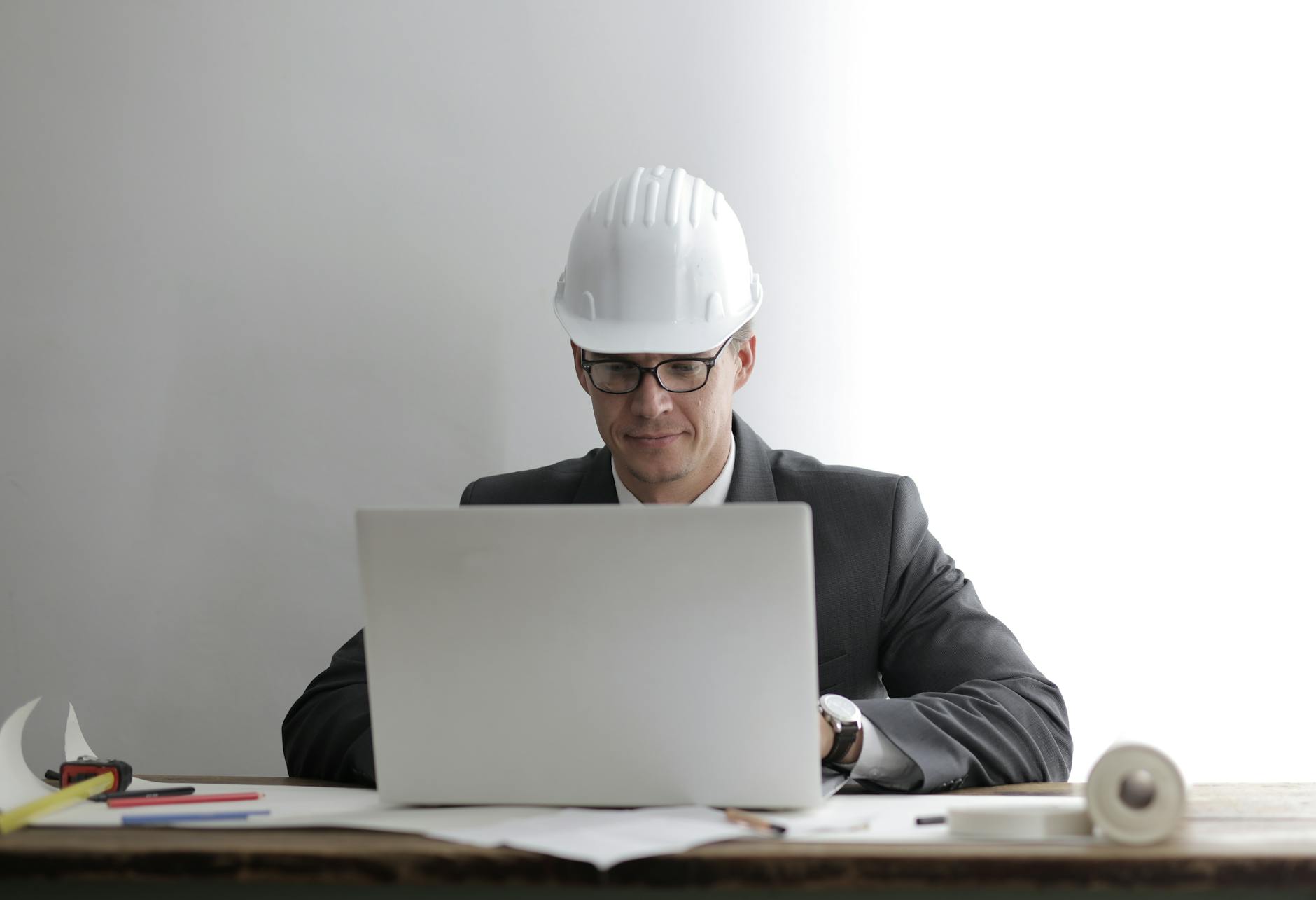
Safety Management Plan Example
Safety in the workplace is paramount to the well-being of employees and the success of a business. A Safety Management Plan serves as a comprehensive strategy to identify, assess, and mitigate risks, ensuring a safe environment for all. In this article, we will explore what a Safety Management Plan entails and provide a practical example to illustrate its implementation.
What is a Safety Management Plan?
A Safety Management Plan is a documented framework that outlines an organization’s approach to managing workplace safety. It encompasses policies, procedures, and protocols designed to prevent accidents, injuries, and illnesses. By systematically addressing potential hazards and implementing control measures, a Safety Management Plan aims to create a secure and healthy work environment.
Importance of having a Safety Management Plan
Having a Safety Management Plan in place is essential for several reasons. Firstly, it demonstrates a commitment to safety from management, fostering a culture of accountability and responsibility among employees. Secondly, it helps identify and mitigate risks before they escalate into incidents, minimizing downtime and loss of productivity. Additionally, a well-executed Safety Management Plan can enhance employee morale, engagement, and retention, as workers feel valued and protected in their workplace.
Components of a Safety Management Plan
A comprehensive Safety Management Plan comprises several key components, each playing a vital role in ensuring workplace safety.
Risk Assessment
Before developing a Safety Management Plan, organizations must conduct a thorough risk assessment to identify potential hazards and evaluate their likelihood and severity. This involves examining various aspects of the work environment, including equipment, processes, and human factors, to pinpoint areas of concern.
Hazard Identification
Once risks have been identified, the next step is to systematically identify specific hazards within the workplace. Hazards can include anything that has the potential to cause harm, such as chemical substances, machinery, ergonomic issues, or environmental factors. By documenting and categorizing hazards, organizations can prioritize them based on their level of risk and develop appropriate control measures.
Emergency Response Procedures
In the event of an emergency, prompt and effective response is crucial to minimizing harm and ensuring the safety of personnel. A Safety Management Plan should outline clear procedures for responding to various emergencies, such as fires, natural disasters, medical incidents, or security threats. This includes establishing evacuation routes, designating assembly points, and providing training on emergency protocols.
Training and Education
Employees play a vital role in maintaining workplace safety, and adequate training and education are essential to equip them with the knowledge and skills necessary to identify hazards, follow safety procedures, and respond appropriately to emergencies. A Safety Management Plan should include provisions for ongoing training and awareness programs tailored to the specific needs of the workforce.
Documentation and Record Keeping
Documentation is a critical aspect of safety management, providing a record of policies, procedures, incidents, inspections, and training activities. Maintaining accurate and up-to-date records allows organizations to track their safety performance, identify trends, and demonstrate compliance with regulatory requirements. A Safety Management Plan should establish protocols for documenting safety-related information and ensure that records are easily accessible and securely maintained.
Developing a Safety Management Plan
Developing a Safety Management Plan requires careful planning and collaboration across all levels of the organization. The following steps outline the process of creating a comprehensive and effective plan:
Gathering Information
Begin by gathering information about the organization’s operations, processes, hazards, and regulatory requirements. This may involve conducting site inspections, reviewing incident reports, consulting with employees, and researching industry best practices.
Setting Objectives
Based on the information gathered, establish clear objectives for the Safety Management Plan. These objectives should align with the organization’s overall goals and priorities and reflect a commitment to continuous improvement in safety performance.
Assigning Responsibilities
Identify key stakeholders responsible for implementing and overseeing the Safety Management Plan. Assign specific roles and responsibilities to individuals or teams, ensuring accountability and clarity regarding who is responsible for various aspects of safety management.
Implementation and Monitoring
Once the plan is developed, implement it systematically across the organization. Monitor its effectiveness regularly through inspections, audits, incident investigations, and performance metrics. Continuously evaluate and adjust the plan as needed to address emerging risks and improve safety outcomes.
Safety Management Plan Example
To illustrate the principles outlined above, let’s consider a hypothetical example of a Safety Management Plan for a manufacturing facility.
Introduction to the Example
Our example organization, XYZ Manufacturing, specializes in producing industrial machinery. With a workforce of 150 employees operating in a large factory setting, safety is a top priority to prevent accidents and ensure compliance with regulatory standards.
Risk Assessment Example
XYZ Manufacturing conducts a comprehensive risk assessment to identify potential hazards associated with its operations, including machinery hazards, electrical hazards, chemical exposure, and ergonomic risks. Through site inspections, hazard mapping, and employee input, the organization identifies high-risk areas and prioritizes them for mitigation.
Hazard Identification Example
Following the risk assessment, XYZ Manufacturing systematically identifies specific hazards within the workplace, such as unguarded machinery, exposed electrical wiring, and improper storage of hazardous materials. Each hazard is documented, evaluated for its severity and likelihood, and categorized according to its potential impact on employee safety.
Emergency Response Procedures Example
In preparation for emergencies, XYZ Manufacturing develops clear and concise emergency response procedures tailored to its unique operational environment. This includes establishing emergency evacuation routes, designating emergency response teams, and conducting regular drills to ensure that employees are familiar with emergency protocols and procedures.
Training and Education Example
To empower employees to contribute to a safe work environment, XYZ Manufacturing invests in comprehensive training and education programs. New hires receive orientation training covering safety policies, procedures, and hazard awareness, while ongoing training sessions and toolbox talks reinforce safety practices and address emerging concerns.
Documentation and Record Keeping Example
XYZ Manufacturing maintains detailed documentation of its safety activities, including incident reports, inspection records, training records, and safety meeting minutes. This information is stored securely and accessible to authorized personnel for review and analysis. Regular audits ensure that documentation remains accurate, up-to-date, and compliant with regulatory requirements.
Conclusion
A well-designed Safety Management Plan is essential for protecting employees, minimizing risks, and promoting a culture of safety within an organization. By systematically addressing potential hazards, implementing control measures, and fostering a proactive approach to safety, organizations can create a secure and healthy work environment conducive to productivity and success.
Health and Safety Statement Example
FAQs
- What is the purpose of a Safety Management Plan?
- A Safety Management Plan serves as a documented framework for managing workplace safety, identifying hazards, and implementing control measures to prevent accidents and injuries.
- How often should a Safety Management Plan be reviewed?
- Safety Management Plans should be reviewed regularly, typically annually or whenever there are significant changes in operations, processes, or regulations.
- Who is responsible for implementing a Safety Management Plan?
- Implementation of a Safety Management Plan is a collective responsibility that involves management, employees, and other stakeholders collaborating to ensure its effectiveness.
- Can a Safety Management Plan be tailored to different industries?
- Yes, Safety Management Plans can and should be tailored to suit the specific needs and requirements of different industries, considering the unique hazards and risks they face.
- How can technology assist in the implementation of a Safety Management Plan?
- Technology can play a significant role in enhancing the implementation of a Safety Management Plan by facilitating incident reporting, conducting risk assessments, delivering training, and monitoring safety performance.