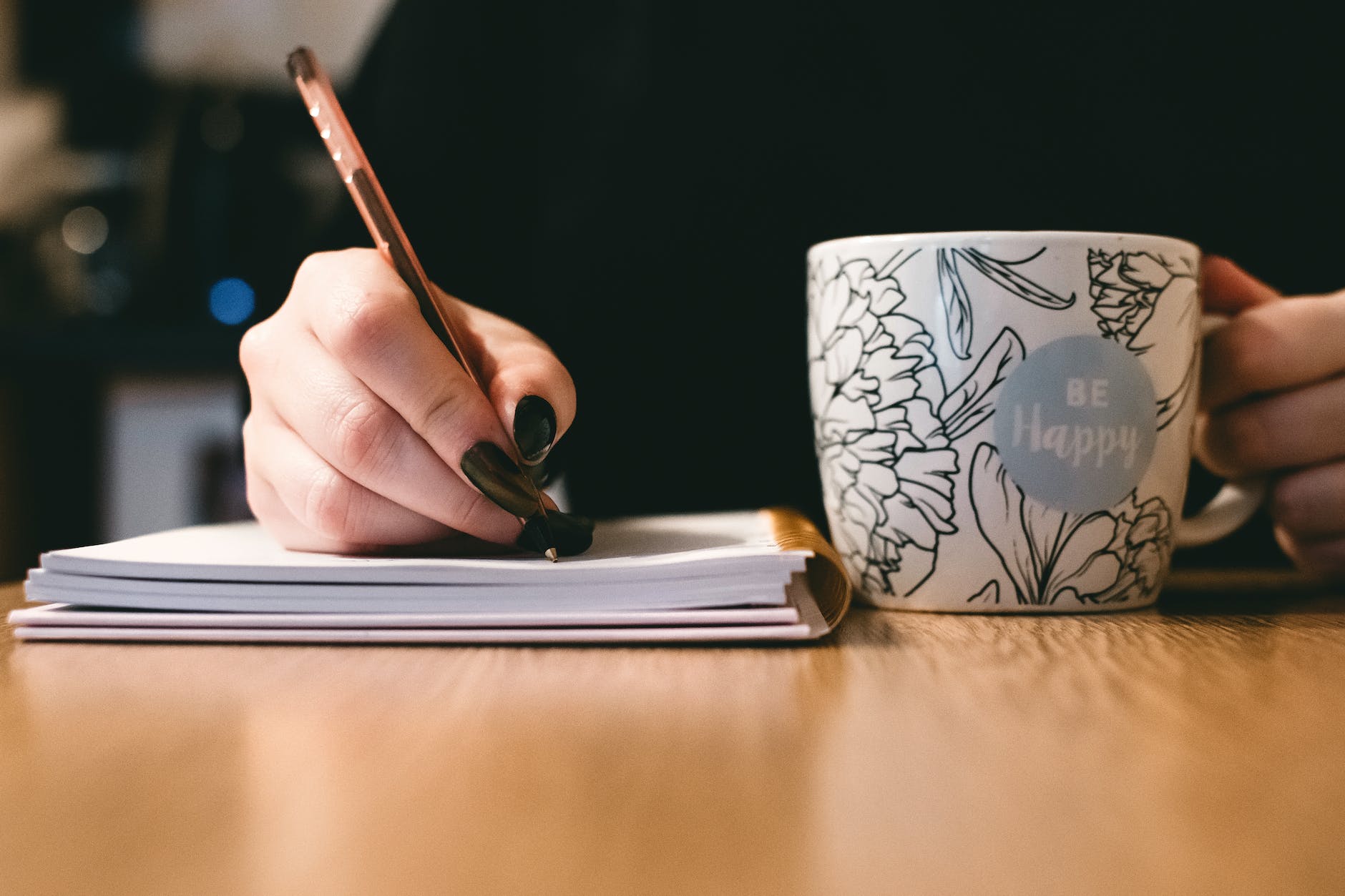
Standard Operating Procedure Examples
Introduction
In the intricate web of business operations, maintaining consistency, compliance, and efficiency is paramount. Enter Standard Operating Procedures (SOPs) – the guiding light that helps businesses navigate complexities while ensuring streamlined processes. Let’s delve into the world of SOPs and uncover their significance, varied examples, and best practices for effective implementation.
Importance of SOPs
Picture a scenario where every task within an organization is conducted in a unique manner. Chaos would reign, right? SOPs act as the unsung heroes, bringing order by providing a structured approach. They ensure uniformity in operations, reducing errors, and enhancing productivity. Businesses rely on SOPs to maintain quality, comply with regulations, and achieve operational excellence.
SOPs in Business
From large corporations to small startups, SOPs infiltrate every aspect of business. They set the protocols for employee onboarding, customer service, inventory management, and more. Whether it’s a manufacturing plant or a service-oriented business, SOPs serve as the backbone, guaranteeing consistent output.
Types of SOPs
SOPs come in various flavors, tailored to specific needs. They span across operational SOPs governing day-to-day tasks, managerial SOPs delineating responsibilities, and technical SOPs outlining specialized procedures. Each type addresses unique challenges within distinct business functions.
SOP Examples
Here are a few examples of standard operating procedures (SOPs) across different industries:
- Customer Service SOP: Outline the steps for handling customer inquiries, including greeting, issue resolution, escalation procedures, and follow-up protocols.
- Manufacturing SOP: Detail the step-by-step process for manufacturing a specific product, covering equipment setup, quality checks, and safety measures.
- Healthcare SOP: Describe the protocol for patient intake, including vital sign measurement, medical history documentation, and initial assessment procedures.
- IT SOP: Define the steps for troubleshooting common technical issues, including software installations, system updates, and cybersecurity protocols.
- HR SOP: Outline the process for employee onboarding, covering paperwork completion, orientation sessions, and HR policy review.
- Restaurant SOP: Detail the guidelines for food preparation, including hygiene practices, cooking procedures, and cleaning routines.
- Financial SOP: Specify the steps for conducting financial audits, including documentation requirements, data analysis methods, and reporting procedures.
These examples showcase how SOPs vary across industries but serve the common purpose of standardizing processes for efficiency, quality, and consistency.
Creating SOPs
Crafting effective SOPs requires meticulous planning. It involves identifying processes, documenting steps, and incorporating feedback from stakeholders. The aim? To create clear, concise, and actionable guidelines that leave no room for ambiguity.
SOP Best Practices
To make SOPs truly effective, certain practices are indispensable. Regular updates, clear communication, and easy accessibility ensure SOPs remain relevant and useful.
Implementing SOPs
Implementing SOPs isn’t just about drafting documents; it’s about embedding them into the organizational culture. Training, monitoring, and feedback mechanisms are vital for successful integration.
SOPs for Compliance
Industries operating under strict regulations heavily rely on SOPs to stay compliant. SOPs act as a shield, ensuring adherence to legal norms and industry standards.
SOPs in Quality Assurance
Quality is non-negotiable. SOPs play a pivotal role in maintaining consistent quality standards, reducing defects, and enhancing customer satisfaction.
Conclusion
Standard Operating Procedures might seem like mere documents, but their impact is far-reaching. They streamline operations, ensure compliance, and elevate the overall efficiency of businesses, regardless of size or industry.
List of Standard Operating Procedures
Safe Operating Procedure for Scaffolding
Safe Operating Procedures in the Workplace
Safe Operating Procedures for Drill Press
FAQs
- What industries benefit most from SOP implementation? Industries across the board benefit from SOPs. However, sectors like healthcare, manufacturing, hospitality, and finance particularly gain due to their complex processes that require precise guidelines for smooth operations.
- How frequently should SOPs be updated? SOPs should undergo regular reviews to ensure relevance and efficiency. Depending on the pace of change within the industry or the organization, updates might range from quarterly to annually.
- Are there any software tools for creating SOPs? Yes, there are numerous software tools available, such as Process Street, SweetProcess, and Tallyfy, designed specifically for creating, managing, and updating SOPs efficiently.
- Can SOPs help in improving employee training? Absolutely. SOPs serve as valuable training material, providing structured guidelines for employees. They offer a clear roadmap for tasks, enhancing understanding and performance.
- How do SOPs contribute to business scalability? SOPs play a critical role in scalability by ensuring consistent processes. They streamline operations, making it easier to replicate successful procedures across various departments or locations, fostering growth and expansion.