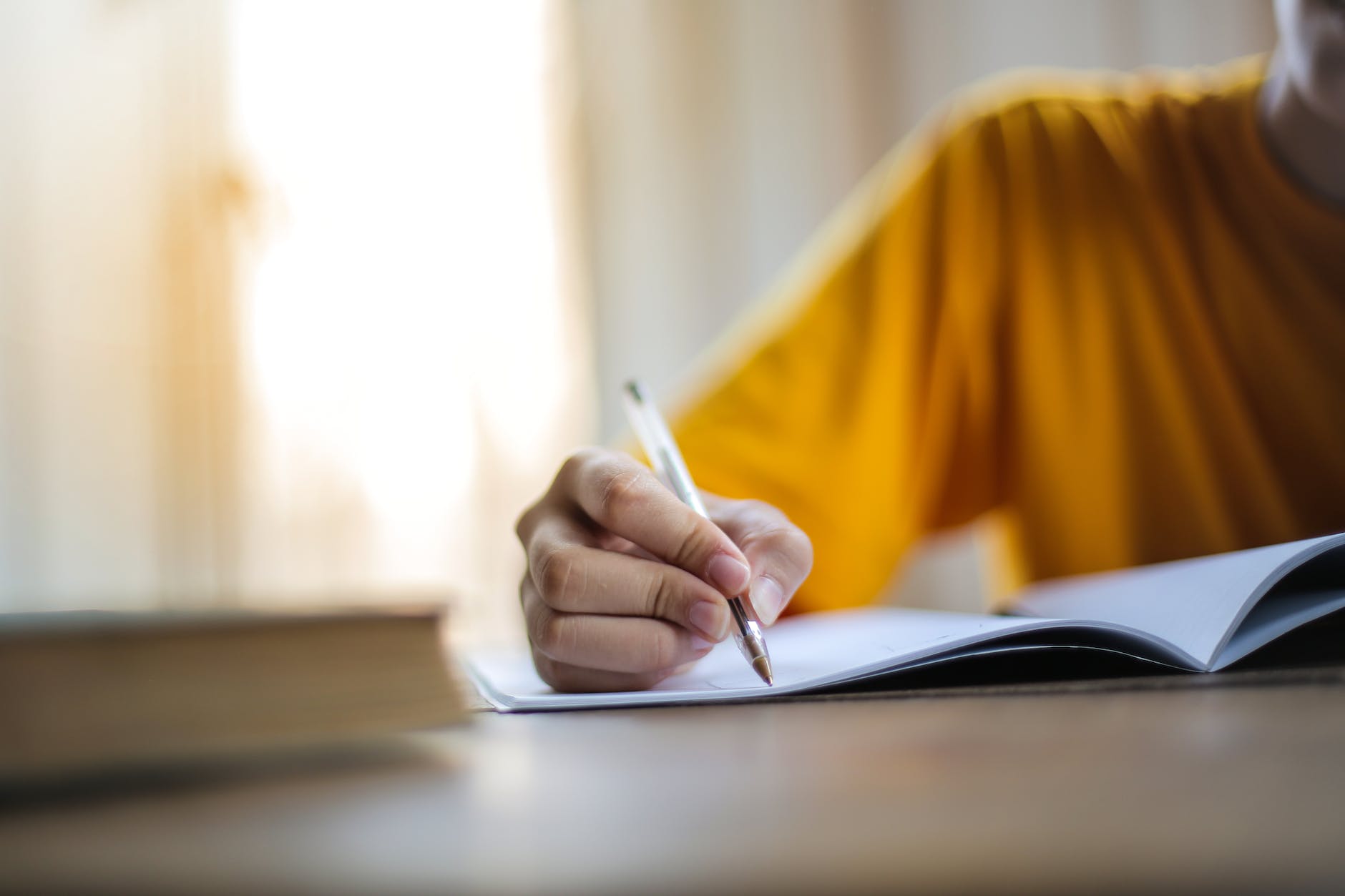
What is Root Cause Analysis (RCA)?
Root Cause Analysis (RCA) is a systematic process used to identify the underlying factors or causes of problems or incidents. It is a methodical approach aimed at understanding the primary reasons behind issues rather than just addressing their symptoms. RCA is widely employed in various fields, including engineering, healthcare, business, and safety, to prevent the recurrence of problems and improve overall processes.
Key Steps in Root Cause Analysis:
1. Define the Problem:
- Clearly articulate the problem or incident to ensure a focused analysis. This step sets the foundation for the entire RCA process.
2. Gather Data:
- Collect relevant information about the problem, including when, where, and how it occurred. This involves examining documents, interviewing involved parties, and reviewing any available data.
3. Identify Causal Factors:
- Determine all the factors and conditions contributing to the problem. This involves looking beyond the immediate causes and exploring deeper into systemic issues.
4. Distinguish Root Causes:
- Differentiate between immediate causes and root causes. Root causes are the fundamental issues that, if addressed, would prevent the problem from recurring.
5. Develop Solutions:
- Once root causes are identified, propose and prioritize corrective actions. These solutions should directly address the underlying issues rather than just mitigating symptoms.
6. Implement and Monitor:
- Put the chosen solutions into action and monitor their effectiveness. Continuous monitoring ensures that the implemented changes have the desired impact.
7. Prevent Recurrence:
- Establish preventive measures to avoid the recurrence of similar problems in the future. This may involve adjusting policies, procedures, or systems to address root causes.
Sample Example of Root Cause Analysis (RCA): Workplace Equipment Failure
1. Define the Problem:
- The problem is recurring breakdowns of a critical piece of manufacturing equipment, leading to production delays and increased downtime.
2. Gather Data:
- Review maintenance logs, interview operators and maintenance staff, and analyze recent incident reports. Collect data on the frequency, timing, and nature of equipment failures.
3. Identify Causal Factors:
- Identify factors contributing to the equipment failures, including inadequate maintenance schedules, outdated components, and variations in operating conditions.
4. Distinguish Root Causes:
- Determine that the root causes involve both procedural and technical issues. Inadequate maintenance schedules highlight a procedural flaw, while outdated components point to a technical deficiency.
5. Develop Solutions:
- Propose solutions, including revising and optimizing maintenance schedules, upgrading outdated components, and implementing predictive maintenance technologies to detect issues before they lead to failure.
6. Implement and Monitor:
- Implement the proposed solutions, adjusting maintenance schedules and replacing outdated components. Monitor the equipment’s performance closely to assess the effectiveness of the changes.
7. Prevent Recurrence:
- Introduce preventive measures such as regular training for maintenance staff, continuous monitoring of equipment health, and periodic reviews of maintenance procedures to prevent the recurrence of breakdowns.
Results:
- Following the implementation of the new maintenance schedules and component upgrades, equipment failures decreased significantly. Downtime was reduced, leading to increased production efficiency and cost savings. The preventive measures put in place contributed to a sustained improvement in equipment reliability.
This example illustrates how Root Cause Analysis can be applied to address recurring issues in a systematic and effective manner, leading to lasting improvements in operational performance.
Benefits of Root Cause Analysis:
1. Problem Prevention:
- By addressing the root causes, RCA helps prevent the recurrence of problems, leading to more sustainable solutions.
2. Continuous Improvement:
- The insights gained from RCA contribute to ongoing improvement efforts within an organization or process.
3. Enhanced Decision-Making:
- RCA provides a structured approach to decision-making, helping organizations make informed choices based on a thorough understanding of the problem.
4. Efficiency and Effectiveness:
- Identifying and addressing root causes lead to more efficient and effective solutions, saving resources and time in the long run.
5. Improved Quality:
- RCA contributes to overall quality improvement by eliminating or mitigating the factors that lead to defects or issues.
Root Cause Analysis is a valuable tool for organizations committed to continuous improvement and proactive problem-solving. It emphasizes a holistic understanding of issues, encouraging a culture of learning and preventing the recurrence of problems in the future.