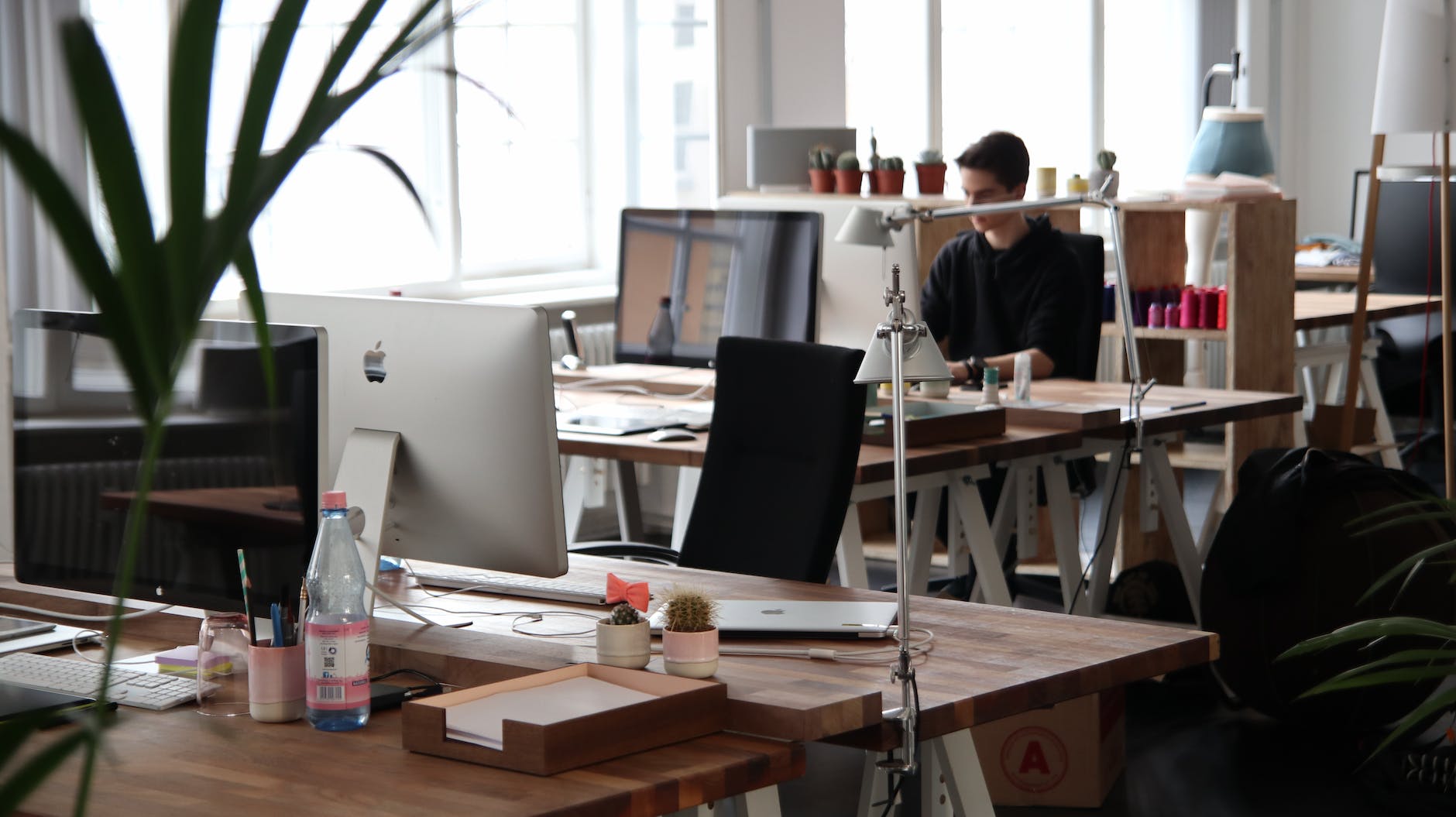
10 Workplace Safety Shortcuts
Shortcuts Safety at Workplace
Safety shortcuts are a common practice within the organization which is completely wrong. Wherever work is being done inside the industry, it is not easy to keep that work place safe.
There are rules and regulations to follow for safety, which is difficult to find out at which places the prescribed safety rules are being followed and at which places they are not.
There are many safety shortcuts at the working place, following which can improve safety. But there are some such safety shortcuts, following which can cause risk to the workers.
That’s why special attention has to be paid to whether the rules and regulations related to security made by the organization are being followed completely or not.
It is very important to make sure that there are no common security-related mistakes being made within the organization.
Safety Shortcuts Example
Let us know about those 10 safety shortcuts which need to be eliminated during work at the workplace, otherwise these safety shortcuts can cause a big problem.
1. Lifting Quickly
When manual handling of heavy materials is done, then back brace is used while lifting it. The biggest advantage of using it is that whatever ergonomics problem related to the waist, the risk of getting it reduces.
If any heavy goods are to be lifted then the help of someone else is taken to lift the load, it gives more security. Because the load that happens gets distributed.
But when there is any light lifting i.e. a person lifts the same according to his capacity, he does not follow the rules of safety prescribed for lifting, he only lifts the material and starts walking. But this kind of negligence exposes the safety risk.
Sometimes when a person goes to lift something, it looks light but it can be deceptively heavy. But if the person shows carelessness in lifting or handling, then it can cause problems related to ergonomics.
Stop when you see workers lifting any kind of material improperly, otherwise, even while lifting heavy objects, they can ignore the rules of lifting, which is enough to injure them.
While lifting a material for manual handling, it is the moral responsibility of the workers to follow the safe lifting techniques that have been prescribed.
2. Use of Improper Tools
Tools and tackles are given according to the kind of work done by the management at the workplace. Giving tools, tackles according to the work means that any kind of work should be done in a safe procedure.
However, in some cases, people start taking safety shortcuts using the tools available with them, instead of taking the time to do the right thing.
Let’s understand it with an example –
It is generally seen that trying to hammer a nail into wood or a wall with the back end of a screwdriver is a safety shortcut. Because hammer has to be used to hit the nail.
Hitting the nail from behind the screw driver can either break the back part of the screw driver or injure the hand of the person driving the nail.
You will get to see many such tasks at the workplace, which are taken as safety shortcuts ignoring the safety. Stopping which is the work of the site supervisor or safety professional, otherwise it can put the workers at risk.
3. Skipping Break
Many times, so much burden of work is put on the workers that people do not take breaks during work, even they are not allowed to have lunch under the pressure of work. And this type of situation creates a problem related to security.
Because workers try to finish the work quickly to take a break and start taking safety shortcuts, which becomes the cause of the accident.
Taking breaks during work is not just a way to relax, but it is an important part of workplace safety.
After taking a break during work, a person becomes physically and mentally refreshed and is able to work safely again.
It is very important to have lunch during the afternoon, lunch provides energy to the person and the person starts working safely.
4. Ignore Near Miss
When there is a major accident at the workplace in which there is loss of life and property, then every person working in that organization knows about that accident.
Because after that accident, the accident is usually investigated and whatever paperwork is done, it is completed. This type of rule is there in every organization and it is a good thing that the cause of the actual accident can be known.
But when there is a ‘near miss’ at the same work place in which there is no damage, people become careless.
But this is wrong, because until we investigate an accident, we will not be able to know its root causes and then we will not be able to know the reason to remove it in future. Which can further cause an accident and cause damage to life and property.
5. Lack of Emergency Equipment
Various types of facilities are provided to promote safety in the company, out of which facility like fire fighting also comes in emergency equipment.
But according to the workplace, if it is less, then in reality it will not give as much protection as the equipment available according to the requirement will provide protection.
Keeping in view the security point of view, those areas have to be identified where emergency equipment is needed, where the risks are high.
Emergency equipment has to be made available according to the risks at such a place. If minimum emergency equipment is available at the workplace, then these are safety shortcuts, which can lead to major problems.
6. Avoid Housekeeping
Cleanliness is also counted in a facility in different types of facilities within the industry which frees the person from various types of hazards.
But many things are not done as much as the housekeeping is required, during housekeeping the person cleans the garbage spread around him and the dust lying on the floor etc. but these are safety shortcuts.
Safety signs are installed at various places inside the industry, which are very important for the safety of the visitors. Dust, grease, dirt or other things get accumulated on such a safety sign and the purpose for which it is installed cannot be fulfilled, because it becomes difficult to read or understand due to accumulation of dust on it.
Such safety signs are not cleaned for years or even months, which increases the risks for the commuters or for those working at that place.
7. No Clear Exit Path
No one knows when an emergency situation may arise in any organization, so it is always necessary to be prepared to deal with the emergency situation.
All the exit routes inside the organization have such signs which glow in the dark and by following them a person can get out of that place in case of emergency.
But if the disruptive material is kept at that exit point, then it will create disturbance in the exit which can cause an accident.
That’s why all the emergency exit points should be kept clean at all times so that they can be used smoothly in case of emergency.
8. Only Initial Training
When a company hires someone, it gives them training before reducing them in that industry, which is known as safety induction.
However, in many cases, they only provide work-related training and do not inform about safety shortcuts at the workplace, which are one of the dangerous types. They put not only themselves in danger but also those working around them.
When employees are hired, they need high quality training and not just once but it has to be provided from time to time and needs to be updated regularly.
When such facilities are made available, safety is followed to a great extent and workers ignore safety shortcuts, which is very important for safety.
9. Lack of Maintenance of Tools, Tackles, Equipment and Machinery
Management’s responsibility is not limited to this that it should provide tools, tackles, equipment and machinery to the workers according to the work.
It is also the responsibility of the management to maintain all the equipment and machines used in it. Get it maintained whenever necessary.
Management should never think that everything is fine if the machine is running, it will be seen after breaking down. This assumption puts workers at risk.
The employer feels that the expenses on maintenance are useless but in reality it is not so. If any workers can get injured due to lack of maintenance of the machine, then the employer may have to spend more than that.
Management should meet the requirements for the maintenance of the machine so that nothing is left out. Running them smoothly will not only keep the facilities safe, but will also prevent disruption in work after accidents and save time.
10. Post Wrong Safety Labels
Safety Labels are very important from the point of view of safety. It plays a very important role in providing security to the visitor.
Using Safety Labels is the best way to communicate safety by features. That’s why safety labels are recommended at the working site.
Using Safety Labels does not just end the solution of the problem, but it has to provide awareness among the people.
Before applying the safety label, it has to be ensured that the place where the label is used or is going to be used, is according to the danger present there or not.
Using the wrong safety labels can put visitors or workers at the facility at risk. Not using safety labels according to danger is a safety shortcut, which makes the workplace unsafe.
Conclusion
Safety Shortcuts is a workplace hazard factor that can put workers at risk.
Those who are supposed to conduct any work at the workplace or who are looking after the safety, they need to take steps to prevent shortcut safety, otherwise the worker himself will not be safe but also those working around him. Will be unsafe
When the safety meeting is going on or the toolbox talks are going on, in such a situation, the possible dangers that occur during the safety shortcuts have to be made aware of them, awareness has to be brought among the workers.
Not only this, the role and responsibilities of the management to prevent safety shortcuts have to be fulfilled honestly, then we can go somewhere and develop a safety culture at the workplace.
NEBOSH Course Fees: Everything You Need to Know
NEBOSH International Diploma in Occupational Health and Safety (NEBOSH IDIP)
NEBOSH Level 6 International Diploma for Occupational Health and Safety Management Professionals