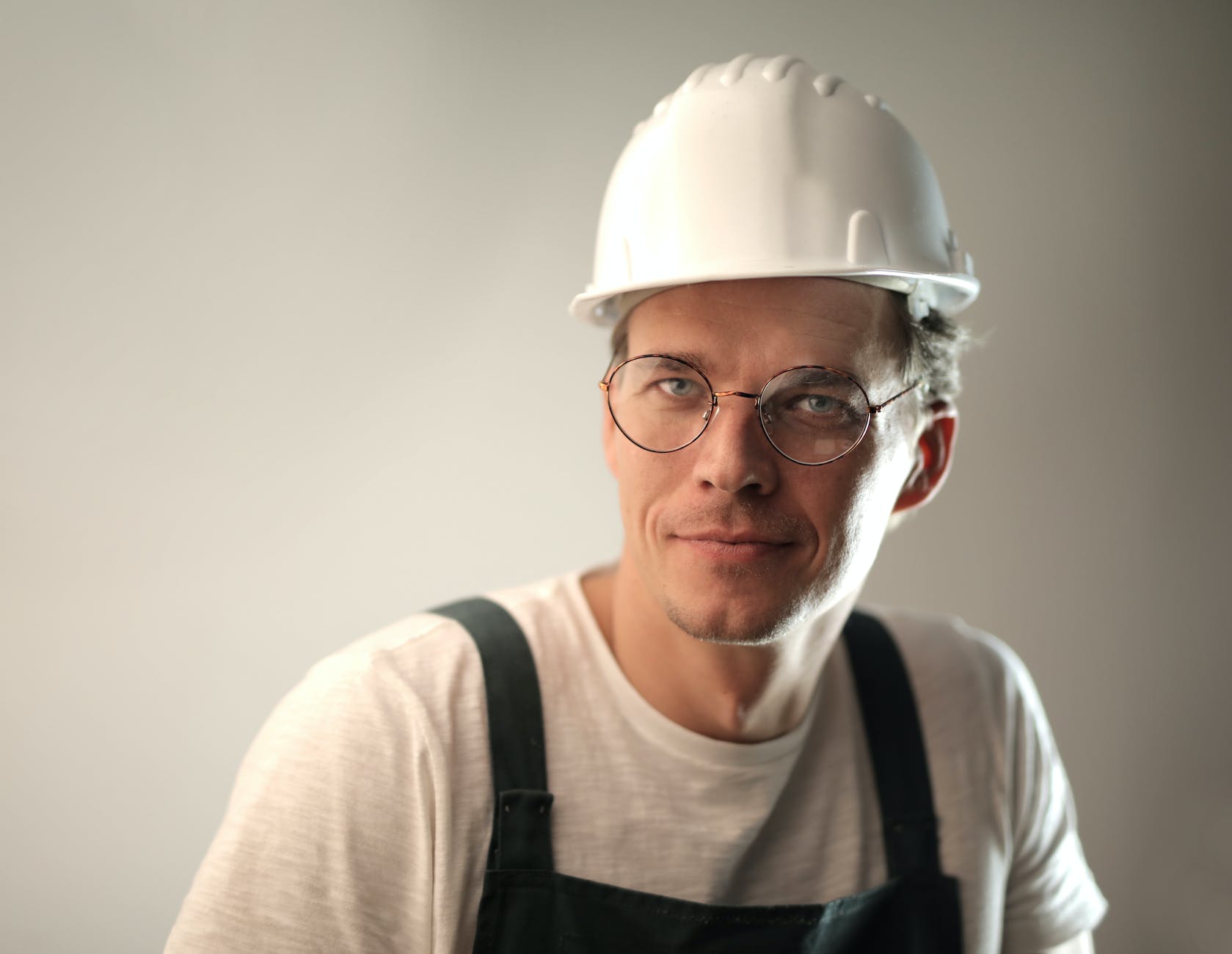
45 Duties Of A Safety Engineer You Must Know
Safety engineers play a crucial role in maintaining a secure working environment, ensuring the well-being of employees, and preventing accidents. Let’s delve into the extensive list of duties that define this profession.
I. Introduction
In a world where workplace safety is paramount, the role of a safety engineer takes center stage. These professionals are tasked with safeguarding employees, preventing accidents, and ensuring compliance with industry regulations. Let’s explore the intricate web of duties that a safety engineer must navigate to create a secure working environment.
II. Educational Requirements
Becoming a safety engineer requires a strong educational foundation. Typically, individuals pursuing this career path need at least a bachelor’s degree in a relevant field such as engineering or occupational health and safety. Continuous education is crucial, given the evolving nature of safety standards and regulations.
III. Core Duties
At its core, the role of a safety engineer encompasses a variety of responsibilities aimed at creating and maintaining a safe workplace. From conducting risk assessments to ensuring compliance with safety regulations, these duties form the backbone of the profession.
IV. Risk Assessment and Management
One of the primary responsibilities of a safety engineer is to conduct thorough risk assessments. This involves identifying potential hazards in the workplace and developing strategies to mitigate these risks effectively. A proactive approach to risk management is essential for preventing accidents and injuries.
V. Workplace Inspections
Regular inspections are a key aspect of a safety engineer’s duties. By systematically inspecting the workplace, these professionals can identify and address potential hazards before they escalate. Implementing corrective actions based on inspection findings is crucial for maintaining a safe environment.
VI. Emergency Response Planning
Preparing for unforeseen incidents is a critical duty of a safety engineer. This involves developing and implementing emergency response plans, ensuring that all employees are well-trained and equipped to handle emergencies effectively. The goal is to minimize the impact of incidents and protect lives.
VII. Safety Training Programs
A safety engineer plays a pivotal role in designing and conducting safety training programs for employees. This includes educating staff on safety protocols, emergency procedures, and the proper use of safety equipment. Ongoing training is essential to keep employees informed and vigilant against potential risks.
VIII. Incident Investigation
When incidents occur, a safety engineer is responsible for conducting thorough investigations. This involves analyzing the root causes of accidents and near-misses, learning from these incidents, and implementing preventive measures to avoid similar occurrences in the future.
IX. Safety Standards Compliance
Staying abreast of industry safety standards is a continuous duty for safety engineers. These professionals must ensure that their organizations not only meet but exceed these standards. Implementing measures to enhance safety beyond regulatory requirements demonstrates a commitment to the well-being of employees.
X. Communication Skills
Effective communication is a cornerstone of the safety engineer’s role. From conveying safety protocols to upper management to ensuring that frontline employees understand and follow safety guidelines, clear and concise communication is essential at all levels of the organization.
XI. Ergonomics and Workplace Design
Addressing ergonomic concerns is a duty that directly impacts employee well-being. Safety engineers contribute to the design of a safe and ergonomic workplace layout, minimizing the risk of musculoskeletal disorders and promoting overall health among employees.
XII. Health and Safety Policies
Developing and updating health and safety policies is an ongoing responsibility. Safety engineers work to create comprehensive policies that address the specific risks associated with their industry. Ensuring that all employees are familiar with and adhere to these policies is crucial for maintaining a safe work environment.
XIII. Data Analysis for Safety Improvement
In the digital age, safety engineers leverage data analysis to identify trends and areas for improvement. By collecting and analyzing data related to safety incidents, these professionals can implement targeted measures to enhance workplace safety continually.
XIV. Continuous Improvement
Embracing a culture of continuous improvement is not just a duty but a mindset for safety engineers. Encouraging feedback from employees, learning from incidents, and innovating safety measures are essential for staying ahead of evolving risks and maintaining a proactive safety approach.
XV. Industry-Specific Regulations
Safety engineers must navigate industry-specific regulations to ensure compliance. This involves staying informed about any changes in regulations, collaborating with regulatory bodies, and adapting safety measures accordingly.
A Safety Engineer plays a crucial role in ensuring the safety and well-being of individuals in various industries. Here are 45 duties of a Safety Engineer:
- Risk Assessments: Conducting risk assessments to identify potential hazards in the workplace.
- Safety Inspections: Regularly inspecting facilities, equipment, and processes to ensure compliance with safety standards.
- Emergency Response Planning: Developing and implementing emergency response plans to handle accidents or disasters.
- Safety Training: Providing safety training to employees on a regular basis.
- Regulatory Compliance: Ensuring compliance with local, state, and federal safety regulations.
- Incident Investigation: Investigating accidents and incidents to determine root causes and prevent recurrence.
- Hazardous Material Management: Managing and controlling the use of hazardous materials in the workplace.
- Personal Protective Equipment (PPE): Recommending and ensuring the use of appropriate PPE.
- Job Hazard Analysis: Conducting job hazard analyses to identify potential risks in specific tasks.
- Safety Policies: Developing and implementing safety policies and procedures.
- Safety Audits: Conducting safety audits to evaluate the effectiveness of safety programs.
- Fall Protection Planning: Implementing fall protection measures in elevated work areas.
- Machine Guarding: Ensuring proper machine guarding to prevent accidents.
- Confined Space Management: Managing confined space entry procedures and precautions.
- Electrical Safety: Implementing measures to ensure electrical safety in the workplace.
- Noise Control: Implementing measures to control and reduce workplace noise levels.
- Fire Safety: Developing and implementing fire safety protocols.
- Ventilation Systems: Ensuring proper ventilation in work areas to control exposure to harmful substances.
- Ergonomics: Assessing and addressing ergonomic issues to prevent musculoskeletal disorders.
- First Aid Programs: Establishing and maintaining first aid programs.
- Chemical Safety: Managing and controlling the use of chemicals in the workplace.
- Safety Data Sheets (SDS): Ensuring proper storage and availability of SDS for hazardous substances.
- Safety Communication: Promoting effective safety communication across all levels of the organization.
- Safety Meetings: Facilitating regular safety meetings with employees.
- Contractor Safety: Ensuring contractors adhere to safety standards while on-site.
- Safety Recordkeeping: Maintaining accurate records of safety-related incidents, training, and activities.
- Safety Culture Promotion: Promoting a culture of safety within the organization.
- Behavior-Based Safety Programs: Implementing programs to encourage safe behaviors among employees.
- Safety Software Implementation: Utilizing safety management software to track and manage safety initiatives.
- Environmental Compliance: Ensuring compliance with environmental regulations that impact safety.
- Safety signage: Placing appropriate safety signs and labels in visible locations.
- Gas Detection Systems: Implementing gas detection systems where relevant.
- Lockout/Tagout Programs: Implementing and managing lockout/tagout procedures for equipment maintenance.
- Training Material Development: Developing training materials for safety programs.
- Safety Committees: Participating in or facilitating safety committees.
- Safety Incentive Programs: Implementing incentive programs to encourage safe practices.
- Emergency Evacuation Drills: Conducting regular emergency evacuation drills.
- Safety Documentation Review: Reviewing and updating safety documentation as needed.
- Safety Performance Metrics: Tracking and analyzing safety performance metrics.
- Safety Equipment Testing: Ensuring regular testing and maintenance of safety equipment.
- Process Safety Management: Implementing process safety management programs.
- Safety Reporting: Creating and submitting safety reports as required.
- Safety Budgeting: Managing budgets related to safety initiatives.
- Job Safety Analysis (JSA): Conducting job safety analyses for various tasks.
- Continuous Improvement: Continuously seeking opportunities to improve safety processes and procedures.
These duties collectively contribute to creating and maintaining a safe working environment for employees.
Conclusion
In conclusion, the role of a safety engineer is multifaceted, requiring a blend of technical knowledge, communication skills, and a proactive mindset. By understanding and fulfilling these 45 duties, safety engineers contribute significantly to the well-being of employees and the overall success of their organizations.
How to Become a Certified Safety Officer in 2024?
How to Become a Certified Safety Engineer?
HSE Manager: What is the Qualification Required to Become an HSE Manager?
HSE Engineer: What is the Qualification Required to Become a HSE Engineer?
HSE Supervisor: What is the Qualification Required to Become an HSE Supervisor?
FAQs (Frequently Asked Questions)
- What qualifications are required to become a safety engineer?
- To become a safety engineer, individuals typically need at least a bachelor’s degree in a relevant field such as engineering or occupational health and safety.
- How often should workplace inspections be conducted?
- Workplace inspections should be conducted regularly to identify and address potential hazards. The frequency may vary based on the nature of the work environment.
- What is the importance of data analysis in improving workplace safety?
- Data analysis helps safety engineers identify trends and areas for improvement, allowing for targeted measures to enhance overall workplace safety.
- How can safety engineers contribute to a culture of continuous improvement?
- Safety engineers can contribute to continuous improvement by encouraging feedback, learning from incidents, and proactively innovating safety measures.
- Why is effective communication crucial for safety engineers?
- Effective communication is essential for conveying safety protocols, ensuring understanding at all organizational levels, and fostering a culture of safety awareness.