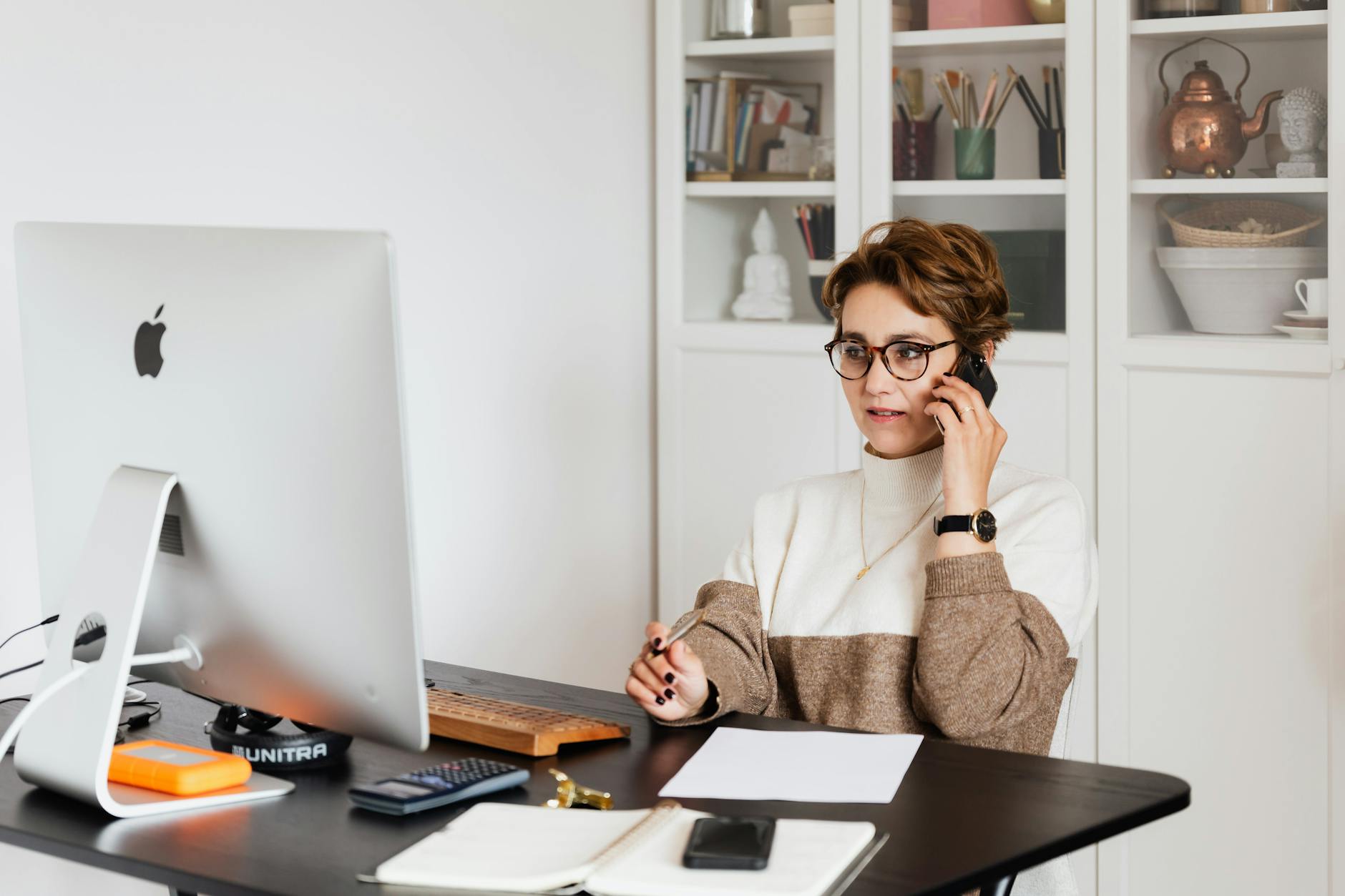
50 Duties Of A Safety Manager You Must Know
Introduction
In the dynamic and fast-paced world of industries and workplaces, the role of a Safety Manager is paramount. These professionals play a crucial role in ensuring the well-being of employees and maintaining a secure working environment. Let’s delve into the 50 essential duties that every Safety Manager should be proficient in.
Qualifications and Skills
To embark on the journey of ensuring workplace safety, a Safety Manager must possess a strong educational background, ideally in occupational health and safety or a related field. Certifications such as Certified Safety Professional (CSP) add value. Exceptional communication skills are imperative for effective collaboration with diverse teams.
Regulatory Compliance
Being well-versed in safety regulations and standards is a foundational duty of a Safety Manager. Implementing and monitoring compliance ensures a proactive approach to avoiding potential hazards.
Risk Assessment and Management
Identifying and assessing potential risks is a key responsibility. Safety Managers must develop strategies to mitigate risks, creating a safer environment for all.
Emergency Response Planning
Crafting detailed emergency procedures and conducting regular drills are duties that ensure a swift and organized response in critical situations.
Safety Training Programs
Safety Managers are tasked with initiating comprehensive training programs for employees, fostering a culture of awareness and preparedness.
Incident Investigation
When incidents occur, Safety Managers lead root cause analyses to determine the reasons behind accidents, implementing preventive measures to avoid future occurrences.
Safety Audits and Inspections
Regular inspections and compliance checks are crucial to maintaining a safe workplace. Safety Managers are at the forefront of these evaluations.
Personal Protective Equipment (PPE)
Ensuring the proper use of PPE and evaluating its effectiveness are duties that directly impact the safety of employees.
Documentation and Record Keeping
Maintaining accurate safety records and reporting incidents promptly are duties that contribute to a proactive approach to safety management.
Communication with Stakeholders
Safety Managers must actively engage with both employees and management, fostering a collaborative approach to safety within the organization.
Safety Culture Promotion
Fostering a safety-oriented environment involves encouraging reporting, ensuring transparency, and making safety a shared responsibility among all team members.
Ergonomics
Assessing workplace ergonomics and implementing improvements contribute to the overall well-being of employees.
Environmental Health and Safety (EHS)
Managing environmental impacts and integrating health and safety practices into everyday operations are duties that align with broader organizational goals.
Here are 50 duties of a safety manager:
- Develop and implement safety policies and procedures.
- Conduct regular safety inspections.
- Identify and assess potential hazards in the workplace.
- Ensure compliance with local, state, and federal safety regulations.
- Conduct safety training for employees.
- Investigate accidents and incidents to determine their causes and prevent recurrence.
- Maintain safety records and documentation.
- Develop emergency response plans.
- Coordinate with management to integrate safety practices into daily operations.
- Inspect and maintain safety equipment.
- Conduct safety audits to evaluate the effectiveness of safety programs.
- Provide guidance on the selection and use of personal protective equipment (PPE).
- Collaborate with department heads to address specific safety concerns.
- Keep abreast of changes in safety regulations and industry best practices.
- Develop and implement safety communication strategies.
- Monitor and evaluate the effectiveness of safety programs.
- Establish and lead a safety committee.
- Conduct risk assessments for new processes or equipment.
- Ensure the proper handling and disposal of hazardous materials.
- Promote a safety culture throughout the organization.
- Develop and deliver safety presentations to employees and management.
- Respond to and investigate employee safety concerns.
- Implement corrective actions based on safety inspection findings.
- Coordinate with external safety organizations and agencies.
- Conduct safety orientations for new employees.
- Review and update safety manuals and documentation.
- Collaborate with human resources to address safety-related issues.
- Analyze accident and incident data to identify trends.
- Recommend improvements to work processes to enhance safety.
- Conduct job hazard analyses.
- Facilitate safety drills and exercises.
- Develop and implement a behavior-based safety program.
- Investigate and report on near misses.
- Ensure proper signage for safety hazards.
- Provide guidance on ergonomics and workstation setup.
- Monitor and enforce compliance with safety rules.
- Develop and implement a lockout/tagout program.
- Evaluate the effectiveness of safety training programs.
- Coordinate with maintenance personnel on safety-related equipment repairs.
- Conduct safety workshops and seminars.
- Review contractor safety programs and practices.
- Collaborate with supervisors to address safety performance.
- Implement safety incentives and recognition programs.
- Ensure that safety information is effectively communicated to all employees.
- Participate in safety conferences and workshops.
- Conduct safety meetings with employees at all levels.
- Monitor and manage workers’ compensation claims.
- Conduct safety drills for emergency evacuation.
- Ensure the proper labeling of hazardous materials.
- Stay current on industry trends and advancements in safety practices.
These duties collectively contribute to creating a safe and healthy work environment for employees.
Conclusion
In conclusion, the role of a Safety Manager is multifaceted and crucial for the well-being of both employees and the organization. By embracing and excelling in these 50 duties, Safety Managers contribute significantly to the overall success and safety of the workplace.
How to Become a Certified Safety Officer in 2024?
How to Become a Certified Safety Engineer?
HSE Manager: What is the Qualification Required to Become an HSE Manager?
HSE Engineer: What is the Qualification Required to Become a HSE Engineer?
HSE Supervisor: What is the Qualification Required to Become an HSE Supervisor?
FAQs
- What are the basic qualifications for a Safety Manager?
- Educational background in occupational health and safety or a related field, and relevant certifications such as CSP.
- How often should safety audits be conducted?
- Regular safety audits should be conducted at least annually, with more frequent checks in high-risk industries.
- Why is communication with stakeholders important for a Safety Manager?
- Effective communication ensures a collaborative approach to safety, involving both employees and management.
- How can Safety Managers foster a safety culture?
- Safety Managers can foster a safety culture by encouraging reporting, ensuring transparency, and making safety a shared responsibility.
- What role does technology play in safety management?
- Technology, such as safety management software, aids Safety Managers in staying ahead of potential risks and enhancing overall safety measures.