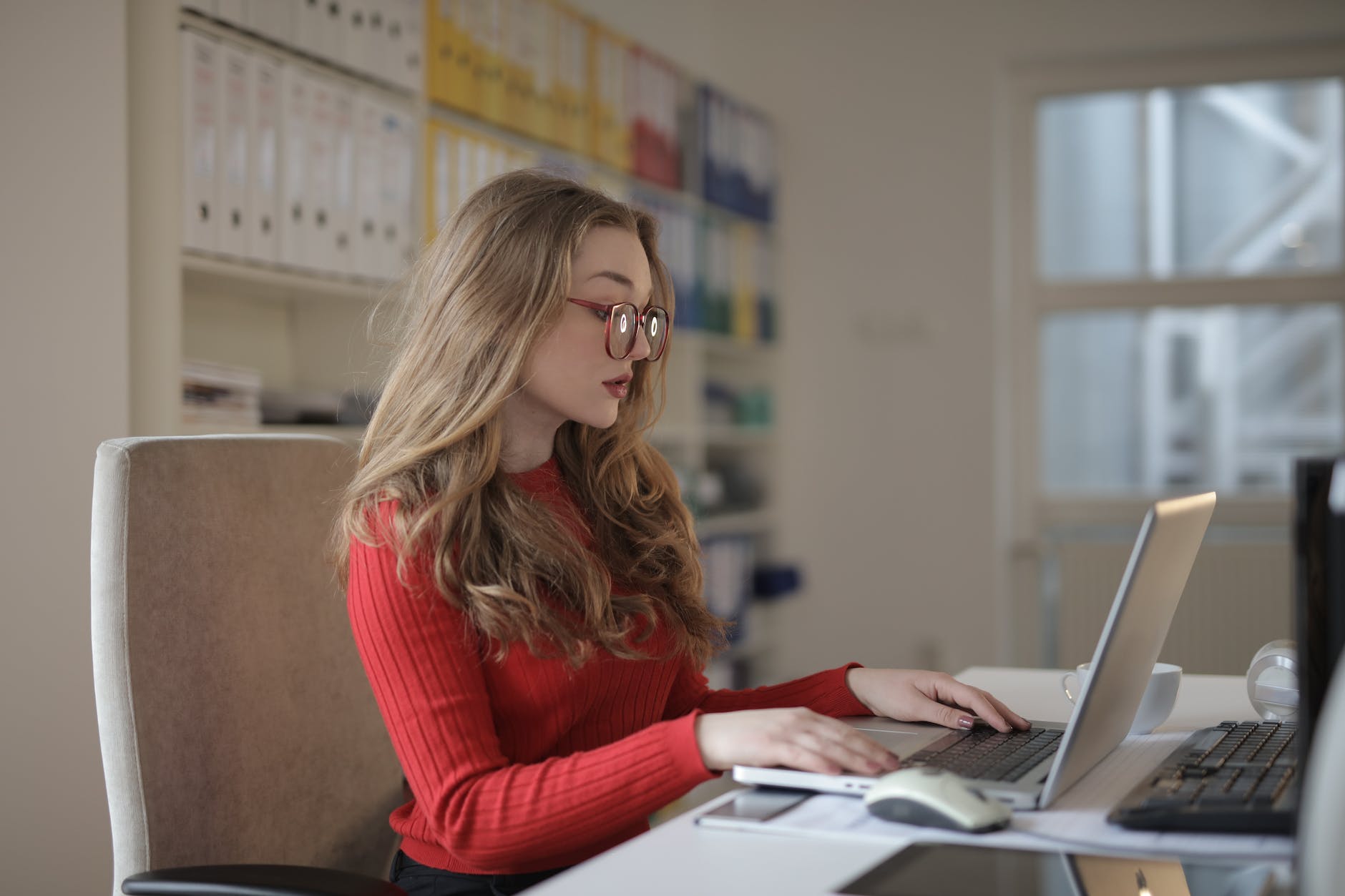
50 Duties of Safety Engineer
50 Duties of Safety Engineer : Safety engineers are unsung heroes in the realm of workplace safety, ensuring that individuals operate in secure environments across various industries. Their role encompasses a wide array of responsibilities, each crucial in maintaining a safe and conducive work atmosphere. Let’s delve into the 50 pivotal duties that safety engineers undertake in their daily practice.
Importance of Safety Engineers
Safety engineers form the backbone of a secure workplace. They meticulously analyze, strategize, and implement measures to prevent potential hazards and safeguard employees’ well-being. Their presence significantly reduces workplace accidents and ensures regulatory compliance, fostering a more productive and harmonious work environment.
Qualifications and Skills
Becoming a safety engineer demands a solid educational foundation in engineering or related fields. Additionally, certifications and specialized training in occupational health and safety are imperative. Skills such as risk assessment, problem-solving, communication, and a keen eye for detail are instrumental in excelling in this role.
Duties in Planning and Implementation
From the initial planning stages to the execution of safety protocols, safety engineers play a pivotal role. They conduct thorough risk assessments, design safety plans, and oversee their implementation, ensuring that every measure aligns with industry standards and regulatory requirements.
Responsibilities in Risk Assessment
Identifying potential hazards is a primary duty of safety engineers. They meticulously analyze work environments, machinery, and processes to pinpoint risks. Once identified, they develop strategies to mitigate these risks and prevent potential accidents or injuries.
Ensuring Compliance and Training
Safety engineers are tasked with enforcing regulatory compliance within organizations. They conduct regular audits, create training programs, and ensure that employees understand and follow safety protocols to minimize risks effectively.
Importance of Communication
Effective communication is fundamental in safety engineering. Safety engineers need to articulate safety procedures clearly, ensure comprehension among employees, and facilitate an open dialogue to address safety concerns promptly.
Emphasizing Workplace Safety Culture
Cultivating a culture of safety is pivotal in preventing accidents. Safety engineers promote awareness and instill a sense of responsibility among employees, encouraging proactive measures to maintain a safe work environment.
Monitoring and Evaluating Safety Measures
Continuous monitoring and evaluation are essential components of a safety engineer’s role. Regular inspections and assessments ensure that safety measures remain effective and identify areas that require improvement.
Handling Emergencies and Incidents
During emergencies or incidents, safety engineers act swiftly. They implement emergency response plans, coordinate evacuations if necessary, and conduct thorough investigations to prevent future occurrences.
Collaborating with Various Departments
Safety engineers collaborate extensively with different departments within an organization. Whether it’s providing guidance on safety protocols or coordinating drills, their cross-departmental collaboration ensures a holistic approach to safety measures.
Documenting and Reporting
Accurate documentation and reporting are vital aspects of a safety engineer’s duties. They maintain records of incidents, conduct analysis, and generate reports to track trends and implement necessary changes for enhanced safety.
Continuous Improvement
Safety engineering is an iterative process. Safety engineers continuously seek ways to enhance safety measures, leveraging data and feedback to implement improvements and adapt to evolving workplace environments.
Here are 50 duties that a safety engineer might typically perform:
- Develop safety procedures and protocols for various work environments.
- Conduct risk assessments to identify potential hazards.
- Create and implement safety training programs for employees.
- Inspect and evaluate workplace environments, equipment, and processes for compliance with safety standards.
- Investigate accidents or incidents to determine causes and prevent recurrence.
- Advise management on safety regulations and best practices.
- Collaborate with engineers and architects to ensure safety in design and construction projects.
- Review and update safety policies and manuals regularly.
- Conduct safety audits and inspections.
- Develop emergency response plans and procedures.
- Analyze data to identify trends and areas for improvement in safety measures.
- Conduct safety meetings and training sessions.
- Ensure compliance with local, state, and federal safety regulations.
- Recommend and implement corrective actions to address safety issues.
- Provide guidance on the selection and use of personal protective equipment (PPE).
- Perform hazard analyses and risk assessments for new projects or processes.
- Monitor and evaluate the effectiveness of safety programs.
- Collaborate with human resources to address safety-related employee concerns.
- Investigate the effectiveness of safety equipment and make recommendations for upgrades or replacements.
- Develop and maintain safety documentation and records.
- Conduct safety workshops and seminars.
- Develop safety protocols for hazardous materials handling and storage.
- Collaborate with suppliers and vendors to ensure safety standards are met.
- Assess and mitigate ergonomic risks in the workplace.
- Develop safety strategies for specific industries or sectors.
- Conduct safety inspections of machinery and equipment.
- Train employees on proper equipment operation and safety procedures.
- Coordinate with regulatory agencies during inspections or audits.
- Identify and address potential environmental health hazards.
- Participate in safety committees or task forces.
- Analyze incident reports to identify patterns and root causes.
- Conduct safety drills and exercises.
- Implement safety incentives and recognition programs.
- Develop safety communication strategies and materials.
- Ensure safety considerations in facility layout and design.
- Evaluate contractor safety performance on job sites.
- Provide safety guidance during the selection of new equipment or technologies.
- Collaborate with medical professionals on workplace health programs.
- Review and interpret safety-related regulations and standards.
- Monitor and update safety databases and reporting systems.
- Conduct safety workshops for new hires.
- Develop safety metrics and key performance indicators (KPIs).
- Implement safety awareness campaigns.
- Provide safety-related technical expertise to other departments.
- Coordinate safety training for remote or off-site workers.
- Analyze near-miss incidents to prevent future accidents.
- Develop safety protocols for remote work arrangements.
- Review and approve safety documentation for regulatory compliance.
- Conduct safety culture assessments and recommend improvements.
- Stay updated on industry trends, technologies, and best practices in safety engineering.
Conclusion
Safety engineers are indispensable in fostering secure work environments. Their multifaceted roles contribute significantly to mitigating risks, ensuring compliance, and promoting a culture of safety within organizations.
Fresher Safety Supervisor Salary
Fresher Safety Engineer Salary
Salary: EHS Officer (November, 2023)
FAQs:
- What are the primary qualifications needed to become a safety engineer? Safety engineers typically require a bachelor’s degree in engineering or a related field, alongside specialized training in occupational health and safety. Certifications in safety-related disciplines further enhance their qualifications.
- How does a safety engineer contribute to improving workplace culture? Safety engineers actively promote awareness and responsibility among employees, fostering a culture of safety through communication, training programs, and proactive safety measures.
- What steps do safety engineers take during emergency situations? During emergencies, safety engineers implement pre-established emergency response plans, coordinate evacuations if needed, and conduct thorough investigations to prevent future occurrences.
- Why is continuous improvement crucial in safety engineering? Continuous improvement ensures that safety measures remain effective and adaptable to evolving workplace dynamics, reducing potential risks and enhancing overall safety.
- How do safety engineers collaborate with other departments for safety measures? Safety engineers work across departments, providing guidance on safety protocols, conducting joint training sessions, and coordinating drills to ensure a cohesive approach to workplace safety.