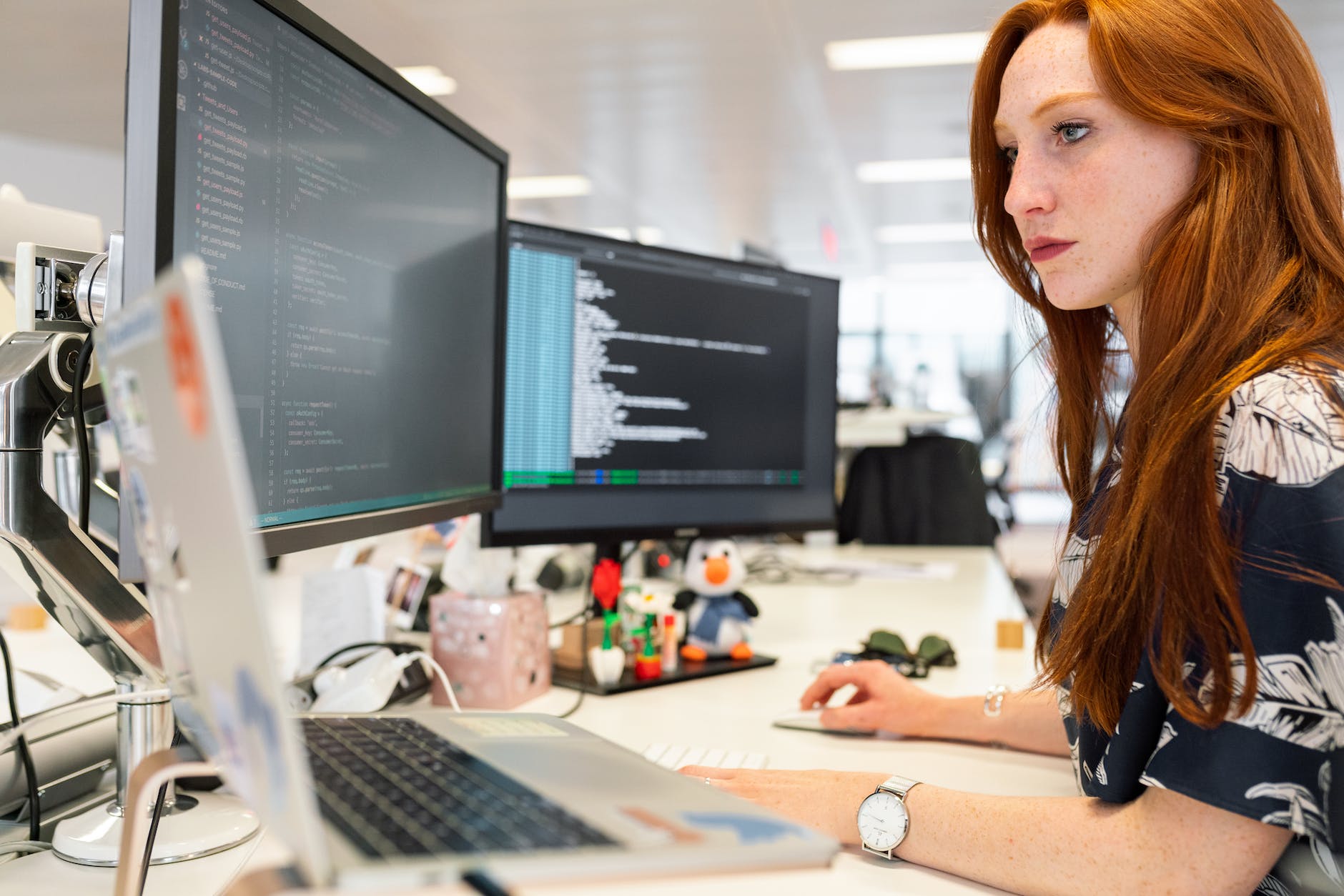
50 Duties of Safety Manager
50 Duties of Safety Manager : Safety managers play a pivotal role in ensuring workplace safety, employing strategies to prevent accidents, injuries, and health hazards. Their duties encompass various facets aimed at creating a secure work environment.
Core Responsibilities of a Safety Manager
Establishing Safety Protocols
Safety managers are responsible for devising and implementing safety protocols tailored to the specific needs of their organization. This involves developing guidelines for safe practices across all operations.
Conducting Risk Assessments
They conduct comprehensive risk assessments to identify potential hazards and mitigate risks effectively. By evaluating work environments, they preemptively address safety concerns.
Ensuring Compliance with Regulations
Safety managers keep abreast of evolving safety regulations and ensure strict adherence to these standards. They act as liaisons between the organization and regulatory bodies.
Training and Education Initiatives
Employee Training Programs
They design and conduct training programs to educate employees about safety procedures, emergency protocols, and the proper use of safety equipment.
Developing Safety Manuals
Safety managers create detailed safety manuals outlining protocols and procedures, serving as comprehensive guides for employees to reference.
Implementing Emergency Response Plans
They develop and implement emergency response plans, ensuring that all employees are aware of procedures to follow during crises.
Safety Inspections and Audits
Regular Site Inspections
Conducting routine inspections across work sites to identify potential hazards and ensure compliance with safety standards.
Auditing Safety Procedures
Regularly auditing existing safety protocols to identify areas for improvement and maintain optimal safety levels.
Incident Investigation and Reporting
Analyzing Incident Reports
Safety managers thoroughly investigate any accidents or incidents, identifying root causes and implementing measures to prevent recurrence.
Implementing Corrective Measures
They proactively implement corrective actions based on incident reports to enhance safety measures.
Maintaining Safety Equipment and Resources
Procuring and Maintaining Safety Gear
Responsible for acquiring, maintaining, and ensuring the proper use of safety equipment throughout the organization.
Managing Safety Budgets
They manage budgets allocated for safety resources, ensuring optimal utilization without compromising safety standards.
Collaboration with Management and Employees
Communication and Training
They foster open communication channels between management and employees, emphasizing the importance of safety measures.
Promoting Safety Culture
Safety managers promote a culture of safety awareness and responsibility among all employees.
Utilizing Technology in Safety Management
Integration of Safety Software
They leverage technological advancements by integrating safety software to streamline safety procedures and data management.
Implementing Innovative Safety Measures
Adopting innovative tools and methodologies to enhance safety protocols and outcomes.
Adapting to Industry Changes and Innovations
Embracing New Safety Standards
Staying updated with evolving safety standards and integrating them into existing practices.
Incorporating Technological Advancements
Adopting new technologies to improve safety measures and stay ahead of industry trends.
Measuring Safety Performance
Key Performance Indicators (KPIs)
Defining and tracking key performance indicators to measure the effectiveness of safety initiatives.
Metrics for Evaluating Safety Initiatives
Developing metrics to evaluate the success of implemented safety measures and making necessary adjustments.
Legal and Regulatory Compliance
Staying Abreast of Legal Changes
Continuously monitoring and adhering to changes in safety regulations and legal requirements.
Ensuring Compliance with Industry Standards
Ensuring the organization’s safety practices align with industry standards and best practices.
Crisis Management and Preparedness
Developing Crisis Response Plans
Creating comprehensive crisis response plans to address potential emergencies effectively.
Conducting Drills and Simulations
Organizing drills and simulations to prepare employees for potential crisis scenarios.
Continuous Improvement in Safety Practices
Feedback Mechanisms
Encouraging feedback from employees to continually improve safety measures.
Evolving Safety Strategies
Adapting safety strategies based on feedback and emerging trends to enhance workplace safety.
Challenges Faced by Safety Managers
Balancing Compliance and Productivity
Navigating the challenge of maintaining strict safety compliance without hindering productivity.
Overcoming Resistance to Safety Measures
Addressing resistance from employees or management towards implementing safety measures effectively.
Here's a comprehensive list of 50 duties that a Safety Manager might perform:
- Develop and implement safety policies and procedures.
- Conduct regular safety inspections and audits.
- Create and maintain safety training programs for employees.
- Investigate accidents and incidents to determine root causes.
- Analyze safety data and trends to identify areas for improvement.
- Ensure compliance with local, state, and federal safety regulations.
- Collaborate with department managers to address safety concerns.
- Conduct risk assessments and develop risk mitigation strategies.
- Monitor workplace conditions to ensure they meet safety standards.
- Provide safety-related guidance and support to employees.
- Manage emergency preparedness and response plans.
- Conduct safety meetings and training sessions.
- Implement and oversee safety equipment and personal protective gear usage.
- Develop and maintain safety communication protocols.
- Lead safety committees or teams.
- Review and update safety manuals and documentation.
- Investigate near misses and potential hazards.
- Conduct safety orientations for new hires.
- Recommend and implement safety improvements.
- Coordinate safety drills and exercises.
- Develop and track safety-related metrics and KPIs.
- Assess and manage safety-related budgets.
- Respond to safety concerns and complaints from employees.
- Conduct incident analysis and reporting.
- Collaborate with HR on safety-related policies and procedures.
- Coordinate with external agencies for safety compliance.
- Develop and maintain relationships with safety vendors and suppliers.
- Conduct safety-related research and stay updated on industry best practices.
- Perform safety audits of contractors and vendors.
- Develop safety awareness campaigns.
- Implement ergonomic assessments and improvements.
- Conduct safety behavior observations.
- Analyze and interpret safety regulations and standards.
- Develop safety-related training materials.
- Review and approve safety-related documentation.
- Conduct safety culture assessments.
- Manage safety-related documentation and records.
- Participate in incident investigation committees.
- Develop safety incentive programs.
- Ensure proper handling and disposal of hazardous materials.
- Coordinate safety-related communication during emergencies.
- Conduct safety-related performance evaluations.
- Develop and maintain safety-related partnerships with industry organizations.
- Implement safety-related technology solutions.
- Monitor and manage safety-related permits and licenses.
- Conduct safety-related vendor evaluations.
- Develop safety-related emergency response plans.
- Review and update safety-related policies in line with industry changes.
- Conduct safety-related benchmarking.
- Provide safety-related guidance during facility design or modifications.
This list isn't exhaustive and can vary depending on the industry, company size, and specific job requirements.
Conclusion
Safety managers hold a critical position in fostering a safe working environment. Their multifaceted duties encompass proactive measures, compliance adherence, and continuous improvement initiatives to ensure the well-being of all personnel.
Fresher Safety Supervisor Salary
Fresher Safety Engineer Salary
FAQs
- What qualifications are essential to become a safety manager?To become a safety manager, a strong educational background in occupational health and safety is crucial. A bachelor’s degree in occupational health, safety engineering, or a related field is often required. Additionally, certifications such as Certified Safety Professional (CSP) or Occupational Health and Safety Technician (OHST) can greatly enhance one’s credentials.
- How do safety managers stay updated with evolving safety regulations?Safety managers keep themselves updated by actively participating in professional development programs, attending workshops, seminars, and conferences related to safety management. They also engage with industry publications and regulatory agencies to stay informed about the latest safety standards and regulations.
- What are the common challenges safety managers encounter in their roles?Safety managers often face challenges in striking a balance between enforcing stringent safety measures and maintaining high productivity levels. Resistance to change from employees or management can also pose a challenge. Additionally, staying updated with rapidly evolving safety regulations and technology advancements is another common challenge.
- How often should safety inspections be conducted within an organization?The frequency of safety inspections varies based on the nature of the workplace, industry standards, and regulatory requirements. Generally, routine inspections are conducted regularly, ranging from daily checks of specific equipment to monthly or quarterly comprehensive inspections of the entire workplace.
- What role does technology play in modern safety management practices?Technology plays a pivotal role in modern safety management practices by offering innovative tools for risk assessment, incident reporting, and safety training. Safety managers utilize safety software, wearable technology, IoT devices, and data analytics to enhance safety protocols, monitor hazards, and improve overall safety outcomes within organizations.