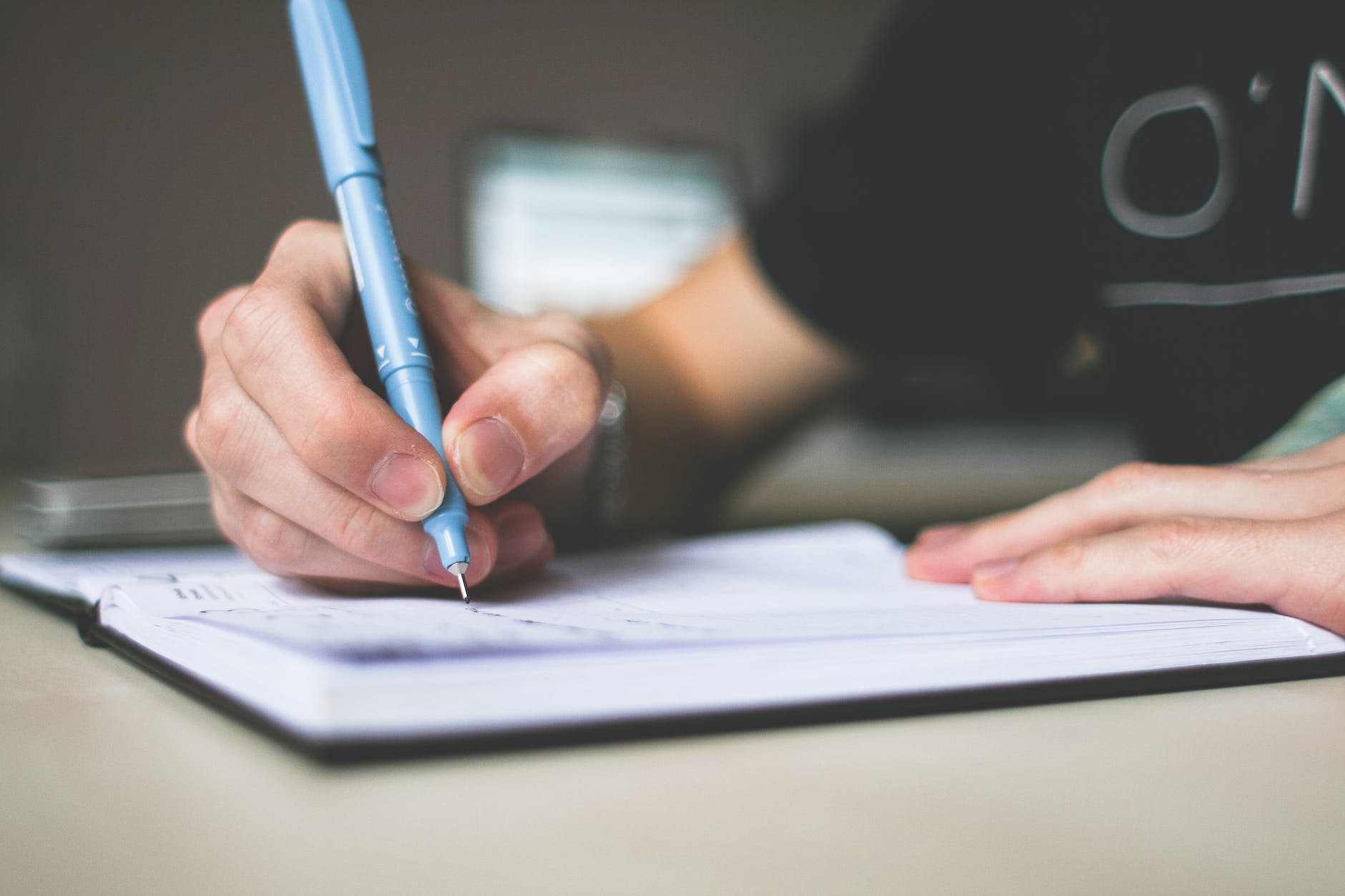
Difference between JHA and JSA | Download PPT
Workplace safety is paramount in any industry, and two vital methodologies contribute significantly to this aspect: Job Safety Analysis (JSA) and Job Hazard Analysis (JHA). Both are critical in identifying and mitigating risks, ensuring the well-being of employees and the smooth functioning of operations.
Introduction to JSA and JHA
Defining JSA and JHA
Job Safety Analysis (JSA) and Job Hazard Analysis (JHA) are systematic approaches used to assess potential risks and hazards in the workplace. JSA primarily focuses on breaking down job tasks into steps to identify potential hazards and implement preventive measures.
Understanding Job Safety Analysis (JSA)
JSA involves a step-by-step process:
- Identifying Tasks: Breaking down tasks into specific steps.
- Identifying Hazards: Recognizing potential risks in each step.
- Risk Mitigation: Implementing preventive measures to reduce identified risks.
- Regular Review: Continuously assessing and improving safety protocols.
Insight into Job Hazard Analysis (JHA)
Differences between JSA and JHA
While JSA is task-oriented, JHA is more focused on the hazards associated with a particular job or workplace. JHA delves deeper into identifying potential hazards and assessing the associated risks comprehensively.
JHA complements JSA by providing a more detailed analysis of potential hazards and their impact on employee safety.
Both Job Safety Analysis (JSA) and Job Hazard Analysis (JHA) are methods used in occupational safety to identify and mitigate risks in the workplace, but there are differences between the two.
Job Safety Analysis (JSA):
- Focus: JSA primarily concentrates on identifying potential safety hazards associated with a specific job or task.
- Purpose: It aims to break down a job into its individual steps, identify potential hazards, and determine preventive measures to ensure the safety of workers.
- Process: JSA involves a systematic approach where each step of a job is analyzed to identify hazards, evaluate risks, and develop controls to minimize or eliminate those risks.
- Key Aspects: Emphasis is on safety procedures, personal protective equipment (PPE), and safe work practices.
Job Hazard Analysis (JHA):
- Focus: JHA looks at a broader spectrum, not only considering safety hazards but also including health and environmental hazards related to a job or task.
- Purpose: It aims not just at identifying risks but also at understanding the potential impact on health and the environment.
- Process: Similar to JSA, JHA involves breaking down a job into steps to identify hazards and assess risks, but it has a more comprehensive approach that considers health and environmental factors as well.
- Key Aspects: Considers a wider range of hazards, including chemical exposure, ergonomics, and environmental impacts.
In summary, while both JSA and JHA focus on analyzing jobs to identify risks and prevent accidents, JSA primarily targets safety hazards, whereas JHA takes a more comprehensive approach by also considering health and environmental factors associated with a job or task.
Key Components of JSA and JHA
Both JSA and JHA share essential components:
- Risk assessment and identification: Identifying potential risks and hazards.
- Employee involvement and training: Ensuring employees are aware and trained to mitigate risks.
- Documentation and implementation: Recording findings and implementing preventive measures.
Advantages of Implementing JSA and JHA
Implementing JSA and JHA offers numerous benefits:
- Reduced workplace accidents: Identifying and mitigating risks proactively.
- Improved safety culture: Encouraging a culture of safety among employees.
- Compliance with safety regulations: Meeting legal requirements for workplace safety.
Challenges and Limitations
While JSA and JHA are effective, challenges exist:
- Resistance to change: Employees may resist new safety protocols.
- Time-consuming: Conducting thorough analyses can be time-intensive.
Best Practices for JSA and JHA Implementation
To ensure successful integration, companies must:
- Involve employees in the process.
- Continuously review and update safety protocols.
Conclusion
JSA and JHA play pivotal roles in maintaining workplace safety. Implementing these methodologies not only reduces accidents but also fosters a culture of safety awareness.
What is the Difference Between JSA and JHA?
Fall Protection Plan PPT | Download PPT
Hazardous Waste Management System PPT | Download PPT
Toolbox Talk Meeting on PPE | Download PPT
Standard Operating Procedure PPT | Download PPT | Safe Operating Procedure (SOP)
FAQs
- Are JSA and JHA the same thing?
- No, while both assess workplace safety, JSA focuses on tasks, while JHA evaluates hazards in jobs.
- Why is employee involvement crucial in JSA and JHA?
- Employee involvement ensures a better understanding of risks and promotes compliance with safety protocols.
- Can JSA and JHA be used in any industry?
- Yes, these methodologies are adaptable and can be applied across various industries.
- How often should JSA and JHA be reviewed?
- Regular reviews are essential to keep safety protocols updated, ideally conducted annually or with significant process changes.
- Do JSA and JHA guarantee zero accidents?
- While they significantly reduce risks, they can’t eliminate accidents entirely. Regular reviews and employee training are vital.