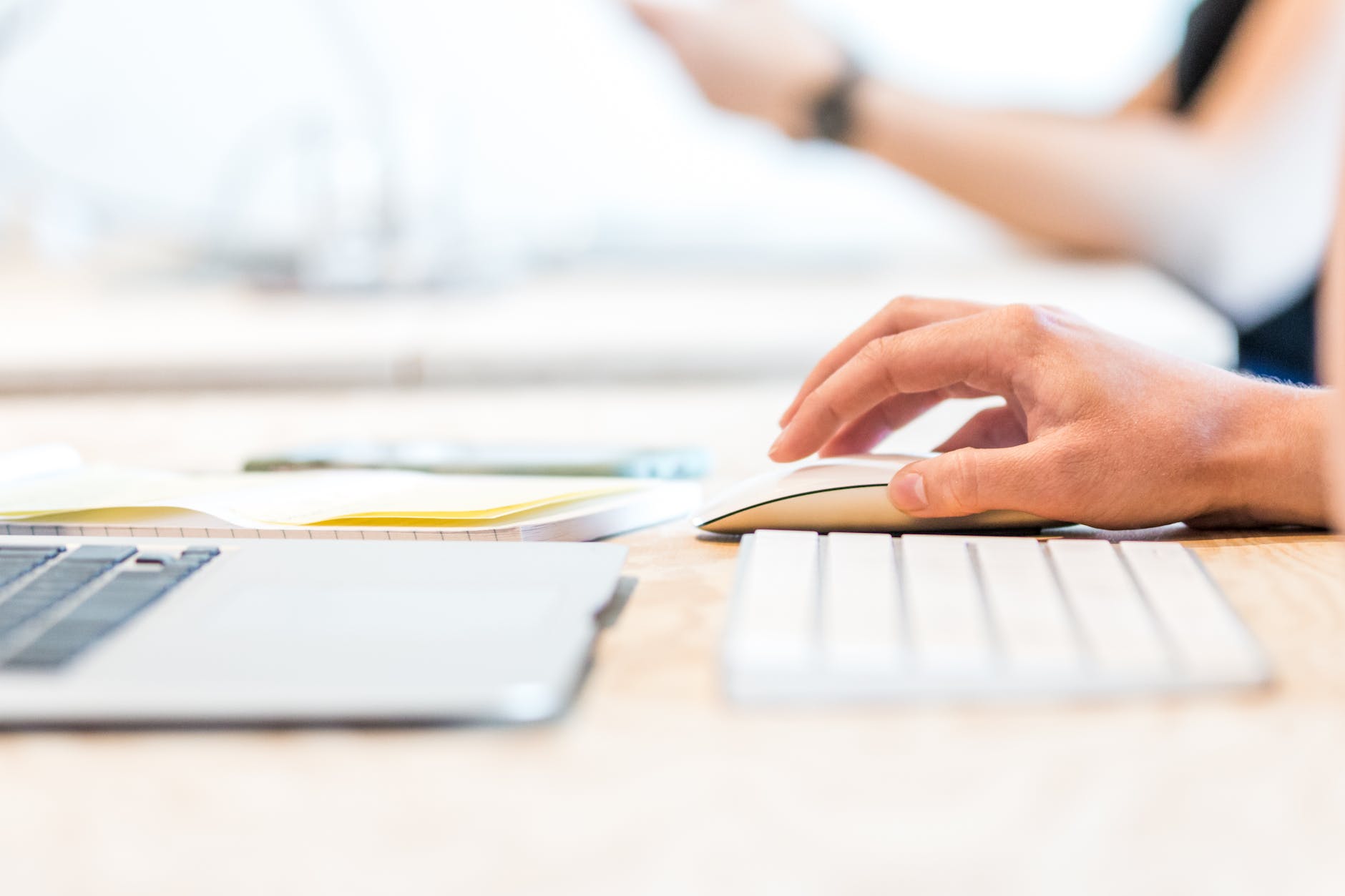
Standard Operating Procedure PPT | Download PPT | Safe Operating Procedure (SOP)
In today’s dynamic work environments, efficiency and safety stand as paramount elements across industries. Two essential frameworks contributing significantly to these aspects are Standard Operating Procedures (SOPs) and Safe Operating Procedures (SOPs). Understanding the nuances between these protocols is crucial for maintaining operational excellence and ensuring safety within organizations.
The difference between a Standard Operating Procedure (SOP) and a Safe Operating Procedure (also abbreviated as SOP) lies primarily in their focus and scope:
- Standard Operating Procedure (SOP):
- An SOP is a set of step-by-step instructions compiled to guide workers in performing routine tasks or processes within an organization. It outlines the best practices, protocols, and sequences necessary to accomplish specific tasks efficiently and consistently.
- SOPs cover a broad range of operations, including administrative tasks, manufacturing processes, quality control measures, and more.
- Its primary aim is to standardize and streamline operations, ensuring uniformity and quality in the outcomes across various departments or individuals performing the task.
- Safe Operating Procedure (SOP):
- A Safe Operating Procedure, on the other hand, specifically focuses on ensuring the safety of individuals while carrying out tasks or working in potentially hazardous environments.
- SOPs for safety detail the precautions, safety measures, protective gear requirements, emergency protocols, and other necessary steps to mitigate risks and prevent accidents or injuries.
- These procedures are often implemented in industries such as construction, manufacturing, laboratories, and any setting where there are potential risks to health and safety.
In summary, while both SOPs and Safe Operating Procedures share the acronym “SOP,” the former concentrates on standardizing operational processes, whereas the latter emphasizes safety measures and precautions to safeguard individuals while performing tasks.
Examples of both a Standard Operating Procedure (SOP) and a Safe Operating Procedure (SOP) in a construction setting:
Standard Operating Procedure (SOP) – Construction Site Setup:
Title: Construction Site Setup Procedure
Objective: To establish the standardized process for setting up a construction site for new projects.
- Preparing the Site:
- Clear the designated area of debris, vegetation, and any obstructions.
- Mark boundaries and access points clearly using safety tape or barriers.
- Equipment and Material Placement:
- Position construction machinery and tools in designated areas.
- Store materials securely, ensuring they don’t obstruct pathways or pose safety risks.
- Safety Measures:
- Install necessary safety signage indicating hazards and safety procedures.
- Provide personal protective equipment (PPE) and ensure its accessibility for workers.
- Utilities Setup:
- Arrange for electricity, water, and other utilities required for construction activities.
- Ensure proper installation of temporary facilities like toilets, first aid stations, etc.
- Inspection:
- Conduct a walkthrough inspection to verify that the site setup adheres to the SOP.
- Address any discrepancies or safety concerns before commencing work.
Safe Operating Procedure (SOP) – Working at Heights:
Title: Working at Heights Safety Procedure
Objective: To ensure the safety of workers performing tasks at elevated heights on the construction site.
- Risk Assessment:
- Identify tasks involving work at heights and assess associated risks.
- Plan and communicate necessary precautions before starting any work.
- Equipment Check:
- Inspect fall protection gear (harnesses, lanyards, etc.) for wear and tear.
- Verify the integrity of scaffolding, ladders, or any elevated platforms being used.
- Use of Personal Protective Equipment (PPE):
- Workers must wear approved safety harnesses securely fastened to appropriate anchor points.
- Use guardrails, toe boards, or safety nets where applicable to prevent falls.
- Safe Practices:
- Avoid overreaching while working and maintain three points of contact on ladders or platforms.
- Secure tools and materials to prevent accidental drops.
- Emergency Procedures:
- Establish clear communication methods in case of emergencies.
- Provide training on rescue and evacuation procedures in case of a fall.
These examples illustrate how a Standard Operating Procedure focuses on the setup and operational aspects of a construction site, while a Safe Operating Procedure concentrates specifically on safety measures to prevent accidents and injuries when working at heights.
Risk Management PPT | Download PPT
COVER LETTER | RESUME/CV/BIODATA | OFFER LETTER | DOWNLOAD FORMAT
HSE Key Performance Indicators and its types with example | Download PPT
Conclusion
In conclusion, while Standard Operating Procedures (SOPs) and Safe Operating Procedures (SOPs) share the common goal of guiding operations, they differ significantly in their focus and objectives. SOPs concentrate on streamlining processes for efficiency, while Safe Operating Procedures (SOPs) prioritize safety measures to prevent accidents and ensure a secure working environment.
Understanding the nuances between SOPs and Safe Operating Procedures (SOPs) is imperative for organizations to establish robust frameworks that not only optimize operations but also prioritize the safety and well-being of their workforce.
FAQs
- Are SOPs and Safe Operating Procedures (SOPs) interchangeable terms? SOPs and Safe Operating Procedures (SOPs) serve different purposes; SOPs focus on operational processes, while Safe Operating Procedures prioritize safety measures.
- How frequently should SOPs and Safe Operating Procedures (SOPs) be updated? Regular reviews are essential to ensure that SOPs and Safe Operating Procedures (SOPs) align with current industry standards and evolving needs, typically updated annually or as needed.
- What industries benefit the most from SOPs and Safe Operating Procedures (SOPs)? Various sectors, including healthcare, manufacturing, aviation, and logistics, rely on SOPs and Safe Operating Procedures (SOPs) to standardize processes and ensure safety.
- Can SOPs and Safe Operating Procedures (SOPs) coexist within an organization? Absolutely. Organizations can benefit from having both SOPs and Safe Operating Procedures (SOPs) to optimize efficiency while prioritizing safety measures.
- How do SOPs and Safe Operating Procedures (SOPs) contribute to regulatory compliance? SOPs and Safe Operating Procedures (SOPs) ensure that organizations adhere to industry standards and legal requirements, maintaining compliance and operational integrity.
It is so useful.