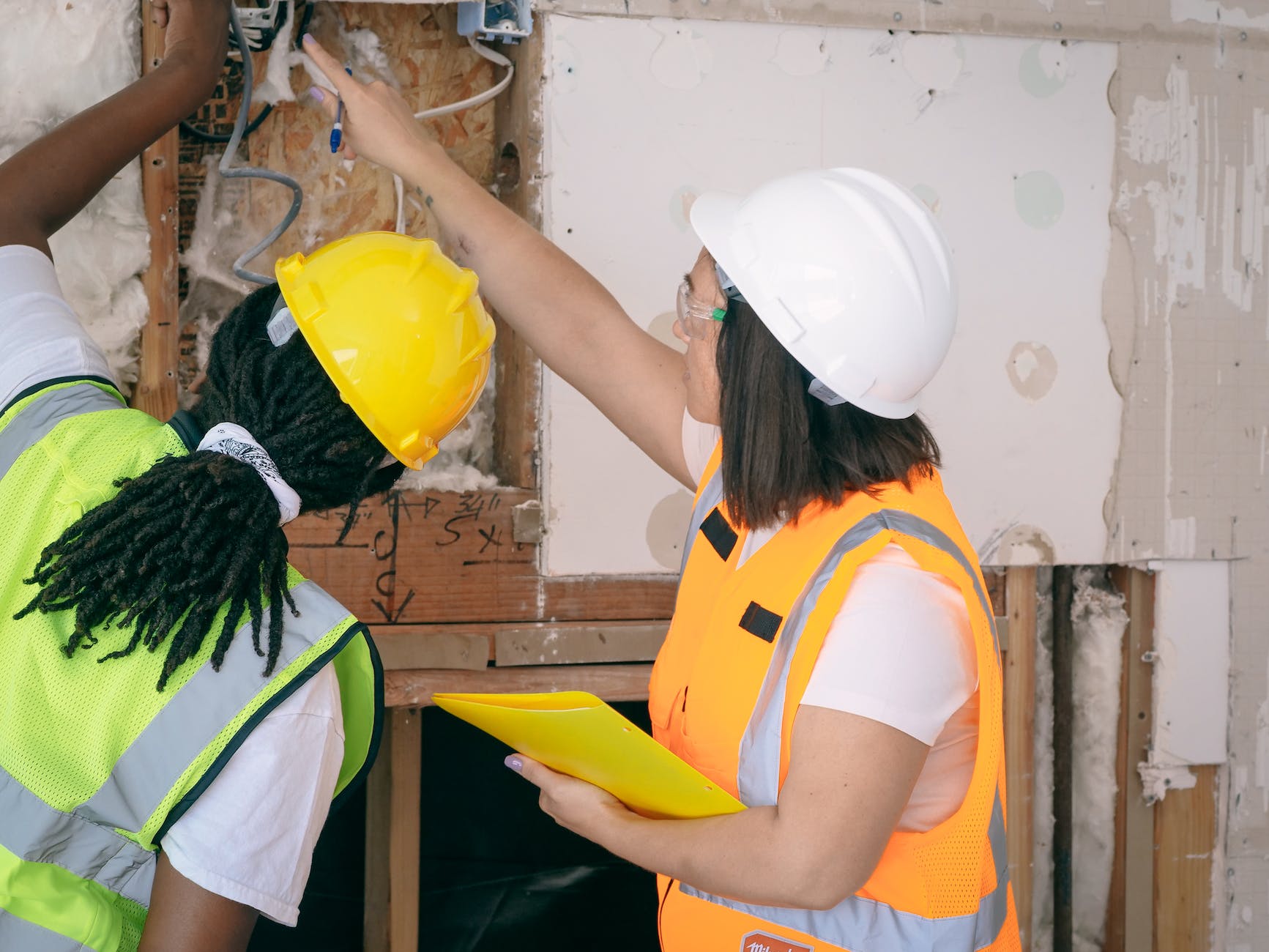
Heat Exchanger Safety: Prioritizing Inspection and Maintenance Procedures
Introduction
Heat exchangers play a pivotal role in various industries, facilitating the transfer of thermal energy between fluids. Ensuring the safety and efficiency of heat exchangers requires a proactive approach to inspection and maintenance. This article delves into the key procedures for maintaining heat exchanger safety, emphasizing the importance of regular inspections and proper maintenance practices.
Understanding the Significance of Heat Exchanger Safety
- Operational Efficiency
- Optimal Heat Transfer: Regular inspection and maintenance ensure that heat exchangers operate at their maximum efficiency, facilitating optimal heat transfer between fluids.
- Energy Conservation: Well-maintained heat exchangers contribute to energy conservation by minimizing energy losses during the heat exchange process.
- Safety Compliance
- Adherence to Regulations: Compliance with safety regulations is paramount. Routine inspections help identify and address issues that may compromise safety and regulatory compliance.
- Risk Mitigation: Proactive maintenance mitigates the risk of accidents, such as leaks or failures, that could lead to hazardous situations.
Inspection Procedures for Heat Exchangers
- Visual Inspections
- External Examination: Conduct regular visual inspections of the external surfaces for signs of corrosion, erosion, or physical damage.
- Leak Detection: Look for any visible signs of leaks, including stains, puddles, or discolored areas around the heat exchanger.
- Internal Inspection
- Tube and Channel Examination: Periodically inspect the interior components, such as tubes and channels, using specialized tools to identify fouling, scaling, or corrosion.
- Fluid Analysis: Conduct fluid analysis to detect any contamination or degradation of the heat transfer fluid.
- Non-Destructive Testing (NDT)
- Ultrasonic Testing: Utilize ultrasonic testing to identify potential defects, thickness variations, or abnormalities within the heat exchanger structure.
- Radiographic Testing: Employ radiographic methods to inspect welds and internal components without disassembly.
Maintenance Practices for Heat Exchanger Safety
- Cleaning Procedures
- Scale and Fouling Removal: Regularly clean heat exchanger surfaces to remove scale, fouling, or deposits that can impede heat transfer efficiency.
- Chemical Cleaning: Implement chemical cleaning procedures for stubborn deposits, ensuring the longevity of the heat exchanger.
- Tightening and Replacement of Components
- Bolt Tightening: Periodically inspect and tighten bolts and fasteners to maintain structural integrity.
- Component Replacement: Replace damaged or corroded components promptly to prevent further deterioration.
- Lubrication and Bearing Maintenance
- Bearing Lubrication: Ensure proper lubrication of bearings to minimize friction and wear.
- Alignment Checks: Regularly check and adjust alignment to prevent excessive stress on components.
Environmental Considerations in Heat Exchanger Safety
- Corrosion Protection
- Coating Application: Apply corrosion-resistant coatings to protect heat exchanger surfaces from environmental elements.
- Cathodic Protection: Implement cathodic protection systems in corrosive environments to mitigate the risk of corrosion.
- Weather-Resistant Enclosures
- Enclosure Installation: Install weather-resistant enclosures to shield heat exchangers from harsh weather conditions.
- Ventilation: Ensure proper ventilation within enclosures to prevent the buildup of heat.
Documentation and Record-Keeping
- Maintenance Logs
- Comprehensive Records: Maintain detailed logs of all inspections, maintenance activities, and repairs performed on heat exchangers.
- Historical Data: Historical data aids in trend analysis, facilitating predictive maintenance and early issue detection.
- Scheduling and Planning
- Routine Maintenance Schedules: Establish routine maintenance schedules based on manufacturer recommendations and operational demands.
- Shutdown Planning: Plan maintenance activities during scheduled shutdowns to minimize operational disruptions.
Conclusion
Heat exchanger safety is paramount for efficient industrial operations and the well-being of personnel. By prioritizing regular inspections, proactive maintenance practices, and adherence to safety regulations, industries can optimize heat exchanger performance and extend their operational lifespan. The integration of environmental considerations and meticulous record-keeping further enhances overall safety protocols, ensuring a secure and reliable heat exchange process.
Occupational Health Surveillance: Monitoring and Preventing Work-Related Health Issues
Energy Sector Safety Engineering: Challenges and Solutions in Oil, Gas, and Renewable Energy
Safety Data Analytics: Leveraging Big Data for Proactive Risk Management
Process Hazard Analysis (PHA): Methodologies and Applications for Safety Engineers
Transportation Safety Engineering: Ensuring Safe Operations in the Transportation Sector
Frequently Asked Questions (FAQs)
- Why is heat exchanger safety important?
- Heat exchanger safety is crucial for operational efficiency, energy conservation, and compliance with safety regulations. Regular inspections and maintenance help identify and address potential issues.
- What are the key inspection procedures for heat exchangers?
- Key inspection procedures include visual inspections, internal examinations, non-destructive testing (NDT), and fluid analysis to identify potential issues such as corrosion, fouling, or leaks.
- What are common maintenance practices for heat exchangers?
- Common maintenance practices include cleaning procedures to remove scale and fouling, tightening and replacement of components, lubrication and bearing maintenance, and environmental considerations such as corrosion protection.
- Why is documentation and record-keeping important for heat exchanger safety?
- Comprehensive records aid in trend analysis, facilitate predictive maintenance, and provide historical data for inspections, maintenance activities, and repairs performed on heat exchangers.
- How can industries ensure environmental considerations in heat exchanger safety?
- Industries can implement corrosion protection measures, apply weather-resistant coatings, install protective enclosures, and consider environmental factors in the design and location of heat exchangers.