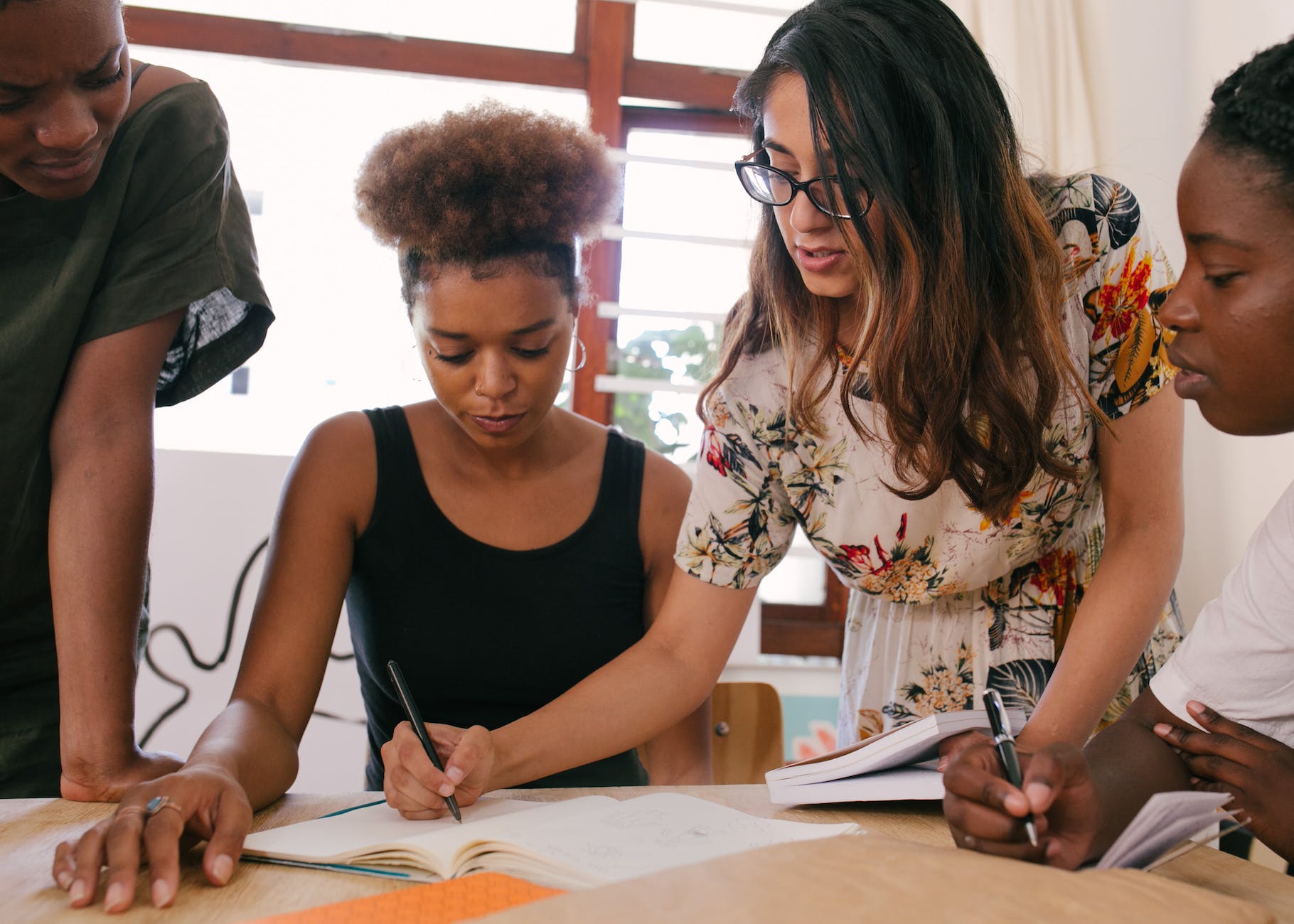
How to Prepare Risk Assessment for Vibration
How to Prepare Risk Assessment for Vibration : Vibrations are common in various industries, but they can pose significant health and safety risks to workers. To ensure the well-being of employees and comply with legal requirements, businesses need to conduct Vibration Risk Assessments. In this article, we will guide you through the process of preparing a Vibration Risk Assessment, step by step.
What is Vibration Risk Assessment?
Vibration Risk Assessment is a systematic process that evaluates the potential risks associated with exposure to hand-arm and whole-body vibrations in the workplace. These assessments are essential in identifying and mitigating health hazards caused by continuous or frequent exposure to vibrations, such as those generated by heavy machinery, vehicles, or hand-held tools.
Importance of Vibration Risk Assessment
Conducting Vibration Risk Assessments is not just a legal obligation but also a moral responsibility. It ensures that workers are protected from health issues caused by prolonged exposure to vibrations. These assessments help organizations:
- Prevent workplace-related health problems
- Enhance employee safety and well-being
- Comply with legal requirements
Legal Requirements for Vibration Risk Assessment
In many countries, there are strict regulations in place to protect workers from the adverse effects of vibrations. Employers are legally obliged to assess and control exposure to vibrations. These laws vary by region but generally require:
- Regular assessments of vibration exposure
- Implementation of control measures
- Monitoring and recording of exposure levels
Steps to Prepare a Vibration Risk Assessment
Understanding the Work Environment
Identifying Sources of Vibration
The first step in conducting a Vibration Risk Assessment is to understand the work environment. Identify the sources of vibration, such as heavy machinery or hand-held power tools. Different sources may require different approaches to assessment.
Assessing Exposure Levels
Measure the vibration exposure levels experienced by employees. This can involve using specialized equipment to record vibrations over a period of time. The data collected will help in determining the level of risk.
Risk Evaluation
Determining Control Measures
Based on the exposure levels, you need to decide on appropriate control measures. These measures can include redesigning work processes, providing personal protective equipment, or implementing vibration-damping technologies.
Monitoring and Review
Continuous monitoring and review are crucial to ensure that control measures are effective. Regularly reassess exposure levels and adjust control measures as necessary.
Vibration Risk Assessment Tools and Equipment
To perform accurate assessments, you’ll need various tools and equipment, including:
- Vibration meters
- Accelerometers
- Software for data analysis
- Personal protective equipment
Training and Education
Properly train employees on the risks associated with vibrations and the use of control measures. Education is key to ensuring the effectiveness of a Vibration Risk Assessment.
Common Mistakes to Avoid
When preparing a Vibration Risk Assessment, avoid common mistakes like:
- Failing to consider all sources of vibration
- Inadequate data collection
- Neglecting regular reviews of control measures
Benefits of Vibration Risk Assessment
Apart from legal compliance, Vibration Risk Assessments offer several benefits:
- Healthier and more productive employees
- Lower healthcare costs
- Enhanced reputation as a responsible employer
Challenges Faced in Vibration Risk Assessment
The process isn’t without its challenges. These can include difficulties in obtaining accurate data, resistance to change, and the initial costs of implementing control measures.
Scenario: Imagine a manufacturing company, ABC Manufacturing, which produces heavy machinery. They have a workforce of skilled technicians responsible for assembling and testing these machines. The machines generate significant vibrations during operation, and there’s a growing concern about the long-term health impact on their employees. To address this issue, ABC Manufacturing decides to conduct a Vibration Risk Assessment.
Vibration Risk Assessment Example:
Step 1: Understanding the Work Environment
Identifying Sources of Vibration
The first step is to identify the sources of vibration in the workplace. At ABC Manufacturing, this includes the large industrial machines, such as hydraulic presses and grinders, which produce vibrations during operation. Additionally, handheld power tools like impact wrenches also contribute to employee exposure.
Assessing Exposure Levels
To assess exposure levels, the company hires a certified safety consultant. The consultant installs vibration meters on key machines and tools to monitor the vibrations over a defined period. This data collection process helps quantify the extent of exposure and identify areas of concern.
Step 2: Risk Evaluation
Determining Control Measures
Based on the data collected, ABC Manufacturing recognizes the need for control measures. The consultant recommends implementing vibration-damping materials on the floors and investing in anti-vibration gloves for workers using handheld power tools. They also suggest ergonomic adjustments to machine operation to minimize vibration transmission.
Monitoring and Review
The company establishes a routine monitoring and review process. They conduct follow-up assessments at regular intervals to ensure the control measures are effective. These periodic reviews also enable them to make adjustments as needed, ensuring a safe working environment.
Training and Education
Recognizing the importance of educating their employees, ABC Manufacturing arranges training sessions. Workers are taught about the risks associated with prolonged exposure to vibrations and the proper use of control measures. The training helps foster a culture of safety within the organization.
Benefits: As a result of their Vibration Risk Assessment, ABC Manufacturing experiences several benefits:
- Employees report fewer health-related issues and are more productive.
- The company’s healthcare costs decrease as a result of reduced worker injuries.
- ABC Manufacturing gains a reputation as a responsible employer, attracting more skilled workers and improving its brand image.
Challenges: ABC Manufacturing also faces some challenges during the process, including the initial costs of implementing control measures and the resistance to change from long-standing work practices. However, these challenges are outweighed by the long-term benefits of a safer work environment.
Future Trends: ABC Manufacturing stays informed about future trends in Vibration Risk Assessment. They invest in new technology, like wearable vibration sensors, to further improve the accuracy of their assessments and enhance their employee safety programs.
In conclusion, ABC Manufacturing’s commitment to conducting a Vibration Risk Assessment has not only protected its employees from health hazards but has also resulted in a safer, more productive, and responsible work environment. This scenario highlights the importance of Vibration Risk Assessments in the manufacturing industry, where the well-being of employees is of paramount concern.
Future Trends in Vibration Risk Assessment
With advancements in technology, we can expect more efficient and accurate tools for Vibration Risk Assessment. Stay updated to ensure your assessments are in line with the latest developments.
Conclusion
In conclusion, Vibration Risk Assessment is a critical aspect of workplace safety. It protects employees from health hazards, ensures legal compliance, and promotes overall well-being. By following the steps outlined in this article and staying informed about future trends, organizations can create safer working environments.
How to Do Hand-Arm Vibration Measurement
Hand-Arm Vibration Risk Assessment
FAQs
- Why is Vibration Risk Assessment important?Answer: Vibration Risk Assessment is essential to protect workers from the health hazards associated with prolonged exposure to vibrations. It helps employers identify and mitigate risks, ensuring a safe and healthy working environment. Additionally, it is often a legal requirement in many regions to comply with workplace safety regulations.
- What are the legal requirements for Vibration Risk Assessment?Answer: Legal requirements for Vibration Risk Assessment vary by country and region. However, they typically mandate regular assessments of vibration exposure, the implementation of control measures, and monitoring and recording of exposure levels. To ensure compliance, it’s crucial to stay informed about the specific regulations in your area.
- How often should Vibration Risk Assessments be conducted?Answer: The frequency of Vibration Risk Assessments depends on the level of vibration exposure in your workplace. In high-risk environments, assessments may need to be conducted more frequently, while lower-risk settings may require less frequent assessments. Regular monitoring and reviews are essential to ensure ongoing safety.
- What are the common mistakes to avoid in Vibration Risk Assessment?Answer: Common mistakes to avoid include failing to consider all sources of vibration in the workplace, inadequate data collection, and neglecting regular reviews of control measures. It’s crucial to conduct comprehensive assessments and ensure that control measures are regularly maintained and adjusted when necessary.
- How can technology improve Vibration Risk Assessment processes?Answer: Technology plays a significant role in improving Vibration Risk Assessment. It allows for more accurate data collection and analysis, offering real-time information on exposure levels. Advanced tools, such as wearable vibration sensors and data analytics software, enable better control measures and quicker responses to potential risks, ultimately enhancing workplace safety.