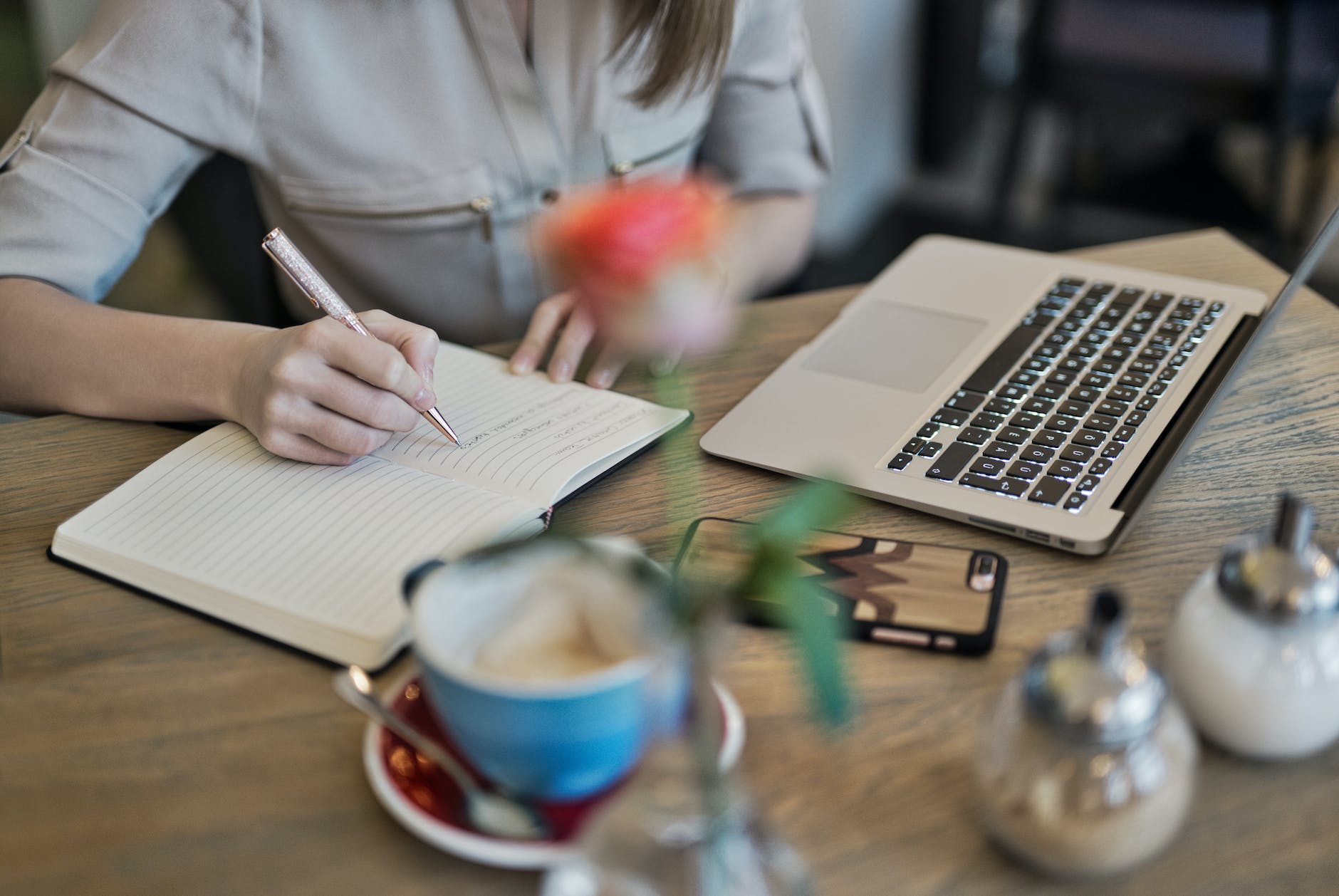
Hydrotest Safety Hazards and Control Measures
In the world of industrial processes and infrastructure development, hydrostatic testing, commonly known as hydrotest, plays a crucial role in ensuring the integrity and safety of various components, pipelines, and equipment. However, as with any industrial process, hydrotesting comes with its own set of safety hazards that need to be recognized and managed effectively. In this article, we will delve into the potential safety hazards associated with hydrotesting and explore the essential control measures that can mitigate these risks.
Introduction
Hydrotest Safety Hazards and Control Measures : Hydrotesting is a crucial step in ensuring the reliability and safety of industrial equipment and pipelines. However, the process involves inherent risks that need to be managed effectively to prevent accidents and incidents.
Understanding Hydrostatic Testing
Hydrostatic testing involves pressurizing equipment or pipelines with liquid, usually water, to assess their structural integrity and identify potential leaks. This process helps detect weaknesses before the equipment is put into operation.
Safety Hazards During Hydrotesting
High-Pressure Risks
The primary hazard during hydrotesting is the risk of high pressure. The pressure exerted during the test can lead to equipment rupture, causing severe injuries and even fatalities.
Equipment Failure Possibilities
Faulty equipment or materials can fail under pressure, leading to catastrophic consequences. Equipment failure can result from manufacturing defects, corrosion, or inadequate quality control.
Chemical Exposure
The liquids used in hydrotesting can sometimes contain chemicals that pose health hazards. Workers who come into contact with these liquids without proper protective gear might suffer skin irritation, respiratory issues, or chemical burns.
Structural Integrity Concerns
Hydrotesting might reveal weaknesses in the structural integrity of equipment or pipelines. These weaknesses, if not addressed, can compromise the performance and safety of the equipment during operation.
Control Measures to Ensure Safety
Thorough Risk Assessment
Before conducting a hydrotest, a comprehensive risk assessment should be performed. This assessment helps identify potential hazards and develop strategies to mitigate them.
Proper Equipment Inspection
Regular inspection of equipment before testing is essential to identify any defects or weaknesses that might lead to failure under pressure.
Effective Communication
Clear communication among all team members involved in the hydrotest is vital. Everyone should be aware of their roles, responsibilities, and emergency procedures.
Chemical Handling Protocols
If chemicals are present in the testing liquids, proper handling protocols must be followed. Personal protective equipment (PPE) and safety procedures should be strictly adhered to.
Structural Analysis and Reinforcement
Weaknesses detected during testing should be addressed through structural analysis and reinforcement. This ensures that the equipment can withstand operational pressures safely.
Importance of Training and Awareness
Proper training and awareness programs for workers and technicians involved in hydrotesting are essential. They should be knowledgeable about the risks and safety protocols to minimize accidents.
Emergency Preparedness and Response
An emergency response plan should be in place, outlining the steps to take in case of an unexpected equipment failure or other hazardous situations.
Regulatory Compliance and Standards
Adherence to industry regulations and standards is crucial. These guidelines ensure that hydrotesting is conducted safely and effectively.
Hydrotest Planning and Execution
Thorough planning is essential for a safe and successful hydrotest. This includes selecting the right testing methods, equipment, and personnel.
Continuous Monitoring and Evaluation
Regular monitoring and evaluation of the equipment’s performance post-hydrotest are essential to ensure its ongoing integrity and safety.
Conclusion
Hydrotest safety hazards are a critical concern in the world of industrial testing. By recognizing these risks and implementing effective control measures, industries can ensure the safety of their workers, equipment, and the environment. Proper planning, inspection, communication, and adherence to standards are key to preventing accidents and incidents during hydrotesting.
FAQs
- What is hydrostatic testing? Hydrostatic testing involves pressurizing equipment with liquid to assess its structural integrity and identify leaks before operation.
- Why is risk assessment important before a hydrotest? Risk assessment helps identify potential hazards and develop strategies to mitigate them, ensuring the safety of the testing process.
- What are some common safety hazards during hydrotesting? Common hazards include high-pressure risks, equipment failure, chemical exposure, and structural integrity concerns.
- Why is continuous monitoring necessary after a hydrotest? Continuous monitoring ensures that any potential issues or weaknesses are identified and addressed post-testing to maintain equipment integrity.