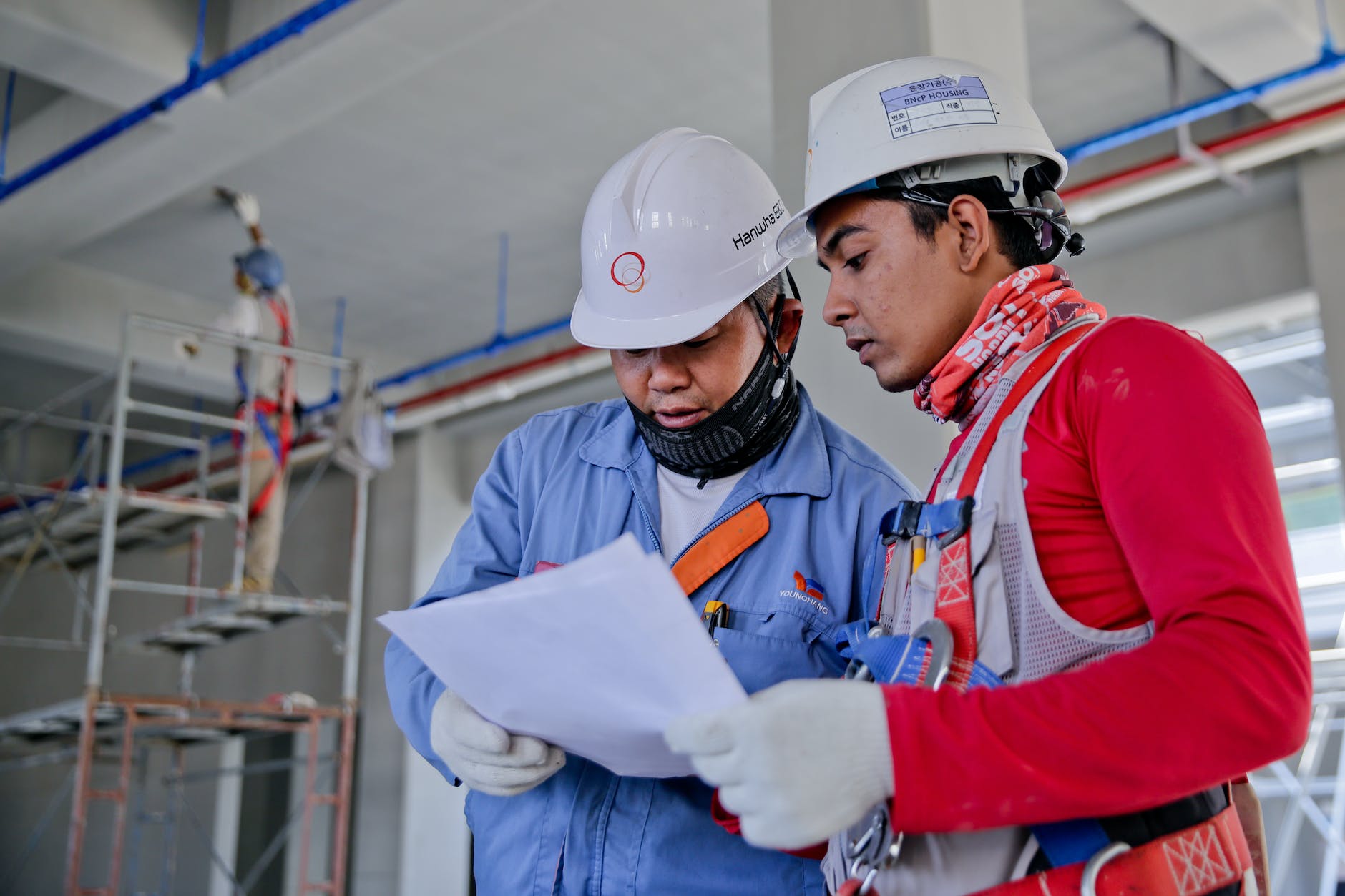
Hydrotest Safety: Ensuring Safety and Compliance in Pressure Testing
Pressure testing is a critical aspect of various industries, ensuring the integrity and reliability of equipment designed to withstand different operating conditions. One common method employed for pressure testing is hydrostatic testing, which involves subjecting equipment or pipelines to water or another liquid at high pressures to detect any potential weaknesses or leaks. While hydrostatic testing is essential for ensuring the safety and performance of equipment, it also presents its own set of safety challenges. In this article, we will delve into the significance of hydrotest safety, best practices to minimize risks, and the importance of regulatory compliance.
Understanding Hydrostatic Testing
Hydrotest Safety : Hydrostatic testing involves filling equipment, pipes, or vessels with liquid to test their strength and integrity under pressure. It is commonly used in industries such as oil and gas, construction, manufacturing, and more. The process helps identify weak points, defects, and potential leaks, ensuring that the equipment can safely handle the pressures it will experience during regular operation.
The Significance of Hydrotest Safety
Safety is paramount when conducting hydrostatic tests. The high pressures involved pose risks to both personnel and equipment. Inadequate safety measures can lead to catastrophic failures, injuries, and environmental damage. Implementing stringent safety protocols is crucial to prevent accidents and ensure the well-being of everyone involved.
Common Hazards Associated with Hydrostatic Testing
Pressure-Related Risks
The primary hazard during hydrostatic testing is the potential for overpressurization. If equipment is subjected to pressures beyond its design limits, it can rupture, leading to hazardous releases of fluid and causing harm to nearby personnel.
Equipment Failure
Weak or compromised equipment can fail under the high pressures of testing, resulting in leaks, ruptures, or explosions. Such failures can have severe consequences, including injuries, loss of life, and significant property damage.
Environmental and Property Damage
A leak or rupture during testing can lead to the release of liquids that are harmful to the environment. Moreover, property damage from equipment failures can result in costly repairs, downtime, and legal liabilities.
Ensuring Safe Hydrostatic Testing
To ensure hydrotest safety, several practices should be followed:
Adequate Training and Expertise
Personnel involved in hydrostatic testing should receive proper training on the equipment, procedures, and safety protocols. Adequate knowledge and experience are vital to making informed decisions during testing.
Thorough Inspection of Equipment
Before testing, equipment must undergo a thorough inspection to identify any pre-existing defects or weaknesses. Any issues should be addressed before testing begins.
Proper PPE and Safety Measures
Personnel should wear appropriate personal protective equipment (PPE) to safeguard against potential hazards. Safety measures, such as barricades and warning signs, should also be implemented.
Controlled Pressure Increase
Pressure should be increased gradually during testing to ensure that the equipment can handle incremental increases without failing suddenly.
Emergency Procedures and Contingency Plans
Clear emergency procedures and contingency plans should be established before testing. Personnel should know how to respond to unexpected events and quickly shut down the test if necessary.
Regulatory Compliance and Standards
Hydrostatic testing is subject to various regulatory standards and codes, including:
API Standards
The American Petroleum Institute (API) provides guidelines for pressure testing in the oil and gas industry. Following API standards ensures that testing is conducted safely and effectively.
ASME Codes
The American Society of Mechanical Engineers (ASME) codes offer guidance on pressure vessel and piping testing. Adhering to these codes helps ensure compliance and safety.
Local Regulations
Local regulations and industry-specific standards must also be considered during hydrostatic testing. These regulations may vary by region and application.
Importance of Documentation
Thorough documentation is crucial for hydrotest safety and compliance:
Test Plans and Procedures
Detailed test plans and procedures should be developed before testing begins. These documents outline the steps to be taken and help ensure consistency.
Record Keeping
Accurate record keeping of test results, observations, and any deviations from the plan is essential. These records provide valuable insights for future testing and regulatory compliance.
Collaboration and Communication
Hydrostatic testing requires collaboration among various teams:
Cross-Functional Teams
Different departments, such as engineering, operations, and safety, must collaborate to ensure a well-rounded testing process.
Clear Communication Channels
Open communication among team members and stakeholders is critical to address any concerns, share observations, and make real-time decisions.
Conclusion
Hydrostatic testing is a vital process for verifying the integrity of equipment under pressure. However, it comes with inherent risks that must be managed effectively. By adhering to strict safety protocols, regulatory standards, and thorough documentation, industries can mitigate hazards and ensure the safety of personnel, equipment, and the environment.
FAQs
- What is hydrostatic testing? Hydrostatic testing involves subjecting equipment or pipelines to liquid at high pressures to identify weaknesses or leaks.
- Why is hydrotest safety important? Hydrotest safety is crucial to prevent accidents, injuries, equipment failures, and environmental damage.
- What are the primary hazards of hydrostatic testing? Pressure-related risks, equipment failure, and environmental damage are common hazards.
- What standards govern hydrostatic testing? Hydrostatic testing is governed by API standards, ASME codes, and local regulations.
- Why is documentation essential in hydrostatic testing? Documentation ensures compliance, consistency, and the ability to learn from past tests.