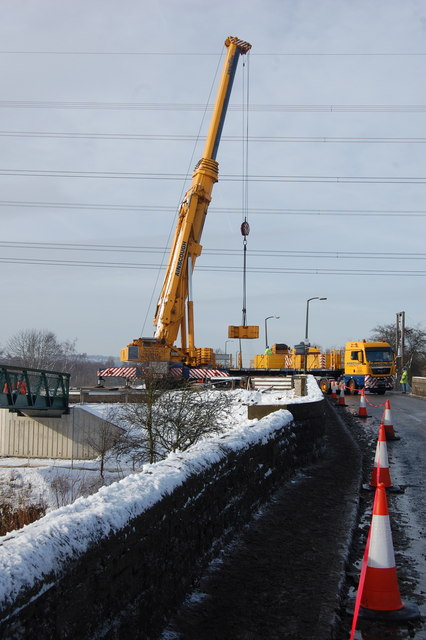
Load Moment Indicator (LMI) of Crane Safety | Download PPT
Introduction
Crane safety is a paramount concern in various industries, and one of the key contributors to ensuring safe crane operations is the Load Moment Indicator (LMI). This article delves into the intricacies of LMI, its components, installation, and the pivotal role it plays in preventing overloads, thereby enhancing overall safety.
Understanding Load Moment Indicator (LMI)
Load Moment Indicator, commonly known as LMI, is a critical safety feature integrated into cranes. Essentially, it is a device designed to monitor the load being lifted and the corresponding moment exerted on the crane. This real-time data allows operators to make informed decisions, preventing overloads and potential accidents.
Components of Load Moment Indicator
The LMI comprises various components working in tandem to ensure accurate monitoring. Sensors, often strategically placed on the crane, detect crucial data regarding load and angles. This information is then processed by a data processing unit, and the results are displayed on an interface accessible to the operator.
Importance in Preventing Overloading
The primary function of LMI is to detect and prevent overloads. By constantly monitoring the load and comparing it to the crane’s capacity, LMI ensures that the equipment operates within safe limits. Overloading not only poses risks to personnel but also leads to significant wear and tear on the crane, impacting its longevity and performance.
Types of Load Moment Indicators
There are several types of LMIs available, catering to different crane setups. Wireless LMIs offer flexibility, while hard-wired LMIs provide stability. Hydraulic and electronic LMIs offer unique features, allowing companies to choose the most suitable option for their specific needs.
Installation and Calibration of LMI
Proper installation and calibration are crucial for the effective functioning of LMI. Sensors must be positioned accurately, and regular recalibration is necessary to maintain precision. This ensures that the LMI provides reliable data, enabling operators to make swift and informed decisions.
Regulations and Standards
Various regulatory bodies, including OSHA, have established guidelines for the implementation of LMIs. Adhering to these standards is not only a legal requirement but also a proactive measure to enhance safety on worksites.
Benefits of Load Moment Indicator
Implementing LMI brings several benefits to crane operations. Enhanced safety is the foremost advantage, followed by increased operational efficiency and reduced maintenance costs. The real-time monitoring provided by LMI contributes to a smoother workflow and minimizes the risk of accidents.
Challenges in LMI Implementation
While LMI is a powerful safety tool, its implementation comes with challenges. Technical issues and the need for operator training are common hurdles that companies must address to ensure the successful integration of LMI into their crane operations.
A Load Moment Indicator (LMI) is a crucial safety device used in cranes to prevent overloading and ensure safe lifting operations. It is designed to monitor the load on the crane's hook and provide real-time feedback to the operator about the load moment, which is the product of the load weight and its distance from the crane's center of rotation.
Here are some key aspects of Load Moment Indicators and their role in crane safety:
- Overload Prevention: The primary function of an LMI is to prevent overloading of the crane. If the load being lifted approaches or exceeds the crane’s rated capacity, the LMI activates alarms and, in some cases, automatically stops crane operations to avoid unsafe conditions.
- Load Monitoring: LMI continuously monitors the load on the crane’s hook and considers factors such as the boom length, angle, and configuration. This information is used to calculate the load moment and compare it with the crane’s rated capacity.
- Visual and Audible Warnings: When the load moment approaches the safe limit, the LMI provides visual and audible warnings to alert the crane operator. These warnings help operators make informed decisions and take corrective actions to avoid potential hazards.
- Cut-off Function: In critical situations where the load moment exceeds the safe limits, the LMI may have a cut-off function that automatically stops crane movement to prevent overloading. This adds an additional layer of safety to crane operations.
- Calibration and Configuration: Regular calibration and proper configuration of the LMI are essential for accurate load monitoring. This ensures that the LMI provides precise information to the crane operator, maintaining the overall safety of lifting operations.
- Adaptability to Crane Type: LMIs are designed to suit different types of cranes, including mobile cranes, tower cranes, and crawler cranes. The system must be compatible with the specific crane model to ensure effective load monitoring.
- Training for Operators: Crane operators should receive training on the proper use and interpretation of LMI readings. Understanding the LMI’s signals and warnings is crucial for operators to make safe and informed decisions during lifting operations.
In summary, Load Moment Indicators play a vital role in crane safety by preventing overloading, providing real-time load monitoring, and offering visual and audible warnings to operators. Proper calibration, configuration, and operator training are essential to ensure the effective functioning of LMIs and maintain a safe working environment.
Let's consider a scenario where a mobile crane equipped with a Load Moment Indicator (LMI) is lifting a load. The LMI provides real-time feedback to the operator to ensure safe lifting operations.
Scenario: Mobile Crane Operation with Load Moment Indicator
Setting: A construction site where a mobile crane is lifting a load onto a building structure.
- Load Preparation:
- The crane operator receives instructions to lift a load of steel beams onto the 10th floor of the building under construction.
- The LMI is calibrated and configured to the specifications of the mobile crane, considering factors such as boom length, angle, and load radius.
- Lifting Operation:
- As the crane begins to lift the load, the LMI continuously monitors the load on the hook.
- The load moment, calculated based on the load weight and its distance from the crane’s center of rotation, is displayed on the LMI panel in the operator’s cabin.
- Real-time Monitoring:
- The operator observes the LMI readings, which include the current load moment and other relevant parameters.
- The LMI provides visual indicators, such as a color-coded display, to show whether the load is within the safe operating range or approaching the capacity limit.
- Warnings and Alarms:
- As the load moment approaches the safe limit, the LMI activates visual warnings on the display and audible alarms in the operator’s cabin.
- The visual warnings may change from green to yellow, indicating a cautionary zone, and eventually to red if the load moment exceeds the safe capacity.
- Operator Response:
- In response to the warnings, the crane operator assesses the situation and decides whether to adjust the load position, reduce the load weight, or take any corrective actions.
- If necessary, the operator can communicate with the ground crew to ensure a safe and controlled lifting operation.
- Automatic Cut-off (if applicable):
- In extreme cases where the load moment surpasses the safe limits, the LMI may have an automatic cut-off function. This function stops crane movements to prevent overloading and potential accidents.
- Safe Completion of Lift:
- The crane operator makes necessary adjustments based on the LMI feedback, ensuring that the load moment remains within the safe operating range.
- Once the load is safely positioned on the 10th floor, the lifting operation is completed successfully.
This example illustrates how a Load Moment Indicator contributes to crane safety by providing real-time monitoring, warnings, and potential automatic cut-off in critical situations, ultimately ensuring a safe and efficient lifting operation on the construction site.
40 Duties of a Safety Officer PPT | Download PPT
Occupational Safety & Health Management System (OSHMS) | Download PPT
Top 10 Safety Rules of Oil and Gas Industry | Download PPT
HSE Management System PPT | Download PPT
Oil and Gas Industry Hazards and Control Measures PPT | Download PPT
Conclusion
In conclusion, the Load Moment Indicator is a crucial element in ensuring the safety of crane operations. By preventing overloads and providing real-time data to operators, LMI significantly reduces the risk of accidents, contributing to safer and more efficient worksites.
FAQs
- What is the primary function of a Load Moment Indicator?
- The primary function of an LMI is to monitor the load and moment on a crane in real-time, preventing overloads and enhancing safety.
- How often should LMI systems be recalibrated?
- LMI systems should be recalibrated regularly, following manufacturer guidelines, to maintain accuracy and reliability.
- Are there any specific industries where LMI is mandatory?
- While requirements may vary, industries such as construction and oil and gas often mandate the use of LMIs for crane safety.
- Can LMI be retrofitted to older crane models?
- Yes, LMI systems can often be retrofitted to older crane models, providing an upgrade to enhance safety features.
- How does LMI contribute to overall worksite safety?
- LMI contributes to worksite safety by preventing overloads, reducing the risk of accidents, and promoting efficient crane operations.