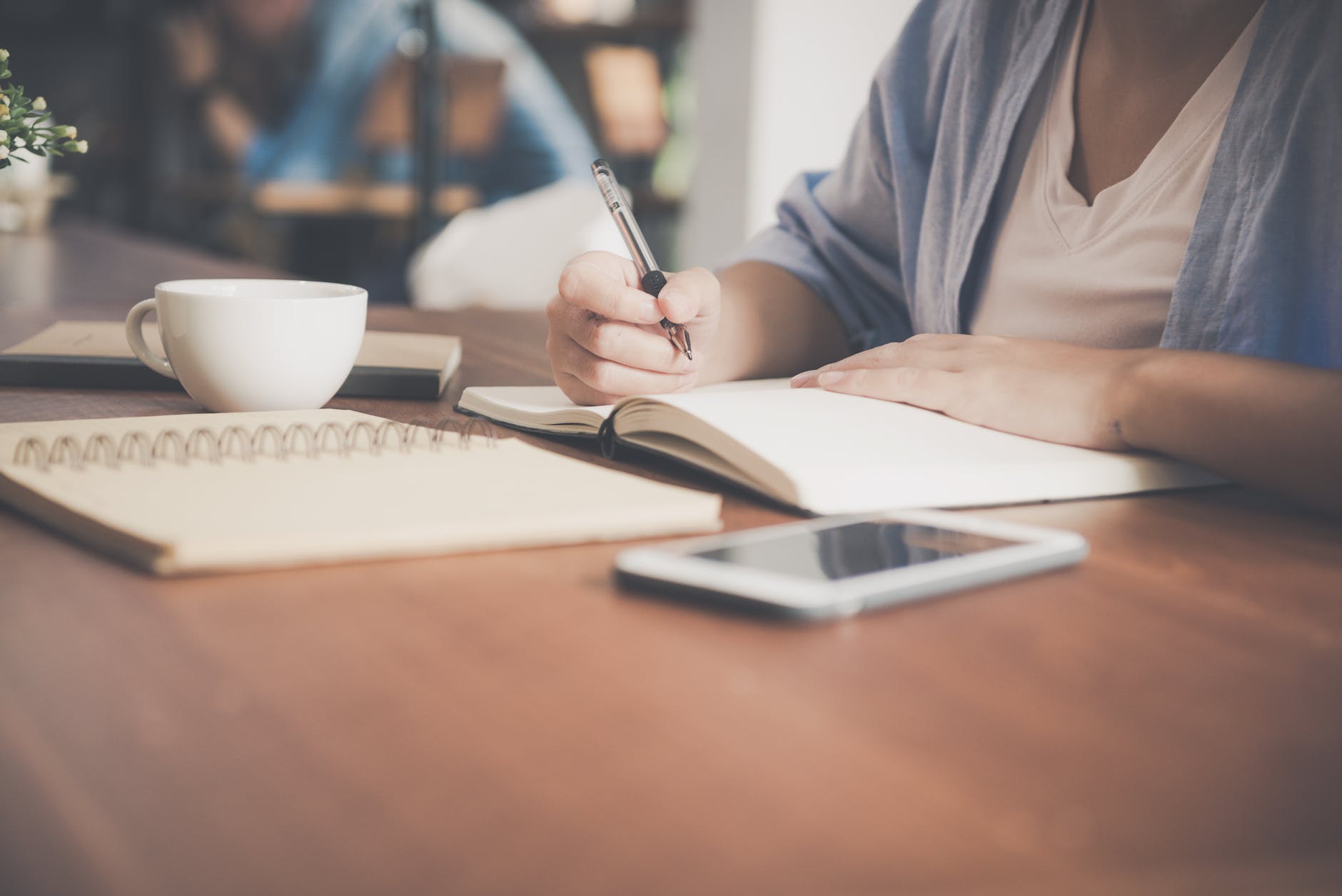
Root Cause Analysis Methods: Unveiling the Essence of Effective Problem Solving
In the dynamic landscape of business and operations, challenges are inevitable. The key to sustained success lies in the ability to tackle these challenges at their core. Root Cause Analysis (RCA) methods emerge as powerful tools in unraveling the essence of issues, ensuring long-term solutions rather than mere symptomatic relief.
Introduction
Root Cause Analysis, in essence, is the systematic process of identifying the underlying issues that contribute to problems. It is a proactive approach that delves beyond surface-level symptoms, aiming to eradicate issues from their roots. Effective implementation of RCA methods can lead to enhanced operational efficiency, improved quality, and increased overall organizational performance.
Common Root Cause Analysis Methods
Fishbone Diagram (Ishikawa)
The Fishbone Diagram, also known as the Ishikawa diagram, is a visual representation that categorizes potential causes of a problem to identify its root. By dissecting the issue into categories like people, process, equipment, and more, this method provides a comprehensive view.
5 Whys Technique
This method involves iteratively asking “why” to uncover the sequential causes leading to a problem. By peeling away layers of causation, the 5 Whys Technique ensures a deep understanding of the issue, facilitating targeted corrective actions.
Failure Mode and Effects Analysis (FMEA)
FMEA is a structured approach to identifying potential failure modes in a system and assessing their impact. By assigning severity, occurrence, and detection ratings to each failure mode, organizations can prioritize and address issues systematically.
Fault Tree Analysis (FTA)
FTA is a top-down, deductive failure analysis method that visually represents the relationship between a specific undesired event and its contributing factors. It is particularly effective in high-risk industries where a comprehensive understanding of potential failures is crucial.
Choosing the Right Method
Selecting the appropriate RCA method is pivotal to success. Factors such as the nature of the problem, available data, and the organizational context play a crucial role. Tailoring methods to suit the specific situation enhances the effectiveness of the analysis.
Fishbone Diagram (Ishikawa)
Explanation of the Method
The Fishbone Diagram begins with a problem statement, represented as the “fish’s head.” The spine and branches categorize potential causes, such as equipment, people, process, environment, and materials. Each branch is further detailed to identify specific causes contributing to the problem.
How to Create a Fishbone Diagram
- Start with a clear problem statement.
- Draw a horizontal line (the spine) with the problem statement at one end.
- Branch out categories (bones) such as people, process, equipment, etc.
- Identify and list specific causes under each category.
- Analyze and prioritize causes to determine the root cause.
Real-life Examples
In a manufacturing setting, a delay in production is analyzed using a Fishbone Diagram. Causes may include machine breakdowns (equipment), insufficient training (people), or inadequate raw materials (materials). This method visually links these factors to the core issue.
5 Whys Technique
Overview of the Method
The 5 Whys Technique, rooted in the simple act of asking “why” repeatedly, peels away layers of causation. Starting with the problem, each subsequent “why” prompts an exploration of deeper causes until the root cause is identified.
Application in Different Scenarios
In IT, when faced with system downtime, asking “why” may lead to discovering that a server failed. Further questioning may reveal insufficient cooling as the root cause. This method unveils the layers of causation leading to the ultimate issue.
Limitations and Tips for Effective Use
While powerful, the 5 Whys Technique may oversimplify complex issues. It is crucial to balance it with other methods for a comprehensive analysis. Additionally, involving diverse perspectives during the process enhances its effectiveness.
Failure Mode and Effects Analysis (FMEA)
Understanding FMEA
FMEA is a proactive approach to identifying and addressing potential failures before they occur. It involves evaluating the severity, occurrence, and detectability of each failure mode, assigning ratings to prioritize corrective actions.
Steps Involved in FMEA
- Identify potential failure modes.
- Assess the severity, occurrence, and detection ratings for each mode.
- Calculate the Risk Priority Number (RPN) by multiplying the ratings.
- Prioritize corrective actions based on RPN.
- Implement and monitor changes.
Case Studies Illustrating FMEA
In healthcare, FMEA is applied to surgical procedures. Identifying potential failure modes such as miscommunication among surgical staff, the severity of the issue is assessed. By implementing communication protocols, the occurrence of such failures is minimized.
Fault Tree Analysis (FTA)
Insight into FTA
FTA starts with an undesired event, represented as the “top event.” It then maps the potential causes and contributing factors, branching down to detailed levels. This method is particularly effective in industries where understanding complex system interactions is crucial.
Building a Fault Tree
- Define the top event (undesired outcome).
- Identify contributing factors and draw branches.
- Break down branches into sub-events until specific causes are reached.
- Analyze the fault tree to identify critical points.
Instances Where FTA Is Most Effective
In aviation, FTA is employed to analyze accidents. The top event may be a plane crash, with contributing factors branching into areas like pilot error, mechanical failure, or adverse weather conditions. This detailed analysis aids in developing preventive measures.
Combining Methods for Comprehensive Analysis
Synergizing multiple RCA methods enhances the accuracy and depth of the analysis. While Fishbone Diagrams, 5 Whys, FMEA, and FTA each offer unique perspectives, their combination provides a more holistic understanding of complex issues.
Real-world Applications
Success stories abound where organizations have successfully implemented RCA methods to address challenges. From reducing downtime in manufacturing to improving patient safety in healthcare, these methods prove invaluable in diverse settings.
Challenges in Root Cause Analysis
Identifying and overcoming obstacles in the RCA process is crucial. Whether dealing with complex system interactions or resistance to change, strategies must be in place to navigate challenges and ensure effective problem-solving.
Continuous Improvement Through RCA
Integrating RCA into the organizational culture fosters a proactive approach to problem-solving. By consistently applying these methods, organizations can create a culture of continuous improvement, staying ahead of potential issues.
Training and Skill Development
To ensure the effective application of RCA methods, training teams in the intricacies of these techniques is essential. Developing RCA skills among employees creates a pool of problem-solvers capable of driving sustainable improvement.
Monitoring and Evaluation
Establishing metrics for success and regularly reviewing the effectiveness of implemented corrective actions is crucial. Continuous monitoring ensures that organizations remain agile in addressing emerging challenges.
Future Trends in Root Cause Analysis
As technology evolves, so do RCA methodologies. Emerging trends include the integration of artificial intelligence in data analysis and the development of more sophisticated modeling techniques. Organizations need to stay abreast of these trends for continued effectiveness.
Conclusion
In the pursuit of operational excellence, Root Cause Analysis methods stand as beacons of problem-solving. By going beyond surface-level issues and digging deep into the core of challenges, organizations can create lasting solutions, fostering a culture of continuous improvement.
FAQs (Frequently Asked Questions)
- What is the primary goal of Root Cause Analysis?
- The primary goal is to identify and address the underlying causes of problems rather than just treating symptoms.
- How do organizations choose the right RCA method?
- Organizations consider factors like the nature of the problem, available data, and organizational context to choose the most suitable RCA method.
- Can RCA methods be used in any industry?
- Yes, RCA methods are versatile and can be applied in various industries, from manufacturing to healthcare and beyond.
- Is it necessary to combine multiple RCA methods for analysis?
- While not mandatory, combining methods such as Fishbone Diagrams, 5 Whys, FMEA, and FTA can provide a more comprehensive understanding of complex issues.
- What role does training play in the success of RCA implementation?
- Training is crucial for ensuring teams possess the necessary skills to effectively apply RCA methods, leading to successful implementation.