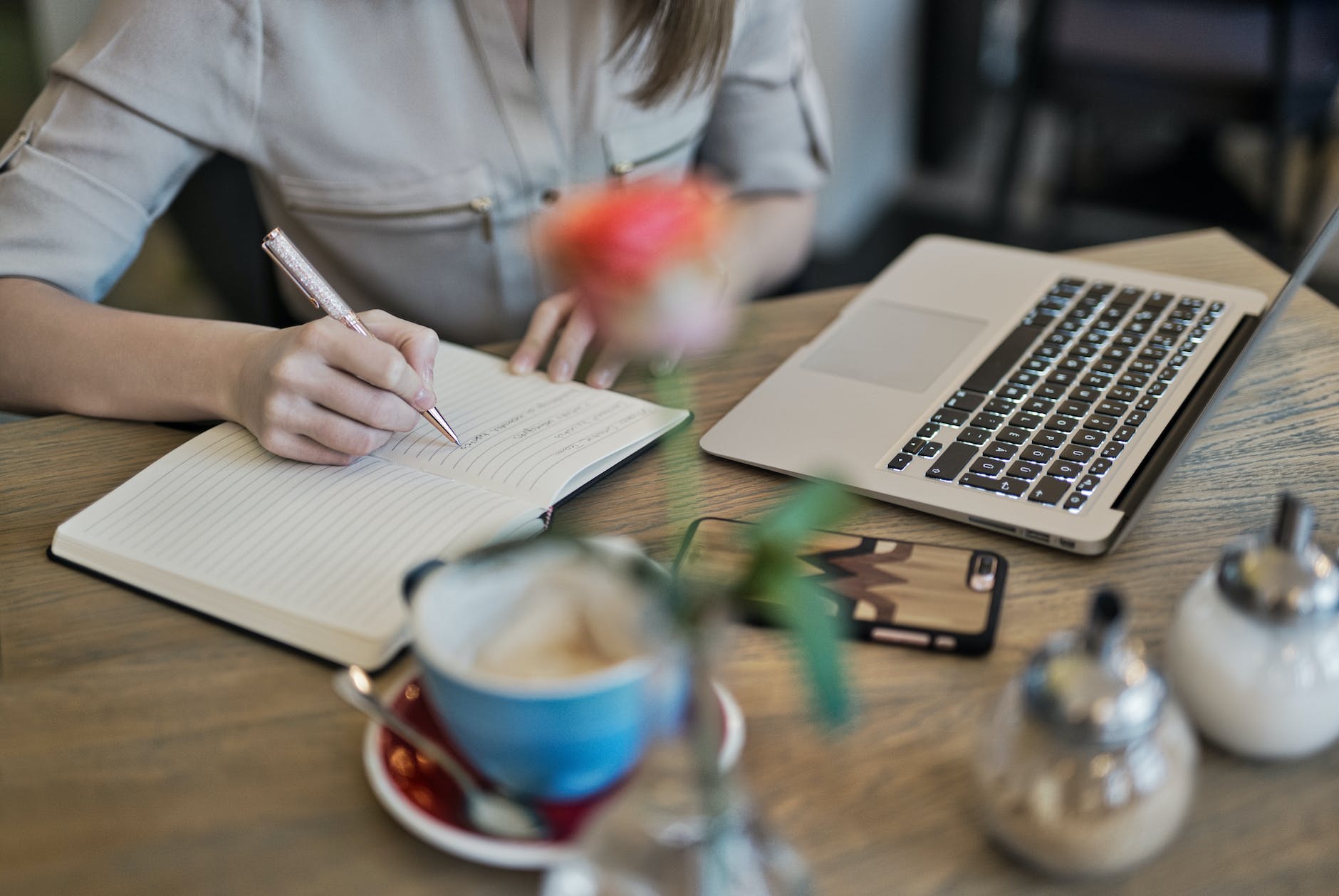
Root Cause Analysis Tools in Six Sigma: Unveiling the Secrets to Effective Problem Solving
Root Cause Analysis (RCA) stands at the core of problem-solving methodologies, and when coupled with Six Sigma, it becomes a powerful tool for organizations striving for excellence. In this article, we will delve into the intricacies of root cause analysis tools within the context of Six Sigma, exploring their applications, benefits, and the key to successful implementation.
Understanding Six Sigma Methodology
Six Sigma is a data-driven methodology designed to improve business processes by removing defects and minimizing variations. It focuses on achieving consistent, high-quality results by identifying and eliminating the root causes of problems.
The Role of Root Cause Analysis in Six Sigma
Root Cause Analysis plays a pivotal role in the Six Sigma methodology. By dissecting complex issues and uncovering their underlying causes, organizations can make informed decisions and implement effective solutions, contributing to continuous improvement.
Common Challenges in Root Cause Analysis
However, the journey of Root Cause Analysis is not without challenges. Inaccurate data, vague problem definitions, and lack of collaboration among team members can hinder the process. Overcoming these challenges is essential for successful RCA implementation.
Overview of Root Cause Analysis Tools
Various tools assist in uncovering the root causes of problems. Three widely used tools in Six Sigma are the Fishbone diagram, 5 Whys, and Pareto Analysis. Let’s explore each of them in detail.
Application of Fishbone Diagram in RCA
The Fishbone diagram, also known as the Ishikawa diagram, visually represents the potential causes of a problem. Its structured approach aids teams in identifying and categorizing factors contributing to an issue.
To create a Fishbone diagram, the team first defines the problem at the “fish’s head” and then categorizes potential causes into branches representing different factors. For instance, in a manufacturing scenario, branches could include materials, machines, methods, manpower, and measurements.
Real-world examples abound where Fishbone diagrams have been instrumental in unraveling complex issues. For instance, a manufacturing plant experiencing a surge in defective products used a Fishbone diagram to trace the problem back to a malfunctioning machine, leading to swift corrective action.
Utilizing 5 Whys for Root Cause Analysis
The 5 Whys technique is a straightforward yet powerful approach. It involves asking “why” repeatedly to drill down to the fundamental cause of a problem. Each answer leads to another “why” until the root cause is identified.
This method’s strength lies in its simplicity, as it encourages teams to explore the deeper layers of an issue. Case studies show that asking “why” five times often unveils the root cause, facilitating targeted corrective actions.
Pareto Analysis in Six Sigma RCA
Pareto Analysis, based on the 80/20 rule, prioritizes factors contributing to a problem. It helps teams focus their efforts on addressing the most significant issues first, maximizing the impact of interventions.
Integrating Pareto Analysis into RCA involves identifying and categorizing problems, determining their frequency, and prioritizing them based on their impact. This allows teams to allocate resources efficiently and address the most critical issues upfront.
Benefits of Implementing Root Cause Analysis in Six Sigma
The integration of Root Cause Analysis into Six Sigma yields numerous benefits. It enhances problem-solving efficiency, reduces the recurrence of issues, and contributes to overall process optimization.
Organizations leveraging RCA within the Six Sigma framework witness improved product quality, increased customer satisfaction, and streamlined operations. The holistic approach of addressing root causes ensures sustained improvements and long-term success.
Selecting the Right Root Cause Analysis Tool
Choosing the appropriate tool for Root Cause Analysis is crucial. Different tools are suitable for different problems, and considering factors such as the team’s expertise and the project’s requirements is essential.
While Fishbone diagrams are ideal for visualizing complex issues, the 5 Whys technique is effective for drilling down to the root cause. Pareto Analysis, on the other hand, aids in prioritizing actions based on their impact.
Best Practices for Successful Root Cause Analysis
Successful Root Cause Analysis relies on adhering to best practices. Thorough data collection, involving cross-functional teams, and fostering a continuous improvement mindset are essential components.
Common Misconceptions about Root Cause Analysis in Six Sigma
Despite its effectiveness, Root Cause Analysis is sometimes surrounded by misconceptions. Addressing these myths is crucial to ensuring its proper implementation. One common misconception is that RCA is time-consuming and resource-intensive. In reality, the investment in RCA pays off by preventing recurring issues and optimizing processes.
Root Cause Analysis (RCA) is a critical component of the Six Sigma methodology, aimed at identifying and addressing the underlying causes of process defects or problems. Several tools are commonly used in Six Sigma for effective root cause analysis. Here are some key tools:
- Ishikawa Diagram (Fishbone Diagram):
- This visual tool helps to identify possible causes of a problem by categorizing them into specific branches, such as people, process, equipment, materials, and environment. It encourages a systematic exploration of potential root causes.
- 5 Whys:
- This technique involves asking “Why” repeatedly (typically five times) to drill down into the root cause of a problem. It helps in uncovering deeper layers of causation beyond the obvious symptoms.
- Pareto Analysis:
- Based on the Pareto Principle (80/20 rule), this tool helps prioritize potential causes by focusing on the most significant factors contributing to the problem. It aids in allocating resources to address the most critical issues first.
- Failure Mode and Effects Analysis (FMEA):
- FMEA is a systematic method for evaluating processes to identify where and how they might fail and assessing the relative impact of different failures. It prioritizes areas for improvement based on severity, occurrence, and detection.
- Control Charts:
- Control charts help in monitoring and controlling process variations over time. Sudden shifts or trends in the data may indicate potential root causes that need further investigation.
- Statistical Analysis:
- Tools such as hypothesis testing, regression analysis, and design of experiments (DOE) are employed for statistical validation of potential root causes. Statistical methods provide a rigorous and objective approach to identifying significant factors.
- Scatter Diagrams:
- These diagrams help visualize the relationship between two variables. Identifying patterns or correlations can lead to insights into potential root causes.
- Process Mapping:
- Creating a visual representation of the process flow can reveal inefficiencies, bottlenecks, or areas prone to errors. It aids in understanding the entire process and identifying potential points of failure.
- Histograms:
- Histograms display the distribution of a set of data. They are useful for identifying patterns, trends, and variations within a process, which can point towards potential root causes.
- Affinity Diagrams:
- This tool is helpful for organizing and categorizing large amounts of data or ideas. It can be used to identify patterns and relationships, assisting in the identification of potential root causes.
Using a combination of these tools in a systematic and disciplined manner enhances the effectiveness of root cause analysis within the Six Sigma framework. It promotes a data-driven and evidence-based approach to problem-solving.
Conclusion
In conclusion, Root Cause Analysis is a cornerstone of Six Sigma, offering a systematic approach to identifying and addressing the underlying causes of problems. By employing tools like Fishbone diagrams, 5 Whys, and Pareto Analysis, organizations can enhance their problem-solving capabilities and achieve sustained improvements.
As we look to the future, the integration of advanced technologies into Root Cause Analysis will further elevate its effectiveness. Embracing RCA within the Six Sigma framework is not just a best practice but a strategic imperative for organizations aiming for operational excellence.
Frequently Asked Questions (FAQs)
- Q: Is Root Cause Analysis applicable only in manufacturing industries?
- A: No, Root Cause Analysis is applicable across various industries, including healthcare, finance, and services, where identifying and addressing the root causes of problems is essential for continuous improvement.
- Q: How long does it typically take to conduct a Root Cause Analysis using the 5 Whys method?
- A: The duration of a 5 Whys analysis depends on the complexity of the problem. It can range from a few minutes for simple issues to several hours for more intricate challenges.
- Q: Are there any specific skills required to lead a Root Cause Analysis team?
- A: Effective leadership, problem-solving skills, and the ability to facilitate collaboration are crucial for leading a successful Root Cause Analysis team.
- Q: Can Root Cause Analysis tools be used for proactive problem prevention?
- A: Yes, Root Cause Analysis tools are not only reactive but can also be applied proactively to identify potential issues before they escalate.
- Q: How often should organizations conduct Root Cause Analysis to ensure continuous improvement?
- A: The frequency of Root Cause Analysis depends on the organization’s goals and the nature of its operations. Regular analyses, especially after significant incidents, contribute to ongoing improvement.