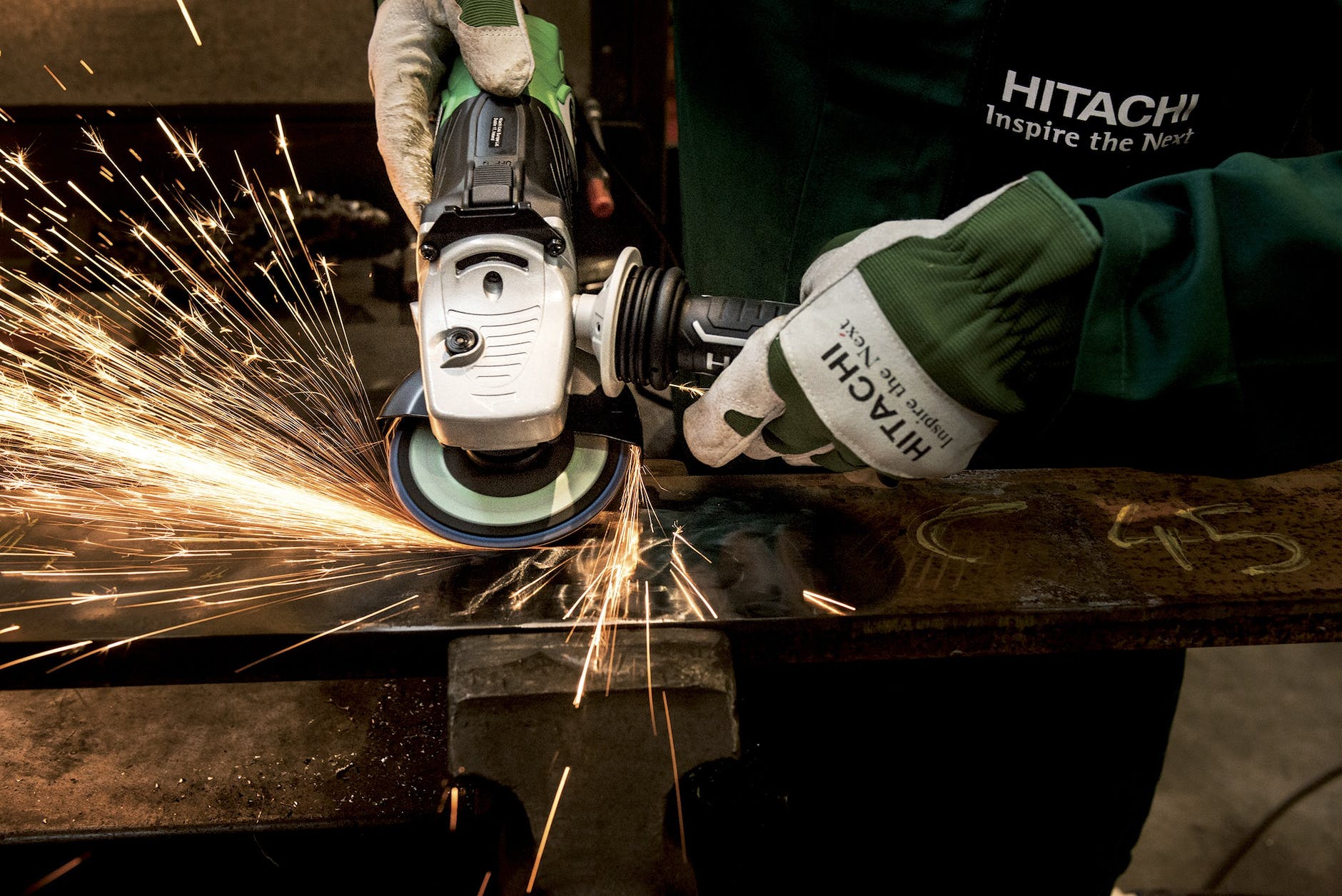
Safe Operating Procedures for Power Tools
Safe Operating Procedures for Power Tools : Operating power tools requires strict adherence to safety protocols to prevent accidents and ensure the well-being of users. Here is a detailed guide to safe operating procedures:
1. Training and Familiarization
- Training Programs: Provide comprehensive training to users on the specific power tool they will operate, emphasizing safety measures and proper handling.
- Understanding Equipment: Familiarize users with the functions, controls, and safety features of each power tool before operation.
2. Personal Protective Equipment (PPE)
- Mandatory PPE: Require the use of appropriate PPE, including safety goggles, hearing protection, gloves, and appropriate footwear, as recommended for each power tool.
- Respiratory Protection: Use respiratory protection, such as dust masks, when working with tools generating airborne particles.
3. Workspace Preparation
- Clear Workspace: Ensure the work area is clean, organized, and free from clutter to prevent tripping hazards.
- Adequate Lighting: Ensure proper lighting to facilitate safe and accurate operation of power tools.
4. Machine Inspection and Maintenance
- Pre-Use Inspection: Conduct a thorough inspection of each power tool before use, checking for any damage, loose parts, or malfunctioning components.
- Regular Maintenance: Follow manufacturer guidelines for maintenance schedules to keep tools in optimal working condition.
5. Electrical Safety Measures
- Grounding and Plugs: Ensure power tools are properly grounded, and use three-prong plugs to prevent electrical shocks.
- Cord Management: Keep power cords away from sharp edges, heat sources, or water to avoid damage.
6. Safe Tool Handling
- Proper Grip: Hold power tools firmly with both hands and maintain a secure grip to prevent accidental slippage.
- Use Correct Attachments: Ensure the use of appropriate accessories and attachments recommended for each specific power tool.
7. Start-Up and Operation
- Safe Start-Up: Check the power tool’s switch or trigger before starting, and never force a tool that is jammed or not functioning correctly.
- Stable Operation: Maintain a stable stance and balance while operating power tools to control movements effectively.
8. Material Handling and Work Techniques
- Secure Workpieces: Secure materials properly before working on them to prevent movement or slippage during operation.
- Safe Cutting Techniques: Use steady and controlled movements, keeping hands and fingers away from cutting areas.
9. Emergency Response Procedures
- Emergency Stop: Know the location of the tool’s emergency stop and how to use it in case of an emergency.
- First-Aid Kit: Keep a well-equipped first-aid kit accessible in case of minor injuries.
10. Post-Use Procedures
- Tool Shutdown: Turn off the power tool and unplug it after use, and store it in a safe and designated place.
- Clean-Up: Remove debris and dust from the work area and inspect tools for any damage or issues post-operation.
11. Continuous Improvement
- Feedback and Training Updates: Encourage user feedback to improve safety protocols and update training programs regularly to incorporate new safety measures or equipment.
Conclusion
Adhering to these safe operating procedures for power tools significantly reduces the risk of accidents, ensuring the safety of users and those around them.
Safe Operating Procedure for Bar Bending Machine
Safe Operating Procedure for Working at Height
Safe Operating Procedure (SOP)
7 Types of Permit To Work (PTW)
FAQs
- Why is PPE crucial when using power tools? PPE protects users from potential hazards, such as flying debris, noise, and electrical shocks.
- How should users respond in case of a malfunctioning power tool? Stop using the tool immediately, unplug it, and report the issue to the supervisor or maintenance personnel.
- What should be checked during pre-use inspection of power tools? Check for damage, loose parts, frayed cords, and ensure all safety features are operational.
- Why is workspace preparation essential when using power tools? A well-prepared workspace reduces the risk of accidents and enhances user efficiency and accuracy.
- What actions should be taken in case of an emergency while using power tools? Immediately stop the tool, use emergency stops if available, and seek help if needed.