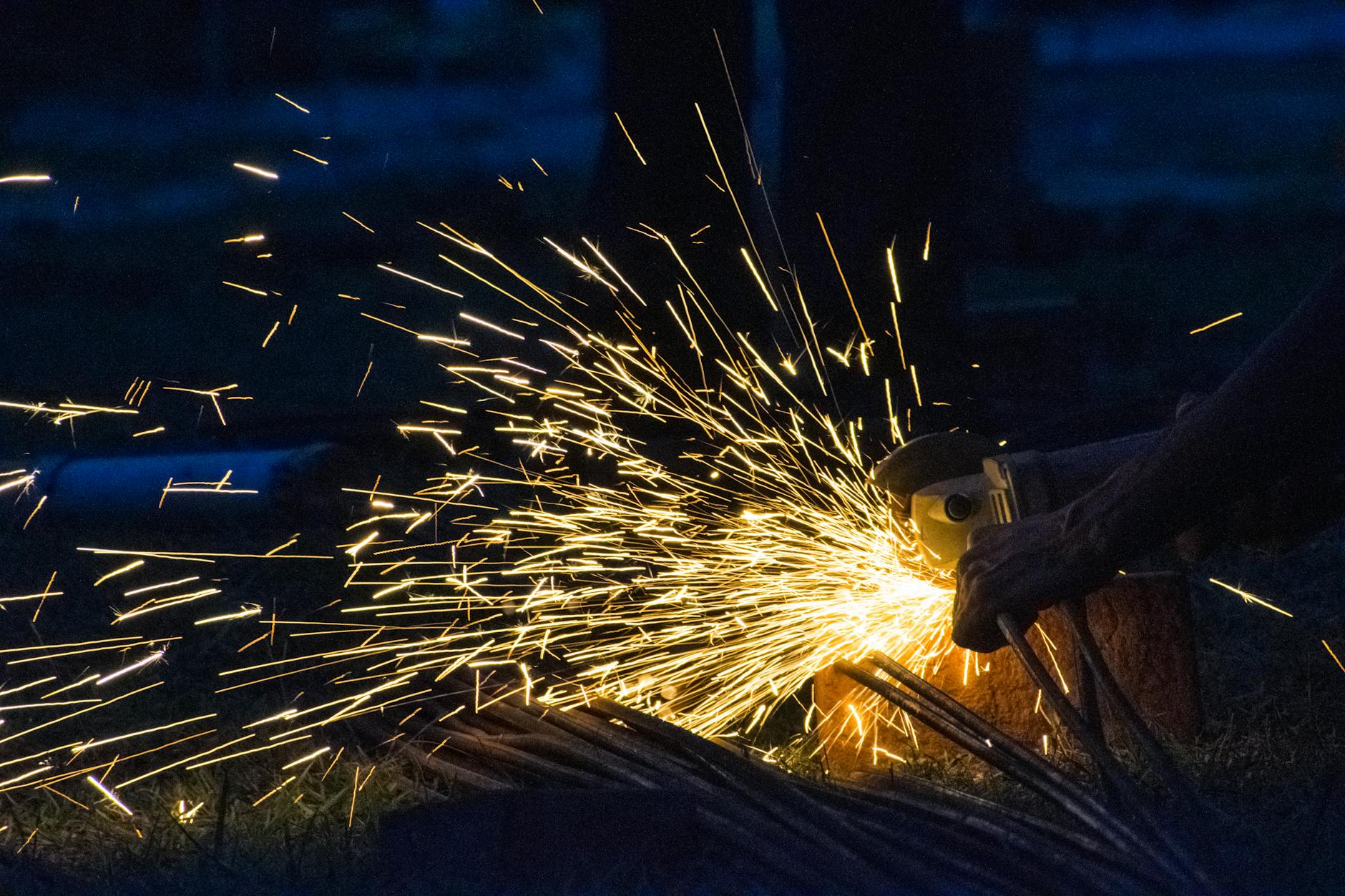
Safe Operating Procedures for Welding and Cutting
Safe Operating Procedures for Welding and Cutting : Welding and cutting operations demand strict adherence to safety protocols to prevent accidents and ensure the well-being of operators. Here is a comprehensive guide to safe operating procedures:
1. Training and Certification
- Comprehensive Training: Provide thorough training to operators on welding and cutting techniques, equipment operation, and safety measures.
- Certification: Ensure operators possess relevant certifications for the specific welding and cutting tasks they will perform.
2. Personal Protective Equipment (PPE)
- Mandatory PPE: Mandate the use of appropriate PPE, including welding helmets with protective lenses, flame-resistant clothing, gloves, and closed-toe shoes.
- Respiratory Protection: Utilize respiratory protection, such as dust masks or respirators, when working in environments with fumes or airborne particles.
3. Work Area Preparation
- Clear Workspaces: Ensure the work area is clutter-free, well-ventilated, and free from flammable materials to prevent fire hazards.
- Secure Surroundings: Establish barriers or warning signs to prevent unauthorized access to the welding and cutting areas.
4. Machine Setup and Inspection
- Pre-Operational Check: Inspect welding and cutting equipment for any damage, gas leaks, or worn-out parts before operation.
- Secure Gas Cylinders: Properly secure and store gas cylinders, ensuring they are upright and chained to prevent tipping.
5. Electrical and Gas Safety Measures
- Proper Grounding: Ensure welding and cutting equipment is correctly grounded to prevent electric shock hazards.
- Gas Leak Checks: Perform regular checks for gas leaks and ensure proper ventilation to prevent the accumulation of flammable gases.
6. Safe Welding and Cutting Techniques
- Positioning: Maintain a stable posture and use proper body positioning during welding and cutting to prevent strains or injuries.
- Controlled Techniques: Utilize controlled techniques to manage the welding or cutting arc effectively.
7. Fire Prevention and Control
- Fire Extinguishers: Keep appropriate fire extinguishing equipment nearby, and train operators on their use.
- Hot Work Permits: Obtain necessary permits for hot work, especially in industrial settings, to prevent fire hazards.
8. Post-Operation Procedures
- Cooling Period: Allow welded or cut materials to cool before handling to avoid burns or accidents.
- Inspection: Inspect the finished work for quality and structural integrity, and properly store equipment after use.
9. Emergency Response Protocols
- Emergency Plan: Establish clear procedures for responding to accidents, injuries, or equipment malfunctions.
- Emergency Contacts: Display emergency contact information prominently in the work area.
10. Continuous Improvement
- Feedback and Evaluation: Encourage feedback from operators to improve safety protocols continually.
- Training Updates: Regularly update training programs to incorporate new safety measures or equipment.
Conclusion
Adhering to these safe operating procedures for welding and cutting significantly reduces the risk of accidents, ensuring the safety of operators and those working in the vicinity.
Safe Operating Procedures for Machinery
Safe Operating Procedure for Bar Bending Machine
Safe Operating Procedure for Working at Height
Safe Operating Procedure (SOP)
7 Types of Permit To Work (PTW)
FAQs
- Why is PPE crucial when welding and cutting? PPE protects operators from sparks, radiation, and potential hazards associated with welding and cutting processes.
- How should operators respond to a gas leak during welding? Immediately cease operations, evacuate the area, and report the leak to supervisory personnel.
- What should be checked during the pre-operational inspection of welding equipment? Check for damage, gas leaks, and the condition of welding cables, ensuring all safety features are operational.
- Why is work area preparation essential for welding and cutting tasks? A well-prepared work area reduces the risk of accidents, fire hazards, and enhances overall safety.
- How often should operators inspect their welding and cutting equipment? Regular inspections before each use and routine maintenance checks are recommended to ensure equipment safety.