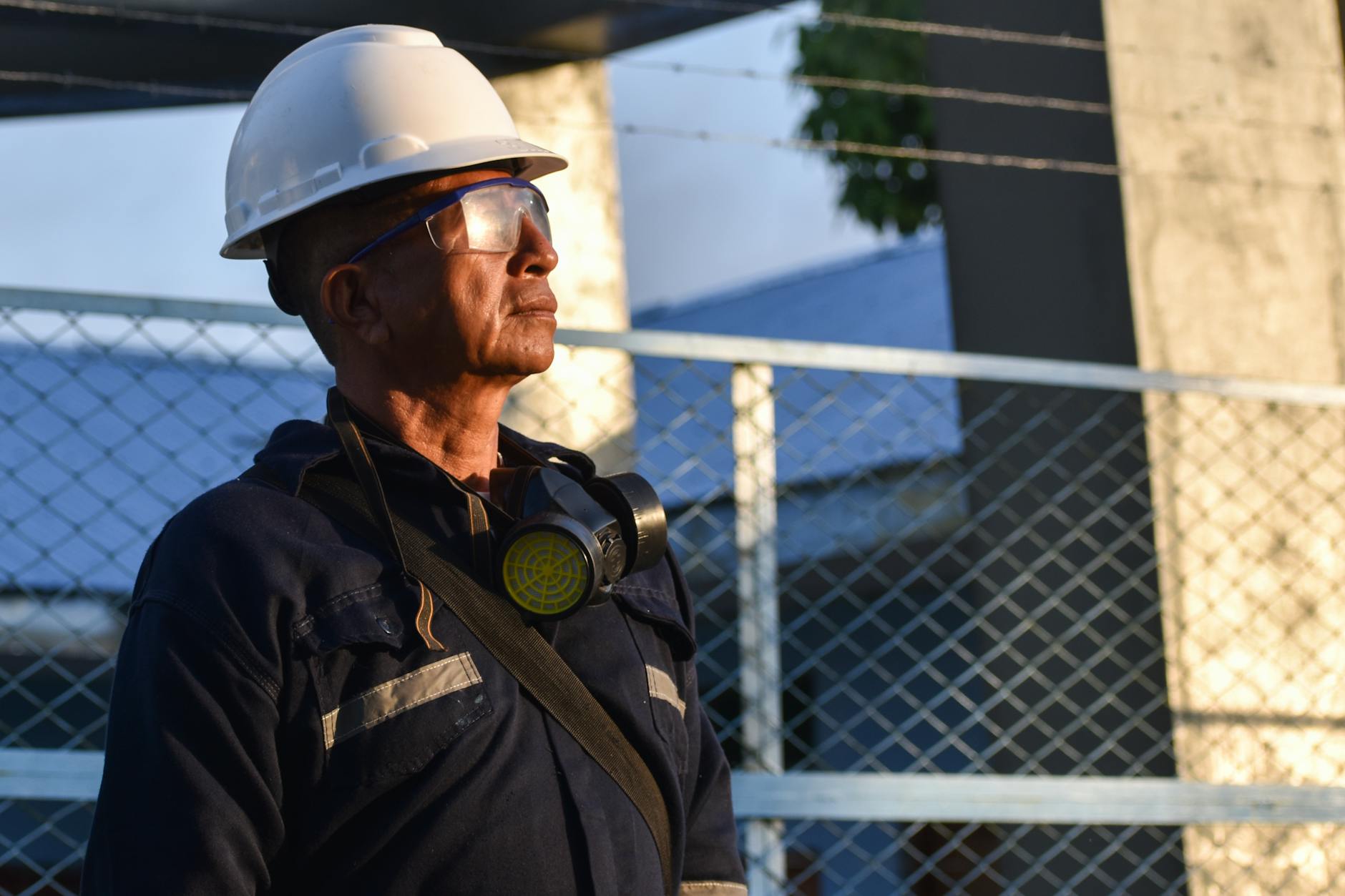
Safety Kaizen | Download PPT
In today’s rapidly evolving industrial landscape, ensuring workplace safety is not just a legal requirement but also a moral obligation for organizations. Safety Kaizen, a concept rooted in the principles of continuous improvement, has emerged as a powerful strategy to enhance safety standards in various industries. In this article, we delve into the concept of Safety Kaizen, its significance, implementation strategies, benefits, challenges, and real-life examples.
Introduction to Safety Kaizen
Safety Kaizen is a methodology that combines the principles of safety management with the philosophy of Kaizen, which originated in Japan and emphasizes continuous improvement. It entails making incremental changes to safety processes, procedures, and behaviors to achieve a safer work environment.
Understanding Kaizen Principles
Definition of Kaizen
Kaizen, derived from the Japanese words “kai” (change) and “zen” (good), refers to the practice of making continuous improvements in processes and systems.
Importance of Continuous Improvement
Kaizen emphasizes the importance of small, incremental changes over time, rather than large, sporadic improvements. It fosters a culture of ongoing refinement and innovation, leading to sustainable growth and efficiency.
The Integration of Safety and Kaizen
Why Safety is Paramount
Safety is a fundamental aspect of any workplace, safeguarding employees from accidents, injuries, and occupational hazards. Prioritizing safety not only protects human lives but also preserves organizational reputation and productivity.
Implementing Kaizen in Safety Processes
By integrating Kaizen principles into safety management systems, organizations can foster a proactive approach to safety improvement. This involves identifying potential hazards, analyzing root causes, and implementing preventive measures in an iterative manner.
Benefits of Safety Kaizen
Improved Safety Culture
Safety Kaizen fosters a culture of continuous learning and improvement, where employees are encouraged to actively participate in identifying safety issues and proposing solutions. This collaborative approach enhances employee engagement, morale, and commitment to safety.
Reduction in Accidents and Injuries
Implementing Safety Kaizen leads to a significant reduction in workplace accidents and injuries. By systematically addressing safety concerns and implementing preventive measures, organizations can create safer work environments and protect their most valuable assets—their employees.
Steps to Implement Safety Kaizen
Conducting Safety Assessments
The first step in implementing Safety Kaizen is to conduct comprehensive safety assessments to identify existing hazards and areas for improvement. This may involve inspecting work areas, analyzing incident reports, and soliciting feedback from employees.
Involving Employees in Safety Improvement
Engaging employees at all levels is crucial for the success of Safety Kaizen initiatives. Organizations should empower employees to participate in safety improvement efforts by providing training, resources, and incentives for proactive safety behaviors.
Regular Reviews and Adjustments
Safety Kaizen is an ongoing process that requires regular reviews and adjustments. Organizations should establish mechanisms for monitoring safety performance, collecting feedback, and making necessary modifications to safety processes and procedures.
Challenges in Implementing Safety Kaizen
Resistance to Change
One of the primary challenges in implementing Safety Kaizen is resistance to change. Employees may be hesitant to adopt new safety practices or may perceive Kaizen initiatives as additional burdens on their workload.
Resource Constraints
Limited resources, such as time, budget, and expertise, can pose significant barriers to implementing Safety Kaizen effectively. Organizations must allocate adequate resources and support to sustain continuous improvement efforts.
Overcoming Challenges and Sustaining Safety Kaizen Initiatives
To overcome resistance to change, organizations should invest in comprehensive training and communication strategies to educate employees about the benefits of Safety Kaizen and involve them in decision-making processes. Additionally, fostering a supportive work environment that encourages innovation and experimentation can help overcome resource constraints and sustain Safety Kaizen initiatives in the long term.
Kaizen Safety for Construction
Kaizen, a Japanese term meaning "continuous improvement," is a philosophy that can be effectively applied to enhance safety practices in the construction industry. By integrating Kaizen principles into safety management systems, construction companies can create a culture of safety excellence and reduce the risk of accidents and injuries on job sites.
Here are some key strategies for implementing Kaizen Safety in construction:
- Employee Involvement: Encourage active participation from all levels of the organization, from management to frontline workers, in identifying safety hazards and suggesting improvements. Workers are often the ones most familiar with potential risks and can provide valuable insights into developing safer work procedures.
- Regular Training and Education: Provide ongoing safety training and education to all employees to ensure they are aware of best practices, regulations, and potential hazards associated with their tasks. Continuous learning ensures that workers remain vigilant and proactive in maintaining a safe work environment.
- Visual Management: Utilize visual cues such as signage, color coding, and safety markings to clearly communicate safety protocols and hazards throughout the construction site. Visual management tools help reinforce safe behaviors and remind workers to stay alert and compliant with safety procedures.
- Standardization of Processes: Establish standardized processes and procedures for common tasks to streamline operations and minimize the potential for errors or accidents. Clearly documented protocols ensure consistency and provide a framework for continuous improvement efforts.
- Root Cause Analysis: Conduct thorough investigations into the root causes of accidents, near misses, and safety incidents to identify underlying issues and prevent recurrence. By addressing the underlying causes rather than just the symptoms, construction companies can implement more effective corrective actions and prevent future incidents.
- Continuous Monitoring and Feedback: Implement systems for ongoing monitoring of safety performance and provide regular feedback to employees on their safety practices. Recognize and reward individuals and teams for their contributions to safety improvements, fostering a culture where safety is valued and prioritized.
- Kaizen Events: Organize regular Kaizen events or workshops focused specifically on safety improvement initiatives. These events bring together cross-functional teams to brainstorm ideas, develop action plans, and implement changes aimed at enhancing safety performance.
- Embrace Technology: Leverage technology such as wearables, drones, and digital safety management systems to enhance safety monitoring, data collection, and analysis. Technology can provide real-time insights into safety risks and enable proactive intervention to prevent accidents before they occur.
By integrating Kaizen principles into safety management practices, construction companies can create a safer work environment, reduce the frequency of accidents and injuries, and ultimately improve overall productivity and profitability.
Conclusion
Safety Kaizen offers a systematic approach to enhancing workplace safety through continuous improvement. By integrating Kaizen principles into safety management systems, organizations can create safer work environments, reduce accidents and injuries, and foster a culture of proactive safety improvement. Despite challenges, with commitment, collaboration, and perseverance, organizations can successfully implement and sustain Safety Kaizen initiatives to ensure the well-being of their employees and the overall success of their operations.
How To Calculate Risk Assessment | Download PPT
THE FACTORIES ACT 1948 Section 40 (B) Safety Officers | Download PPT
Scaffolding Technical Specification | Download PPT
44 HSE Interview Questions and Sample Answers | Download PDF
PSSR for Safety | Pre-Startup Safety Review (PSSR) | Download PPT
Unique FAQs
- What industries can benefit from implementing Safety Kaizen?Safety Kaizen principles are applicable across various industries, including manufacturing, construction, healthcare, and transportation, among others. Any organization that prioritizes workplace safety can benefit from adopting Safety Kaizen practices.
- How can organizations measure the effectiveness of Safety Kaizen initiatives?Organizations can measure the effectiveness of Safety Kaizen initiatives by tracking key safety performance indicators, such as incident rates, near-miss reports, and employee participation in safety improvement activities. Regular audits and feedback mechanisms also provide valuable insights into the impact of Safety Kaizen on workplace safety.
- What role do leaders play in promoting Safety Kaizen?Leaders play a crucial role in promoting Safety Kaizen by setting clear safety objectives, providing resources and support for improvement efforts, and actively participating in safety improvement initiatives. Their commitment and involvement send a strong message about the organization’s commitment to safety excellence.
- How can organizations sustain Safety Kaizen initiatives in the long term?Sustaining Safety Kaizen initiatives requires ongoing commitment from all levels of the organization. This includes fostering a culture of continuous improvement, providing regular training and reinforcement of safety practices, and allocating resources for ongoing safety improvement projects.
- What are some common pitfalls to avoid when implementing Safety Kaizen?Some common pitfalls to avoid when implementing Safety Kaizen include overlooking employee input and feedback, neglecting to allocate sufficient resources and support, and failing to address underlying cultural barriers to change. Organizations should prioritize communication, collaboration, and employee engagement to overcome these challenges and ensure the success of Safety Kaizen initiatives.