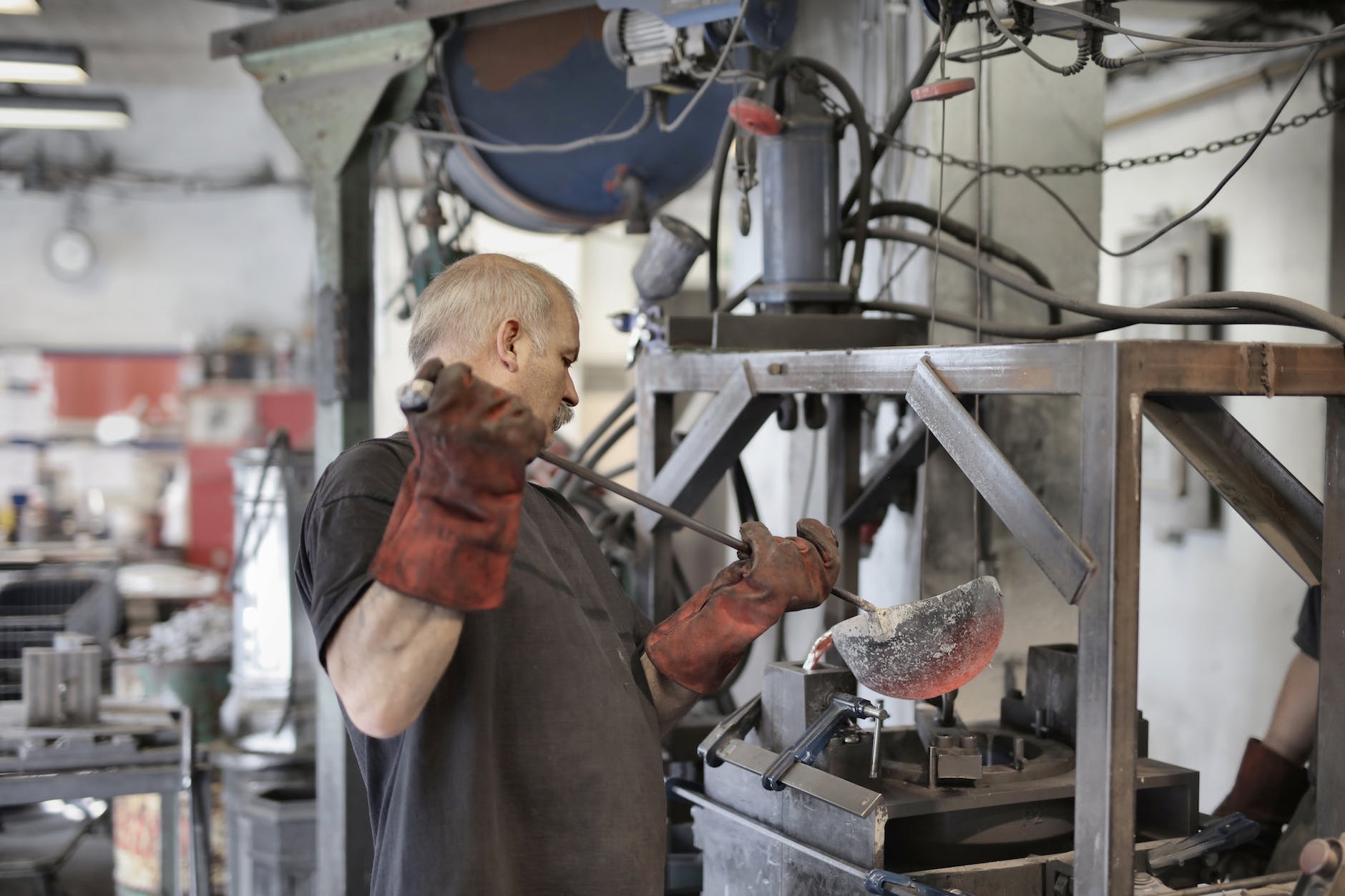
HAZOP Study for Process Industry | Download PPT
HAZOP (Hazard and Operability Study) is a systematic method used in the process industry to identify potential hazards, deviations from design intent, and operability issues in a system. It involves a team of experts analyzing each element of a process system to uncover possible deviations that could lead to hazards or operational problems.
The process typically involves the following steps:
- Selecting the Study Nodes: The system or process being analyzed is divided into nodes, which are individual sections or components. These nodes are thoroughly examined.
- Identifying Deviations: The team systematically reviews each node and considers various parameters like temperature, pressure, flow rates, etc. They then brainstorm deviations from normal operating conditions, considering both known and unforeseen scenarios.
- Determining Consequences: For each identified deviation, the team assesses the potential consequences in terms of safety, environmental impact, and operability.
- Identifying Safeguards: Safeguards and existing control measures are evaluated to determine if they adequately address the identified deviations or if additional measures are needed.
- Recording and Reporting: All findings, including deviations, consequences, and recommended actions, are documented in a HAZOP report.
- Implementing Recommendations: Once the study is complete, recommendations for mitigating identified hazards or improving operability are implemented.
The goal of a HAZOP study is to proactively identify and address potential hazards and operability issues before they can cause harm or disrupt the process. It's a critical part of ensuring safety and efficiency in industries where processes involve significant risks.
Node: Reactor
Parameter: Temperature
Normal Operating Condition: The reactor operates at 150°C.
Deviation 1: What if the temperature increases to 200°C?
Consequences: This could lead to an accelerated reaction rate, potentially causing a runaway reaction and overpressure in the reactor vessel.
Safeguard: Install an automatic temperature control system with emergency shutdown protocols to prevent overheating.
Deviation 2: What if the temperature drops to 100°C?
Consequences: A lower temperature might slow down the reaction or result in incomplete conversion of reactants, affecting product quality.
Safeguard: Implement a backup heating system or improve insulation to maintain a consistent temperature.
Node: Pressure Vessel
Parameter: Pressure
Normal Operating Condition: The vessel operates at 5 bar pressure.
Deviation 1: What if the pressure increases to 10 bar?
Consequences: Higher pressure can exceed the vessel’s design limits, leading to potential rupture or leakage.
Safeguard: Install pressure relief valves set to activate at safe pressure thresholds.
Deviation 2: What if the pressure drops to 3 bar?
Consequences: Low pressure might cause inefficient mixing or affect downstream processes.
Safeguard: Implement pressure monitoring systems and alarms to alert operators of pressure drops.
These are simplified examples, but a comprehensive HAZOP study would explore various parameters, deviations, consequences, and safeguards for each node in the process, ensuring a thorough evaluation of potential hazards and operability issues.
According to OSHA and NEBOSH: Difference Between Accident and Incident | Download PPT
Difference between JHA and JSA | Download PPT