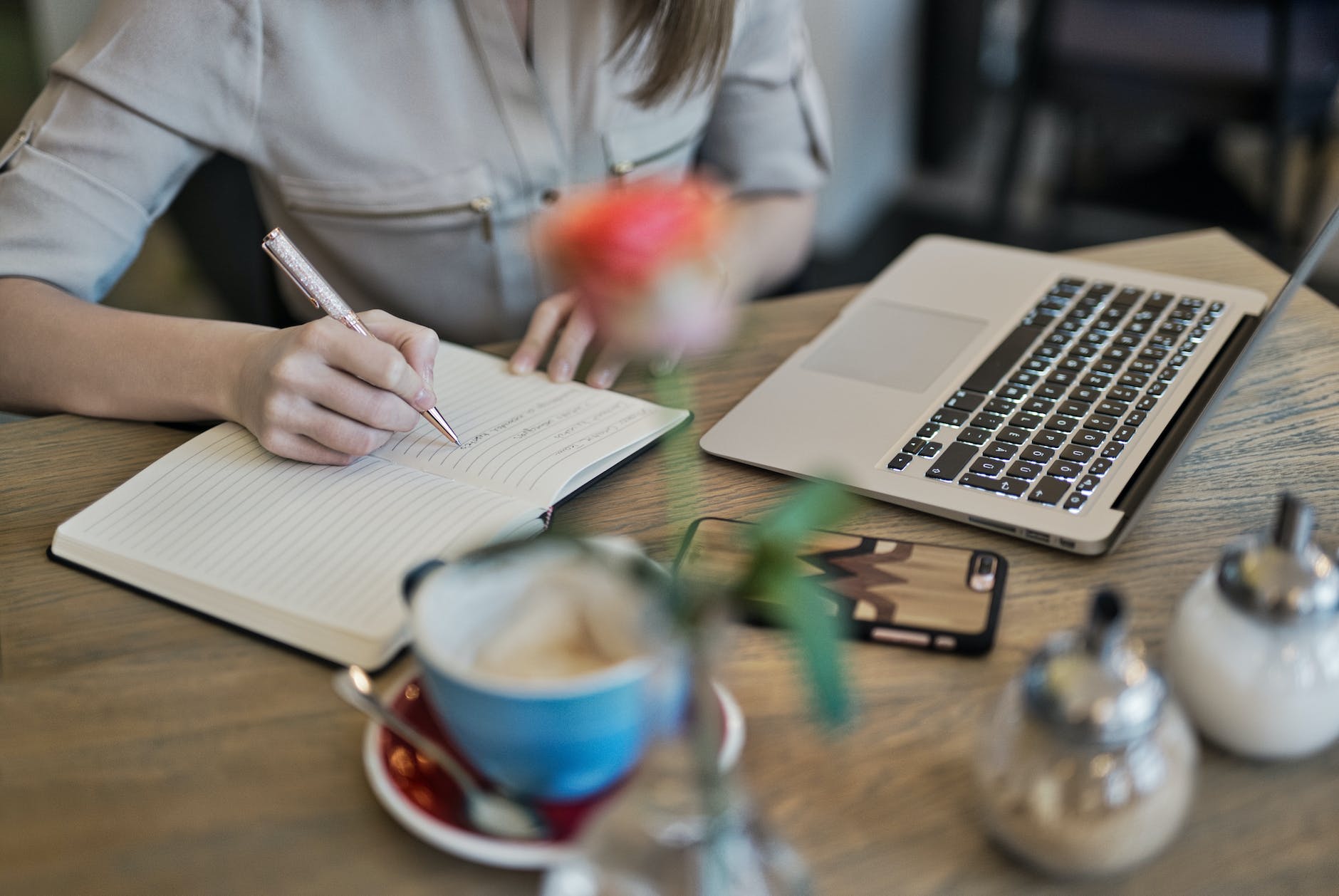
Job Safety Analysis (JSA): Identifying and Mitigating Workplace Hazards
Introduction
Job Safety Analysis (JSA), also known as Job Hazard Analysis (JHA), is a systematic process designed to identify and address potential hazards associated with specific job tasks. By breaking down each step of a job, JSA empowers organizations to implement preventive measures and ensure the safety of workers. This article explores the significance of JSA in workplace safety and provides insights into creating a secure working environment.
Understanding Job Safety Analysis
- Definition of JSA
- Systematic Assessment: JSA is a systematic approach to identify, assess, and mitigate potential hazards associated with a particular job or task.
- Proactive Safety: It emphasizes proactive safety measures to prevent accidents and injuries.
- Key Objectives of JSA
- Hazard Identification: Identify potential hazards at each step of a job.
- Risk Assessment: Assess the level of risk associated with each identified hazard.
- Preventive Measures: Implement preventive measures to eliminate or mitigate risks.
Steps in Conducting a Job Safety Analysis
- Selecting the Job or Task
- Specificity: Choose a specific job or task for analysis rather than broad job categories.
- Relevance: Prioritize jobs with a higher risk of accidents or injuries.
- Breaking Down the Job into Steps
- Detailed Analysis: Divide the selected job into individual steps, focusing on each action.
- Sequence Identification: Identify the correct sequence of steps in performing the job.
- Identifying Potential Hazards
- Equipment and Materials: Evaluate potential hazards related to tools, equipment, and materials used.
- Environmental Factors: Consider environmental factors, such as weather conditions, that may contribute to hazards.
- Assessing the Risk Level
- Likelihood and Severity: Evaluate the likelihood and severity of each identified hazard.
- Risk Matrix: Use a risk matrix to categorize risks and prioritize them based on their potential impact.
- Implementing Preventive Measures
- Engineering Controls: Modify equipment or processes to eliminate hazards.
- Administrative Controls: Implement changes in work procedures or training to minimize risks.
- Personal Protective Equipment (PPE): Provide and ensure the proper use of PPE when necessary.
Benefits of Job Safety Analysis
- Injury Prevention
- Proactive Approach: JSA prevents injuries by identifying and addressing potential hazards before they lead to accidents.
- Safety Culture: Fosters a safety culture where employees are actively involved in ensuring their well-being.
- Increased Efficiency
- Streamlined Processes: Identifying and eliminating unnecessary steps in a job enhances efficiency.
- Optimized Workflows: Streamlined processes contribute to improved productivity.
- Employee Engagement
- Involvement in Safety: Involving employees in JSA promotes a sense of ownership in workplace safety.
- Open Communication: Encourages open communication between workers and management regarding safety concerns.
- Compliance with Regulations
- Regulatory Adherence: JSA ensures that organizations comply with safety regulations and standards.
- Legal Protection: Demonstrating a commitment to safety through JSA provides legal protection in case of accidents.
Integration of JSA into Work Practices
- Training and Awareness
- Employee Training: Train employees on the importance of JSA and how to conduct it effectively.
- Continuous Education: Keep employees informed about new hazards and safety measures.
- Regular JSA Reviews
- Dynamic Process: JSA is a dynamic process that should be regularly reviewed and updated.
- Changing Work Conditions: Update JSA when there are changes in work conditions, equipment, or procedures.
- Documentation and Record Keeping
- Comprehensive Records: Maintain comprehensive records of conducted JSAs, including identified hazards and implemented controls.
- Reference for Training: Use documentation as a reference for employee training and orientation.
Conclusion
Job Safety Analysis is a proactive and systematic approach that empowers organizations to create a safer working environment. By breaking down job tasks, identifying hazards, and implementing preventive measures, JSA not only prevents injuries but also enhances efficiency and employee engagement. Integrating JSA into work practices ensures a continual commitment to workplace safety.
How to Validate Root Cause in Six Sigma
Root Cause Analysis Tools in Six Sigma
Process of Root Cause Analysis
Frequently Asked Questions (FAQs)
- What is the primary objective of Job Safety Analysis (JSA)?
- The primary objective of JSA is to systematically identify, assess, and mitigate potential hazards associated with specific job tasks, promoting proactive safety measures.
- How can organizations benefit from conducting Job Safety Analysis?
- Organizations benefit from JSA by preventing injuries, increasing efficiency, engaging employees in safety, and ensuring compliance with safety regulations.
- What steps are involved in conducting a Job Safety Analysis?
- The steps in conducting JSA include selecting a specific job, breaking down the job into steps, identifying potential hazards, assessing the risk level, and implementing preventive measures.
- Why is regular review and documentation important in the JSA process?
- Regular review ensures that JSA remains relevant to changing work conditions, while documentation provides comprehensive records for reference, training, and legal protection.