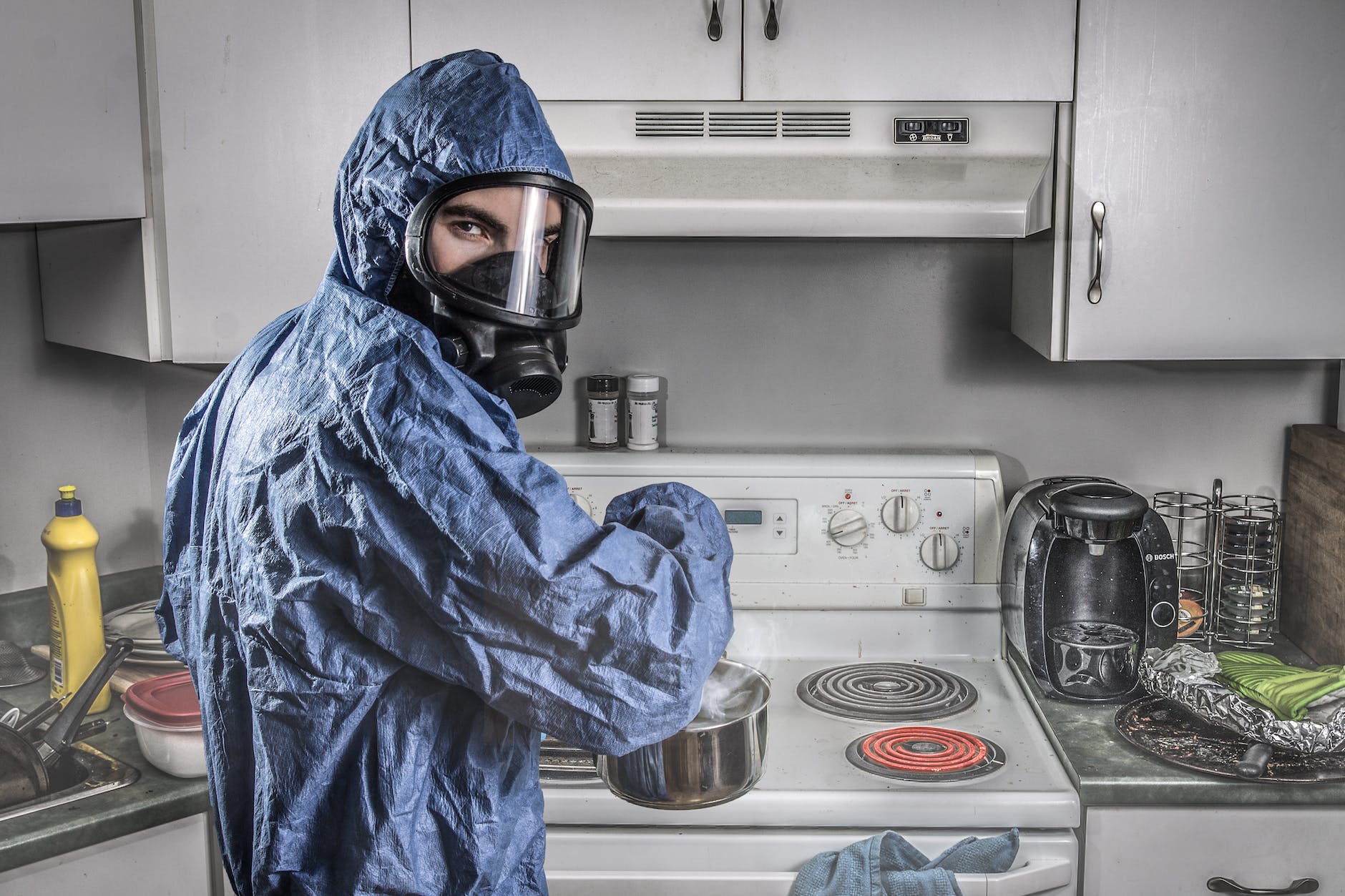
The Importance of Process Hazard Analysis in Ensuring Safety
Process Hazard Analysis (PHA) is a systematic and structured approach used in various industries, particularly in chemical, petrochemical, and manufacturing sectors, to identify and assess potential hazards associated with a specific process or operation. The primary goal of PHA is to prevent accidents, protect the safety of workers and the public, and safeguard the environment. Here are the key steps and methods involved in conducting a Process Hazard Analysis:
- Select the Process or System: Choose the specific process, operation, or system that you want to analyze. This could include chemical manufacturing, oil refining, food processing, or any other industrial activity.
- Assemble a Multidisciplinary Team: Form a team of experts and stakeholders with diverse knowledge and experience relevant to the process being analyzed. This team typically includes engineers, operators, safety professionals, and others who have a deep understanding of the process.
- Choose a PHA Method: There are several methods for conducting a PHA, and the choice of method depends on the complexity of the process and the industry standards. Common PHA methods include Hazard and Operability Study (HAZOP), Failure Modes and Effects Analysis (FMEA), What-If Analysis, and Fault Tree Analysis, among others.
- Define Process Components: Break down the process into its individual components, including equipment, chemicals, operating procedures, and safety systems.
- Identify Hazards: Systematically review each component of the process and identify potential hazards, such as chemical releases, fires, explosions, toxic releases, or other events that could lead to accidents or incidents.
- Evaluate Consequences: Assess the potential consequences of each identified hazard, considering factors like severity, likelihood, and the number of people or the environment that could be affected.
- Determine Risk Levels: Calculate the risk associated with each hazard by combining the severity and likelihood assessments. This helps prioritize hazards based on their risk levels.
- Recommend Risk Reduction Measures: Develop recommendations and strategies for mitigating or eliminating the identified hazards. This may involve changes in equipment design, operating procedures, emergency response plans, or the implementation of safety systems.
- Document Findings: Thoroughly document the results of the PHA, including all identified hazards, their risk levels, and the recommended actions. This documentation serves as a crucial reference for ongoing safety management and regulatory compliance.
- Implement Recommendations: Put the recommended risk reduction measures into action. This may involve making physical changes to the process, updating procedures, providing training to personnel, or enhancing safety systems.
- Review and Update: Periodically review and update the PHA to account for changes in the process, equipment, regulations, or industry standards. This ensures that the process remains safe over time.
- Management of Change: Establish a formal process for managing changes to the process or system to ensure that new hazards are not introduced inadvertently.
Process Safety: The Importance of Process Safety
Industrial Safety and Health Act
Excavation Safety Basic Knowledge
Electrical Safety Basic Knowledge
Process Hazard Analysis is an essential part of process safety management and helps organizations identify and control potential risks to prevent accidents and protect both human and environmental health. Compliance with industry-specific regulations and standards is typically a requirement when conducting PHAs.