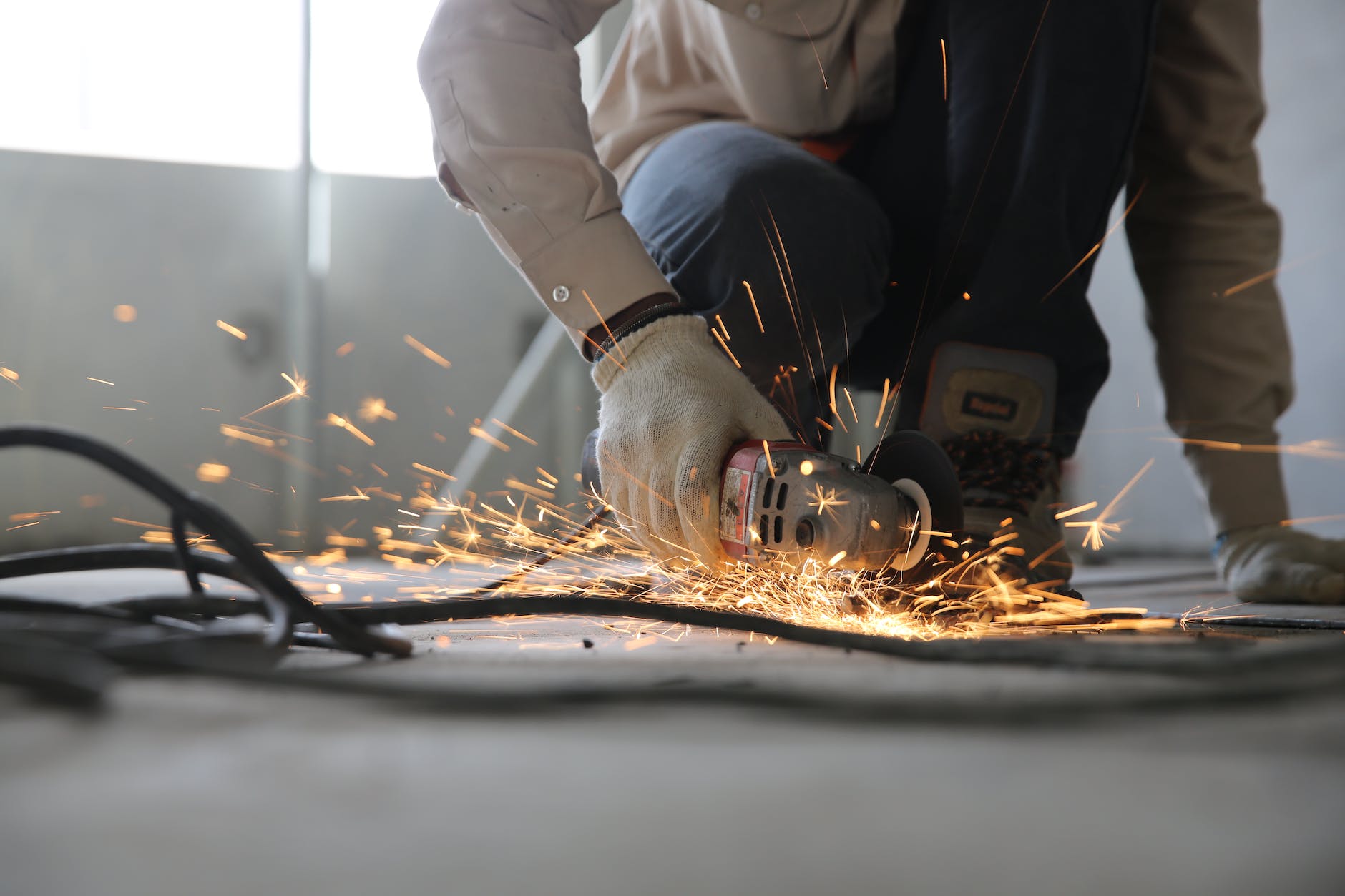
Workplace Hazards and Control Measures
Workplace safety is a critical aspect of any professional environment. Employees across various industries encounter diverse hazards that pose risks to their health and well-being. Understanding and mitigating these hazards are paramount to ensuring a secure and productive work environment.
Introduction to Workplace Hazards
Definition and Importance
Workplace hazards encompass any potential source of harm to employees while on the job. Recognizing and addressing these hazards are crucial for maintaining employee safety.
Types of Workplace Hazards
Different categories of workplace hazards exist, including physical, chemical, biological, ergonomic, and psychosocial hazards. Each presents unique risks that require specific control measures.
Common Workplace Hazards
Physical Hazards
These hazards involve risks related to machinery, noise, temperature extremes, and other physical aspects of the work environment.
Chemical Hazards
Chemical hazards arise from exposure to various substances, including toxic chemicals, gases, and fumes, which can lead to health complications.
Biological Hazards
Biological hazards encompass risks from exposure to pathogens, bacteria, viruses, and other infectious materials.
Ergonomic Hazards
Poor ergonomics can result in musculoskeletal disorders due to improper workstation setups or repetitive movements.
Psychosocial Hazards
Psychosocial hazards involve workplace stress, harassment, bullying, and other mental health-related risks.
Impact of Workplace Hazards
Workplace hazards can significantly impact employee health, leading to injuries, illnesses, or long-term health issues. Moreover, these hazards can diminish productivity and efficiency, affecting overall business performance.
Identifying and Assessing Workplace Hazards
Risk Assessment Methods
Various methodologies, such as job safety analysis and hazard mapping, aid in identifying and evaluating potential hazards.
Importance of Hazard Identification
Early detection and assessment of hazards allow for timely implementation of control measures, reducing risks to employees.
Control Measures for Workplace Hazards
Engineering Controls
Modifying equipment or processes to mitigate hazards directly at the source.
Administrative Controls
Implementing policies, procedures, and training to minimize exposure to hazards.
Personal Protective Equipment (PPE)
Using protective gear such as helmets, gloves, or masks to safeguard against hazards.
Training and Education
Providing employees with comprehensive training on hazard awareness and safety protocols.
Workplace hazards can vary widely depending on the industry, but here are some common types and control measures:
- Physical Hazards:
- Control Measures: Use of proper safety gear (helmets, gloves, goggles), regular equipment maintenance, implementing barriers or guards around dangerous machinery.
- Chemical Hazards:
- Control Measures: Providing adequate ventilation, labeling hazardous substances, ensuring proper storage and handling, using personal protective equipment (PPE) like masks and gloves.
- Biological Hazards:
- Control Measures: Proper sanitation practices, vaccinations where necessary, using protective clothing, and implementing protocols for handling potentially infectious materials.
- Ergonomic Hazards:
- Control Measures: Providing ergonomic furniture, encouraging regular breaks, offering training on proper lifting techniques, and adjusting workstations to minimize strain.
- Psychosocial Hazards:
- Control Measures: Promoting a supportive work environment, offering stress management programs, addressing workplace bullying or harassment, and providing counseling services.
- Fire Hazards:
- Control Measures: Installing fire alarms and extinguishers, conducting regular fire drills, ensuring proper storage of flammable materials, and providing fire safety training.
- Electrical Hazards:
- Control Measures: Regular inspection of wiring and equipment, using circuit breakers and ground fault circuit interrupters, and providing training on electrical safety protocols.
Implementing a comprehensive health and safety program that includes risk assessments, employee training, regular inspections, and continual improvement is crucial to effectively control workplace hazards.
Implementing Workplace Safety Programs
Importance of Safety Culture
Fostering a culture of safety where all employees prioritize and actively contribute to maintaining a safe workplace environment.
Strategies for Effective Safety Programs
Developing robust safety policies, regular training sessions, and incentivizing safety compliance.
Legal and Ethical Considerations
Regulatory Compliance
Ensuring adherence to local, national, and international safety regulations.
Employer Responsibilities
Employers have the ethical and legal obligation to provide a safe working environment for their employees.
Monitoring and Reviewing Safety Measures
Importance of Continuous Evaluation
Regular assessment and reassessment of safety measures to address evolving risks.
Adjustments and Improvements
Making necessary changes based on feedback, incidents, or advancements in safety technology.
Conclusion
Safeguarding employees against workplace hazards is a fundamental responsibility of employers. Prioritizing safety through comprehensive hazard identification, effective control measures, and ongoing evaluation not only protects employees but also enhances organizational efficiency and morale.
5S Principles in the Workplace
Workplace Safety Toolbox Talk Meeting
How to Promote a Safe Workplace
Unique FAQs
- Why is identifying workplace hazards important? Identifying hazards allows for timely implementation of measures to protect employees from potential risks, reducing accidents.
- What are some examples of engineering controls? Examples include machine guards, ventilation systems, and equipment modifications to reduce hazards.
- How can employers promote a safety culture? Encouraging open communication, recognizing safety efforts, and involving employees in safety decision-making foster a safety-oriented culture.
- Are there legal consequences for not addressing workplace hazards? Yes, failure to address hazards can result in legal liabilities, fines, or penalties for non-compliance with safety regulations.
- Why is continuous monitoring of safety measures necessary? Continuous monitoring allows for adjustments to be made in response to changing workplace conditions or emerging risks, ensuring sustained employee safety.