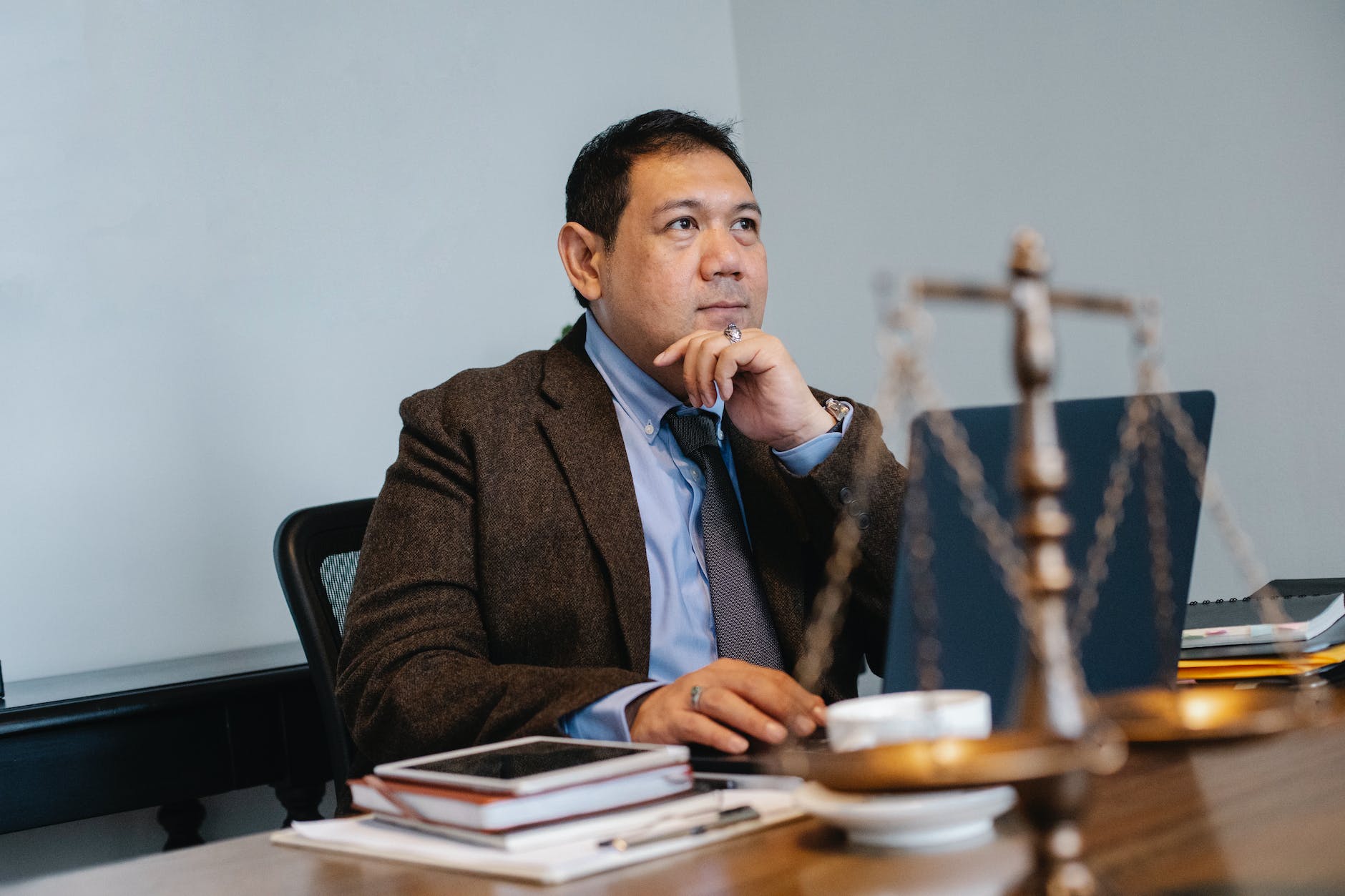
OSHA Horizontal Lifeline Requirements
When it comes to workplace safety, adhering to OSHA guidelines is paramount. For industries involving work at heights, such as construction or maintenance, understanding and implementing OSHA horizontal lifeline requirements are crucial. These guidelines aren’t just formalities; they are designed to ensure the safety of workers operating in elevated environments.
Understanding OSHA Guidelines
OSHA, the Occupational Safety and Health Administration, sets regulations to protect workers’ safety and health. Specifically, when it comes to working at heights, OSHA’s guidelines outline the necessity of horizontal lifelines. These guidelines provide a comprehensive framework to safeguard workers, focusing on specific aspects like lifeline components and their installation.
OSHA (Occupational Safety and Health Administration) has specific requirements for horizontal lifelines to ensure worker safety when working at heights. Here are some key aspects of OSHA's requirements:
- Design and Installation: Horizontal lifelines must be designed, installed, and used under the supervision of a qualified person. The design should meet specific load requirements and be installed according to manufacturer instructions.
- Anchorage Strength: The lifeline’s anchorage points should have sufficient strength to support the intended loads. They must be securely attached to structural members capable of supporting the load requirements.
- Fall Clearance: Adequate fall clearance must be provided to prevent workers from striking a lower level or obstruction in case of a fall. This may involve calculating the distance a worker could fall and ensuring that the lifeline system accounts for this.
- Connectors and Lifelines: Connectors used on the lifeline (e.g., lanyards, deceleration devices) must be compatible with the lifeline and capable of sustaining the anticipated loads.
- Inspection and Maintenance: Regular inspection, maintenance, and replacement of components are necessary to ensure the lifeline’s effectiveness and safety. This includes checking for wear, corrosion, and damage.
- Training and Use: Workers must be trained in the proper use of horizontal lifelines, including how to properly connect, adjust, and use personal fall protection equipment in conjunction with the lifeline.
It's crucial to refer directly to OSHA's guidelines and regulations, as they can vary based on the specific industry, work environment, and circumstances. Always ensure compliance with the most recent OSHA standards to maintain a safe working environment.
Components of a Horizontal Lifeline System
A horizontal lifeline system comprises several essential components. Anchorage points, which provide secure attachment, are crucial. The choice of lifeline materials and design also plays a pivotal role in ensuring durability and effectiveness.
Proper installation and regular maintenance are imperative for the functionality of these lifeline systems. Following specific installation procedures and conducting routine inspections are fundamental to ensure these lifelines remain reliable and secure.
Training and Safety Measures
Apart from having the right equipment, training workers to properly use and maintain these lifelines is vital. Educating them on safety measures to follow while using these systems significantly reduces the risk of accidents.
Compliance and Penalties
Non-compliance with OSHA regulations can lead to severe consequences. Violations can result in penalties that not only affect the company financially but also compromise the safety of workers.
Advancements in Horizontal Lifeline Technology
Technology in this field continually evolves. Innovations in lifeline systems have introduced more efficient and safer solutions, enhancing worker safety and productivity.
Case Studies and Examples
Real-life examples of successful implementation of these lifelines showcase their effectiveness in ensuring worker safety, providing insights into best practices.
Challenges and Solutions
Implementing lifeline systems might pose challenges, but there are solutions available to address these hurdles effectively. Understanding common obstacles and how to overcome them is crucial for successful implementation.
Industry-specific Requirements
Different industries may have unique requirements when it comes to lifeline systems. Understanding these industry-specific needs is crucial in implementing the right lifeline solution.
Best Practices for Implementation
Following recommended best practices ensures the effective implementation of horizontal lifeline systems, enhancing workplace safety.
Future Trends and Predictions
As technology advances, there are emerging trends in lifeline systems, and predicting the future of OSHA regulations in this area becomes essential.
Conclusion
OSHA horizontal lifeline requirements are fundamental for ensuring workplace safety in industries involving work at heights. Adhering to these guidelines, implementing best practices, and staying updated with technological advancements are key to creating a safe working environment.
OSHA Fall Protection Requirements
OSHA Anchor Point Requirements
Full Body Harness 100% Tie Off
FAQs
- Do all industries need to comply with OSHA horizontal lifeline requirements? Yes, industries involving work at heights or elevated environments need to comply with OSHA horizontal lifeline requirements to ensure worker safety. These industries may include construction, maintenance, telecommunications, and more.
- What are the consequences of non-compliance with these regulations? Non-compliance with OSHA regulations can lead to serious consequences, including hefty fines, potential legal actions, work stoppages, and most importantly, increased risks to worker safety.
- How often should lifeline systems undergo maintenance and inspection? Lifeline systems should undergo regular maintenance and inspection as per the manufacturer’s guidelines and OSHA recommendations. Typically, inspections should occur at least annually or more frequently based on usage and environmental conditions.
- Are there specific training programs available for using these lifelines? Yes, there are specialized training programs designed to educate workers on the proper use, inspection, and maintenance of horizontal lifeline systems. These programs help ensure that workers are well-equipped to use the equipment safely and effectively.
- What are some common challenges faced during lifeline implementation, and how can they be mitigated? Common challenges during lifeline implementation may include issues with proper anchorage, determining the right lifeline materials, or ensuring adequate training for workers. These challenges can be mitigated by thorough planning, adherence to guidelines, proper training, and regular inspections.